冷間静水圧プレスの概要
目次
冷間静水圧プレス(CIP) は、液体の圧力を使用して粉末を圧縮することによって材料を加工する方法です。これは金型加工に似ており、封入された流体内の圧力は大きさを変えることなく全方向に均等に伝わるというパスカルの法則に基づいています。
冷間静水圧プレス (CIP) の定義と説明
冷間静水圧プレスでは、粉末をエラストマー型に封入し、均一な液体圧力を加えて型を圧縮します。これにより、非常に緻密な固体材料が得られます。 CIPは、プラスチック、グラファイト、セラミックス、粉末冶金、スパッタリングターゲットなどのさまざまな材料に使用できます。
CIPの種類:ウェットバッグとドライバッグ
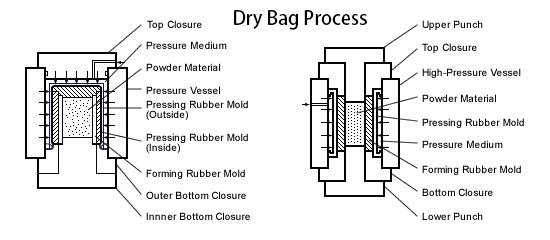
冷間静水圧プレスには 2 つのタイプがあります。
ウェットバッグ技術: このプロセスでは、粉末を金型に充填し、圧力容器の外側でしっかりと密封します。次に、金型を容器内の圧力流体に浸し、等静圧を加えて粉末を固体の塊に圧縮します。ウェットバッグ技術は他のタイプの CIP ほど一般的ではありませんが、さまざまな生産サイズや形状に使用できます。
ドライバッグ技術: このプロセスは自動化と高い生産率に適しています。ウェットバッグプロセスと同様に、粉末は金型に充填され、圧力容器の外側で密封されます。ただし、ドライバッグプロセスは自動化に適しており、より長い生産工程に対応できます。
粉体の品質と工具設計の役割
CIP で使用される粉末の品質とツールの設計は、プロセスの成功に重要な役割を果たします。粉末の品質は最終成形体の密度と完全性に影響を与えますが、工具の設計により適切な成形と均一な圧力分布が確保されます。
ウェットバッグ静水圧プレス:コンセプト、利点、プロセス
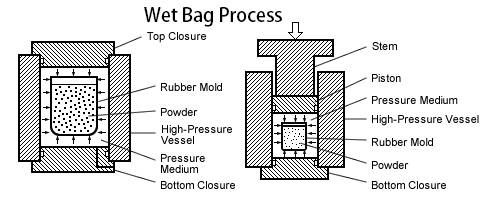
湿式バッグ静水圧プレスでは、粉末を充填した密閉型を圧力流体に浸漬します。次に、等方圧を適用して粉末を固体の形状に圧縮します。この方法は静水圧プレスの理論的概念に近づくことができ、均一な密度と低い閉じ込め応力を備えた成形体が得られます。湿式袋プレスは、機械加工が最小限で済み、焼成時の歪みが少ない成形体を製造できるという利点があります。
ドライバッグ静水圧プレス: 自動化と高生産率に適しています
乾式バッグ静水圧プレスは、湿式バッグプレスと比較して、自動化と高い生産率に適しています。このプロセスでは、圧力容器の外側で粉末を充填した型を密閉します。次に、金型を容器にロードし、加圧し、さらに後処理を行うためにアンロードします。乾式バッグプレスは、他の圧縮方法に比べてより高価な粉末を必要とし、生産速度が低い場合がありますが、自動化に優れており、長時間の生産に適しています。
要約すると、冷間静水圧プレス (CIP) は、液体の圧力を使用して粉末材料を圧縮する方法です。 CIPにはウェットバッグとドライバッグの2種類があります。湿式袋プレスは均一な密度と低い歪みを実現しますが、乾式袋プレスは自動化と高い生産率に適しています。粉末の品質とツールの設計は、CIP を成功させるために重要な考慮事項です。
冷間静水圧プレスとダイプレスの比較
CIPと金型プレスの違い
冷間静水圧プレス (CIP) と金型プレスは材料加工に使用される 2 つの方法であり、それぞれに独自の利点と制限があります。これら 2 つの手法の違いを理解すると、特定のアプリケーションに最適な方法を決定するのに役立ちます。
CIP では、原料の粉末材料をウレタン、ゴム、ポリ塩化ビニルなどのエラストマー材料で作られた柔軟な型の中で圧縮します。圧縮は室温で行われ、油や水などの流体を使用して全方向から均一に圧力を加えます。
一方、一軸プレスとしても知られる金型プレスでは、硬い金型を使用して乾燥粉末を金型キャビティに圧縮します。通常、圧縮は単一方向に適用されるため、濃度が不均一になり、歪みが生じる可能性があります。
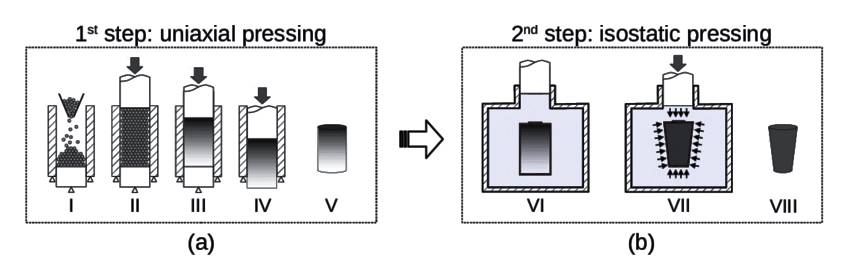
冷間静水圧プレスと一軸成形
一軸金型プレスと比較したCIPの利点: 複雑な形状と歪みの低減
一軸ダイプレスと比較した CIP の大きな利点の 1 つは、複雑な形状の部品を製造できることです。 CIP で使用される柔軟な金型により、金型プレスでは実現が難しい複雑な形状の作成が可能になります。このため、CIP は、複雑なコンポーネントやカスタム設計のコンポーネントを必要とするアプリケーションに特に適しています。
さらに、CIP は不均一な粒子充填によって引き起こされる歪みや亀裂を最小限に抑えます。 CIP ではあらゆる方向から均一な圧力が加えられるため、密度がより均一になり、構造欠陥の可能性が減ります。これは、歪みによって最終製品の機能や構造的完全性が損なわれる可能性がある複雑な形状のコンポーネントにとって特に重要です。
一軸金型プレスよりも CIP の使用が有利な状況
CIP と金型プレスの両方に利点がありますが、特定の状況では CIP が推奨される方法があります。
複雑な形状: 複雑な形状やカスタム設計のコンポーネントを製造する場合、CIP は金型プレスに比べて柔軟性と精度が高くなります。
歪みの低減: 最終製品に高い寸法精度と最小限の歪みが必要な場合は、圧力が均一にかかるため、CIP が推奨される方法です。
ワックスバインダーの不要: 金型プレスとは異なり、CIP ではワックスバインダーを使用する必要がありません。これにより、脱蝋作業が不要になり、製造プロセスが簡素化され、コストが削減されます。
焼結中の均一な収縮: CIP によって均一なグリーン密度が達成されるため、焼結プロセス中の収縮がより均一になります。これは、最終製品で良好な形状制御と均一な特性を維持するために重要です。
大型または小型の形状: CIP は小型コンポーネントと大型コンポーネントの両方に使用できるため、幅広い用途に使用できる汎用性の高い方法です。
CIP には形状の複雑さと歪みの軽減という点で利点がありますが、特定の用途には依然として金型プレスの方が適している場合があることに注意することが重要です。薄いタイルなどの単純な形状のコンポーネントでは、優れた結果が得られるため、ダイプレスが好まれることがよくあります。
結論として、冷間静水圧プレス (CIP) と金型プレスの違いを理解することは、特定の材料加工用途に最適な方法を選択するために重要です。 CIPは複雑な形状の部品を歪みを抑えて製造することに優れており、形状の柔軟性や寸法制御の点で有利です。ただし、特定の用途、特に高い生産速度と単純な形状のコンポーネントを必要とする用途では、依然として金型プレスが好まれる場合があります。
大量生産における冷間静水圧プレス
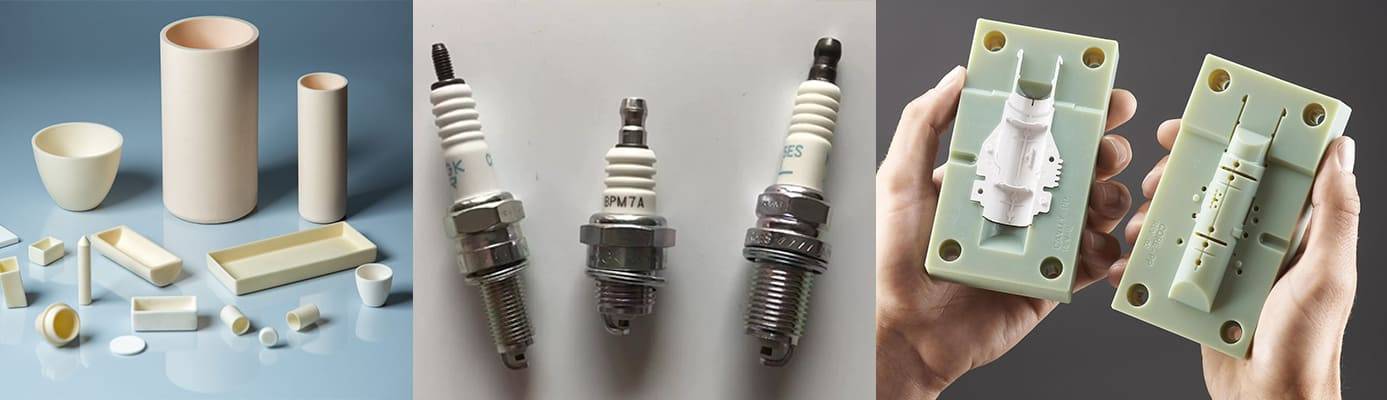
アルミナセラミックスの製造におけるCIPの役割
冷間静水圧プレス (CIP) は、金属およびセラミック部品の製造に使用される粉末ベースのニアネットシェイプ技術です。セラミックス、特にアルミナセラミックスの加工によく使用されています。 CIP を使用すると、一軸金型プレスの能力を超えた複雑な形状の部品の製造が可能になります。粉末材料をゴム袋などの変形抵抗の低い成形型に封入し、液圧を加えて成形体を均一に圧縮する加工です。アルミナ セラミックの CIP 原料には、通常、単純に粉砕したバイエル アルミナまたは噴霧乾燥したバイエル アルミナが含まれます。この方法は、スパーク プラグ絶縁体の製造に一般的に使用されており、世界中で最も生産量の多い CIP セラミック部品の一部です。 CIP を使用して年間約 30 億個のスパーク プラグ絶縁体が製造されています。
スパークプラグ絶縁体の製造におけるCIPの使用
スパーク プラグ絶縁体は、大量生産における CIP の適用に成功した代表的な例です。これらの絶縁体は、内燃エンジンの点火プロセスにおいて重要な役割を果たします。 CIPの採用により、複雑な形状のスパークプラグ絶縁体を高精度に製造することが可能です。この方法により、成形体の均一な圧縮が保証され、一貫した密度と強度を備えた絶縁体が得られます。 CIP プロセスは、複雑な形状の必要性と射出成形などの他の方法の制限のため、スパーク プラグ絶縁体の製造に特に適しています。アルミナ セラミックの高性能特性と強度要件により、CIP はスパーク プラグ絶縁体の製造に理想的な選択肢となります。
CIP と射出成形などの他の方法との比較
CIP は複雑な形状の部品を大量生産する場合に効果的な方法ですが、工業的には射出成形の方が一般的に使用されています。射出成形には、生産サイクルの短縮やコストの削減などの利点があります。ただし、非常に複雑な形状が必要であり、射出成形が現実的ではない場合には、CIP が推奨されます。 CIP では、凹面、中空、細長い形状の部品を製造できるため、他の方法では困難な用途に適しています。さらに、CIP には、ソリッドステート処理、均一な微細構造、低いツールコスト、拡張性などの利点があります。 CIP は、材料の無駄を最小限に抑えてニアネットシェイプの部品を製造できるため、航空宇宙産業や自動車産業などのニッチな用途における金属やセラミックの実行可能な加工ルートとなっています。
結論として、冷間静水圧プレス (CIP) は、複雑な形状の部品、特にアルミナ セラミックの大量生産に価値のある方法です。均一な圧縮、高精度、ニアネットシェイプの部品を製造できるなどの利点があります。射出成形がより一般的に使用されますが、非常に複雑な形状が必要な場合には CIP が推奨されます。スパークプラグ絶縁体の製造における CIP の適用の成功は、高性能コンポーネントの製造における CIP の能力を実証しています。全体として、CIP は、さまざまな業界における大量生産の需要を満たすための信頼性が高く効率的な方法です。
冷間静水圧プレスのプロセスと材料の要件
均一加圧によるCIPの仕組み
冷間静水圧プレス (CIP) は、金属およびセラミック部品の製造に使用される粉末ベースのニアネットシェイプ技術です。 CIPの仕組みは、ゴム袋などの変形抵抗の低い成形型に封入された粉体材料に均一な圧力を加えるというものです。圧力が成形体の表面全体に均一に伝わり、緻密で均一な部品が得られます。
加圧および減圧の制御速度の重要性
CIP では、加圧と減圧の速度が重要です。制御された速度により均一な圧縮が保証され、最終部品の欠陥のリスクが最小限に抑えられます。急激な圧力変化は、不均一な密度分布や構造的脆弱性を引き起こす可能性があります。したがって、最適な結果を得るには、加圧および減圧の速度を慎重に制御することが不可欠です。
CIPの自動化と大規模適用
プロセス能力と粉末冶金の進歩により、CIP はますます自動化され、大規模用途に適しています。 CIP の自動化により、生産量の増加、プロセス制御の改善、人件費の削減が可能になります。 CIP の拡張性により、高性能金属部品の製造が必要とされる航空宇宙や自動車などの業界にとって、CIP は実行可能な選択肢となります。
冷間静水圧プレス (CIP) 装置: 生産コストを圧縮!
CIP (Cold Isostatic Pressing) は、粉末の圧縮に使用される材料処理方法です。これには、粉末をエラストマー型に閉じ込め、四方から高圧をかけることが含まれます。 CIP は、粉末冶金、超硬合金、耐火材料、グラファイト、セラミック、プラスチックなどを含む幅広い材料で利用できます。
冷間静水圧プレスサービスを選択するときは、材料の能力を考慮することが重要です。 CIP を使用すると、アルミニウムおよびマグネシウム合金、超硬、切削工具、カーボンおよびグラファイト、セラミック、複合材料などのさまざまな材料およびコンポーネントを製造できます。一部の冷間静水圧プレス サービスは、コーティング、溶射溶射、銅合金、ダイヤモンド状材料など、特定の材料またはプロセスに特化しています。
冷間静水圧プレスサービスの圧力範囲と能力も考慮すべき重要な要素です。部品の製造に必要な最大動作圧力は、材料と部品の形状によって異なります。直径と高さを含むチャンバーのサイズによって、サービスプロバイダーの能力が決まります。
冷間静水圧プレスは、ウレタン、ゴム、ポリ塩化ビニルなどのエラストマー材料で作られた金型を使用して、室温で実行されます。 CIP で使用される流体は通常、油または水であり、操作中に適用される圧力は 60,000 lbs/in2 (400 MPa) から 150,000 lbs/in2 (1000 MPa) の範囲になります。 CIP には、柔軟な金型が原因で幾何学的精度が低いという欠点があることに注意することが重要です。ただし、粉末は CIP によって均一に圧縮でき、その後、圧粉体を従来の方法で焼結して、目的の最終部品を製造できます。
セラミックスの冷間静水圧プレスの長所と短所

他の方法と比較したアルミナセラミックスに対するCIPの利点
冷間静水圧プレス (CIP) は、粉末ベースのニアネットシェイプ技術であり、セラミック、特にアルミナ セラミックの製造にいくつかの利点をもたらします。他の方法と比較して、CIP には次の利点があります。
より複雑な形状も可能: CIP を使用すると、一軸ダイプレスなどの他の方法では実現できない複雑な形状の製造が可能になります。
プレス圧力勾配の低減: CIP は、プレスプロセス中の歪みや亀裂のリスクを大幅に低減します。これは、セラミック部品の寸法の完全性と全体的な品質を維持するのに有益です。
低い金型コスト: CIP は、必要な金型コストが低いため、少量の生産量で複雑な部品を製造するのに最適です。さらに、CIP 後の金型コストがかからないため、全体の生産コストがさらに削減されます。
サイズ制限なし:他のセラミック成形法とは異なり、CIP にはプレスチャンバーの制限以外にサイズ制限がありません。これにより、非常に大きなコンポーネント、特に複雑な形状のコンポーネントの製造に適しています。 CIP は、重量 1 トンを超えるコンポーネントの製造に使用されて成功しています。
短い処理サイクル時間: CIP により、乾燥やバインダーの燃え尽きの必要がなくなり、処理サイクル時間が短縮されます。これにより、生産の高速化と効率の向上が可能になります。
寸法制御、形状の複雑さ、粉末要件に関する CIP の制限
冷間静水圧プレスにはいくつかの利点がありますが、特に寸法制御、形状の複雑さ、粉末要件の点で一定の制限もあります。これらの制限には次のものが含まれます。
寸法制御の制限: CIP では、正確な寸法制御を達成することが困難な場合があります。このプロセスで使用されるエラストマーの型またはシースは非常に薄く、均一な厚さである必要がありますが、それでも高精度を達成するのは困難です。
形状の複雑さの制限: CIP では、一軸金型プレスと比較してより複雑な形状が可能ですが、形状の複雑さの点では粉末射出成形 (PIM) などの他の方法よりも劣っています。 PIM を使用すると、複雑で非常に複雑な形状を柔軟に作成できます。
粉体流動性の要件: CIP に使用される粉体は、優れた流動性を備えている必要があります。多くの場合、必要な流動性を実現するために、スプレー乾燥や充填時の金型の振動などの追加プロセスが必要になります。これにより、全体のコストが増加し、製造プロセスが複雑になる可能性があります。
これらの制限にもかかわらず、冷間静水圧プレスはセラミック、特にアルミナ セラミックの製造において依然として実行可能な選択肢です。形状の複雑さ、工具コストの低さ、大型で複雑なコンポーネントの製造能力といった利点により、特定の用途では望ましい選択肢となります。ただし、セラミック部品に最適な製造方法を決定する際には、CIP の特定の要件と制限を考慮することが重要です。
冷間静水圧プレスの産業用途
CIPを活用した先進的・複雑形状セラミックスの量産化
冷間静水圧プレス (CIP) は、金属およびセラミック部品の製造に使用される粉末ベースのニアネットシェイプ技術です。 CIP はセラミックの加工に一般的に使用されてきましたが、最近の加工能力と粉末冶金の発展により、高性能金属部品にも CIP が使用されることが増えています。
CIP の主な利点の 1 つは、複雑な形状の部品を高精度で製造できることです。そのため、複雑な設計が必要な先端セラミックスの量産に適しています。このプロセスにより固体状態での処理が可能になり、均一な微細構造と優れた機械的特性が得られます。
CIP を通じて製造される特定のコンポーネント
CIP は、さまざまな業界向けの幅広いコンポーネントの製造に使用できます。一般的な例としては次のようなものがあります。
セラミック粉末の圧縮: CIP は、窒化ケイ素、炭化ケイ素、窒化ホウ素、炭化ホウ素、ホウ化チタン、スピネルなどのセラミック粉末の圧縮に広く使用されています。この技術により、優れた強度と熱特性を備えた高密度セラミック部品の製造が可能になります。
スパッタリング ターゲットの圧縮: CIP は、薄膜堆積プロセスで使用されるスパッタリング ターゲットの圧縮にも使用されます。この技術により、ターゲット材料の均一な密度と優れた密着性が保証され、高品質のコーティングが得られます。
バルブコンポーネントのコーティング: CIP を使用して、エンジンで使用されるバルブコンポーネントをコーティングし、シリンダーの摩耗を軽減できます。このプロセスはコンポーネントの耐久性と性能を向上させ、自動車産業や航空宇宙産業における要求の厳しい用途に適したものにします。
アルミナ産業、特にスパークプラグ絶縁体の製造における CIP の役割
アルミナ業界では、CIP はスパーク プラグ絶縁体の製造において重要な役割を果たしています。スパークプラグ絶縁体は、内燃エンジンで高電圧の電気をスパークプラグに伝達するために使用される重要な部品です。断熱性が高く、高温や機械的ストレスに対する耐性が必要です。
CIP は、アルミナ粉末を強化し、優れた電気的および熱的特性を備えた複雑な形状の絶縁体を形成するために使用されます。このプロセスにより、高密度で均一な微細構造を備えた絶縁体の製造が可能になり、要求の厳しいエンジン環境において信頼性の高い性能が保証されます。
全体として、CIP は、複雑なセラミックの大量生産、特定のコンポーネントの生産、スパーク プラグ絶縁体用のアルミナ産業における CIP の役割など、産業用途にいくつかの利点をもたらします。材料の無駄を最小限に抑えてほぼネットシェイプの部品を製造できる能力と、低い工具コストおよびプロセスの拡張性を組み合わせることで、さまざまな業界にとって実行可能な加工ルートとなっています。
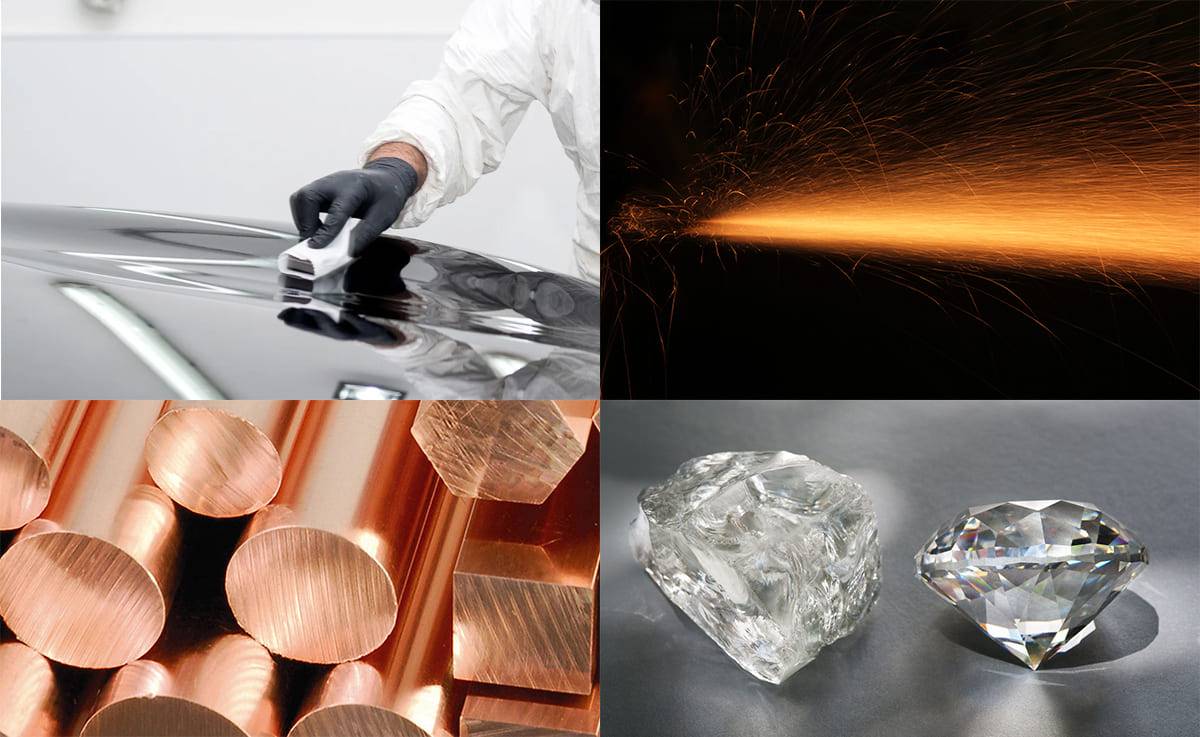
冷間静水圧プレスと他の圧縮技術の比較
冷間静水圧プレス (CIP)
冷間静水圧プレス (CIP) は、焼結の準備ができた理論上 60 ~ 80% の密度の部品を得るために使用される粉末圧縮プロセスです。材料を高圧の流体媒体に浸漬し、油圧を加えることにより、材料を四方八方から均一な圧力にさらします。 CIP は、粉末材料の成形と強化、複雑な形状の作成、および高いグリーン密度の達成に特に効果的です。
冷間静水圧プレスと熱間静水圧プレス: 比較の概要
材料加工の分野では、冷間等方圧プレス (CIP) と熱間等方圧プレス (HIP) という 2 つの強力な技術が際立っています。どちらの方法も材料特性を向上させるという共通の目標を持っていますが、異なる条件下でそれを行うため、それぞれに独自の利点があります。
冷間静水圧プレス (CIP) では、材料にあらゆる面から均一な圧力を加え、複雑な形状を作成し、高いグリーン密度を実現します。特に粉末材料の成形や固化に効果を発揮します。
熱間静水圧プレス (HIP) では、材料を高温と高圧の両方に同時に曝して、完全に緻密な部品を取得します。主に、高性能用途に最適な特性を必要とする人工セラミックスに使用されます。
冷間等方圧プレスと熱間等方圧プレスのどちらを選択するかは、プロジェクトの具体的な目標と関係する材料の特性によって異なります。
衝撃圧縮などの代替圧縮技術の導入
ホットプレス、熱間静水圧プレス、および熱間押出成形では、ほぼ完全に密度の高い製品を生成できます。しかし、これらの方法は、特に圧縮された MA 粉末の調製中にナノ粒子の粗大化を引き起こす傾向があります。これを克服するために、衝撃圧縮や衝撃波圧縮など、加熱時間が非常に短い代替圧縮技術が開発され、ある程度の成功を収めています。
衝撃圧縮には、非常に高い圧力、中程度の温度、非常に短い反応時間、および非常に高いひずみ速度を特徴とする衝撃波の生成が含まれます。この技術では、粒子を大幅に変形させ、局所的な溶融を引き起こす可能性があり、その結果、粒子が成長することなく完全に緻密で圧縮されたサンプルが得られます。以前はミクロンサイズの粉末の圧縮に使用されていたエアガンや爆発性衝撃波などの方法が、現在ではナノ粉末の圧縮に使用されています。
ナノ粉末の圧縮における衝撃圧縮の応用
衝撃圧縮技術は、ナノパウダーを圧縮するのに効果的であることが証明されています。粉末に短い高圧の衝撃波を加えることで、粒子が成長することなく、粒子を十分に緻密かつ緻密にすることができます。この方法は、ナノ粉末の圧縮に有望なソリューションを提供し、高品質で完全に密度の高い製品の製造を可能にします。
結論として、 冷間静水圧プレス (CIP) は粉末材料の成形と固化において独自の利点を提供しますが、熱間静水圧プレス (HIP) は完全に緻密な部品を得るのに適しています。衝撃圧縮などの代替圧縮技術は、ナノ粉末を圧縮するためのソリューションを提供し、最終製品の高密度と品質を保証します。圧縮技術の選択は、プロジェクトの特定の要件と関連する材料によって異なります。
無料相談はお問い合わせください
KINTEK LAB SOLUTION の製品とサービスは、世界中のお客様に認められています。弊社スタッフがどんなご質問にも喜んで対応させていただきます。無料相談にお問い合わせいただき、製品スペシャリストにご相談いただき、アプリケーションのニーズに最適なソリューションを見つけてください。