スパッタリングと熱蒸着は、さまざまな産業で使用されている2つの異なる薄膜蒸着技術であり、それぞれ独自のメカニズム、利点、用途を持っている。スパッタリングでは、高エネルギーイオンを使用してターゲット材料から原子を物理的に離し、基板上に堆積させる。このプロセスは低温で作動するため、熱に弱い材料に適している。一方、熱蒸着は、ターゲット材料を加熱して蒸気流を発生させ、基板上に凝縮させる。この方法は、蒸着速度が速く、運転時間が短いことで知られており、迅速なコーティングを必要とする用途に理想的である。これらの手法のどちらを選択するかは、材料適合性、希望する膜特性、生産要件などの要因によって決まる。
キーポイントの説明
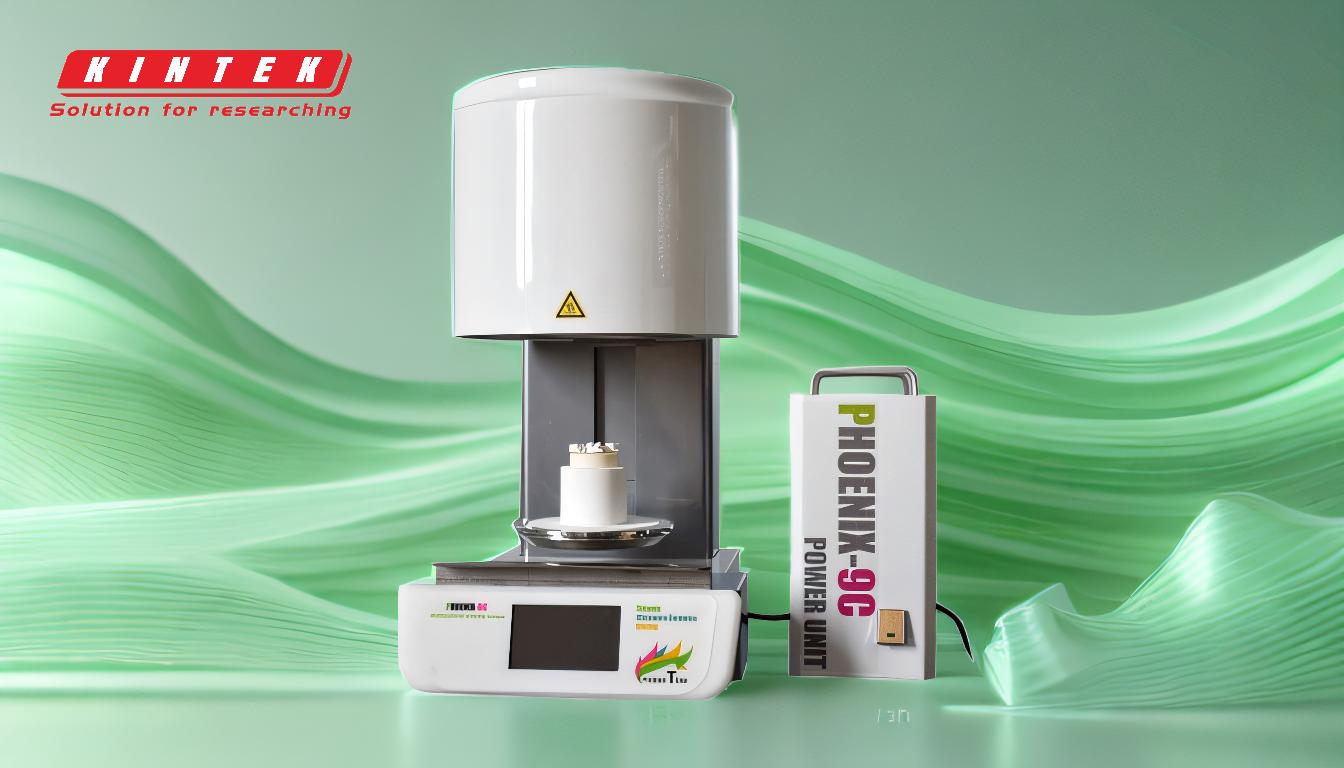
-
成膜のメカニズム
-
スパッタリング:
- 制御されたガス(通常はアルゴン)で満たされた真空チャンバー内のカソードに電気的に通電することで発生するプラズマを利用する。
- 陽電荷を帯びたガスイオンがターゲット材料に向かって加速され、原子や分子が物理的にはじき出される。
- 放出された原子は蒸気流を形成し、薄膜として基板上に堆積する。
-
熱蒸着:
- ターゲット材料を蒸発点まで加熱し、強力な蒸気流を発生させる。
- 蒸気は基板上に凝縮し、薄膜を形成する。
- このプロセスは、高温に耐えられる材料では、より速く、より効率的に行われることが多い。
-
スパッタリング:
-
温度感受性:
-
スパッタリング:
- 低温で動作するため、プラスチック、有機物、特定の金属など、熱に敏感な材料のコーティングに適している。
- 熱応力によって基材が損傷したり、材料特性が変化したりする可能性のある用途に最適。
-
熱蒸着:
- ターゲット材料を蒸発させるために高温が必要。
- 金属やセラミックなど、熱応力に耐えられる基板や材料に最適。
-
スパッタリング:
-
成膜速度と効率:
-
スパッタリング:
- 単原子または小さなクラスターを放出するため、熱法に比べて成膜速度が遅い。
- 膜厚と均一性を正確に制御できるため、高品質のコーティングを必要とする用途に最適。
-
熱蒸着:
- 堅牢な蒸気流を生成し、より高い蒸着速度と短い運転時間を可能にします。
- 大規模生産またはスピードが重要な用途でより効率的。
-
スパッタリング:
-
用途
-
スパッタリング:
- 薄膜トランジスタ、OLED、反射コーティングの作成など、電気および光学製造によく使用される。
- フィルム特性の精密な制御や、熱に敏感な基板との互換性を必要とする用途に適している。
-
熱蒸着:
- ソーラーパネル製造、ガラスコーティング、金属膜蒸着などの産業でよく使用される。
- 迅速なコーティングと高スループットが不可欠な用途に最適です。
-
スパッタリング:
-
材料適合性
-
スパッタリング:
- 高温を必要とせず、金属、合金、セラミックスなど幅広い材料を成膜できる。
- 熱蒸着が困難な材料に特に有効。
-
熱蒸着:
- 分解や劣化なしに蒸発させることができる材料に限定される。
- 蒸発点が明確な金属や単純な化合物に適している。
-
スパッタリング:
-
装置とプロセスの複雑さ:
-
スパッタリング:
- プラズマの生成と制御に特殊な装置を必要とするため、プロセスが複雑になり、コストが高くなる可能性がある。
- ターゲット材料や基板との互換性の点で柔軟性が高い。
-
熱蒸着:
- 主に発熱体と真空チャンバーが関与する、よりシンプルな装置セットアップ。
- 大量生産のためのスケールアップが容易だが、材料の選択肢という点では汎用性に劣る。
-
スパッタリング:
要約すると、スパッタリングと熱蒸着は相補的な技術であり、それぞれが特定のシナリオにおいて優れている。スパッタリングは精密、低温用途、熱に敏感な材料に好まれ、熱蒸着はその速度、効率、高温耐性基板への適合性から好まれる。両者の選択は、材料特性、希望する膜特性、生産上の制約など、プロジェクトの具体的な要件によって決まる。
総括表
側面 | スパッタリング | 熱蒸着 |
---|---|---|
メカニズム | 高エネルギーイオンを使用して、ターゲット材料から原子を離脱させる。 | ターゲット材料を加熱して蒸着用の蒸気流を作る。 |
温度感受性 | 低温で動作し、熱に敏感な素材に最適。 | 高温が必要で、熱に強い基板に適しています。 |
蒸着速度 | より低速ですが、膜厚と均一性を正確に制御できます。 | 蒸着速度が速く、ハイスループット用途に最適。 |
用途 | 電気/光学製造(例:OLED、薄膜トランジスタ)。 | ソーラーパネル、ガラスコーティング、金属膜蒸着 |
材料適合性 | 金属、合金、セラミック、熱に弱い素材に使用可能。 | 劣化させることなく蒸発させることができる材料に限る。 |
装置の複雑さ | 専用のプラズマ発生装置が必要で、セットアップが複雑。 | ヒーターと真空チャンバーによるシンプルなセットアップ。 |
適切な薄膜形成技術の選択にお困りですか? 当社の専門家に今すぐご連絡ください オーダーメイドのソリューションを