射出成形は非常に効率的な製造プロセスであり、特にスピード、費用対効果、精度の面でいくつかの利点があります。特に、複雑な形状や厳しい公差を持つ小型部品の製造に適しています。このプロセスは、他の方法と比べて硬化時間が大幅に短縮されるため、大量生産をより迅速かつ経済的に行うことができます。さらに、射出成形は、製品の品質と精度を維持するために重要な、一貫した収縮と高い再現性を保証します。最初のセットアップが完了すれば、1時間あたり大量の部品を生産できるため、大量生産に最適です。
キーポイントの説明
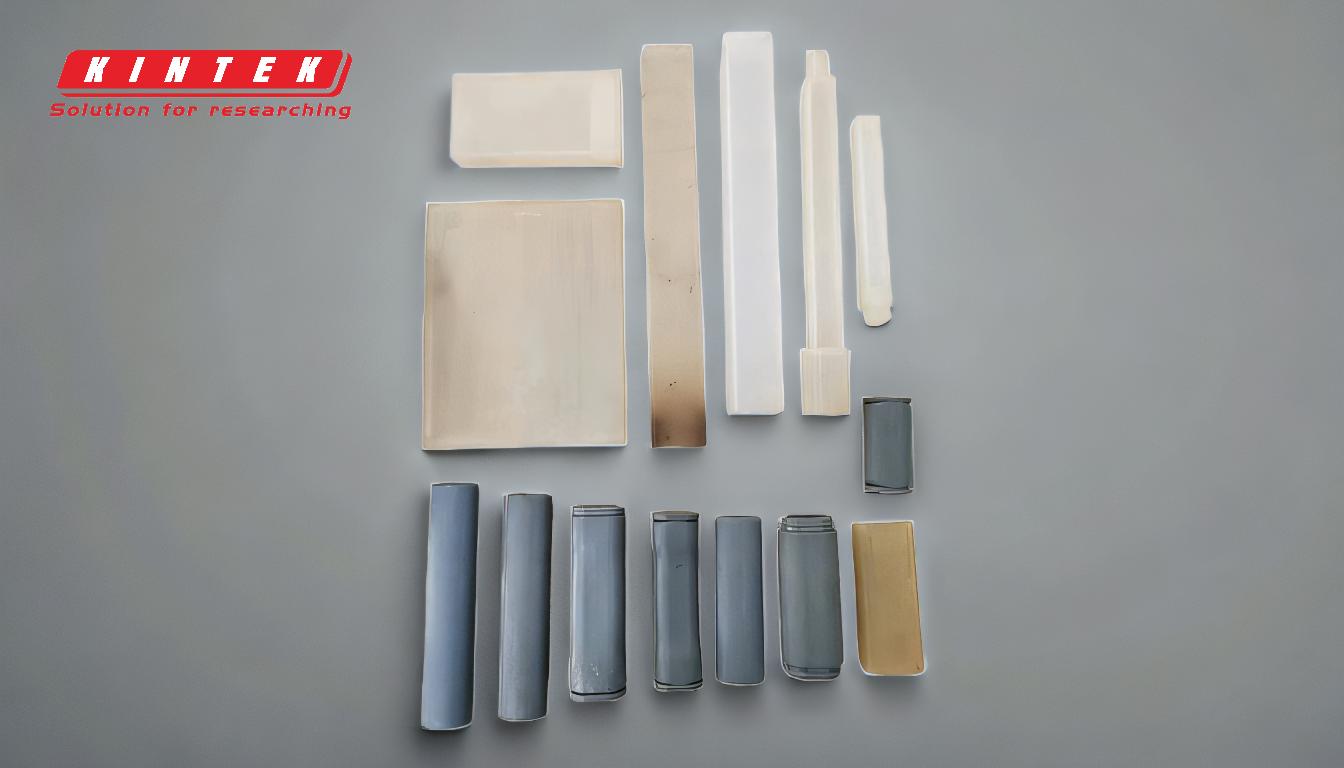
-
硬化時間の短縮:
- 射出成形は、圧縮成形やトランスファー成形のような他の成形方法と比較して、硬化時間を大幅に短縮します。射出成形の成形サイクルは約10秒ですが、他の方法では10~20分かかります。この時間の短縮は、生産速度の向上と人件費の削減につながります。
-
費用対効果:
- 射出成形は、そのスピードと効率性により、費用対効果に優れている。各成形サイクルに必要な時間を短縮することで、射出成形は人件費を最小限に抑え、スループットを向上させます。さらに、1時間に大量の部品を生産できるため、費用対効果がさらに高まります。
-
複雑な形状の生産:
- 射出成形では、複雑な形状で公差の小さい部品の生産が可能です。これは、複雑な設計や正確な寸法を必要とする産業にとって特に有益です。このプロセスにより、最も複雑な形状でも高い精度で製造することができます。
-
安定した収縮率:
- 射出成形の主な利点の一つは、一貫した収縮率で部品を製造できることです。この一貫性は、最終製品の寸法精度と品質を維持するために非常に重要です。一貫した収縮率により、各パーツが要求仕様を満たすことが保証され、生産後の調整の必要性が減少します。
-
高い繰り返し精度:
- 射出成形は再現性の高いプロセスであり、生産される各部品は前回とほとんど同じです。この再現性は、一貫性と品質が最優先される大量生産には不可欠です。このプロセスにより、すべての部品が同じ高い基準を満たすことが保証され、欠陥のリスクが減少し、製品全体の信頼性が向上します。
-
素材の多様性:
- 射出成形は、さまざまなプラスチックや液状シリコーンゴムのようなエラストマーなど、幅広い材料に使用することができます。この多様性により、メーカーは特定の用途に最も適した材料を選択することができ、最終製品が望ましい性能基準を満たすことを保証します。
-
大量生産:
- 射出成形は、最初のセットアップが完了すれば、1時間に大量の部品を生産することができます。そのため、高い生産量と効率が重要な大量生産に理想的な選択肢となります。射出成形が様々な産業で広く使用されている主な理由の一つは、迅速かつ安定的に大量の部品を生産する能力です。
まとめると、射出成形には、硬化時間の短縮、費用対効果、複雑な形状の製造能力、一貫した収縮率、高い再現性、材料の多様性、大量生産能力など、数多くの利点があります。これらの利点により、高品質な部品を効率的かつ経済的に生産したい製造業者にとって、射出成形は好ましい選択肢となっている。
総括表
利点 | 特徴 |
---|---|
硬化時間の短縮 | 成形サイクルは、他の方法では10~20分かかるのに対し、10秒程度で完了する。 |
費用対効果 | 人件費を最小限に抑え、大量生産のスループットを向上させます。 |
複雑な形状と公差 | 複雑なデザインと精密な寸法の小さな部品を生産します。 |
一貫した収縮率 | 寸法精度を確保し、生産後の調整を軽減します。 |
高い繰り返し精度 | 実質的に同一の部品を生産し、一貫性と品質を保証します。 |
材料の多様性 | 様々なプラスチックやエラストマーに対応し、多様な用途に使用できます。 |
大量生産 | 1時間に大量の部品を生産する大量生産に最適です。 |
製造工程を強化する準備はできていますか? 今すぐご連絡ください 射出成形がお客様のビジネスにどのようなメリットをもたらすか、今すぐお問い合わせください!