スパッタリングは薄膜成膜に広く使用されている技術であるが、その効率、コスト、特定の用途への適性に影響するいくつかの顕著な欠点がある。これらの欠点には、高い設備投資、材料によっては低い成膜速度、潜在的な膜汚染、膜厚と均一性の制御における課題などが含まれる。さらに、スパッタリングには複雑な装置や冷却システムが必要な場合が多く、運用コストが上昇し、生産率が低下する可能性がある。このプロセスはまた、特定の材料、特にイオン衝撃で分解する可能性のある有機固体との相性が悪い。さらに、スパッタリングは基板に不純物を混入させる可能性があり、その拡散輸送メカニズムは膜構造化のためのリフトオフプロセスとの統合を複雑にする。
要点の説明
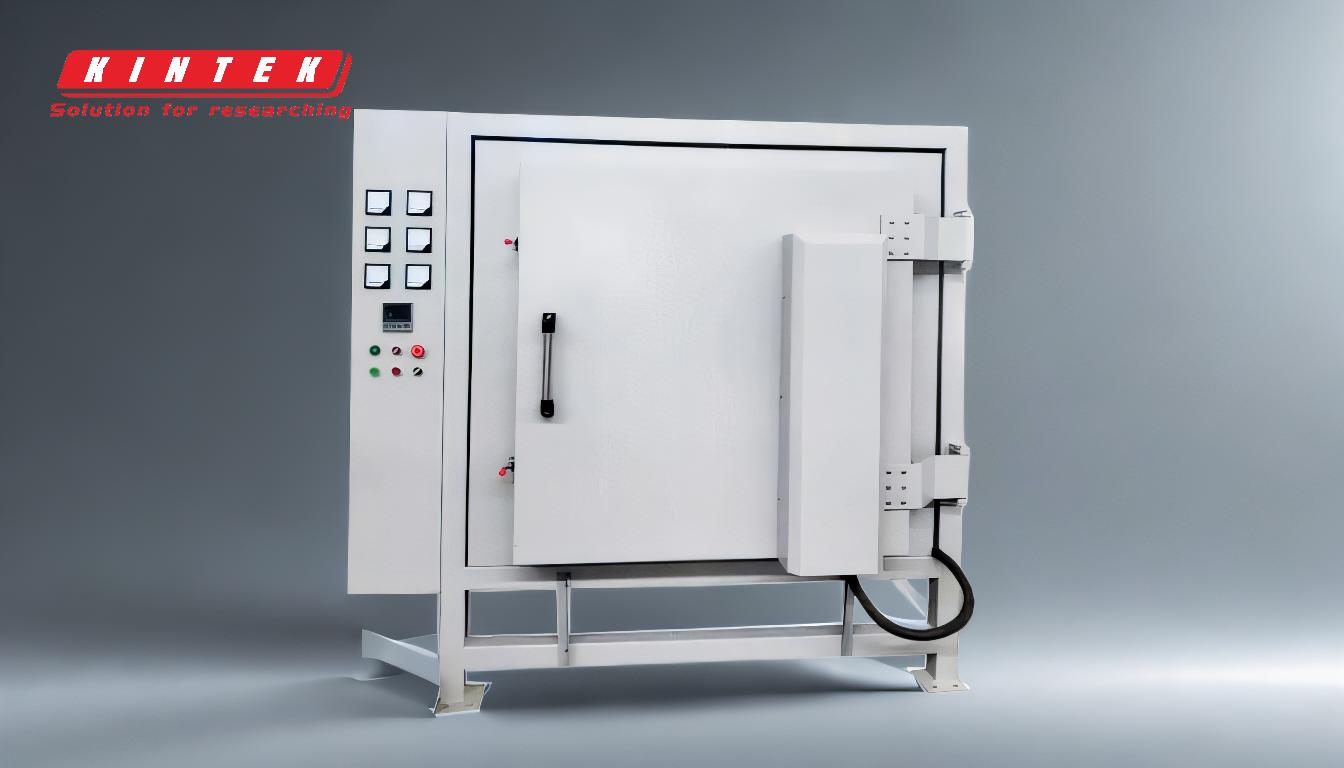
-
高額な設備投資:
- スパッタリング装置は高価であることが多く、多額の先行投資を必要とする。これには、高圧装置、冷却システム、その他の特殊部品のコストが含まれる。
- 冷却システムの必要性は、初期資本コストを増加させるだけでなく、継続的なエネルギー費用を増加させ、プロセスの全体的な費用対効果を低下させる。
-
低い蒸着率:
- スパッタリングは一般に、熱蒸発法などの他の技法に比べて成膜速度が低い。これは特にSiO2のような特定の材料に当てはまり、生産速度を低下させる。
- スパッタリングレートが低いと、スピードが重要な高スループット製造環境では大きな制約となる。
-
膜の汚染:
- スパッタリングの大きな欠点の一つは、膜汚染のリスクである。ターゲット材料やスパッタリング環境からの不純物が膜に混入し、膜の品質を劣化させる可能性がある。
- プラズマ中のガス状汚染物質が活性化して成長膜に取り込まれることもあり、汚染のリスクがさらに高まる。
- 反応性スパッタ蒸着では、汚染につながるターゲット被毒を防ぐため、ガス組成を注意深く制御する必要がある。
-
膜厚と均一性の制御の難しさ:
- スパッタリングでは、蒸着フラックスの分布が均一でないため、均一な膜厚を達成することが困難な場合があります。このため、均一なコーティングを確保するために、移動治具を使用する必要がしばしば生じる。
- スパッタされた原子の拡散輸送により、完全なシャドーイングを達成することが難しく、膜構造化のためのリフトオフプロセスとの統合を複雑にしている。
-
材料の限界:
- 一部の材料、特に有機固体は、スパッタリング・プロセス特有のイオン衝撃によって劣化しやすい。このため、この技法で効果的に成膜できる材料の範囲が制限される。
- また、融点が非常に高い材料はスパッタリングに適さない場合があるため、コーティング材料の選択は融点によっても制約を受ける。
-
不純物の導入:
- スパッタリングは蒸着に比べて真空度が低いため、基板に不純物が混入する可能性が高くなる。このため、蒸着膜の純度や性能に影響を及ぼす可能性がある。
-
複雑な設備とメンテナンス:
- スパッタリングプロセスには、高圧装置や冷却システムを含む複雑な装置が必要であり、保守や操作が困難な場合がある。
- ユーザーによるメンテナンスの必要性やプロセスパラメーターの制限が、産業用途でのスパッタリングの使用をさらに複雑にしている。
-
高い基板温度上昇:
- スパッタリング工程は、基板温度の大幅な上昇を引き起こす可能性があり、温度に敏感な材料や用途には望ましくない場合がある。
- ま た 、こ の 温 度 上 昇 は 、基 板 を 不 純 物 ガ ス に よ っ て 汚 染 さ れ や す く す る こ と も あ る 。
要約すると、スパッタリングは多用途で広く使用されている成膜技術であるが、用途によってはその有効性を制限するいくつかの欠点がある。これには、高コスト、低い成膜速度、汚染リスク、膜特性の制御の難しさ、材料の制限、複雑な装置要件などが含まれる。これらの欠点を理解することは、特定の用途に適した成膜方法を選択し、スパッタリングプロセスを最適化してその制約を緩和する上で極めて重要である。
総括表:
デメリット | デメリット |
---|---|
高額な設備投資 | 高価な装置と冷却システムにより、初期費用と継続費用が増加する。 |
低い蒸着速度 | SiO2のような材料では蒸着速度が遅いため、高スループット生産が制限される。 |
膜の汚染 | ターゲットやプラズマからの不純物は、フィルムの品質を劣化させます。 |
膜厚制御 | 不均一な蒸着フラックスは均一なコーティングの達成を困難にする。 |
材料の制限 | 有機固体はイオン衝撃で分解するため、高融点材料は適さない。 |
不純物の導入 | 真空度が低いと基板の不純物リスクが高まる |
複雑な装置 | 高圧装置や冷却システムには多大なメンテナンスが必要です。 |
基板の温度上昇 | 温度に敏感な材料は、スパッタリング中に発生する熱によって劣化する可能性があります。 |
適切な薄膜形成方法の選択についてお困りですか? 当社の専門家に今すぐご連絡ください オーダーメイドのソリューションを