CIP(定置洗浄)システムは、食品、飲料、医薬品などの産業において、衛生と作業効率を維持するために不可欠です。ウェットバッグCIPシステムとドライバッグCIPシステムは一般的な2つの構成で、それぞれ異なる操作特性と用途があります。ウェットバッグCIPシステムは、スプレー装置を洗浄液に浸漬するため、洗浄サイクルが頻繁な小規模なオペレーションに適しています。一方、ドライバッグCIPシステムは、スプレー装置を使用していないときは乾燥した状態に保つため、洗浄頻度の少ない大規模なオペレーションに適しています。両者の選択は、生産規模、洗浄頻度、操作上の要件などの要因によって決まる。
主なポイントの説明
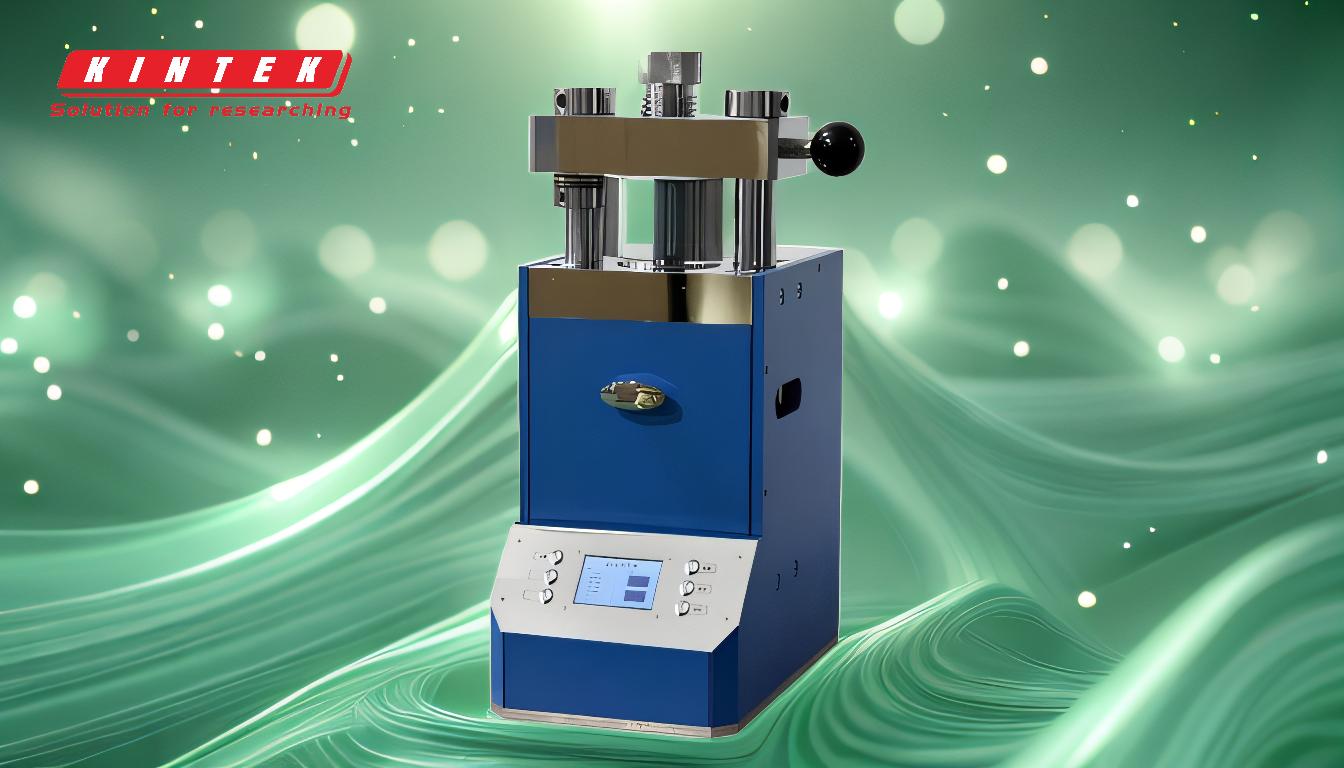
-
ウェットバッグCIPの定義と操作:
- ウェットバッグCIPシステムは、未使用時にスプレー装置が洗浄液に浸るように設計されています。このため、スプレー装置は常にすぐに使用できる状態にあり、頻繁な洗浄サイクルを必要とする作業には特に有益です。
- ウェットバッグシステムでは、スプレー装置が水没しているため、装置自体の清浄度が維持され、汚染のリスクが低減されます。
- ウェットバッグシステムは通常、洗浄頻度が高く、必要な洗浄液の量が管理可能な小規模のオペレーションで使用されます。
-
ドライバッグCIPの定義と操作:
- ドライバッグCIPシステムは、未使用時にスプレー装置を乾燥状態に保ちます。洗浄液がシステムに導入されるのは洗浄サイクルの間だけなので、洗浄剤を節約でき、洗浄液の滞留による汚染のリスクも低減できます。
- ドライバッグシステムは、洗浄サイクルの頻度が少なく、必要な洗浄液の量が多い大規模なオペレーションに適しています。
- ドライバッグシステムのスプレー装置は乾燥しているため、微生物の繁殖や汚染のリスクが低く、衛生要件が厳しい業界に最適です。
-
洗浄効率の比較:
- ウェットバッグCIPシステムは一般的に、洗浄液をすぐに利用できるため、頻繁な洗浄が必要なオペレーションではより効率的です。しかし、常に洗浄液にさらされるため、時間の経過とともにスプレー装置の摩耗や破損につながる可能性があります。
- ドライバッグCIPシステムは、頻繁な洗浄サイクルの効率は劣るものの、洗浄剤の保存性が高く、スプレー装置の磨耗を抑えることができる。ドライバッグCIPシステムは、洗浄サイクルの間隔が広く、洗浄液の滞留による汚染のリスクが懸念されるオペレーションに適しています。
-
メンテナンスと運用上の注意点
- ウェットバッグCIPシステムは、洗浄液の効果を維持し、スプレー装置を良好な状態に保つため、定期的なメンテナンスが必要です。常に洗浄液にさらされるため、時間の経過とともに腐食やその他の劣化が生じる可能性があります。
- 一方、ドライバッグCIPシステムは、スプレー装置が洗浄液にさらされることが少ないため、メンテナンスの頻度が少なくて済む。しかし、各サイクル中の洗浄液の導入と除去を管理するために、より複雑な配管と制御システムが必要になる場合があります。
-
さまざまな産業での応用
- ウェットバッグCIPシステムは、洗浄液の量が管理可能で、即時洗浄の必要性が重要な小規模の食品・飲料製造など、高頻度の洗浄が必要な産業で一般的に使用される。
- ドライバッグCIPシステムは、洗浄液の量が多く、洗浄サイクルの頻度が低い、大規模な医薬品製造や乳製品加工のような大規模なオペレーションで好まれます。コンタミネーションのリスクが少なく、洗浄剤の保存性が高いドライバッグシステムは、このような用途に適しています。
結論として、ウェットバッグCIPシステムとドライバッグCIPシステムのどちらを選択するかは、生産規模、洗浄サイクルの頻度、衛生基準など、業界特有の運用要件によって決まる。ウェットバッグシステムは即座に洗浄が可能であり、小規模なオペレーションに適している。一方、ドライバッグシステムは洗浄剤の保存性が高く、汚染リスクを低減できるため、大規模なオペレーションに最適である。
総括表
特徴 | ウェットバッグCIPシステム | ドライバッグCIPシステム |
---|---|---|
スプレー装置の状態 | 洗浄液に浸漬 | 使用しないときは乾燥させる |
洗浄頻度 | 高頻度の洗浄サイクル | 洗浄頻度の低いサイクル |
運用規模 | 小規模事業 | 大規模オペレーション |
メンテナンス | 定期的なメンテナンスが必要 | メンテナンス頻度が少ない |
用途 | 小規模食品、飲料製造 | 大規模医薬品、乳製品製造 |
汚染リスク | 中程度 | 低い |
洗浄効率 | 即時の洗浄準備 | 洗浄剤の保存性が向上 |
お客様のオペレーションに適したCIPシステムの選定にお困りですか? 当社の専門家にご連絡ください。 にご相談ください!