設備や機械の安全な運転を確保することは、生産性が高く、危険のない職場を維持する上で重要な側面です。そのためには、適切なトレーニング、定期的なメンテナンス、安全手順の遵守、適切な安全機器の使用などを組み合わせる必要があります。機械に関連するリスクを理解し、予防策を実施することで、組織は事故や機器の故障の可能性を大幅に減らすことができる。このアプローチは、労働者を保護するだけでなく、機器の寿命と効率を高める。
キーポイントの説明
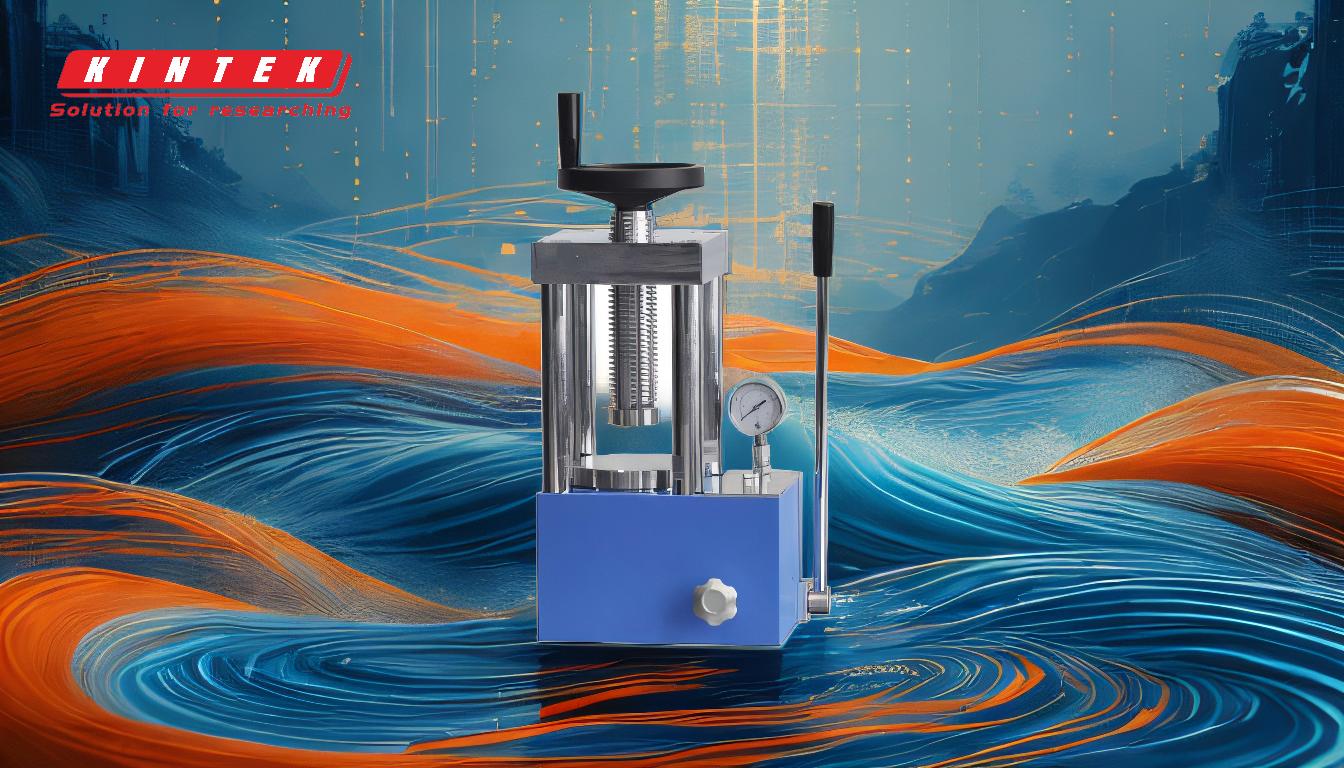
-
オペレーターのための総合トレーニング
- 重要な理由 オペレーターは、機械の機能、潜在的な危険性、緊急時の手順など、使用する機械を理解するための徹底的な訓練を受けなければならない。
- 実施 実地研修、安全マニュアル、定期的な再教育コースを提供し、オペレーターがベストプラクティスを常に最新の状態に保てるようにする。
- 成果: よく訓練されたオペレーターは、事故や機器の損傷につながるミスを犯す可能性が低くなります。
-
定期的なメンテナンスと点検
- 重要な理由 適切にメンテナンスされていない機械は誤動作する可能性があり、安全上のリスクやコストのかかるダウンタイムにつながります。
- 実施 日常点検、潤滑、必要に応じた部品交換など、定期的なメンテナンススケジュールを確立する。診断ツールを使用して、潜在的な問題を早期に特定する。
- 結果を出す: 定期的なメンテナンスにより、機器の効率的な稼働を確保し、予期せぬ故障のリスクを低減する。
-
安全手順と基準の遵守
- 重要な理由 安全プロトコルは、リスクを最小限に抑え、業界の規制を確実に遵守するために設計されています。
- 実施する: ロックアウト/タグアウト手順、個人用保護具(PPE)の適切な使用、安全作業限度などの安全ガイドラインを作成し、実施する。
- 成果 安全プロトコルに従うことで、事故の可能性を低減し、法的および規制要件を確実に遵守する。
-
安全装置とガードの使用
- 重要な理由 ガード、非常停止ボタン、センサーなどの安全装置は、危険な状況において物理的な障壁を作ったり機械を停止させたりすることで、負傷を防ぐことができる。
- 実施方法 すべての可動部品に安全ガードを設置・維持し、非常停止ボタンにアクセスできるようにし、センサーを使用して危険な状態を検知する。
- 結果 安全装置の適切な使用により、運転者の負傷や装置損傷のリスクを大幅に低減する。
-
リスクアセスメントと危険の特定
- なぜ重要なのか 潜在的な危険が危害をもたらす前に特定することは、安全な職場環境を作るために不可欠です。
- 実施 定期的なリスクアセスメントを実施し、機械、作業プロセス、環境要因を評価する。特定されたリスクには、工学的管理、管理上の変更、またはPPEを通じて対処する。
- 成果 積極的な危険の特定と緩和により、事故を防止し、職場全体の安全性を向上させる。
-
緊急事態への備えと対応計画
- なぜ重要なのか 事故は予防措置にもかかわらず発生する可能性があるため、明確な対応計画を持つことが重要である。
- 実施する: 避難経路、応急処置の手順、緊急サービスの連絡先など、緊急時の手順を作成し、周知する。定期的に訓練を実施し、準備態勢を確保する。
- 成果: 十分に準備されたチームは、緊急事態に効果的に対応し、被害とダウンタイムを最小限に抑えることができる。
-
モニタリングと継続的改善
- なぜ重要なのか 安全性は継続的なプロセスであり、定期的な評価と改善が必要である。
- 実施する: インシデント、ヒヤリハット、メンテナンスに関するデータを収集し、傾向と改善点を特定する。安全慣行を改善するために、労働者からのフィードバックを奨励する。
- 成果: 継続的な改善により、安全対策は新たな課題に対処するために進化し、高い安全水準を維持する。
これらの重要な戦略を実施することで、組織は労働者と設備の両方を保護する安全で効率的な作業環境を作り出すことができる。安全を優先することは、事故のリスクを低減するだけでなく、生産性を高め、責任と配慮の文化を育むことにもなる。
総括表
主要戦略 | 重要な理由 | 実施 | 成果 |
---|---|---|---|
総合的なトレーニング | オペレーターのミスや事故を減らす | 実践的トレーニング、安全マニュアル、再教育コース | よく訓練されたオペレーターが事故や機器の損傷を最小限に抑える |
定期的なメンテナンス | 故障やコストのかかるダウンタイムを防ぐ | 定期点検、潤滑、部品交換、診断ツール | 効率的な運転と故障リスクの低減 |
安全手順の遵守 | コンプライアンスの徹底とリスクの最小化 | ロックアウト/タグアウト手順、PPE、安全作業限度 | 事故削減と規制遵守 |
安全装置の使用 | 怪我や機器の損傷を防ぐ | セーフティガード、非常停止ボタン、センサー | オペレーターの怪我や設備故障のリスクを低減 |
リスクアセスメント | 危害が発生する前に危険を特定 | 定期的なリスク評価、技術的管理、PPE | 積極的な危険の軽減が職場の安全性を向上させる |
緊急事態への備え | 事故への効果的な対応 | 緊急手順、訓練、応急処置プロトコル | 緊急時の被害とダウンタイムの最小化 |
継続的改善 | 安全対策を最新かつ効果的に維持 | データ収集、フィードバック、安全対策の改善 | 進化する安全対策は新たな課題に対処し、高い水準を維持する |
職場の安全性と設備効率を高める準備はできていますか? 今すぐご連絡ください までご連絡ください!