スパッタリングと蒸着は、基板上に薄膜を形成するために用いられる2つの異なる物理蒸着(PVD)技術である。どちらの手法も表面に材料を堆積させることを目的としているが、そのメカニズム、操作条件、結果において根本的に異なる。スパッタリングは、高エネルギーのイオンをターゲット材料に衝突させて原子を放出し、その原子が基板上に堆積する。対照的に、蒸発は材料が気化するまで加熱し、基板上に凝縮する蒸気流を形成する。これらの違いは、成膜速度、膜質、スケーラビリティ、アプリケーションの適合性に差異をもたらす。これらの違いを理解することは、特定の用途に適した技術を選択する上で極めて重要である。
キーポイントの説明
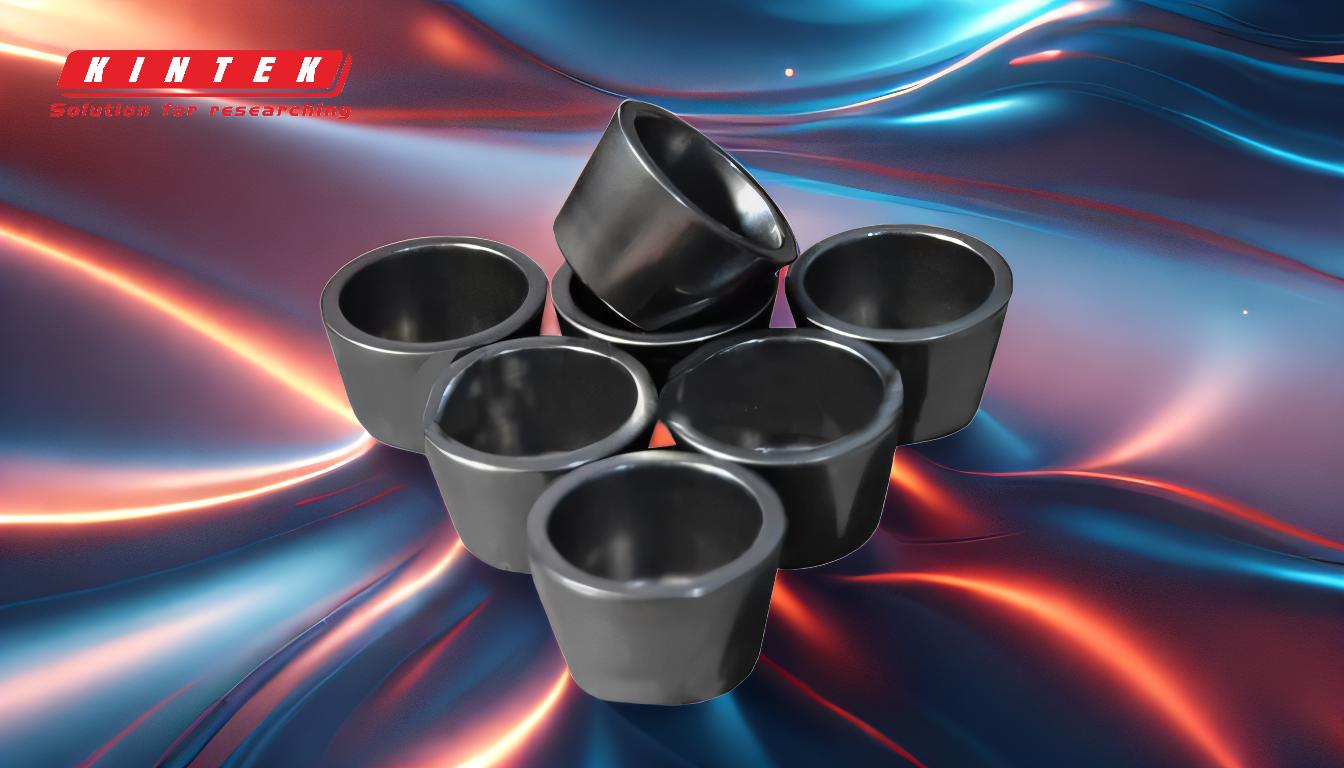
1. 析出のメカニズム
-
スパッタリング:
- 真空環境で高エネルギーイオン(通常はアルゴンイオン)をターゲット物質に照射する。
- 衝突によってターゲットから原子やクラスターが放出され、基板上に堆積する。
- このプロセスは非熱的で、加熱ではなく運動量移動に依存する。
-
蒸発:
- 熱エネルギーを使って、原料を気化温度に達するまで加熱する。
- 気化した材料は蒸気ストリームを形成し、基板まで視線方向に移動し、そこで凝縮する。
- 一般的な方法には、電子ビームで材料を加熱する電子ビーム蒸発法がある。
2. 運営状況
-
真空レベル:
- スパッタリングは比較的低い真空レベル(5-15 mTorr)で行われるため、スパッタされた粒子を熱化させる気相衝突が可能である。
- 蒸発には、気相の衝突を最小限に抑え、直接蒸気の流れを確保するための高真空環境が必要である。
-
蒸着率:
- 蒸着は一般に蒸着速度が速いため、短時間で厚いコーティングを必要とする用途に適している。
- スパッタリングは、純金属を除いて成膜速度は低いが、膜厚と均一性をよりよく制御できる。
3. フィルムの特徴
-
接着:
- スパッタリングは、蒸着粒子のエネルギーが高いため密着性が良く、基板との接合性が向上する。
- 蒸発膜は、特に融点の高い材料では、密着性が低くなることがある。
-
フィルムの均質性と粒径:
- スパッタリングでは、粒径が小さく均質性の高い膜が得られるため、膜特性の精密な制御が必要な用途に最適です。
- 蒸発によって粒径が大きくなり、均質性が低下する傾向があるが、要求の少ない用途では許容できる。
4. スケーラビリティと自動化
-
スパッタリング:
- 拡張性が高く、大量生産の自動化が可能なため、半導体製造のような産業用途に適している。
- 上方(トップダウン)から材料を堆積させることができるため、基板の配置や取り扱いの柔軟性が増す。
-
蒸発:
- 高真空と精密な熱制御が必要なため、拡張性は低い。
- 通常、ボトムアップ蒸着に限定されるため、基板の向きや取り扱いが制限される可能性がある。
5. 堆積種のエネルギー
-
スパッタリング:
- 蒸着粒子はエネルギーが高く、膜密度と密着性を高める。
- この高いエネルギーはまた、欠陥の可能性を減らし、フィルムの品質を向上させる。
-
蒸発:
- 蒸着粒子はエネルギーが低いため、膜の密度が低くなり、密着性が低下する可能性がある。
- しかし、これはデリケートな素材や熱に弱い素材を蒸着するのに有利に働く。
6. アプリケーション
-
スパッタリング:
- 光学コーティング、半導体デバイス、磁気記憶媒体など、高品質で均一な膜を必要とする用途によく使用される。
- 金属、合金、セラミックなど幅広い材料の蒸着に適している。
-
蒸発:
- 装飾コーティング、ソーラーパネル、特定の電子部品など、高い蒸着速度と厚いコーティングを必要とする用途に最適。
- 融点が低く、フィルムの品質要求がそれほど厳しくない材料に最適。
7. 吸収ガスと汚染
-
スパッタリング:
- チャンバー内にスパッタリングガス(アルゴンなど)が存在するため、ガス吸収の可能性が高い。
- これはフィルムの純度に影響を与える可能性があり、コンタミネーションを最小限に抑えるための追加ステップが必要になる場合がある。
-
蒸発:
- 高真空環境によるガス吸収の低減により、より純粋なフィルムが得られる。
- しかし、原料が不純物であったり、真空が損なわれていたりすると、やはり汚染は起こりうる。
8. 堆積の方向性
-
スパッタリング:
- 粒子はより分散し、方向性があるため、複雑な形状や凹凸のある表面をよりよくカバーできる。
- このため、スパッタリングは複雑な形状や高アスペクト比の基板のコーティングに適している。
-
蒸発:
- 粒子は視線方向の軌跡をたどるため、複雑な表面や凹んだ表面ではカバー範囲が制限されることがある。
- この方法は、平坦な形状や単純な形状に適している。
9. コストと複雑さ
-
スパッタリング:
- イオン源や磁場などの特殊な装置が必要なため、一般的に高価。
- このプロセスはより複雑で、イオンエネルギーとターゲット材料の特性を正確に制御する必要がある。
-
蒸発:
- 一般的に、特に小規模または研究用途では、コストが安く、セットアップも簡単である。
- しかし、高純度あるいは高スループットのシステムでは、コストが増大する可能性がある。
まとめると、スパッタリングと蒸発のどちらを選択するかは、膜質、成膜速度、基板形状、予算など、アプリケーションの具体的な要件によって決まる。スパッタリングは優れた膜質と拡張性を提供し、高性能アプリケーションに理想的である。一方、蒸着はより速い成膜速度と簡便性を提供し、それほど要求の高くないタスクや高スループットタスクに適している。
総括表:
アスペクト | スパッタリング | 蒸発 |
---|---|---|
メカニズム | ターゲットにイオンを衝突させ、蒸着用の原子を放出する。 | 材料を加熱して気化させ、蒸着用の蒸気流を形成する。 |
真空レベル | 低真空 (5-15 mTorr) | 高真空 |
蒸着率 | より低い(純金属を除く) | より高い |
接着 | 高エネルギー粒子による優れた接着性 | 特に高融点材料に対する接着性が低い。 |
フィルムの均質性 | 粒径が小さく、均質性が高い | 粒径が大きく、均質性が低い |
スケーラビリティ | 産業用途に適した高い拡張性 | スケーラビリティが低く、真空と熱制御の制約を受ける |
粒子のエネルギー | より高いエネルギー、より高密度な膜、より少ない欠陥 | 低エネルギー、低密度のフィルム |
アプリケーション | 光学コーティング、半導体、磁気ストレージ | 装飾用コーティング、ソーラーパネル、特定の電子機器 |
コスト | より高価で複雑なセットアップ | より安価でシンプルなセットアップ |
お客様の用途に適したPVD技術の選択にお困りですか? 専門家にご相談ください 個別指導のために!