金型製作のプロセスにはいくつかの重要な段階があり、まず設計と構想の段階から始まり、そこで部品の3Dモデルが作成される。続いて、耐久性と性能を確保するために不可欠な金型の適切な材料を選択します。その後のステップには、金型設計の作成、CNC機械加工や3Dプリンターなどの技術を使った金型の製造、そして最後に、金型が必要な仕様を満たしていることを確認するためのテストと改良が含まれます。高品質な金型を製造するには、各工程で入念な計画と実行が必要です。
キーポイントの説明
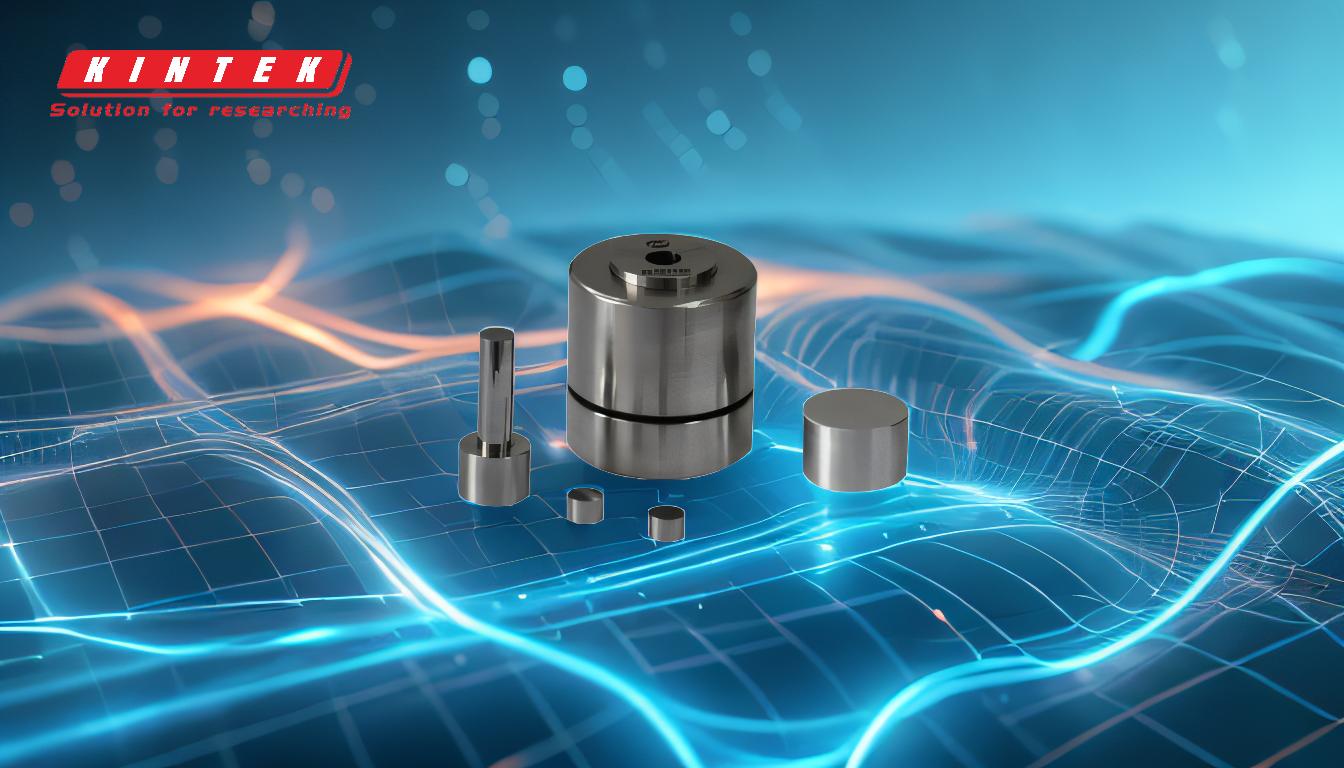
-
デザインと構想:
- 目的:この段階では、製造する部品の詳細な3Dモデルを作成します。これにより、金型が希望する形状と特徴を正確に再現できるようになります。
- 工程:エンジニアとデザイナーは、CAD(コンピュータ支援設計)ソフトウェアを使用して、部品の形状、材料の流れ、冷却要件などの要素を考慮しながらモデルを開発します。
- 成果:金型製作工程全体を導く正確な設計図。
-
材料選択:
- 重要性:金型に使用される材料は、高温や高圧を含む製造工程のストレスに耐えなければならない。
- 基準:熱伝導性、硬度、耐摩耗性などの要素が考慮される。一般的な材料には、スチール、アルミニウム、複合材料などがある。
- インパクト:適切な材料は、金型の寿命と最終製品の品質を保証します。
-
金型設計:
- 詳細:このステップでは、3Dモデルを金型設計に変換し、キャビティ、コア、冷却チャンネルを作成します。
- 考慮事項:設計者は、部品の突き出し、収縮、反りやエアトラップのような潜在的な欠陥を考慮する必要があります。
- 工具:高度なソフトウェアツールを使用して射出成形プロセスをシミュレートし、効率と品質のために設計を最適化します。
-
金型製造:
- テクニック:金型は通常、複雑さと素材に応じて、CNC機械加工、放電加工(EDM)、3Dプリンティングで製造される。
- 精度:金型部品が完全に適合し、最終製品が寸法公差を満たすためには、高い精度が要求されます。
- 品質管理:製造工程では、設計からの逸脱を検出し修正するために、厳格な品質チェックが行われます。
-
テストと改良:
- 目的:金型が製造されると、必要な仕様に適合した部品を製造するためのテストを受けます。
- 工程:初期テストランを実施し、製造された部品に欠陥がないか検査する。必要に応じて金型の調整が行われる。
- 最終仕上げ:テストに成功した後、金型は生産準備に入り、製造された部品の安定した品質を保証します。
これらのステップを綿密に踏むことで、メーカーは様々な産業で精密かつ信頼性の高い部品を製造するのに不可欠な高品質の金型を作ることができる。
総括表
ステップ | 主な内容 |
---|---|
デザインと構想 |
- CADソフトウェアを使用して3Dモデルを作成します。
- 部品の形状、材料の流れ、冷却を考慮する。 |
材料の選択 | - 熱伝導率や耐久性を考慮して、スチールやアルミニウムなどの素材を選択します。 |
金型設計 |
- 3Dモデルを金型設計に変換します。
- キャビティ、コア、冷却チャンネルを含む。 |
金型製造 |
- CNC機械加工、放電加工、3Dプリンターを使用。
- 精度と品質管理を保証します。 |
テストと改良 |
- 試運転を行い、部品を検査する。
- 仕様を満たすために金型を改良します。 |
あなたのプロジェクトに高品質の金型が必要ですか? 今すぐご連絡ください までご連絡ください!