粉末ベースの製造プロセスの目的
目次
ほとんどの粉末ベースの製造プロセスの目的
粉末冶金 (PM) などのほとんどの粉末ベースの製造プロセスの目標は、出発材料を溶かさずに気孔率 1% 未満の緻密な部品を製造することです。これらのプロセスで使用されるルースパウダーは通常、積層密度が低く、ランダムに積層された完全な球形の粒子の理論上の最大密度はわずか 64% です。ただし、適切な粉末粒度分布または変形可能な粉末を使用することにより、90% を超える充填密度を達成できます。
一軸プレスの限界
粉末ベースの製造プロセスで満足のいく結果を得るには、圧力を加えることが重要です。一方向に圧力を加える一軸プレスが一般的です。ただし、この方法には、特に厚い部品の場合には制限があります。プレス方向に沿って密度に差が生じる傾向があり、最終部品の品質に影響を与える可能性があります。
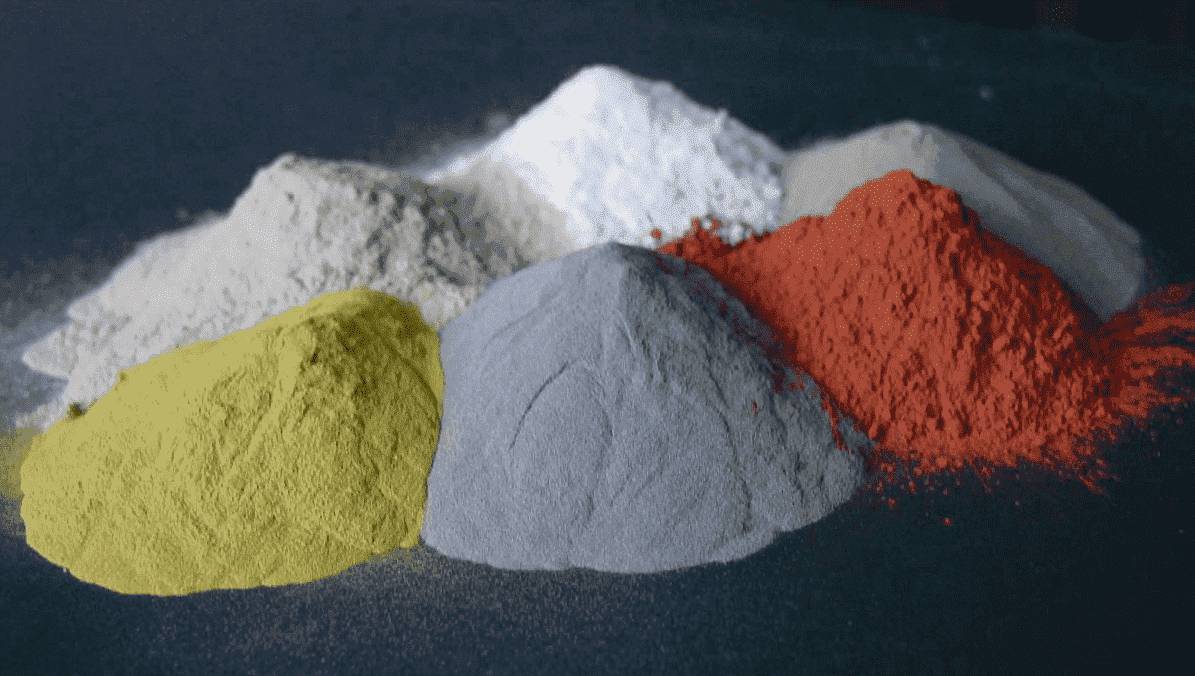
解決策:静水圧プレス
一軸プレスの限界を克服するために、バルク部品には静水圧プレスがよく使用されます。静水圧プレスは、流体圧力を使用して部品を圧縮する粉末処理技術です。金属粉末はフレキシブルコンテナに入れられ、部品の型として機能します。流体圧力が容器の外面全体にかかり、粉末が圧縮されて所望の形状に成形されます。一軸プレスとは異なり、静水圧プレスでは全方向から圧力がかかるため、より均一な密度分布が得られます。
代替プロセス
静水圧プレス
静水圧プレスは、均一な圧力を加えて粉末を固めたり、鋳造品の欠陥を修復したりする、広く使用されている粉末ベースの製造プロセスです。セラミック、金属、複合材料、プラスチック、カーボンなど、さまざまな材料に使用できます。このプロセスには、粉末を柔軟な型に入れて密封し、あらゆる方向から圧力をかけることが含まれます。静水圧プレスは、正確な公差で製品形状を形成できるため、コストのかかる機械加工の必要性を軽減できるため、セラミックおよび耐火物の用途に独特の利点をもたらします。
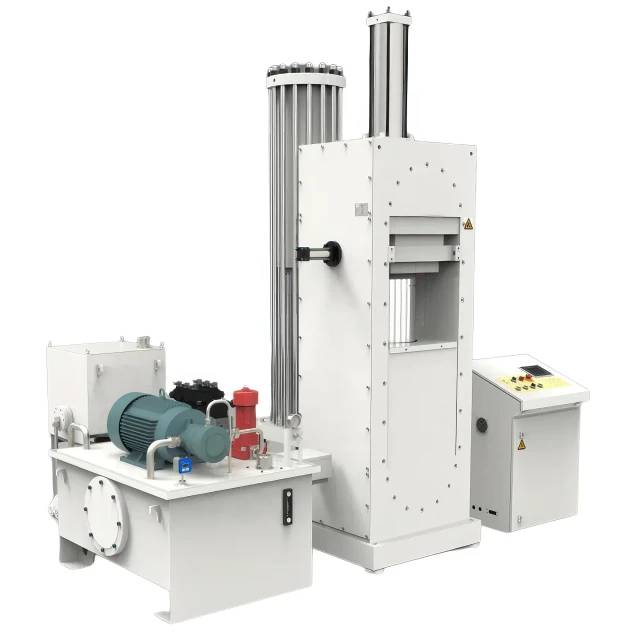
粉末金属加工
粉末金属加工は、合金材料を超える特性を備えた製品の製造を可能にするもう 1 つの粉末ベースの製造技術です。このプロセスでは、金属またはセラミックの粉末を結合剤とともに混合して、所望の形状にプレスできる混合物を形成します。大きな部品の場合は、混合物を型に充填します。このプロセスは、深井戸掘削用の多結晶ダイヤモンド複合材 (PDC) ドリルビットなどの製品の製造に一般的に使用されており、混合物をプレスして焼成してニアネットシェイプの製品を生成します。
粉末冶金の進歩
粉末圧縮、粉末熱間静水圧プレス (P-HIP)、金属射出成形 (MIM)、および放電プラズマ焼結などの粉末ベースのプロセスは、ネットシェイプ (NS) およびニアネットシェイプ (NS) の製造にますます使用されています。高性能合金の形状 (NNS) コンポーネント。これらのプロセスは、必要な最終形状に厳密に一致する部品を製造し、機械加工や仕上げなどのプロセスステップを最小限に抑えることでコスト、リードタイム、材料の無駄を削減することを目的としています。粉末ベースの技術は、鋳造などの従来の製造プロセスの性能特性に匹敵するか、それをさらに向上させることができる性能特性を備えた部品を製造する能力を備えています。これは、粒子状材料に伴う均一な微細構造や、粉末形式での幅広い高性能合金の製造を可能にする粉末冶金の進歩などの要因によるものです。
結論として、粉末ベースの製造プロセスの目的は、高い充填密度と最小限の気孔を備えた高密度の部品を製造することです。静水圧プレスは、一軸プレスの限界を克服するために使用される貴重な技術であり、厚い部品でより均一な密度分布を実現します。さらに、粉末金属加工や粉末冶金の進歩などの代替プロセスにより、粉末ベースの製造能力が拡大し、複雑な形状や高性能合金の製造が可能になりました。
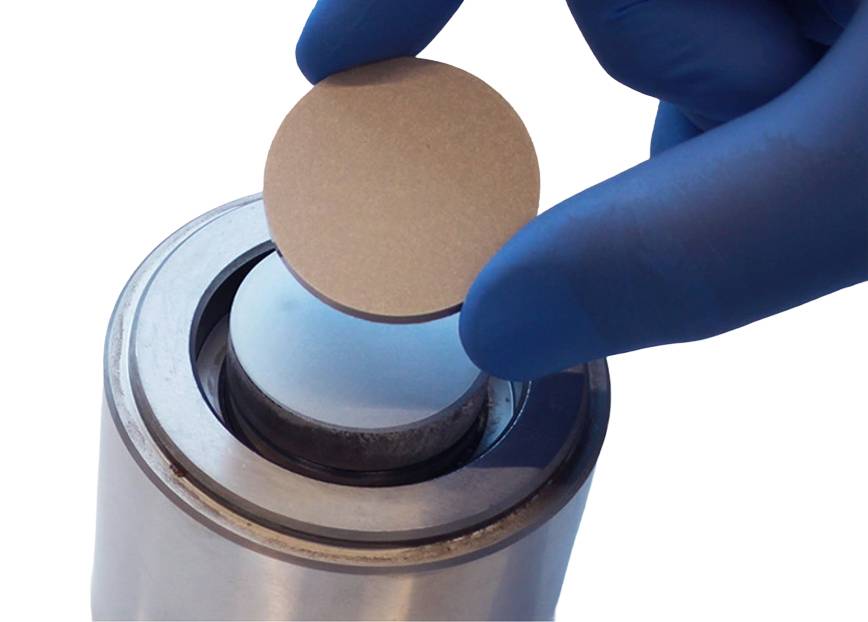
冷間静水圧プレス (CIP) プロセス
CIPのプロセス
冷間静水圧プレス (CIP) は、粉末をさまざまなサイズや形状のコンポーネントに成形および圧縮するために使用される材料処理方法です。これには、粉末または低密度の緑色部品を密閉されたフレキシブルな容器に入れ、圧力容器内の液体に浸すことが含まれます。数千バールの圧力が加えられ、圧粉体が可能な限り最大充填密度に近づくように圧縮されます。このより高い初期密度により、熱サイクルにおける最終密度までの固化が加速されます。
CIP は、フランスの科学者ブレーズ パスカルによって提案された原理を利用しています。この原理は、密閉された非圧縮性流体内の圧力変化が、流体のあらゆる部分とその容器の表面に減衰せずに伝わるというものです。ゴム袋などの変形抵抗の低い成形型に粉末材料を封入し、液圧を加えて成形体を全面均一に圧縮します。
金型プレスはCIPと同様のプレス方法です。金型と下パンチで囲まれた空間に粉末材料を充填する方法です。次に、上下のパンチ間の距離を狭めて圧縮します。
熱サイクルにおける最終密度への固化を加速する際の高い初期密度の利点
CIP プロセスによって達成される高い初期密度は、粉末の固化においていくつかの利点をもたらします。これらの利点には次のものが含まれます。
後続の焼結プロセス中の予測可能な圧縮: 高い圧縮と均一な密度により、焼結プロセス中の予測可能な圧縮が実現され、一貫した信頼性の高い最終密度が得られます。
大型、複雑、完璧な形状の加工能力:CIP により、大型で複雑な形状を高精度に加工できます。これにより、後処理プロセスの時間とコストが節約されます。
均一な密度を持つ大きなアスペクト比の部品の生成: CIP は、コンポーネント全体で均一な密度を維持しながら、アスペクト比が 2:1 を超える部品を生成できます。
プロセス内での取り扱いや処理に適したグリーン強度: CIP によって形成されたグリーンコンパクトは、プロセス内でのハンドリングや処理を受けるのに十分な強度を備えているため、製造コストが削減されます。
全体として、CIP プロセスは粉末の効率的かつ効果的な成形と圧縮を実現し、その結果、望ましい密度を備えた高品質のコンポーネントが得られます。さまざまな材料を加工できる汎用性と能力により、精密製造、航空宇宙、防衛、自動車などの業界で貴重な方法となっています。
DataInteloのレポートによると、世界の冷間等静圧加圧(CIP)装置市場は、2020年から2026年の予測期間中に大幅なCAGRで成長すると予測されています。精密製造、航空宇宙、防衛、自動車などの業界における CIP 加工製品の需要の増加が、この成長を推進しています。
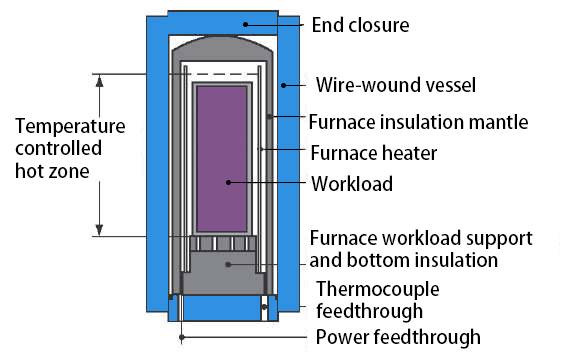
熱間静水圧プレス (HIP) プロセス
HIP における一軸加圧焼結の活用
熱サイクル中に圧力を加えることもできます。一軸加圧焼結では、通常、板状の製品しか製造できません。より複雑な部品の場合は、熱間静水圧プレス (HIP) が使用されます。 HIP はガス雰囲気中で実行されるため、主な要件は、処理された部品の外面が最初から気密であることです。したがって、このプロセスは、部品の粉末を軟鋼のシェルに真空封入することによって部品を製造するために使用できます。圧力を均一に加えることで、パーツやシェルが収縮しても形状が保持されます。 HIP 戦略を使用して処理された粉末は、通常、過度の温度が必要になったり、好ましくない微細構造が生じたりするため、溶融プロセスには適合しません。それにもかかわらず、これらの材料を加工するために余分な労力が費やされているということは、低レベルの気孔率ですら受け入れられない要求の厳しい用途での使用を示しています。
HIP プロセスの要件と結果
熱間静水圧プレス (HIP) は、金属やその他の材料の機械的特性を向上させるために、指定された時間にわたって高温と圧力を同時に適用することです。 HIP ユニットでは、高温炉が圧力容器内に密閉されています。温度、圧力、処理時間はすべて正確に制御され、最適な材料特性が得られます。部品は不活性ガス (通常はアルゴン) 中で加熱され、全方向に均一に「等静圧」圧力がかかります。これにより、材料が「可塑性」になり、差圧下で空隙が潰れるようになります。空隙の表面が拡散結合して欠陥を効果的に除去し、理論密度に近い密度を達成しながら、インベストメント鋳造などの部品の機械的特性を向上させます。
HIP 戦略を使用して処理された粉末と溶融プロセスとの非互換性
熱間静水圧プレス (HIP) は、熱と圧力を使用して材料の物理的特性を向上させる材料処理プロセスです。通常、金属やセラミックに対して行われます。これらの種類の材料は熱と圧力にさらされると、物理的特性が変化します。 HIP は、粉末ベースの積層造形部品の欠陥を除去し、疲労特性と延性が向上した 100% 緻密な材料を生成する効果的なプロセスです。
分野 HIP は、鋳造や鍛造と同等の規模に達して以来、その真価を発揮し、原材料コストの高い用途では鍛造や鋳造の経済的競合相手として認識されるようになりました。現在、HIP には石油とガス、発電、航空宇宙の 3 つの主要なセクターがあります。 PM HIP コンポーネントの製造は、通常の従来の冶金プロセスよりも無駄がなく、短時間で行えます。エネルギーおよび材料コストに対する HIP のコストは、過去 20 年間で 65% 減少しました。
はじめに 熱間静水圧プレス (HIP) は、炉内で高圧 (100 ~ 200 MPa) および 900 ~ 1250°C の温度で、鋼や超合金などの粉末または鋳造および焼結部品を緻密化するプロセスです。ガス圧力は全方向に均一に作用し、等方性特性と 100% の緻密化を実現します。これには多くの利点があり、多くの用途において鍛造、鋳造、機械加工などの従来のプロセスに代わる実行可能で高性能な代替手段となっています。
焼結/粉末冶金: 熱間静水圧プレス (HIP) 技術
過去 50 年の間に、熱間静水圧プレスは研究室から本格的な通常生産に移行しました。材料特性の改善、粉末材料の使用、ネットシェイプまたはネットシェイプに近い部品の製造への要望が加速するにつれて、この技術の将来は明るいと思われます。
容器内の抵抗加熱炉温度源
もともとガス圧接合として知られていた HIP プロセスは、1955 年にオハイオ州コロンバスにあるバッテル記念研究所の研究室で開発されました。当初の用途は、核燃料要素用のジルコニウム - ジルコニウム - ウラン合金へのジルコニウムの拡散接合被覆でした。同じ頃、ASEA-スウェーデンは、最初の合成ダイヤモンドを圧縮するために圧力の静水圧の適用を利用していました。熱間静水圧プレス (HIP) は、金属の気孔率を減らし、多くのセラミック材料の密度を高めるために使用される製造プロセスです。これにより、材料の機械的特性と加工性が向上します。
熱間静水圧プレス (HIP) とは何ですか?
熱間静水圧プレス (HIP) または「ヒッピング」は、材料に熱と高圧を同時に適用することです。このプロセスは、気孔率を最大 100% 除去することで積層造形製品の特性を改善するのに理想的です。
現在、このプロセスは積層造形製品の改良にすでに使用されています。ヒッピングの結果、内部空隙 (多孔性) が除去され、微細構造が改善され、機械的特性が大幅に改善されました。 HIP は、チタン、鋼、アルミニウム、銅、マグネシウムなどの幅広い合金に適用できます。
マルチマテリアル積層造形による構造物の単一ステップ前処理の機会
CIP プロセスと HIP プロセスの両方におけるマルチマテリアル積層造形の潜在的な利点
マルチマテリアル積層造形は、等方圧プレス (CIP) プロセスと熱間等方圧プレス (HIP) プロセスの両方でさまざまな潜在的な利点をもたらします。このアプローチは、選択的粉末堆積を使用することにより、新しい積層造形技術とハイエンド コンポーネントの従来の製造方法の間のギャップを埋めることができます。確立された技術で部品を集約することで、AM製品の品質や信頼性への不安を軽減します。
マルチマテリアル積層造形の主な利点の 1 つは、製造コストの削減です。部品の複雑さが増し、処理ステップが減り、時間が短縮されるため、メーカーはコスト削減を達成できます。これは、効率と費用対効果が重要な小規模シリーズやプロトタイプの生産に特に有益です。
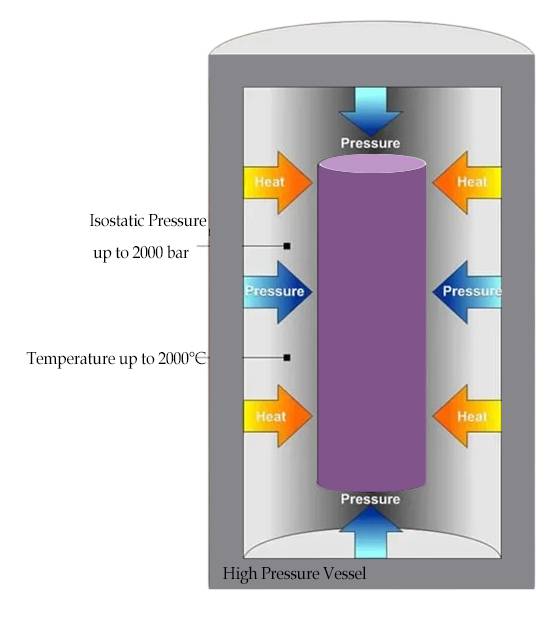
部品の複雑さの増加、処理ステップの減少、および時間の短縮により、製造コストが削減される可能性があります。
複数材料の積層造形を使用すると、製造コストの削減につながる可能性があります。従来のサブトラクティブ マニュファクチャリング手法には幾何学的限界があり、アディティブ マニュファクチャリングには適用されなくなりました。これは、製造コストを大幅に増加させることなく、複雑な形状やデザインを作成できることを意味します。さらに、生産コストを変えることなく同じ製品の複数のバージョンを作成できるため、コストをさらに削減できます。
マルチマテリアル添加剤製造のもう一つの大きな利点
加工廃棄物を大幅に削減することです。目的の物体が得られるまで材料を段階的に追加するため、従来のサブトラクティブ製造法と比較して無駄が最小限に抑えられます。これはコストを削減するだけでなく、より持続可能な製造プロセスにも貢献します。
金属積層造形の世界では、金属射出成形 (MIM)、バインダー ジェッティング (BJ)、熱溶融堆積モデリング (FDM) などの手法の使用が顕著に増加しています。これらの方法には、コスト、設計の柔軟性、材料特性の点で独自の利点があります。

金属積層造形では、印刷後の熱による脱脂が重要なプロセスです。これには、結合剤やその他の添加剤を除去して、完全に緻密な金属部品を得ることが含まれます。金属積層造形で製造された部品を適切に脱バインダすることは、望ましい機械的特性と寸法精度を達成するために不可欠です。
CIP プロセスと HIP プロセスは両方とも、複数の材料構造を利用します。 CIP ではセラミック粉末を含むポリマー シェルの使用が含まれますが、HIP ではハイエンドの粉末冶金合金を使用した溶接された軟鋼シート材料のケーシングが使用されます。これらの方法は、複数材料の積層造形による構造の単一ステップの前処理の機会を提供します。
このアプローチは、より少ない処理ステップとより短い時間で部品の複雑性を高めることができるため、小規模なシリーズやプロトタイプを生産する場合に特に有益です。マルチマテリアル積層造形の利点を活用することで、メーカーは生産プロセスの効率とコスト効率の向上を達成できます。
HIPプロセスの産業基盤は、材料特性の向上と粉末材料の使用に対する需要の高まりにより急速に拡大しています。さらに、HIP 装置の進歩、処理時間の短縮、経済性の向上により、HIP プロセスは幅広い材料に対して実行可能な選択肢となっています。これにより、複数材料の積層造形による構造物の単一ステップ前処理の可能性がさらに高まります。
結論として、マルチマテリアル積層造形は、CIP プロセスと HIP プロセスの両方で効率を向上させ、コストを削減し、複雑な設計を実現する大きな機会を提供します。このテクノロジーの利点を活用することで、メーカーはイノベーションの最前線に留まり、今日の競争の激しい市場の需要を満たすことができます。
kintek の選択的堆積技術の静水圧プレスでの使用
異なる材料の同時蒸着
静水圧プレスは、高圧の流体に浸されたエラストマー容器内で粉末を圧縮する方法です。伝統的に、このプロセスは主にセラミックと金属に使用されてきました。しかし、kintek の革新的なアプローチなど、選択的堆積技術の最近の進歩により、静水圧プレスの新たな可能性が開かれました。
KinTek の選択堆積技術により、異なる材料の同時堆積が可能になります。これは、単一の粉末材料を使用する代わりに、複数の材料を層ごとに堆積できることを意味します。これにより、独自の特性を持つ複雑なマルチマテリアル部品を作成するための幅広い可能性が開かれます。
圧縮されていないセラミック粉末を取り囲む、成形された液密ポリマーシェルの作成
KinTek の静水圧プレスにおける選択的堆積技術の主な利点の 1 つは、圧縮されていないセラミック粉末を囲む成形された液密ポリマー シェルを作成できることです。このシェルはバリアとして機能し、静水圧プレスプロセス中にセラミック粉末が分散するのを防ぎます。
選択的蒸着を使用してこのシェルを作成することにより、高さ/直径比が大きい部品であっても均一なグリーン密度を達成することが可能です。これは、航空宇宙産業や自動車産業など、寸法管理が重要な用途では特に重要です。
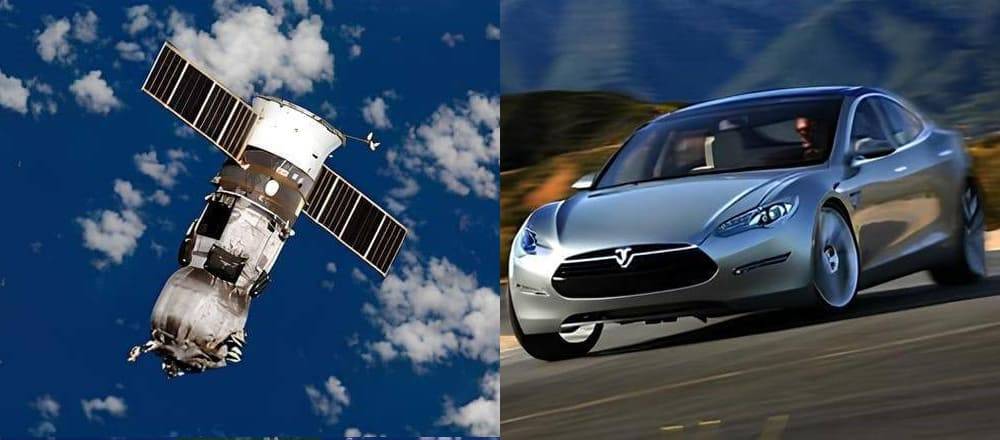
CIP マシン内での構造物の輸送と配置が簡単
の選択堆積技術のもう 1 つの利点は、冷間静水圧プレス (CIP) 機械内での構造の輸送と配置が容易であることです。この構造は、圧縮されていないセラミック粉末が充填された成形ポリマーシェルで構成されており、簡単に取り扱い、CIP マシン内に配置することができます。
この輸送と配置の容易さにより、効率が向上するだけでなく、積み込みプロセス中に構造物が損傷するリスクも軽減されます。これにより、より合理化された信頼性の高い静水圧プレスプロセスが可能になり、一貫した結果と高品質の部品が保証されます。
結論として、 の選択堆積技術は静水圧プレスに刺激的な可能性をもたらします。さまざまな材料の同時蒸着、成形された液密ポリマー シェルの作成、CIP マシン内での構造体の輸送と配置の容易さはすべて、この製造プロセスの進歩に貢献しています。の技術は、さらなる開発と改良により、寸法制御と性能が向上し、複雑な複数材料の部品を製造する方法に革命をもたらす可能性があります。
HIP を使用して加工された部品に対する同様のアプローチの可能性
選択的粉末堆積システムを使用した軟工具鋼と PM 特有の合金の同時堆積
HIP を使用して処理する必要がある部品についても、同様のアプローチを使用できます。軟工具鋼と PM 特有の合金は、選択的粉末堆積システムを使用して同時堆積でき、工具鋼の外側のみを強化する必要があります。 PM 合金は溶かす必要がないため、溶接板金から製造される HIP 製造部品と同様に、真空下でこのケーシングを溶接シールできる配管付きのプレフィルド ケーシングを製造することは容易に想像できます。残りの HIP 処理は従来のルートに従うことができます。
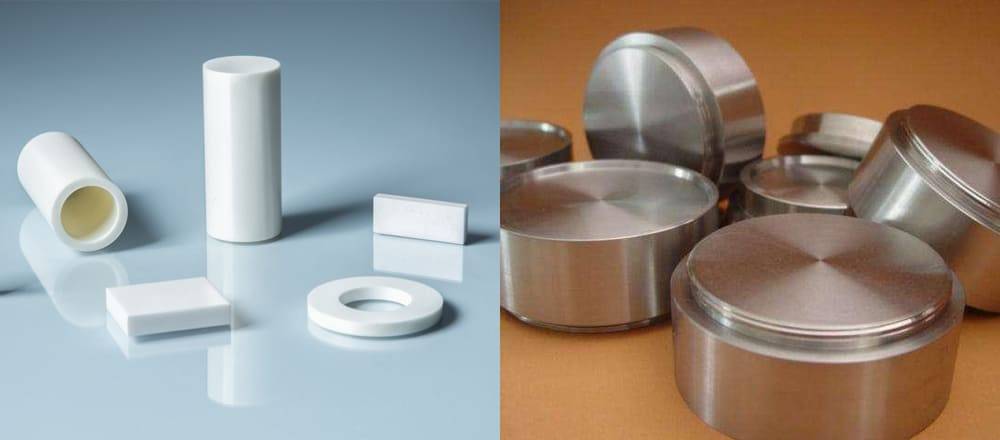
真空下での溶接シール用の配管を備えたプレフィルドケーシングの製造
HIP 処理に対する同様のアプローチは、HIP 処理が必要な部品にも使用できます。選択粉末堆積システムを使用して軟工具鋼と PM 特定合金を共堆積することにより、真空下で溶接シール用の配管を備えたプレフィルド ケーシングを製造することができます。これにより、PM 合金の完全性を維持しながら工具鋼の外側を強化することができます。残りの HIP 処理は通常どおり続行できます。
残りのHIP処理の従来のルート
選択的粉末堆積システムを使用して軟工具鋼と PM 特定合金を共堆積し、工具鋼の外側を強化した後、残りの HIP 処理は従来のルートに従うことができます。これには、処理の経済性を高め、最終的な材料特性を向上させるための高度な冷却技術の使用が含まれます。アルゴンガスと内部冷却システムを使用してより速く冷却できる機能により、HIP サイクルが大幅に短縮され、コスト削減と部品品質の向上につながります。
さまざまな業界での HIP の使用は、非常に有益であることが証明されています。 HIP は、石油およびガス部品やネット シェイプ インペラなどの大型で巨大なニア ネット シェイプ金属部品を含む、幅広い部品の製造に使用できます。小型の PM HSS 切削工具や歯科用ブラケットなどの小さな部品の製造にも適しています。このプロセスは長年にわたって進化し、金属およびセラミック部品を製造するための高性能、高品質、そしてコスト効率の高い方法になりました。
HIPing には、機械的特性の向上、スクラップの削減、機械加工の最小限化、古い部品の再生機能など、数多くの利点があります。アルミニウム、鋼、ステンレス鋼、超合金、チタン、セラミックスなどのさまざまな材料に適用できます。 HIP 装置と処理時間の進歩により、HIP プロセスは幅広い材料や用途でますます一般的になってきています。
結論として、HIP 処理に対する同様のアプローチは、HIP 処理が必要な部品に適用できます。選択的粉末堆積システムを使用して軟工具鋼と PM 特定合金を共堆積することにより、真空下で溶接シール用の配管を備えたプレフィルド ケーシングを製造することができます。このアプローチには、部品品質の向上、処理時間の短縮、コスト削減など、多くの利点があります。 HIP テクノロジーの継続的な進歩により、さまざまな業界でこのアプローチを使用できる可能性が拡大し続けています。
結論: 新しい積層造形と従来の製造の間の選択的粉末堆積の架け橋
新しい積層造形技術と従来のハイエンドコンポーネントの製造との間に架け橋を生み出す選択的粉末堆積の可能性
選択的粉末堆積には、新しい積層造形 (AM) 技術とハイエンド コンポーネントの従来の製造との間のギャップを埋める可能性があります。このアプローチは、業界ですでに利用可能であり、十分に理解されている圧力処理および熱サイクル プロセスを利用します。これらの確立された方法を使用して AM によって作成された部品を統合することにより、この新しいテクノロジーによって製造される製品に対する業界の不安を軽減できます。
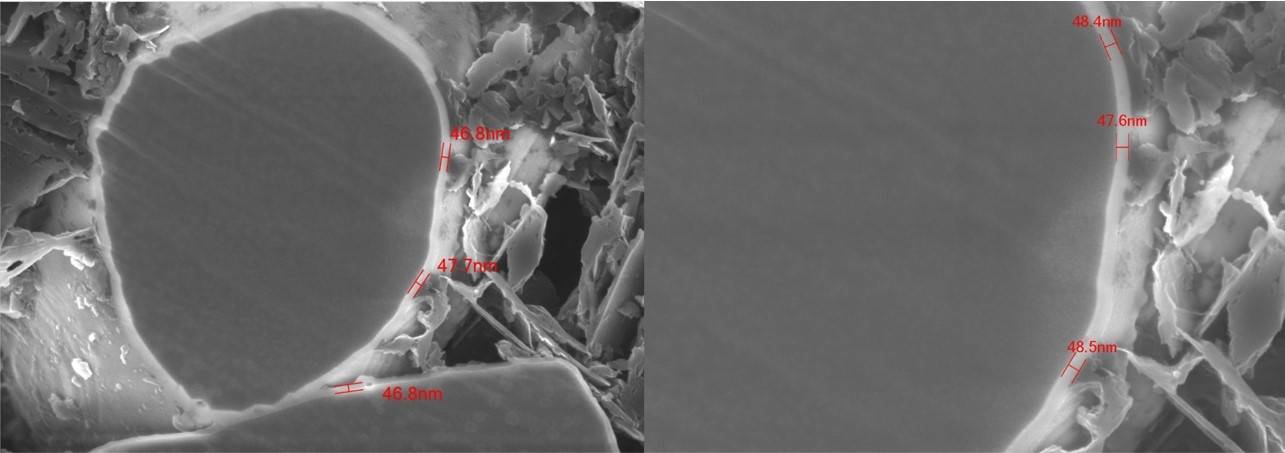
このアプローチにより、AM経由で生産される品目に対する業界の不安が軽減される可能性
積層造形に関して業界での主な懸念事項の 1 つは、最終製品の品質と信頼性です。伝統的な製造方法は数十年にわたって改良されており、これらのプロセスを通じて生産されるコンポーネントには一定の信頼と自信があります。
選択的粉末堆積を使用することにより、AM によって作成された部品を新しい技術を使用して成形しながら、長年確立された方法を使用して統合することができます。これは、ハイエンド コンポーネントでの AM の使用に関する不安の一部を軽減するのに役立ちます。
結論として、選択的粉末堆積は、新しい積層造形技術と従来の製造の間のギャップを埋める有望なソリューションを提供します。伝統的な製造で確立されたプロセスと技術を活用することで、AM を通じて製造されるコンポーネントに対する信頼と自信を築くことができます。
無料相談はお問い合わせください
KINTEK LAB SOLUTION の製品とサービスは、世界中のお客様に認められています。弊社スタッフがどんなご質問にも喜んで対応させていただきます。無料相談にお問い合わせいただき、製品スペシャリストにご相談いただき、アプリケーションのニーズに最適なソリューションを見つけてください。