スパークプラズマ焼結(SPS)は、粉末から緻密で均質な材料を製造するための最先端の焼結技術です。パルス状の直流電流(DC)と一軸の圧力を用いて粉末を急速に加熱・焼結するため、従来の方法に比べて低温・短時間で高品質な材料を作ることができる。SPS装置はいくつかのメーカーが製造しているが、キンテック・ソリューションはその代表的な例である。Kintek社は技術革新と高品質のシステム性能を最優先しており、この分野のリーディング・サプライヤーとなっている。SPSは、防護服、ロケットノズル、炭素繊維複合材料などの先端材料の製造を含め、研究および商業用途の両方で広く使用されています。
要点の説明
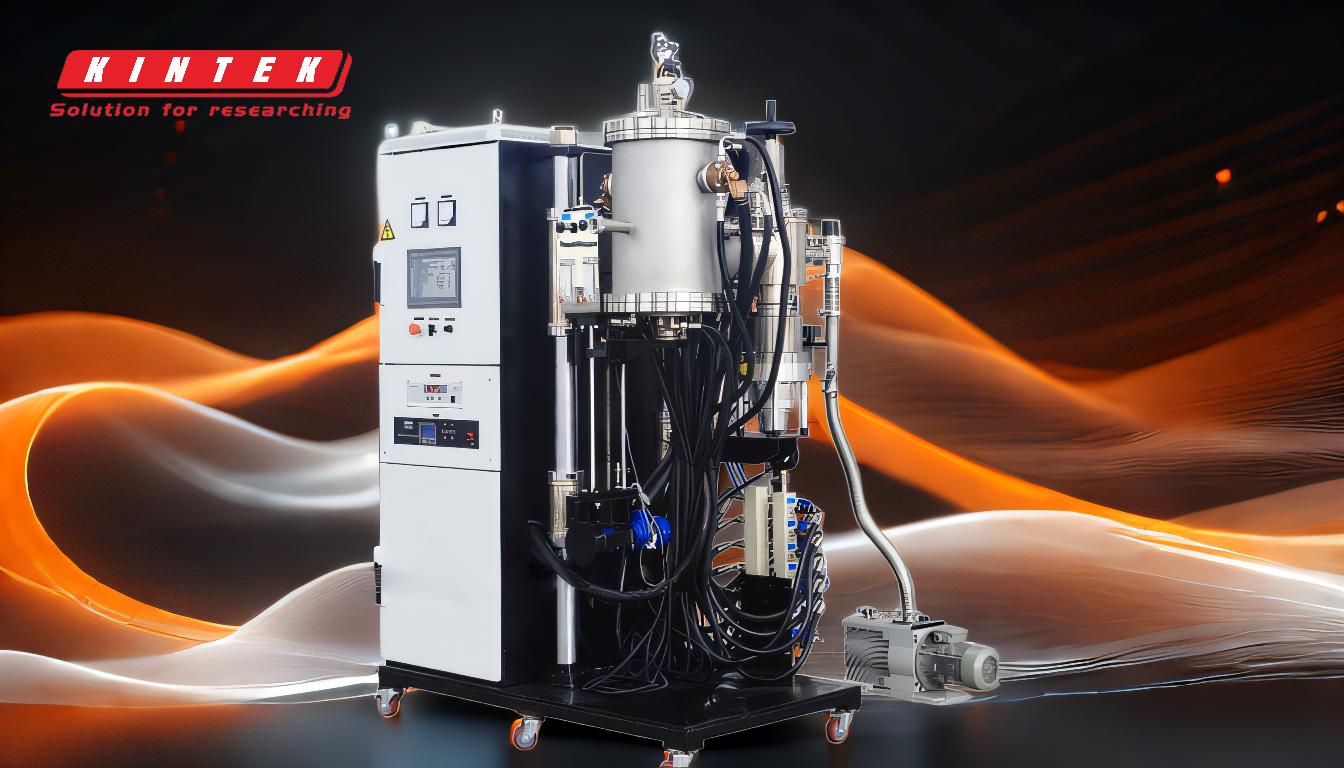
-
スパークプラズマ焼結(SPS)とは?
- SPSは、パルス直流電流(DC)と一軸圧力を用いて粉末を緻密で高品質な材料に凝集させる高度な焼結技術です。
- 従来の焼結法に比べて低温・短時間で作動するため、非常に効率的である。
- このプロセスでは、多くの場合グラファイト製の導電性ダイスを通して粉末を内部および外部から加熱するため、急速な加熱と冷却が可能である。
-
SPS技術の主な特徴
- 迅速な加熱と冷却: SPSは非常に速い加熱・冷却速度を可能にし、処理時間を大幅に短縮します。
- 低い焼結温度: 従来の方法よりも数百度低い温度で材料を焼結することができます。
- 高密度製品: このプロセスにより、高密度で均質な材料が得られ、要求の厳しい用途に適しています。
- 汎用性: SPSは、金属、セラミック、複合材料を含む幅広い材料の焼結に使用できる。
-
SPS装置のメーカー
- キンテック ソリューション SPS装置のトップメーカーであるキンテック社は、イノベーションと高品質のシステム性能を重視している。同社のシステムは、研究用途と産業用途の両方のニーズを満たすように設計されている。
- その他のメーカー Kintekは著名なメーカーであるが、他のメーカーもSPS装置を製造しており、様々な産業や研究ニーズに対応している。
-
SPSの用途
- 商業生産: SPSは、防護服、ロケットノズル、炭素繊維複合材などの製品を商業規模で製造するために使用されている。
- 研究開発: この技術は、新素材の開発や既存素材の改良に、研究所で広く使われている。
- ハイブリッド材料: SPSは、セラミックスと金属など、異なる物質の性質を組み合わせたハイブリッド材料の作製に特に有用である。
-
別称と誤解:
- SPSは、Field Assisted Sintering Technique (FAST)、Electric Field Assisted Sintering (EFAS)、Direct Current Sintering (DCS)などの別名でも知られている。
- 火花プラズマ焼結」という名称にもかかわらず、実際にはプラズマは使われていないことが研究により明らかになっている。この名称は誤用ですが、この技術が非常に効果的であることに変わりはありません。
-
従来の焼結を超える利点
- エネルギー効率: 焼結温度を下げ、処理時間を短縮することで、大幅なエネルギー節約を実現します。
- 材料の品質: 急速な加熱と冷却速度により、材料の微細構造が維持され、優れた機械的特性が得られます。
- プロセス制御: 電流と圧力を精密に制御できるため、焼結プロセスを微調整でき、安定した結果が得られる。
-
将来の展望
- 材料科学が進歩し続けるにつれて、SPS技術の需要は拡大すると予想される。高品質な材料を効率的に生産できるSPSは、研究・産業双方にとって貴重なツールである。
- 制御システムの強化や生産規模の拡大など、SPS装置の改良が進めば、その応用範囲はさらに広がるだろう。
要約すると、スパークプラズマ焼結は高効率で汎用性の高い焼結技術であり、従来の方法に比べて大きな利点があります。Kintek Solution社はSPS装置のトップメーカーであり、その革新的なアプローチと高品質のシステムで知られています。この技術は、研究および商業アプリケーションの両方で広く使用されており、材料科学が進化し続ける中、将来が有望視されている。
総括表
アスペクト | 詳細 |
---|---|
プロセス | パルスDCと一軸加圧により、粉体を高速で焼結します。 |
主な特徴 | 急速加熱・冷却、低い焼結温度、高密度製品 |
用途 | 防護服、ロケットノズル、炭素繊維複合材料、ハイブリッド材料。 |
利点 | エネルギー効率、優れた材料品質、精密なプロセス制御。 |
大手メーカー | 革新的で高品質なSPSシステムで知られるKintek Solution。 |
SPSがお客様の材料生産にどのような革命をもたらすか、検討する準備はできていますか? 今すぐご連絡ください までご連絡ください!