イオン窒化とガス窒化は、どちらも金属部品の耐摩耗性、疲労強度、硬度を向上させるために使用される表面硬化プロセスです。しかし、プロセスの仕組み、効率、コスト、窒化層の品質などの点で大きく異なります。イオン窒化はグローイオン窒化とも呼ばれ、ガス窒化に比べて処理時間が短く、作業コストが低く、窒化層の品質が優れている、より高度で最新の技術です。高圧電界を利用して窒素の拡散を促進し、制御された高品質の表面層を形成します。一方、ガス窒化は、アンモニアガスと金属表面の化学反応に依存するため、速度が遅く、効率も低い。イオン窒化には高い初期投資が必要ですが、操作上の利点と優れた結果があるため、多くの用途で選ばれています。
重要ポイントの説明
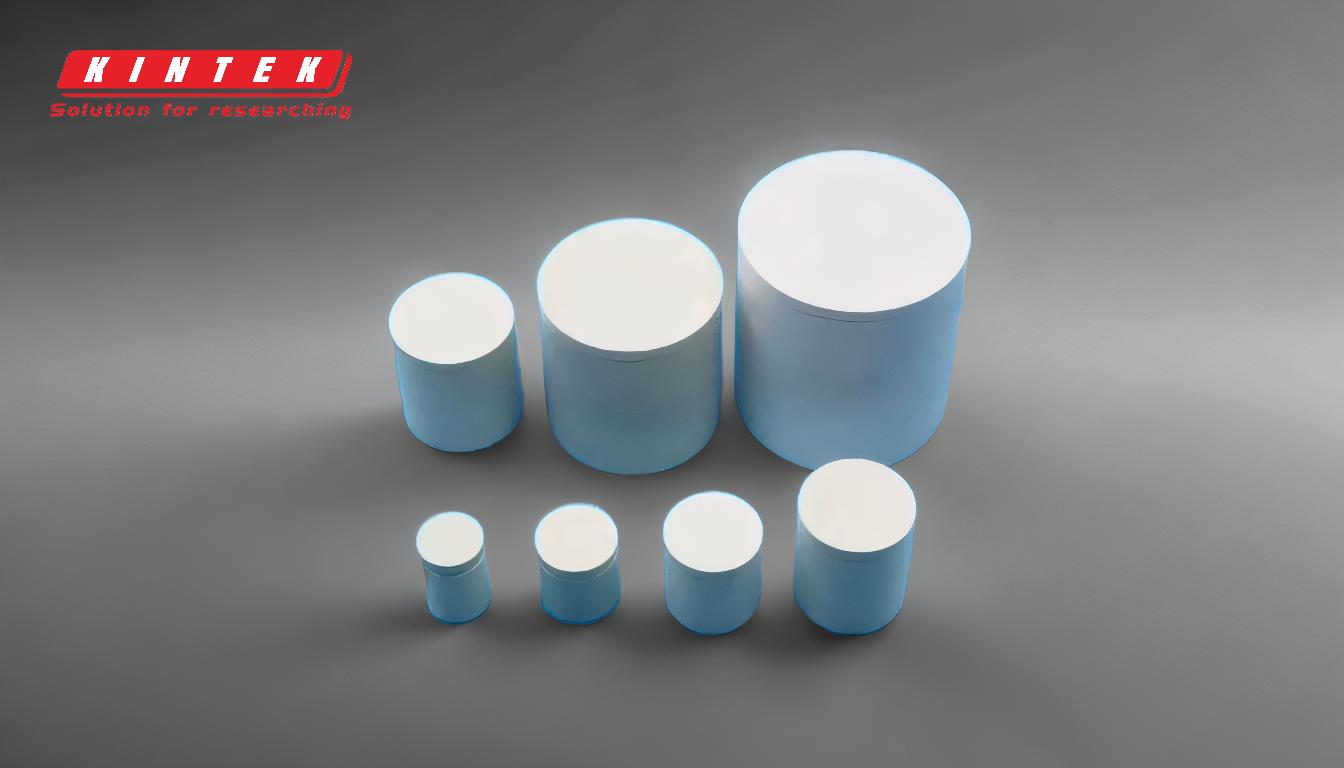
-
プロセス力学:
- イオン窒化:このプロセスでは、金属部品を真空チャンバーに入れ、高電圧の電界でイオン化した窒素ガスのプラズマを発生させる。窒素イオンは金属表面に向かって加速され、材料の中に拡散して硬い窒化物層を形成する。この方法によって、窒化工程と形成される層の特性を正確に制御することができます。
- ガス窒化:このプロセスでは、金属部品はアンモニアガスの雰囲気中で加熱される。アンモニアは金属表面で分解し、窒素原子を放出して材料内に拡散する。この方法は、イオン窒化に比べて時間がかかり、制御性も劣る。
-
加工時間:
- イオン窒化:窒化プロセスは著しく速く、通常3~10時間かかる。これは、高圧電界の影響下で窒素原子が急速に拡散するためである。
- ガス窒化:プロセスが遅く、同等の窒化層を得るには長時間を要することが多い。
-
操業コスト:
- イオン窒化:操業コストはガス窒化の約60%。これは、処理時間が速く、エネルギー消費量が少ないためである。
- ガス窒化:処理時間が長く、エネルギー消費量が多いため、操業コストが高くなる。
-
窒化層の品質:
- イオン窒化:高い靭性、耐疲労性、耐摩耗性を持つ窒化層を生成。脆い白色セメント相(Fe2N)を0~0.2mmに制御できるため、研削加工が不要。表面硬度はHV900(HRC64)に達することができ、窒化層の深さは0.09~0.87 mmに制御できます。
- ガス窒化:硬い表面層を作ることができるが、一般的に品質はイオン窒化より劣る。このプロセスは制御しにくく、層の厚さや特性にばらつきが生じる。
-
部品の変形:
- イオン窒化:表面の急速な加熱と冷却による部品の変形を抑え、部品の他の部分を低温(100℃)に保つ。これにより、熱応力と歪みを最小限に抑えます。
- ガス窒化:加熱・冷却速度が遅いため、部品の変形リスクが高く、熱応力や歪みが大きくなる可能性がある。
-
初期投資:
- イオン窒化:初期投資が高い。例えば、容量400kgのイオン窒化炉は約90万元。
- ガス窒化:初期投資が少なく、同容量の炉で約4万元。
-
環境・エネルギー効率:
- イオン窒化:処理時間の短縮とエネルギー消費の低減により、より環境に優しく、エネルギー効率に優れている。
- ガス窒化:エネルギー効率が低く、廃棄ガスが多く発生するため、環境にやさしくない。
まとめると、イオン窒化は初期投資が高くなるものの、処理速度、操業コスト、窒化層の品質の点で優れているため、多くの用途で優れた選択肢となる。ガス窒化は、初期費用は安いものの、処理速度が遅く、効率が低く、品質の低い窒化層が得られる。
総括表
側面 | イオン窒化 | ガス窒化 |
---|---|---|
プロセスの仕組み | 高電圧の電界でプラズマを発生させ、窒素を拡散させる。 | 窒素拡散はアンモニアガスの分解に頼る。 |
処理時間 | 3~10時間(拡散が速いため早い)。 | より遅く、同等の結果を得るにはより長い時間を要することが多い。 |
運転コスト | ~ガス窒化コストの~60%(エネルギー消費量が少なく、処理が速い)。 | 処理時間とエネルギー消費が長いため、高くなる。 |
窒化層の品質 | 高い靭性、耐疲労性、耐摩耗性。層の深さを制御。 | 層厚や特性の制御が難しく、品質が劣る。 |
部品の変形 | 急速な表面加熱と冷却により最小。 | 加熱・冷却速度が遅いためリスクが高い。 |
初期投資 | 高い(例:400kgの炉で90万元)。 | より低い(例えば、同容量の炉で4万元)。 |
環境への影響 | エネルギー効率が高く、環境に優しい。 | エネルギー効率が低く、環境に優しい。 |
金属部品の性能を向上させたいですか? 今すぐお問い合わせください までご連絡ください!