スパッタリングとイオンプレーティングは、どちらも薄膜形成に用いられる物理的気相成長(PVD)技術であるが、そのメカニズム、プロセス、用途は大きく異なる。スパッタリングは、通常反応性ガスから発生する高エネルギーのイオンをターゲットに照射して材料を放出し、放出された原子を基板上に堆積させます。対照的に、イオンプレーティングでは、高電流を使用して金属材料を蒸発させ、生成された金属イオンを基板上に誘導しながら、膜成長中に高エネルギーイオンを浴びせます。このボンバードメントが膜密度と密着性を高めるため、イオンプレーティングは硬い薄膜に適している。一方、スパッタリングは、プロセス温度が低いため、プラスチックやガラスを含む幅広い材料にコーティングできることで知られている。
ポイントを解説
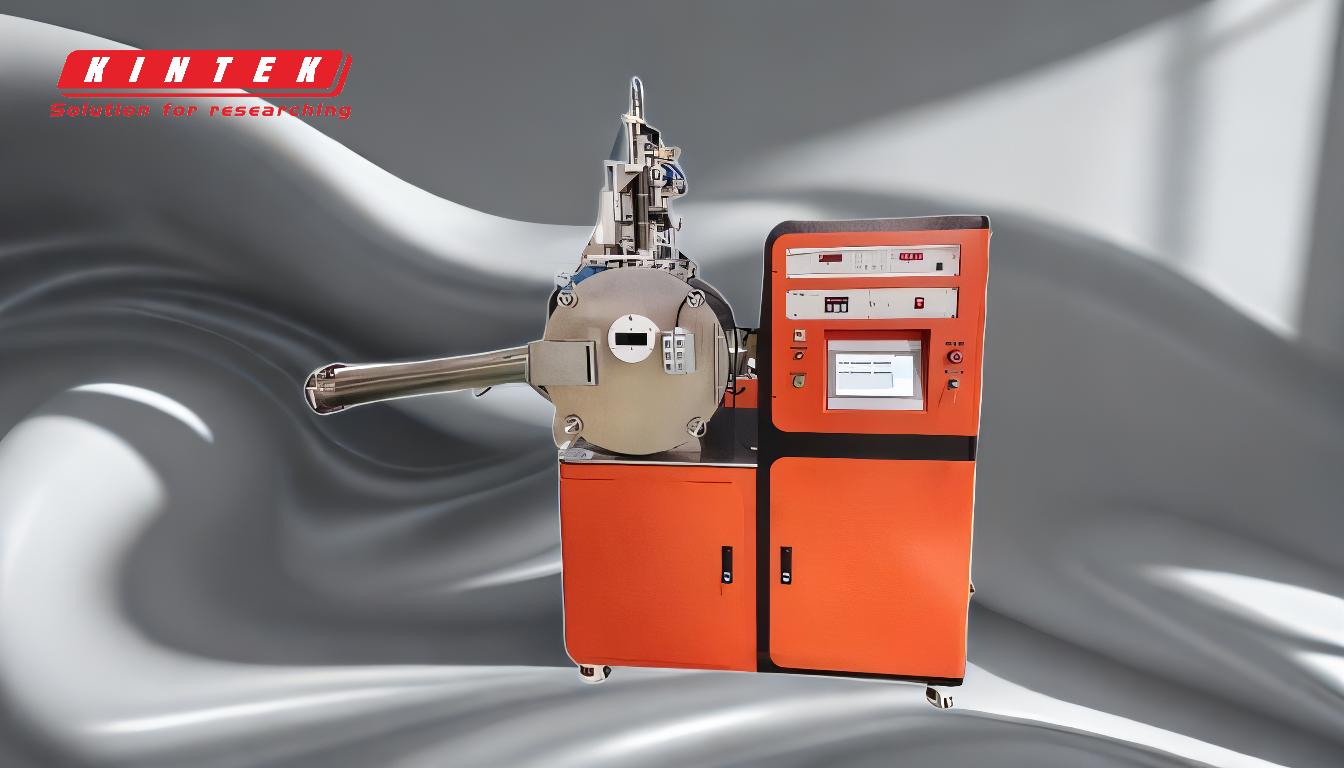
-
素材気化のメカニズム:
- スパッタリング:標的物質から原子を放出させるために、粒子(通常は気体イオン)を衝突させる運動量移動に依存する。このプロセスでは材料は溶解せず、代わりに原子がターゲットから物理的に叩き出される。
- イオンプレーティング:高電流を用いて金属材料を直接蒸発させる。その後、金属イオンを基板上に導き、膜特性を向上させるためにイオンボンバードメントを行うことが多い。
-
エネルギー源とプロセス条件:
- スパッタリング:他のPVD法と比べて低温で作動するため、プラスチックやガラスなど温度に敏感な基板に適している。磁場を利用して反応性ガスを導き、ターゲットに衝突させて材料を排出する。
- イオンプレーティング:高電流やイオン照射など、より高エネルギーのプロセスを伴う。その結果、バルク材料に近い特性を持つ高密度フィルムが得られ、硬い薄膜を必要とする用途に最適。
-
フィルム特性:
- スパッタリング:密着性が高く、結晶粒径が小さく、均質性の高い膜が得られる。このプロセスは、金属、合金、化合物を含む幅広い材料の成膜を可能にする。
- イオンプレーティング:成膜中に連続的または断続的にイオンを照射することで、膜の密度と密着性を向上させる。この技術は、化合物材料上の硬い薄膜の成膜に特に効果的です。
-
応用例:
- スパッタリング:半導体、光学、装飾用コーティングなど、精密な薄膜コーティングを必要とする産業で広く使用されている。温度に敏感な素材へのコーティングが可能なため、汎用性が高い。
- イオンプレーティング:切削工具、航空宇宙部品、耐摩耗性表面など、耐久性のある硬質皮膜を必要とする用途に適している。成膜中のイオンボンバードメントにより、皮膜の耐久性と性能が向上する。
-
プロセスパラメーター:
- スパッタリング:一般的に真空度が低く、純金属を除くほとんどの材料で成膜速度が低い。このプロセスの特徴は、高い密着性と膜中の吸収ガス量である。
- イオンプレーティング:フィルム特性を向上させるイオンボンバードメントを中心に、より高いエネルギーレベルで動作。プロセスにより方向性があり、膜厚と均一性をよりよく制御できる。
これらの主な違いを理解することで、装置や消耗品の購入者は、特定の用途のニーズに最も適した技術を、十分な情報に基づいて決定することができる。スパッタリングは汎用性とプロセス温度の低さを提供し、イオンプレーティングは膜密度と耐久性を向上させるため、要求の厳しい用途に最適である。
総括表
側面 | スパッタリング | イオンプレーティング |
---|---|---|
メカニズム | イオン衝撃による運動量移動で原子を放出。 | 高電流で物質を蒸発させ、イオン砲撃を行う。 |
エネルギー源 | 低温、磁場、反応性ガス。 | より高密度な膜には、大電流とイオンボンバード。 |
フィルム特性 | 高い密着性、小粒径、均質性。 | イオンボンバードメントにより密度と密着性が向上。 |
用途 | 半導体、光学、装飾コーティング、感温材料 | 切削工具、航空宇宙部品、耐摩耗性表面 |
プロセスパラメーター | より低い真空レベル、より低い蒸着速度、高い密着性。 | より高いエネルギーレベル、指向性蒸着、より優れた膜の均一性。 |
お客様の用途に適したPVD技術の選択にお困りですか? 当社の専門家に今すぐご連絡ください にお問い合わせください!