射出成形プロセスは、複雑な形状のプラスチック部品を大量に生産するために使用される非常に効率的な製造方法です。プラスチック材料を溶かし、プレス金型に射出する。 プレス金型 キャビティに高圧をかけ、冷却して固化させ、完成品を射出する。このプロセスは、その精密さ、再現性、複雑なデザインを作り出す能力のために、産業界で広く使用されています。以下は、射出成形プロセスの詳細なステップバイステップの説明です。
主なポイントを説明します:
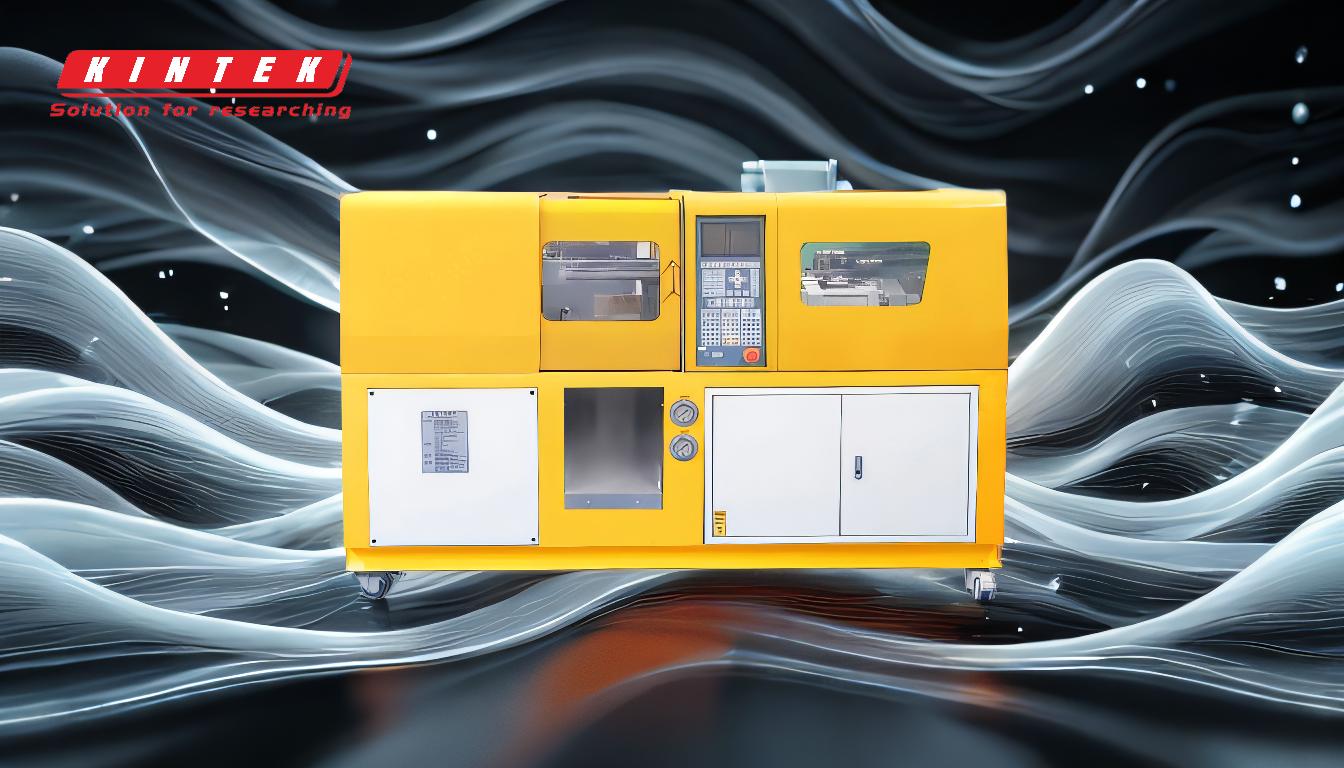
-
材料の準備と供給
- プラスチックペレットや顆粒は、射出成形機のホッパーに供給される。
- その後、材料はバレルに運ばれ、回転するスクリューによって加熱・混合されます。
- スクリューは、プラスチック材料の均一な溶融と均質化を保証します。
-
溶融と可塑化
- バレル内でプラスチック材料は融点まで加熱され、溶融状態になります。
- スクリューは溶融プラスチックを混合・圧縮し続け、粘度と温度を一定に保ちます。
- この工程は、高品質の成形品を得るために非常に重要です。
-
金型キャビティへの射出
- プラスチックが完全に溶けると、スクリューが前進し、プランジャーとして機能し、金型キャビティに溶融材料を注入します。
- 材料が複雑な形状を含む金型の細部まで充填されるように、高い圧力が加えられる。
- 射出圧力に耐えられるよう、金型はクランプ装置によって閉じられた状態に保たれます。
-
冷却と固化
- 金型キャビティが充填された後、溶融プラスチックは冷却固化を開始し、金型の形状になります。
- 冷却時間は、材料の特性、部品の厚み、金型の設計によって異なります。
- 反りやヒケなどの欠陥を防ぐには、適切な冷却が不可欠です。
-
型開きと排出
- 部品が固化すると金型が開き、エジェクターピンが完成品を金型キャビティから押し出します。
- 取り出された部品は、さらなる加工や包装のために回収される。
- 金型は再び閉じられ、次の部品のためのサイクルが繰り返されます。
-
後処理(必要な場合)
- 部品によっては、トリミング、塗装、組み立てなどの追加工程が必要な場合があります。
- これらのステップにより、最終製品が望ましい仕様と品質基準を満たすことが保証される。
詳しい説明
-
材料の準備と供給
この工程は、適切なプラスチック材料を選択することから始まる。プラスチック材料は通常、ペレット状または顆粒状である。これらの材料はホッパーに投入され、射出成形機のバレルに送り込まれる。バレルには回転スクリューが装備されており、材料を必要な温度まで加熱しながら前進させる。このステップにより、材料は次の段階である溶融と可塑化の準備が整います。 -
溶融と可塑化
バレル内でプラスチックは熱とスクリューによる機械的せん断を受ける。熱と摩擦の組み合わせによってプラスチックが溶け、粘性のある液体に変化します。スクリューの設計は、材料の不均一性を排除し、徹底的な混合を保証します。溶融プラスチックの品質は、強度、表面仕上げ、寸法精度などの最終製品の特性に直接影響するため、このステップは非常に重要です。 -
金型キャビティへの射出
プラスチックが完全に溶けたら、射出段階が始まります。スクリューが前進し、溶融材料を金型キャビティに射出するピストンとして機能する。金型は、部品の希望する形状を作り出すために精密に設計されています。射出時に高い圧力がかけられ、材料が細部や薄い部分を含む金型の全領域を満たすようにします。クランプユニットは、高い射出圧力に耐えられるよう金型をしっかりと閉じ、漏れや変形を防ぎます。 -
冷却と固化
金型キャビティが満たされた後、冷却段階が始まる。溶けたプラスチックが冷えて固まり、金型の形になる。冷却時間は、サイクルタイムを決定し、部品の品質に影響を与えるため、射出成形プロセスにおいて非常に重要な要素です。適切な冷却により、部品は均一に固化し、反り、ヒケ、内部応力などの欠陥を最小限に抑えることができます。金型内の冷却システムは、多くの場合、水路を使用し、温度を調整し、プロセスを高速化するのに役立ちます。 -
型開きと射出
部品が十分に冷えて固まったら、金型が開き、完成品が排出されます。金型キャビティから部品を押し出すために、エジェクターピンまたはプレートが使用されます。その後、金型が閉じ、次の部品のためにこのサイクルが繰り返される。このステップでは、部品が損傷なく排出され、金型が次の射出に備えることができるよう、正確さが要求されます。 -
後処理(必要な場合)
用途によっては、後加工が必要な部品もあります。これには、余分な材料(フラッシュ)のトリミング、美観を目的とした塗装やコーティング、複数の部品の組み立てなどが含まれます。後処理は、最終製品が要求される仕様と品質基準を満たすことを保証します。
結論
射出成形プロセスは、複雑な形状を持つ高品質のプラスチック部品を製造するための、多用途で効率的な方法である。材料の準備、溶融、射出、冷却、射出、後処理というステップを踏むことで、製造業者は一貫した正確な結果を得ることができます。このプロセスは、無駄を最小限に抑え、高い再現性で大量の部品を生産できることから、産業界全体で広く利用されている。
総括表
ステップ | 説明 |
---|---|
1.材料の準備 | プラスチックペレットをホッパーに投入し、加熱し、バレル内で混合する。 |
2.溶融と可塑化 | 材料はスクリューによって溶融され、均質化される。 |
3.金型への射出 | 溶融プラスチックを金型キャビティに高圧で射出する。 |
4.冷却と固化 | プラスチックは冷却され、望ましい形に固化する。 |
5.型開きと排出 | 金型が開き、エジェクターピンが完成品を押し出す。 |
6.後処理 | 最終的な品質を保つために、トリミングや塗装などの追加工程が必要になる場合があります。 |
製造工程を最適化する準備はできていますか? 今すぐご連絡ください 射出成形ソリューションの詳細について