スパッタコーティングは、物理的気相成長法(PVD)の一つで、基板上に薄膜を蒸着させる技術である。真空環境で行われ、ターゲット材料に高エネルギーイオン(通常はアルゴン)が照射され、ターゲットから原子が放出され、基板上に蒸着される。このプロセスでは、プラズマを発生させ、ターゲットに向けてイオンを加速し、専用の冷却システムで熱を管理する。この方法は、強力な原子レベルの結合を持つ均一で高品質なコーティングを生成できるため、エレクトロニクス、光学、材料科学などの産業で広く使用されている。
キーポイントの説明
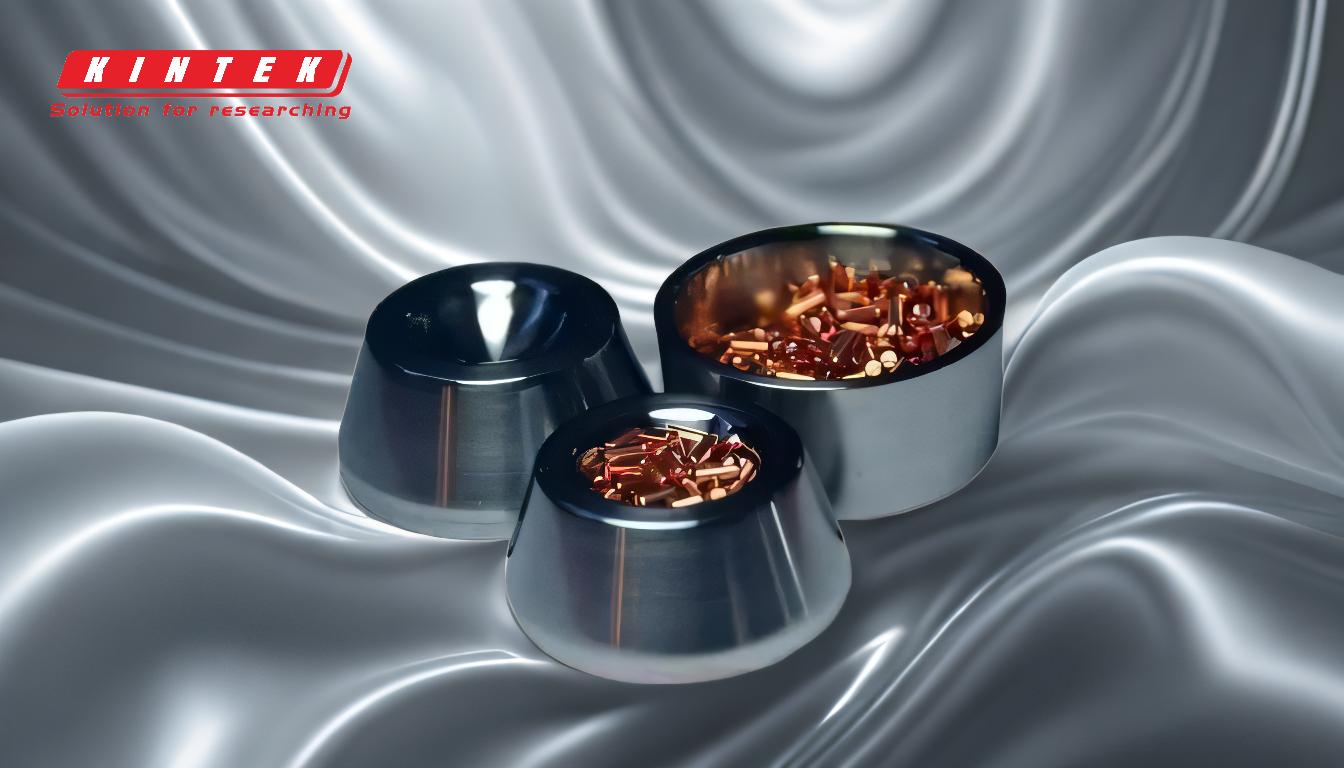
-
真空環境:
- スパッタコーティングは、汚染物質を排除し、制御された環境を確保するため、真空チャンバー内で行われる。
- 真空は他のガスの存在を減少させ、不活性ガス(通常はアルゴン)がプロセスを支配することを可能にする。
-
プラズマの生成:
- 陰極となるターゲット材料に高電圧を印加する。
- この電圧はチャンバー内の不活性ガス(アルゴン)をイオン化し、自由電子、正電荷イオン、中性ガス原子からなるプラズマを生成する。
- このプラズマは、ターゲット材料をスパッタするのに必要な高エネルギーイオンを生成するのに不可欠である。
-
イオン砲撃:
- プラスに帯電したアルゴンイオンは、電界によってマイナスに帯電したターゲット(カソード)に向かって加速される。
- これらの高エネルギーイオンがターゲットに衝突すると、ターゲット原子に運動量が伝わり、スパッタリングと呼ばれるプロセスで表面から放出される。
-
薄膜の蒸着:
- 放出されたターゲット原子は真空中を移動し、基板上に堆積して薄膜を形成する。
- 成膜プロセスは高度に制御されており、均一かつ正確な膜厚を得ることができる。
-
磁場と均一侵食:
- 磁石はプラズマを閉じ込め、集中させるためによく使用され、スパッタリングプロセスの効率を高めます。
- これらの磁場は、ターゲット材料の安定した均一な浸食を保証し、安定した膜質を実現するために重要です。
-
熱管理:
- スパッタリングプロセスでは、高エネルギーの衝突により大きな熱が発生する。
- この熱を管理し、ターゲット、基板、装置への損傷を防ぐために、特殊な冷却システムが採用されている。
-
用途と利点:
- スパッタコーティングは、半導体製造、光学コーティング、装飾仕上げなど様々な産業で使用されている。
- 優れた密着性、高純度、金属、合金、セラミックスなど幅広い材料を成膜できるなどの利点がある。
これらの重要なポイントを理解することで、スパッタコーティングプロセスの複雑さと精度を理解することができ、高度な製造や研究用途で高性能薄膜を作成するための貴重な技術となっている。
総括表:
主な側面 | 内容 |
---|---|
真空環境 | コンタミのない制御された環境で、精密なコーティングを実現します。 |
プラズマの生成 | 高電圧でアルゴンガスをイオン化し、イオン発生用のプラズマを作る。 |
イオン砲撃 | アルゴンイオンがターゲットに衝突し、蒸着用の原子を放出する。 |
薄膜の蒸着 | 放出された原子が基板上に均一で高品質な皮膜を形成します。 |
磁場 | プラズマの効率を高め、ターゲットの均一な侵食を保証します。 |
熱管理 | 冷却システムは、機器を保護し、プロセスの安定性を維持するために熱を管理します。 |
用途 | 半導体、光学、耐久性のあるコーティングの装飾仕上げに使用されます。 |
スパッタコーティングがお客様の製造工程をどのように向上させるかをご覧ください。 今すぐ専門家にお問い合わせください !