ウェットバッグとドライバッグ静水圧プレスは、特にセラミック、金属、先進材料などの業界で、高密度コンポーネントの製造に使用される 2 つの異なる方法です。湿式バッグプレスは、大型または複雑な部品の製造に適しており、摩擦が最小限に抑えられるため、より高い密度を達成できます。ただし、効率が低く、自動化も進んでいないため、小規模なバッチや実験室での生産に最適です。一方、乾式バッグプレスは高度に自動化されており、より高速かつ効率的であるため、より単純な形状の大量生産に最適です。主な違いは、金型のセットアップ、自動化の可能性、生産速度、さまざまな生産規模への適合性にあります。
重要なポイントの説明:
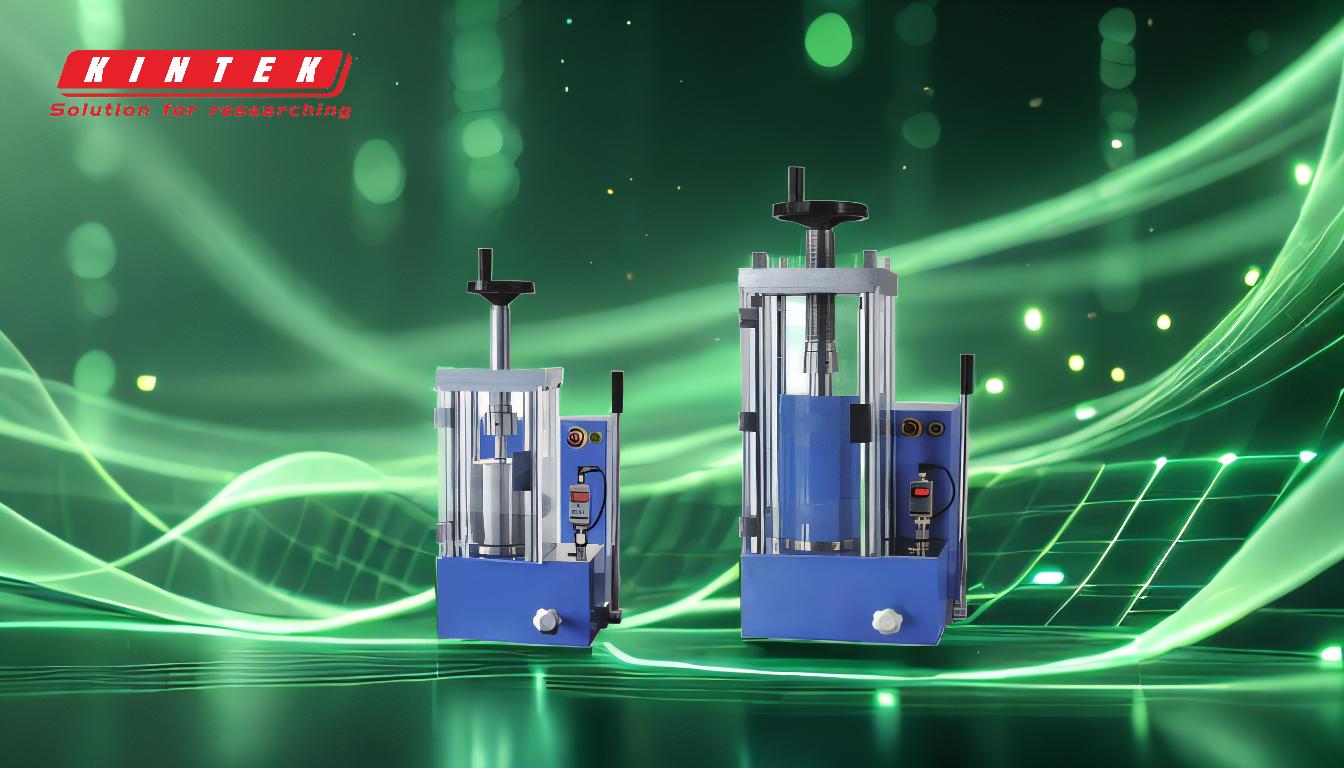
-
金型のセットアップとプロセス:
- ウェットバッグプレス: この方法では、金型 (変形可能なゴムスリーブ) に粉末または予備成形された素地を充填し、次に加圧流体が入った圧力容器に浸します。金型は容器内に固定されていないため、大型部品や複雑な部品を柔軟に取り扱うことができます。プレス後、型は容器から取り外されるため、断続的なプロセスとなります。
- ドライバッグプレス: ここで、金型は圧力容器内に永久的に固定されています。粉末は容器内に残ったまま金型に投入され、流体を通して均一に圧力がかかります。この設定により、より速いサイクルと継続的な生産が可能になります。
-
自動化と生産性:
- ウェットバッグプレス: 金型を手動でロードおよびアンロードする必要があるため、この方法では生産性が低く、自動化も限られています。より労働集約的で時間がかかるため、小規模なバッチや特殊な用途に適しています。
- ドライバッグプレス: この方法は高度に自動化されており、手動介入を最小限に抑えながら継続的な生産を可能にします。 1 時間あたり最大 1500 パーツの生産速度を達成できるため、大量生産に最適です。
-
生産規模への適合性:
- ウェットバッグプレス: 研究室での準備、少量のバッチ生産、または大型で複雑な部品の製造に最適です。その適応性により、複数の金型を同時に処理できますが、大量生産の場合は効率が低くなります。
- ドライバッグプレス: より単純な形状や部品の量産向けに設計されています。高度な自動化とより速いサイクルタイムにより、大規模製造において経済的に実行可能です。
-
成形体の密度と品質:
- ウェットバッグプレス: プレス工程中の摩擦が最小限に抑えられるため、わずかに高い密度が得られます。このため、高密度コンポーネントを必要とするアプリケーションに適しています。
- ドライバッグプレス: 湿式バッグプレスと同じ密度レベルは達成できないかもしれませんが、それでもほとんどの産業用途に適したコンパクトな微細構造を持つコンポーネントを生産します。
-
サイクルタイムと効率:
- ウェットバッグプレス: サイクル時間は 2 ~ 5 分の範囲であり、プロセスにはより多くのステップが含まれるため、全体の効率が低くなります。
- ドライバッグプレス: サイクルタイムは短くなり、通常は 1 回の実行につき 5 ~ 10 分で、プロセスは効率化のために合理化されているため、大量生産の速度とコスト効率が向上します。
要約すると、湿式バッグ静水圧プレスは、特殊な少量または複雑な部品の生産に最適ですが、乾式バッグ静水圧プレスは、より単純なコンポーネントの大量の自動製造に優れています。どちらを選択するかは、部品のサイズ、複雑さ、必要な生産規模など、生産プロセスの特定の要件によって異なります。
概要表:
側面 | ウェットバッグプレス | ドライバッグプレス |
---|---|---|
金型のセットアップ | 金型は圧力容器内に沈められます。固定されていない。大型/複雑な部品に適しています | カビは容器内に永久的に固定されます。シンプルな形状に最適 |
オートメーション | 自動化が進んでいない。手動による積み込み/積み下ろし。労働集約的な | 高度に自動化されています。手作業による介入は最小限に抑えられます。連続生産 |
生産規模 | 小規模なバッチ、研究室、または複雑な部品に最適 | より単純なコンポーネントの大量生産向けに設計 |
成形体の密度 | 最小限の摩擦により高密度を実現 | 密度はわずかに低いですが、ほとんどの産業用途に適しています |
サイクルタイム | 1 サイクルあたり 2 ~ 5 分。効率が低い | 1 サイクルあたり 5 ~ 10 分。より速く、よりコスト効率の高い大量生産が可能 |
貴社の生産に適した静水圧プレス法の選択にサポートが必要ですか? 今すぐ専門家にお問い合わせください 個別のアドバイスが必要です!