薄膜は、物理的、化学的、電気的手法に大別されるさまざまな成膜技術によって作られる。これらの技法は、膜厚、組成、特性を精密に制御できるため、半導体からフレキシブル・エレクトロニクスまで幅広い用途に適している。最も一般的な方法には、蒸着、スパッタリング、化学蒸着(CVD)、スピンコーティング、ドロップキャスト、プラズマスパッタリングなどがある。各方法にはそれぞれ利点があり、希望する膜特性や用途に応じて選択される。
キーポイントの説明
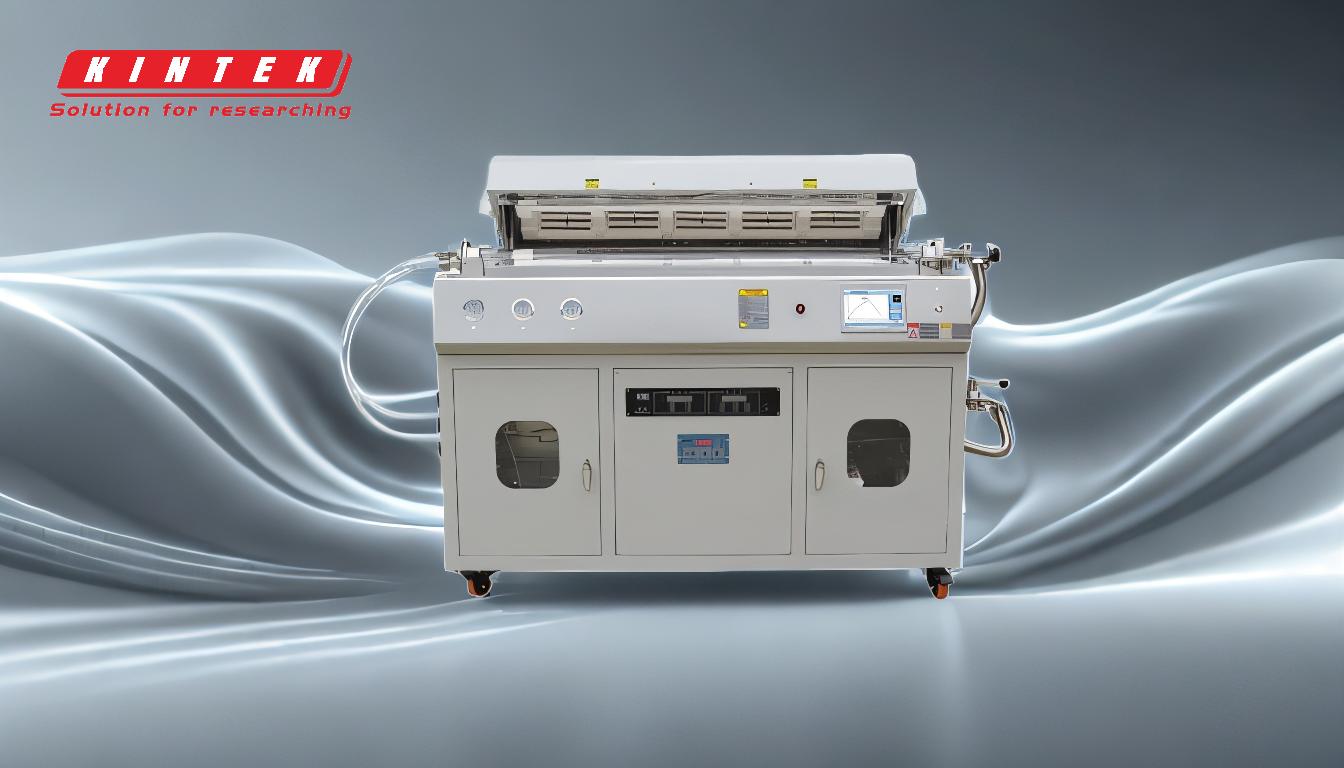
-
蒸着技術の概要:
- 物理的方法:蒸着やスパッタリングなど、材料を基板上に物理的に転写する技術がこれにあたる。
- 化学的手法:化学気相成長(CVD)のような技術は、薄膜を形成するために化学反応を伴う。
- 電気的手法:プラズマスパッタリングなど、電気エネルギーを使って材料を堆積させる方法。
-
蒸着:
- プロセス:真空中で材料を蒸発点まで加熱し、その蒸気を低温の基板上で凝縮させて薄膜を形成する。
- 応用例:光学コーティングや半導体デバイスなどの用途で、金属や単純化合物によく使用される。
-
スパッタリング:
- プロセス:ターゲット材料に高エネルギーのイオンを照射して原子を放出させ、基板上に堆積させる。
- 応用例:マイクロエレクトロニクスや装飾用コーティングの金属、合金、化合物の蒸着に広く使用されている。
-
化学気相成長法(CVD):
- プロセス:化学前駆体を反応室に導入し、そこで反応または分解して基板上に固体膜を形成する。
- 応用例:半導体製造や保護膜の高品質で均一な膜の製造に不可欠。
-
スピンコーティング:
- プロセス:液体プレカーサーを基材に塗布し、高速で回転させることで材料を薄く均一な層に広げる。
- 応用例:フォトレジスト、有機エレクトロニクス、ポリマーフィルムの製造によく使用される。
-
ドロップキャスティング:
- プロセス:材料を含む溶液を基板上に滴下し、乾燥させることで薄膜を形成する。
- 応用例:研究および小規模なアプリケーションで膜を作成するためのシンプルで費用対効果の高い方法。
-
プラズマスパッタリング:
- プロセス:従来のスパッタリングと似ているが、プラズマを使用して成膜プロセスを強化するため、膜特性をより制御できる。
- 応用例:フレキシブル太陽電池やOLEDのような先端用途に使用される。
-
オイル浴:
- プロセス:材料を含む液体に基板を浸し、取り出して乾燥させると薄膜が形成される。
- 用途:あまり一般的ではないが、均一なコーティングが要求される特殊な用途に使用される。
-
コントロールと精度:
- 厚みコントロール:これらの方法はすべて、場合によっては単一原子のレベルまで、膜厚を精密に制御することを可能にする。
- 組成制御:フィルムの組成は、温度、圧力、前駆体濃度などの蒸着パラメーターを調整することにより、細かく調整することができる。
-
応用例:
- 半導体:シリコンベースの薄膜による初期の商業的成功。
- フレキシブルエレクトロニクス:フレキシブル太陽電池とOLEDのための高分子化合物に焦点を当てた新しい方法。
- 光学コーティング:レンズ、ミラー、その他の光学部品に使用され、性能を向上させる。
これらの重要なポイントを理解することで、購入者は特定の用途に最適な成膜方法と材料について、十分な情報を得た上で決定することができ、最適な性能と費用対効果を確保することができる。
要約表
方法 | プロセス | アプリケーション |
---|---|---|
蒸発 | 加熱された材料が蒸発し、基板上で凝縮する。 | 光学コーティング、半導体デバイス |
スパッタリング | 高エネルギーイオンがターゲットに衝突し、基板上に原子を放出する。 | マイクロエレクトロニクス、装飾コーティング |
CVD | 化学前駆体が反応・分解して固体膜を形成 | 半導体製造、保護膜 |
スピンコーティング | 液体プレカーサーを高速回転させて均一な層を形成 | フォトレジスト、有機エレクトロニクス、ポリマーフィルム |
ドロップキャスト | 溶液を基材に滴下し、乾燥させてフィルムを形成 | 研究、小規模用途 |
プラズマスパッタリング | プラズマエンハンスドスパッタリングで膜特性をよりよく制御 | フレキシブル太陽電池、OLED |
オイルバス | 基材を液体に浸し、乾燥させて皮膜を形成する。 | 均一なコーティングを必要とする特殊なアプリケーション |
お客様のアプリケーションに適した薄膜形成方法の選択にお困りですか? 今すぐ当社の専門家にお問い合わせください!