バッチ式熱分解は、酸素のない状態で行われる熱分解プロセスで、密閉された固定バッチ式反応器内で有機物を加熱して低分子に分解し、気体、液体(バイオオイル)、固体残渣(チャー)を生成する。このプロセスは、様々な原料を価値ある製品に変換する能力があるため、廃棄物管理、エネルギー生産、化学合成に広く利用されている。反応器の設計、熱伝達メカニズム、運転パラメーターは、熱分解プロセスの効率と生産量を決定する上で重要な役割を果たす。
キーポイントの説明
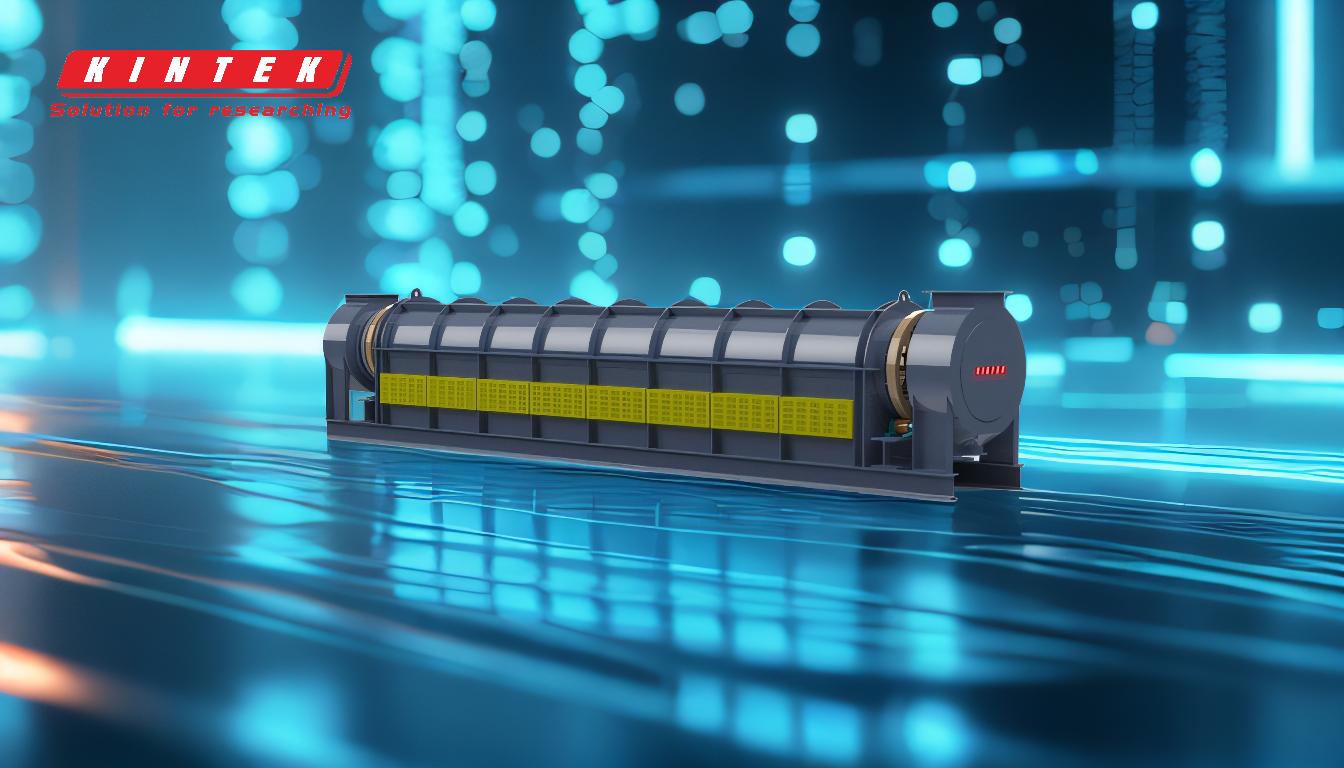
-
バッチ熱分解の定義とプロセス:
- バッチ式熱分解では、密閉された反応器に一定量の原料を投入し、酸素のない状態で加熱し、熱分解させる。このプロセスでは、バイオオイル、合成ガス、チャーという3つの主な出力が得られる。
- 酸素がないため燃焼が起こらず、原料は燃焼ではなく分解を受ける。このため、バッチ熱分解はバイオマス、プラスチック、ゴムなどの材料の処理に最適である。
-
熱分解リアクターの役割:
- その 熱分解リアクター は、原料の熱分解が行われるシステムの中核部品である。高温に耐え、酸素の侵入を防ぐために密閉された環境を維持するように設計されている。
- リアクターには、固定床式、流動床式、ワイヤーメッシュ式など様々な設計があり、それぞれ特定の用途や原料の種類に適している。
-
バッチ式熱分解リアクターの種類:
- 固定床リアクター:シンプルな密閉容器で、原料はベッドに置かれ、均一に加熱される。熱伝達は反応器の壁を通して行われ、一貫した熱分解を保証する。小規模な運転や研究目的に最適です。
- ワイヤーメッシュリアクター:このリアクターは金属グリッドを使用してサンプルを保持し、急速加熱と最小限の二次反応を可能にする。高速熱分解や実験的研究、特に脱揮やガス化などの熱分解の初期段階を調べるために一般的に使用されます。
-
熱分解リアクターシステムの構成要素:
-
システムは通常4つの主要部分から構成される:
- 駆動装置:原子炉の回転や移動に電力を供給する。
- ベース:原子炉を構造的に支える。
- 主炉:原子炉を格納し、必要な熱を供給する。
- ケーシング:システムを密閉し、安全性を確保し、熱損失を防ぎます。
-
システムは通常4つの主要部分から構成される:
-
バッチ式熱分解の利点:
- エネルギー安定性:バッチリアクターは、安定したエネルギー投入と出力を必要とするプロセスに最適です。
- 汎用性:バイオマス、プラスチック、ゴムなど幅広い原料に対応。
- シンプルさ:設計が単純なので、操作やメンテナンスが簡単です。
-
バッチ式熱分解の用途:
- 廃棄物管理:有機廃棄物を有用な製品に変換し、埋立地への依存を減らす。
- エネルギー生産:再生可能エネルギー源として利用可能なバイオオイルと合成ガスを生産。
- 化学合成:廃棄物から貴重な化学物質や原料を生成。
-
課題と考察:
- 熱伝達効率:反応器内の熱分布を均一にすることは、最適な分解に不可欠である。
- 原料の準備:効率的な熱分解を達成するためには、原料のサイズと含水率をコントロールする必要がある。
- 安全性:反応器が密閉型であるため、漏洩や爆発を防ぐための強固な安全対策が必要である。
要約すると、バッチ式熱分解は、有機物質を価値ある製品に変換するための、多用途で効率的なプロセスである。最適な性能、安全性、生産物の品質を確保するためには、熱分解リアクターの設計と運転が極めて重要である。バッチ熱分解の原理と構成要素を理解することで、関係者はこの技術を持続可能な廃棄物管理とエネルギー生産に効果的に活用することができる。
総括表
アスペクト | 詳細 |
---|---|
プロセス | 酸素がない状態での有機物の熱分解。 |
出力 | バイオオイル、合成ガス、チャー |
リアクターの種類 | 固定床、ワイヤーメッシュ、流動床リアクター。 |
主要構成部品 | 駆動装置、ベース、主炉、ケーシング。 |
利点 | エネルギーの安定性、汎用性、シンプルさ。 |
用途 | 廃棄物管理、エネルギー生産、化学合成。 |
課題 | 伝熱効率、原料準備、安全対策。 |
バッチ熱分解がどのように廃棄物を貴重な資源に変えるかをご覧ください。 今すぐ専門家にお問い合わせください !