焼きなましと焼きなましは、いずれも金属の物理的・化学的性質を変化させ、製造に適した状態にするための熱処理である。焼きなましは、金属を低温に加熱し、急速に冷却して靭性を向上させ、脆性を低減させるものであり、焼きなましは、金属を高温に加熱し、ゆっくりと冷却して材料を軟化させ、延性を向上させ、内部応力を緩和させるものである。どちらのプロセスも金属の機械的特性を向上させるために不可欠ですが、温度範囲、冷却速度、達成される具体的な結果が異なります。
キーポイントの説明
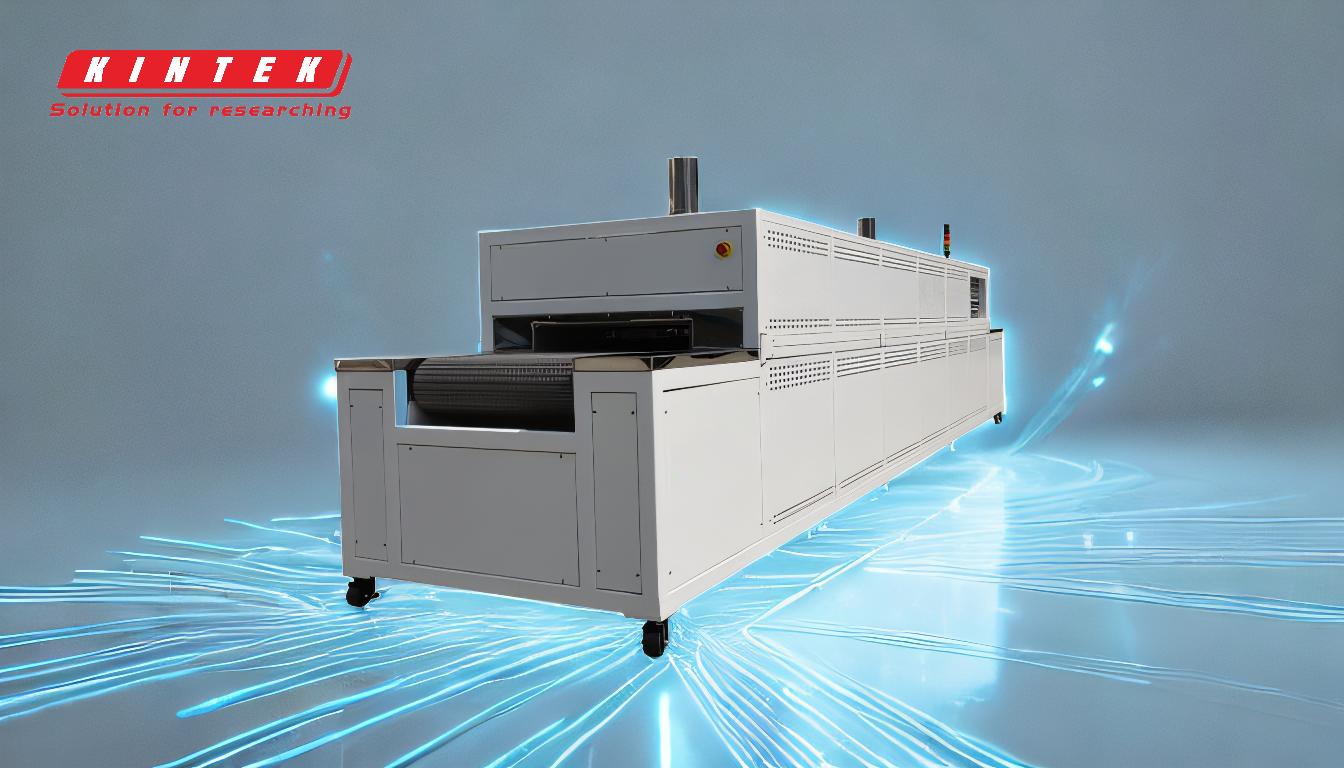
-
熱処理の定義と目的:
- 熱処理は、望ましい物理的・化学的特性を得るために、金属の加熱と冷却を制御する。
- 一般的な目的には、硬度、靭性、延性、応力除去の向上が含まれる。
- 焼戻しや焼なましのような工程は、焼入れ、焼入れ、焼ならしなど、より広範な熱処理方法の一部である。
-
焼きなまし:そのプロセスと成果:
- 温度範囲:焼きなましは通常高温で行われ、材料にもよるが、1,200°Fから2,400°Fの間で行われることが多い。
- 冷却速度:金属をゆっくり冷却する。多くの場合、炉の中で、あるいは断熱材の中に埋めて、微細構造を安定させる。
-
目的:
- 金属を軟化させ、機械加工や成形を容易にする。
- 延性を改善し、内部応力を低減する。
- 結晶粒組織を微細化し、機械的特性を向上させます。
- 用途伸線加工やシートメタル成形など、可鍛性や硬度低下が要求される製造工程で使用される。
-
焼戻し:そのプロセスと結果:
- 温度範囲:焼戻しは、焼入れのような硬化工程の後、通常300°F~1,000°Fの低温で行われる。
- 冷却速度:金属を焼鈍よりも速い速度で、多くの場合、空気中または油中で冷却する。
-
目的:
- 脆性を減らし、靭性を高める。
- 硬度と延性のバランスをとり、性能を向上。
- 焼入れ時の急冷による内部応力を緩和。
- 用途工具、バネ、強度と柔軟性の組み合わせを必要とする構造部品によく使用される。
-
焼戻しと焼きなましの主な違い:
- 温度:焼戻しは、焼きなましに比べて低温で行われる。
- 冷却速度:焼戻しでは冷却が速く、焼きなましでは冷却が遅い。
- 結果:焼戻しは靭性と応力除去に重点を置き、焼なましは軟化と延性に重点を置く。
-
一般的な熱処理方法:
- スルーハードニング:素材全体の硬度を高める。
- ケース焼入れ:表層のみを硬化させ、芯は柔らかくする。
- 焼き入れ:急冷することで高い硬度を得ることができるが、脆性が増す可能性がある。
- 焼ならし:焼鈍に似ているが、結晶粒組織を微細化するため冷却が速い。
- 浸炭:表面に炭素を添加し、硬度を高める。
-
制御された雰囲気の重要性:
- 熱処理では、酸化を防ぎ、均一な結果を得るために、特定の雰囲気(水素、窒素、アルゴンなど)を必要とすることが多い。
- 光輝焼鈍のようなプロセスでは、純粋な水素または窒素を使用して、表面の酸化を最小限に抑えます。
-
製造業への応用:
- アニーリング:銅線や鋼板など、成形や機械加工が必要な材料に使用される。
- 焼き戻し:ギア、ブレード、バネなど、硬さと靭性のバランスを必要とする部品に適用される。
-
応力緩和と均質化:
- 焼戻しと焼きなましはどちらも、機械加工、成形、溶接によって生じた内部応力を緩和することができる。
- 焼きなまし中の均質化により、材料全体の特性が均一になります。
-
材料特有の考慮事項:
- 異なる金属や合金は、最適な結果を得るために特定の熱処理パラメータを必要とします。
- 例えば、鋼は一般的に焼入れの後に焼き戻しを行いますが、アルミニウム合金は析出硬化を行う場合があります。
-
機械的特性の向上における役割:
- 焼戻しや焼きなましのような熱処理工程は、金属の望ましい機械的特性を達成し、特定の用途の性能要件を確実に満たすために重要です。
焼戻しや焼なましの原理と用途を理解することで、製造業者は適切な熱処理工程を選択し、金属の特性を用途に応じて最適化することができます。
総括表
側面 | 焼き戻し | アニール |
---|---|---|
温度範囲 | 300°F - 1,000°F | 1,200°F - 2,400°F |
冷却速度 | 速い(空気またはオイル) | 遅い(炉または断熱材) |
目的 | 靭性の向上、脆性の低減 | 金属を軟化させ、延性を向上させます。 |
用途 | 工具、バネ、構造部品 | 伸線、板金成形 |
適切な熱処理プロセスの選択にお困りですか? 今すぐ専門家にお問い合わせください !