PVD(Physical Vapor Deposition)とCVD(Chemical Vapor Deposition)は広く使われている2つの薄膜蒸着技術で、それぞれメカニズム、材料、用途が異なります。PVDは、一般的に蒸発やスパッタリングなどの方法で材料を物理的に蒸発させ、真空環境で基板上に堆積させる。一方、CVDはガス状の前駆物質と基板との化学反応に依存し、反応を促進するために高温を必要とすることが多い。どちらの方法も半導体、光学、コーティングなどの産業で使用されているが、成膜速度、基板温度要件、膜質、大量生産への適合性などの点で異なる。これらの違いを理解することは、特定の用途に適した方法を選択する上で極めて重要である。
キーポイントの説明
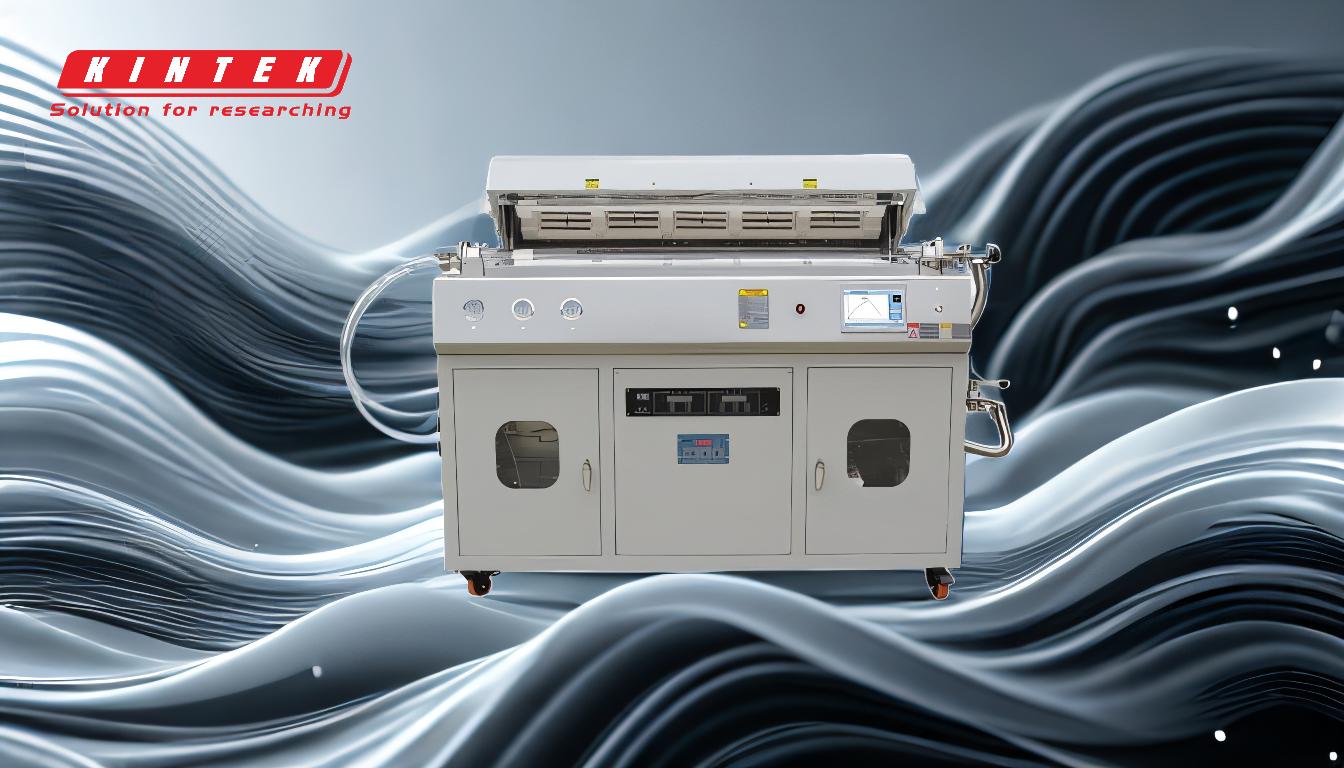
-
成膜メカニズム:
- PVD:蒸発法、スパッタリング法、電子ビーム法などの物理的プロセスを用いて固体材料を蒸発させ、基板上に凝縮させる。このプロセスは真空環境で行われるため、汚染を最小限に抑えることができる。
- CVD:ガス状の前駆物質と基板との化学反応に頼る。ガスは加熱された基板表面で反応または分解し、固体膜を形成する。このプロセスは、熱的に活性化することも、プラズマで強化することもできる。
-
材料の範囲:
- PVD:金属、合金、セラミックスなど、さまざまな材料を成膜できる。ただし、半導体にはあまり使われない。
- CVD:金属、セラミックス、半導体など幅広い材料を成膜できる。CVDは高純度の膜を作ることができるため、特に半導体用途に適している。
-
成膜速度:
- PVD:一般的にCVDに比べて成膜速度は低い。しかし、電子ビームPVD(EBPVD)のような特定のPVD法は、高い蒸着速度(0.1~100μm/分)を達成することができます。
- CVD:一般に成膜速度が速いため、厚膜や高スループットを必要とする用途に適している。
-
基板温度:
- PVD:多くの場合、基板を加熱する必要がないため、温度に敏感な材料に適している。プロセスは比較的低温で実施できる。
- CVD:通常、化学反応を促進するために高い基板温度を必要とするため、温度に敏感な材料への使用が制限されることがある。
-
膜質:
- PVD:フィルムの表面平滑性と密着性が向上する傾向があり、表面特性の精密な制御が必要な用途に最適。
- CVD:フィルムは一般的に高密度で、特に複雑な形状において、より優れた被覆性を提供します。ただし、CVD膜は化学反応により不純物を含むことがある。
-
大量生産への適性:
- PVD:成膜速度が速く、より大きな基板を扱えるため、大量生産に適していることが多い。また、有毒な化学薬品に依存しないため、より安全で扱いやすい。
- CVD:大量生産が可能だが、CVDは高温と腐食性ガスが必要なため、プロセスが複雑になり、運用コストが高くなる可能性がある。
-
環境と安全への配慮:
- PVD:有毒化学物質を使用せず、腐食性の副産物も発生しないため、安全で取り扱いが容易。プロセスは真空中で行われるため、環境への影響を最小限に抑えることができる。
- CVD:有毒ガスや有害ガスを使用する可能性があり、腐食性の副生成物を生成する可能性があるため、慎重な取り扱いと廃棄が必要。
これらの主な違いを理解することで、装置や消耗品の購入者は、半導体製造、光学コーティング、その他の産業用途など、それぞれのニーズに最も適した成膜方法を、十分な情報を得た上で決定することができる。
要約表
側面 | PVD | CVD |
---|---|---|
成膜メカニズム | 真空環境下での物理的プロセス(蒸発、スパッタリング)。 | ガス状前駆体と基板間の化学反応。 |
材料 | 金属、合金、セラミックス。半導体では一般的でない。 | 金属、セラミックス、半導体。高純度膜に最適。 |
蒸着速度 | EBPVDでは0.1~100μm/min。 | レートが高く、厚膜や高スループットに適している。 |
基板温度 | 低温、高感度材料に適している。 | 高温が必要なため、高感度材料での使用は制限される。 |
フィルム品質 | 表面の平滑性と密着性が向上する。 | より緻密なフィルムでカバー力が高いが、不純物を含む場合がある。 |
大量生産 | 効率的で安全、取り扱いが容易。 | 可能だが、複雑な工程と高いコストを伴う。 |
環境安全性 | より安全で、有毒化学物質や腐食性副産物がない。 | 有毒ガスや腐食性副生成物が発生する可能性がある。 |
PVDとCVDの選択でお困りですか? 当社の専門家にお問い合わせください。 にご相談ください!