電着は、コーティングや材料製造に広く使用されているが、その効率、コスト、環境フットプリントに影響を与えるいくつかの欠点がある。主な欠点には、材料適合性の制限、高いエネルギー消費、不均一なコーティング膜厚、有毒な副産物による環境への懸念、複雑な形状で均一な成膜を達成するための課題などがある。さらに、このプロセスではパラメーターを正確に制御する必要があることが多く、操作の複雑さとコストが増大する可能性がある。これらの制限により、電着は特定の用途、特に高精度、環境持続性、費用対効果を必要とする用途には適していない。
キーポイントの説明
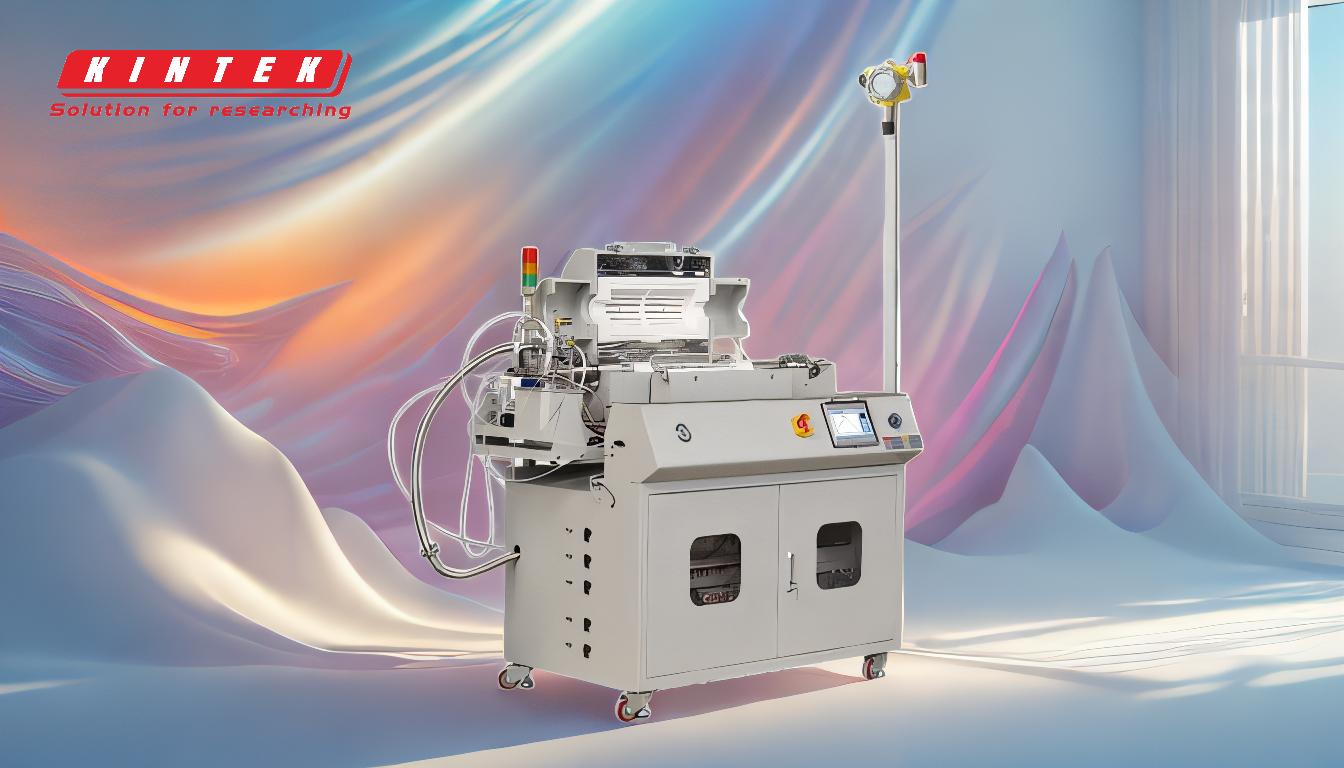
-
限られた材料適合性
- 電解析出は、基板上にイオンを析出させる電流の流れに依存するため、主に導電性材料に適している。
- 非導電性材料は、追加の前処理(例えば、メタライゼーション)を必要とし、コストと複雑さを増加させる。
- また、材料によっては電解液と不利に反応し、接着不良や汚染につながることもあります。
-
高いエネルギー消費
- このプロセスでは、電気化学反応を維持するために継続的な電気エネルギーの供給が必要である。
- エネルギーコストは、特に大規模または長時間の運転の場合、大きなものになる可能性がある。
- 電解液や基材の抵抗など、プロセスにおける非効率性は、エネルギー消費をさらに悪化させる可能性がある。
-
不均一な膜厚
- 電解析出では、特にエッジやコーナー、複雑な形状で、膜厚が不均一になることがよくあります。
- この現象は "エッジ効果 "として知られ、電界が鋭利な特徴に集中するため、その部分の析出が速くなるために起こります。
- 均一な厚さを達成するには、マスキングや後処理などの追加工程が必要になる場合があり、時間とコストが増加します。
-
環境への懸念
- このプロセスでは、重金属や有害化学物質を含む有毒な副産物が発生するため、環境汚染を防ぐために慎重に管理しなければならない。
- 廃水処理と使用済み電解液の処分は、操業コストと規制遵守の負担を増大させる。
- シアン系電解液のような環境に有害な物質の使用は、これらの問題をさらに悪化させる。
-
複雑な形状の課題
- 電着は、複雑な形状や深い凹部を持つ基板に均一なコーティングを施すのに苦労します。
- 遮蔽効果により、手の届きにくい場所での十分な成膜が妨げられ、不完全な被覆につながることがあります。
- この制限により、すべての表面にわたって正確で一貫したコーティングを必要とする用途での使用が制限される。
-
操作の複雑さとコスト
- このプロセスでは、電圧、電流密度、温度、電解液組成などのパラメーターを正確に制御する必要がある。
- これらの条件を維持するには、高度な機器と熟練した人材が必要で、運転コストが増大する。
- 機器の定期的なメンテナンスと電解質の補給は、さらに経費を増加させる。
-
欠陥の可能性
- 一般的な欠陥には、ピンホール、ブリスター、密着不良などがあり、コーティングの品質と耐久性を損なう可能性があります。
- このような欠陥は、電解液中の不純物、不適切な下地処理、プロセスパラメーターの変動などから発生することが多い。
- 欠陥に対処するためには、部品の再加工や廃棄が必要となり、材料の浪費やコスト増につながる可能性があります。
-
蒸着速度の制限
- 電着は、物理的気相成長法(PVD)や溶射など、他のコーティング法に比べて一般的に速度が遅い。
- 析出速度が遅いことは、大量生産環境ではボトルネックになり得る。
- 成膜速度を上げるには、より高い電流密度が必要になることが多く、粗さや多孔性などの品質問題につながる可能性がある。
-
基板の導電性への依存性
- プロセスが効果的に機能するためには、基板が導電性でなければならない。
- 非導電性基板は、導電層を塗布するなどの前処理工程が必要で、時間とコストがかかる。
- 前処理を行ったとしても、良好な接着性と均一性を達成するのは困難な場合がある。
-
健康と安全のリスク
- 危険な化学薬品や高電圧機器の使用は、作業員にリスクをもたらす。
- 保護具や換気システムなどの適切な安全対策は不可欠だが、作業の複雑さとコストを増大させる。
- 有毒物質や電気的危険への偶発的な暴露は、深刻な健康・安全事故につながる可能性がある。
これらのデメリットを理解することで、装置や消耗品の購入者は、電着が特定の用途に適しているかどうかについて、十分な情報を得た上で決定することができます。コスト、環境への影響、または精度が重要な要素である場合には、別のコーティング方法がより適切である可能性があります。
総括表
デメリット | 主な詳細 |
---|---|
限られた材料適合性 | 非導電性基板は前処理が必要。 |
高いエネルギー消費 | 継続的に電気エネルギーを必要とするため、運転コストが高くなる。 |
不均一な膜厚 | 特にエッジや複雑な形状での不均一な成膜。 |
環境への懸念 | 有毒な副産物が発生し、コストのかかる廃棄物管理が必要になる。 |
複雑な形状の課題 | 複雑な形状や深い凹部への均一なコーティングに苦労しています。 |
操作の複雑さ | パラメータを正確に制御する必要があり、コストと複雑さが増す。 |
欠陥の可能性 | ピンホール、ブリスター、接着不良などのリスクがある。 |
蒸着速度の制限 | 他のコーティング法に比べて遅いため、大量生産に影響する。 |
基板の導電性への依存性 | 非導電性基板は前処理が必要で、時間とコストがかかる。 |
健康と安全のリスク | 危険な化学薬品や高電圧機器を使用するため、安全対策が必要です。 |
より良いコーティングソリューションをお探しですか? 当社の専門家にご連絡ください。 にご相談ください!