熱分解は、酸素がない状態で起こる熱分解プロセスであり、有機物質を気体、液体、固体の生成物に変換する。熱分解の運転条件は、効率、生成物の分布、生成物の品質を決定する上で非常に重要である。主な要因には、温度、圧力、滞留時間、加熱速度、原料組成、粒子径などがある。これらの変数は、熱分解経路、生成物の収率、生成される気体、液体、固体フラクションの特性に影響を与える。これらの条件を理解し最適化することは、産業および環境用途で望ましい結果を得るために不可欠である。
キーポイントの説明
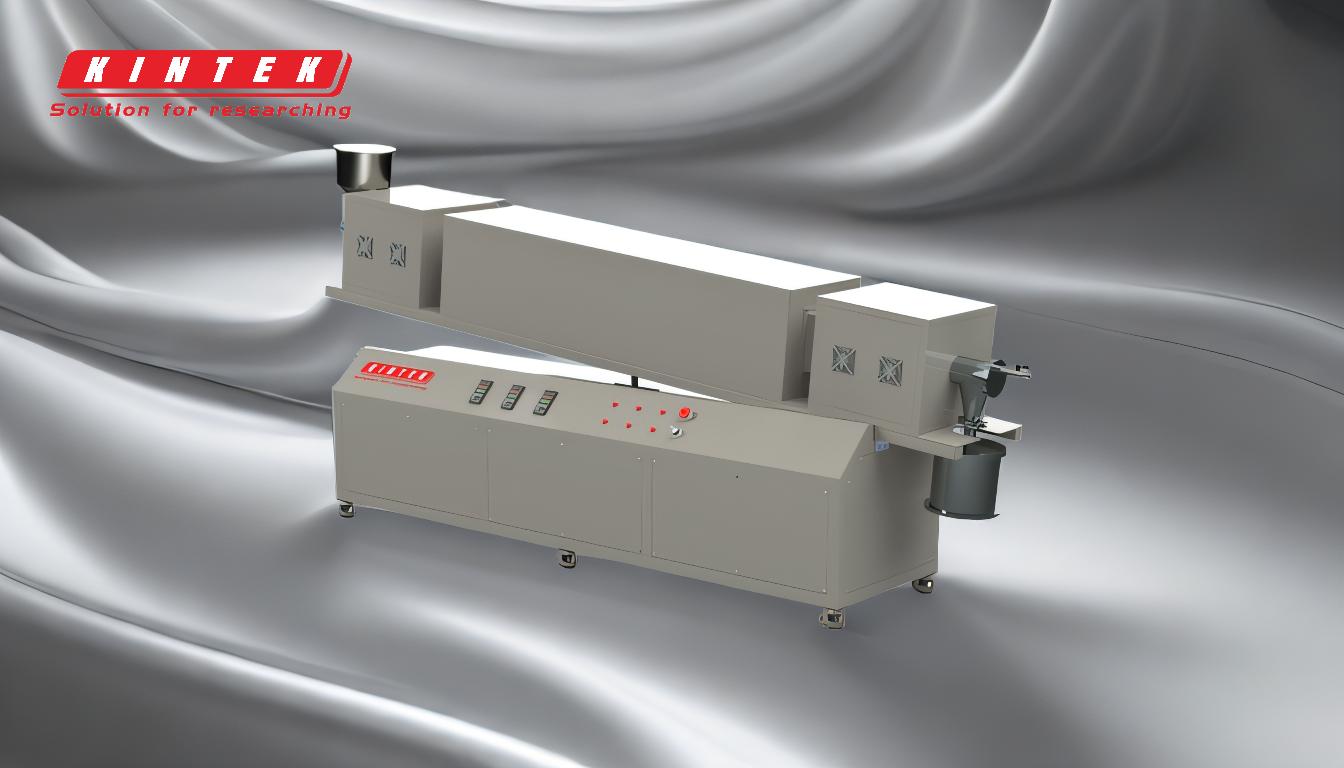
-
温度:
- 役割:温度は有機物の熱分解に直接影響するため、熱分解において最も重要な要素である。
-
影響:
- 高温(700℃以上):高分子化合物の完全分解による非凝縮性ガス(水素、メタンなど)の発生を促進する。
- 中温 (450-550°C):燃料や化学製品の製造に有用な液体有機製品(バイオオイル)の生成を促進する。
- 低温(400℃以下):チャーやコークスのような固形残渣が得られ、土壌改良や炭素隔離などの用途に有用である。
- 例:バイオマスの場合、450℃から550℃の温度がバイオオイルの収率を最大化するのに最適な温度である。
-
圧力:
- 役割:圧力は熱分解中の相挙動と反応速度論に影響する。
-
影響:
- 圧力上昇:縮合や重合などの二次反応を促進し、より高いチャー収率をもたらす。
- 減圧:二次反応を最小限に抑えることで、気体や液体の生成に有利。
- 例:真空熱分解では、液体収率を最大にし、炭化物の形成を減らすために、より低い圧力が使用される。
-
滞留時間:
- 役割:滞留時間とは、原料が熱分解反応器内に滞留する時間を指す。
-
影響:
- 長い滞在時間:より完全な熱変換を可能にし、ガス収率を高め、液体と固体の排出を減らす。
- 短い滞留時間:二次クラッキング反応を最小限に抑えることで、液体製品の製造を促進する。
- 例:高速熱分解プロセスでは、短い滞留時間(2秒未満)でバイオオイルの生産を最大化します。
-
加熱速度:
- 役割:原料の加熱速度は、分解経路と生成物の分布に影響を与える。
-
影響:
- 高加熱率:急速な熱分解を促進し、液体や気体の生成に有利。
- 低加熱率:よりゆっくり、より制御された分解により、炭化物の形成を促進する。
- 例:高速熱分解では、100~1,000℃/秒の加熱速度を採用し、バイオオイルの収率を最大化する。
-
原料組成:
- 役割:原料の化学的・物理的特性(含水率、揮発性物質、固定炭素など)は、熱分解の結果に大きく影響する。
-
影響:
- 高含水率:蒸発のための追加エネルギーを必要とするため、熱分解の効率を低下させる。
- 高揮発性物質:液体および気体製品の収率を高める。
- 高固定炭素:チャーのような固形残渣の生成を促進する。
- 例:セルロースとヘミセルロースを多く含むバイオマスはより多くのバイオオイルを生産し、リグニンを多く含む原料はより多くのチャーを生産する。
-
粒子サイズ:
- 役割:原料粒子の大きさは、熱伝達と反応速度論に影響する。
-
影響:
- より小さな粒子:熱伝達を促進し、より迅速で均一な熱分解と高い液体収率をもたらす。
- より大きな粒子:不完全分解のため、加熱が遅くなり、炭化物の生成が増加する。
- 例:高速熱分解では、熱伝導を最適化するために、原料は通常2mm以下の小さな粒径に粉砕される。
-
雰囲気:
- 役割:熱分解反応器内のガス環境は、反応経路に影響を与える可能性がある。
-
影響:
- 不活性雰囲気(窒素など):酸化を防ぎ、純粋な熱分解を保証します。
- 反応性雰囲気(蒸気など):二次反応によりガス収率を高め、生成物の組成を変えることができる。
- 例:水蒸気熱分解は、バイオマスからの水素製造を増加させるために使用される。
-
供給速度:
- 役割:原料を反応器に導入する速度は、プロセス全体の効率と製品分布に影響する。
-
影響:
- 高送り速度:分解が不完全になり、製品の品質が低下する可能性がある。
- 最適な供給率:一貫した熱変換を保証し、製品収率を最大化します。
- 例:連続熱分解システムでは、安定した運転条件を維持するために正確な供給量制御が必要です。
-
二次反応:
- 役割:二次反応(分解、重合など)は最初の熱分解の後に起こり、最終製品の組成に影響を与える。
-
影響:
- クラッキング:大きな分子を小さな分子に分解し、ガスの収率を高める。
- 重合:より大きな分子を形成し、チャーやタールの形成につながる。
- 例:高速熱分解では、二次分解反応を最小限に抑えることが、バイオオイルの収率を最大化するために極めて重要である。
-
環境と経済性への配慮:
- 役割:運転条件は、環境への影響(温室効果ガスの排出など)や経済的実現可能性も考慮しなければならない。
-
影響:
- エネルギー効率:温度、圧力、滞留時間を最適化することで、エネルギー消費と運転コストを削減できる。
- 排出コントロール:プロセス条件を適切に管理することで、温室効果ガスやその他の汚染物質の排出を最小限に抑えることができる。
- 例:廃熱回収システムを統合することで、熱分解プラントの全体的なエネルギー効率を向上させることができる。
これらの運転条件を注意深く制御することで、熱分解プロセスは、所望の特性を持つ特定の生成物(気体、液体、または固体)を生産するように調整することができ、廃棄物管理、再生可能エネルギー、および化学物質生産のための汎用性の高い価値ある技術となる。
総括表
ファクター | 役割 | 影響 | 例 |
---|---|---|---|
温度 | 熱分解に影響する。 | 高温では気体が、中温では液体が、低温では固体が好まれる。 | バイオマスからのバイオオイルには450~550℃が最適。 |
圧力 | 相挙動と反応速度論に影響する。 | 圧力を上げるとチャー収率が向上し、圧力を下げるとガスや液体生成物が有利になる。 | 真空熱分解は液体収率を最大化する。 |
滞留時間 | 原料が反応器内に滞留する時間。 | 長時間はガス収率を高め、短時間は液体生成に有利。 | 高速熱分解は、バイオオイルに2秒未満を使用する。 |
加熱速度 | 原料の加熱速度は分解経路に影響する。 | 高い加熱速度は液体とガスを促進し、低い加熱速度は炭化物の形成を促進する。 | 高速熱分解はバイオオイルに100-1,000℃/秒を使用する。 |
原料組成 | 化学的/物理的特性が結果に影響する。 | 揮発分が多いと液体/ガスが増加し、固定炭素が多いとチャーが増加する。 | セルロースを多く含むバイオマスはバイオオイルを多く生産する。 |
粒子径 | 熱伝達と反応速度に影響。 | 小さな粒子は熱伝達と液体収率を高め、大きな粒子は炭化物の生成を増加させる。 | 高速熱分解では2mm以下の粒子を使用します。 |
雰囲気 | 気体環境は反応経路に影響する。 | 不活性雰囲気は酸化を防ぎ、反応性雰囲気(水蒸気など)はガス収率を高める。 | 水蒸気熱分解は水素発生量を増加させる。 |
供給速度 | 原料の投入率は、効率と製品の品質に影響する。 | 高い率は品質を低下させるが、最適な率は安定した変換を保証する。 | 連続システムは正確な供給率制御を必要とする。 |
二次反応 | 分解後に起こり、最終製品の組成に影響を与える。 | クラッキングはガスを増加させ、重合はチャー/タールにつながる。 | クラッキングを最小化することで、高速熱分解のバイオオイルを最大化する。 |
環境/経済性 | 排出量と実現可能性を考慮。 | 最適化された条件は、エネルギー使用と排出を削減し、廃熱回収は効率を向上させる。 | 熱回収システムを統合することで、プラントの効率が向上します。 |
熱分解プロセスを最適化する準備はできましたか? 当社の専門家に今すぐご連絡ください オーダーメイドのソリューションを