熱蒸発源は、薄膜蒸着プロセス、特に物理蒸着(PVD)法で使用される装置である。ターゲット材料を蒸発点まで加熱して気化させ、基板上に凝縮させて薄膜を形成する。この技術は、精密で均一なコーティングを形成できることから、エレクトロニクス、光学、パッケージングなどの産業で広く利用されている。熱蒸着は、OLED、太陽電池、薄膜トランジスタなどの用途で金属やその他の材料を蒸着するのに特に有用である。
キーポイントの説明
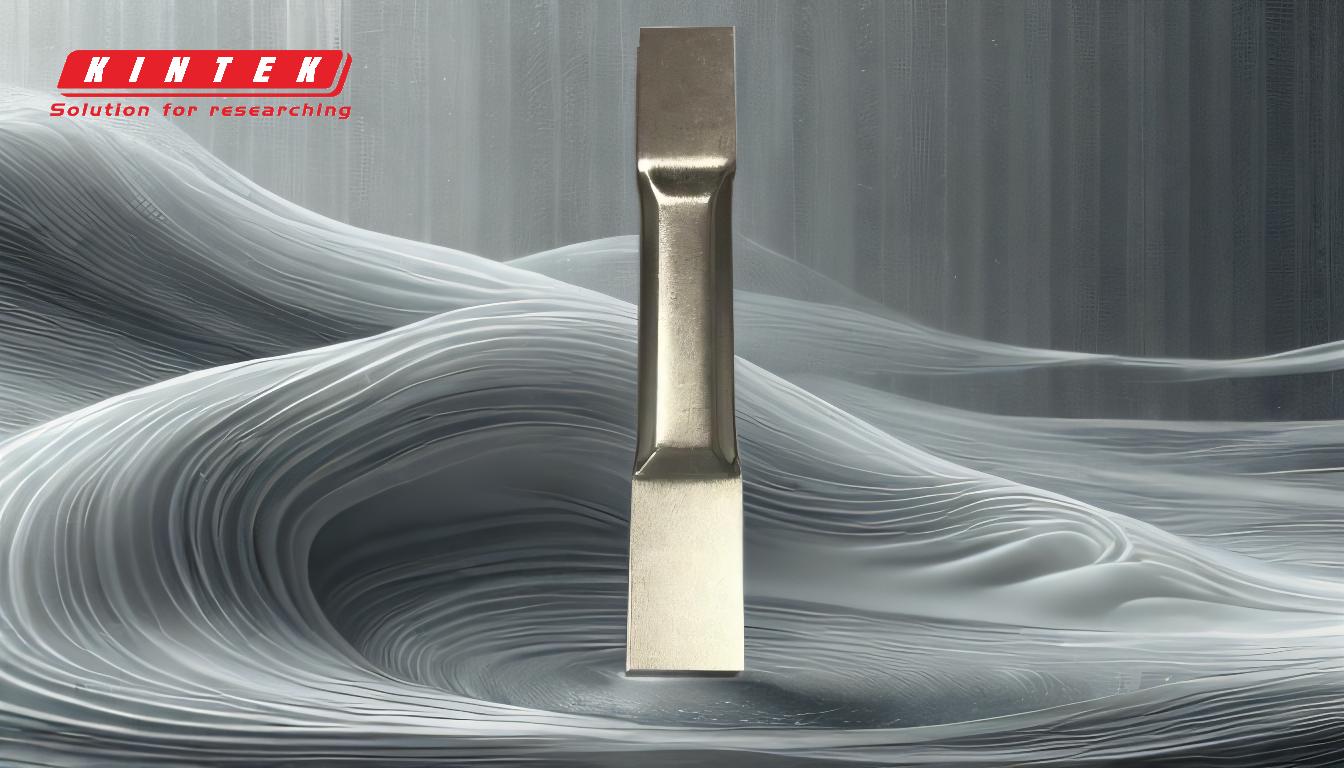
-
熱蒸発の定義とプロセス
- 熱蒸着は物理蒸着(PVD)の一形態で、ターゲットとなる材料を極端な高温に加熱して気化させる。
- 気化した材料は、真空または低圧環境を通過し、基板上に凝縮して薄膜を形成します。
- このプロセスはシンプルでありながら、均一で高品質なコーティングを形成するのに有効です。
-
熱蒸発システムの主要コンポーネント
- 蒸発源:通常、タングステンやグラファイトなど高温に耐えられる材料で作られたるつぼやボート。
- 加熱メカニズム:必要な蒸発温度を達成するために、抵抗加熱や電子ビーム加熱を行うことが多い。
- 真空チャンバー:コンタミネーションを防ぎ、効率的な材料搬送を可能にするために、管理された環境を確保します。
- 基板ホルダー:気化された材料を均一に受けるように基板を位置決めします。
-
熱蒸発の用途
- エレクトロニクス:OLED、薄膜トランジスタ、太陽電池の金属接合層の形成に使用。
- パッケージング:食品包装、断熱、装飾などの目的で、ポリマー上にアルミニウムなどの金属薄膜を成膜する。
- 航空宇宙と安全:NASAの宇宙服、消防士の制服、緊急用毛布に反射性と断熱性を目的として使用されている。
- 工業用途:航空機の帯電防止コーティングや防音エンクロージャーなど。
-
熱蒸発の利点
- 高純度:真空環境はコンタミネーションを最小限に抑え、高純度フィルムを実現します。
- 精度:膜厚と均一性を正確にコントロールできます。
- 汎用性:金属、合金、一部の有機化合物を含む幅広い材料に適している。
-
他の蒸着法との比較
- スパッタリング:熱蒸着とは異なり、スパッタリングはイオン化したガスを用いてターゲット材をアブレートする。
- 化学気相成長法(CVD):熱蒸着は純粋に物理的なものであるのに対し、CVDは化学反応によって成膜する。
- 電子ビーム蒸着:加熱に電子ビームを使用する熱蒸発のバリエーション。
-
装置購入時の考慮事項
- 材料の互換性:お客様のアプリケーションに必要な特定の材料と温度に対応できるシステムであることをご確認ください。
- 真空品質:最適なフィルム特性を得るためには、高品質の真空システムが不可欠です。
- スケーラビリティ:必要であれば、生産量を増やすためにシステムを拡張できるかどうかを検討する。
- メンテナンスと耐久性:部品、特に蒸発源と発熱体の寿命とメンテナンスの容易さを評価する。
熱蒸発法は、薄膜形成のための多用途で信頼性の高い方法であり、特に高純度と精度が要求される用途に適しています。より詳細な洞察については、以下をご覧ください。 熱蒸発 .
総括表:
アスペクト | 詳細 |
---|---|
定義 | 材料を加熱して気化させ、基板上に凝縮させるPVD法。 |
主な構成要素 | 蒸発源、加熱機構、真空チャンバー、基板ホルダー |
用途 | エレクトロニクス(OLED、太陽電池)、パッケージング、航空宇宙、工業用途。 |
利点 | 高純度、高精度、汎用性 |
他との比較 | スパッタリング(イオン化ガス)やCVD(化学反応)とは異なる。 |
バイヤーの考慮事項 | 材料適合性、真空品質、拡張性、メンテナンス。 |
サーマル・エバポレーションがお客様の薄膜プロセスをどのように強化できるかをご覧ください。 今すぐ専門家にお問い合わせください !