押出成形は、材料をダイに押し込んで成形する製造工程である。押出成形には、以下の2つの基本タイプがある。 熱間押出 および 冷間押出 熱間押出は高温で行われ、材料の成形が容易である。熱間押出成形は高温で行われるため材料の成形が容易で、自動車や航空宇宙部品の製造によく使用される。一方、冷間押出は室温または室温に近い温度で行われるため、最終製品の強度が高くなり、ファスナーや精密自動車部品の製造によく使用されます。以下では、この2つのタイプのプロセス、用途、利点を中心に詳しく説明します。
キーポイントの説明
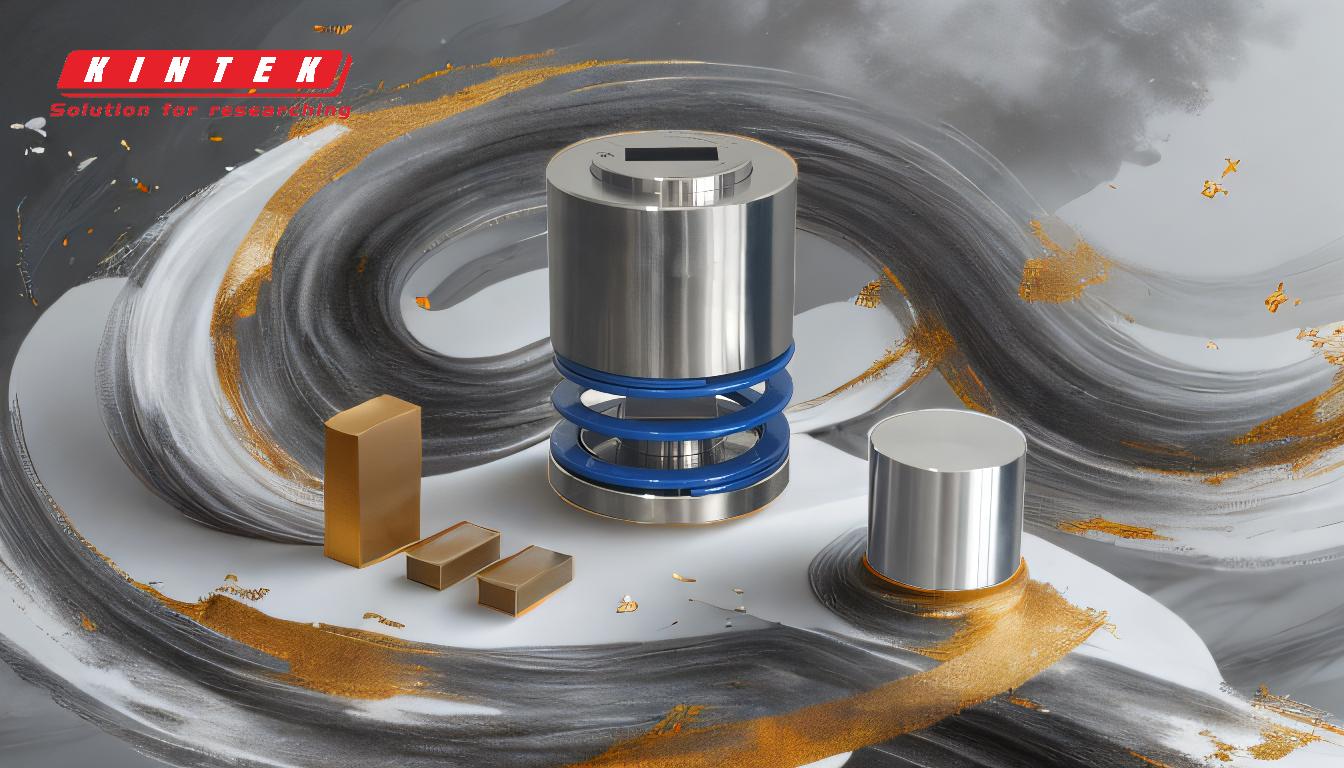
-
熱間押出
- 定義:熱間押出は、材料(一般的にはアルミニウム、銅、鋼鉄などの金属)を再結晶温度以上に加熱してから、ダイスに押し込む。
-
工程:
- 材料を高温(多くの場合、融点の50%から75%)に加熱して硬度を下げ、展延性を高める。
- 軟化した材料は、次に、実験室用油圧プレスを用いて金型に押し込まれる。 油圧プレス または機械式プレスで所望の形状に仕上げる。
-
用途:
- 自動車部品(エンジン部品、フレームなど)。
- 航空宇宙部品(構造要素、タービン部品など)
- 大型構造部品(梁、レールなど)。
-
利点:
- 材料の硬度が低いため、成形が容易。
- 複雑な形状や大きな断面の製造に適している。
- 冷間押出しに比べ、必要な力が小さい。
-
制限事項:
- 加熱によるエネルギー消費量の増加。
- 材料表面の酸化やスケールの可能性。
-
冷間押出
- 定義:冷間押出は、室温または室温に近い温度で行われ、材料は大きな加熱なしにダイスを通して押し出される。
-
プロセス:
- 材料は通常、延性を向上させるために前処理(アニールなど)が施される。
- を使い、材料に高圧を加える。 ラボプレス 金型に押し込んで目的の形状を作ります。
-
用途:
- ファスナー(例:ボルト、ナット、ネジ)。
- 自動車部品(例:ギア、シャフト)
- 自転車部品(クランク、スプロケットなど)。
-
利点:
- 加工硬化により、より強く耐久性のある部品ができる。
- 表面仕上げと寸法精度が向上
- 熱間押出に比べてエネルギー消費量が少ない
-
制限事項:
- 必要な力が大きく、部品のサイズが制限される可能性がある。
- 室温で十分な延性を持つ材料に限定される。
-
熱間押出と冷間押出の比較
- 温度:熱間押出は高温で行われ、冷間押出は室温または室温付近で行われる。
- 材料特性:熱間押出は材料の硬度を下げて成形しやすくし、冷間押出は加工硬化によって材料の強度を高める。
- 用途:熱間押出成形は大型で複雑な部品に最適であり、冷間押出成形は小型で精密な部品に適している。
- エネルギー消費:熱間押出は加熱に大きなエネルギーを必要とするが、冷間押出はエネルギー効率が高い。
- 表面仕上げ:通常、冷間押出成形は熱間押出成形に比べて表面仕上げが良く、公差も厳しくなります。
-
熱間押出と冷間押出の選択
- 材料の種類:常温での成形が困難な材料には熱間押出が好まれ、アルミニウムや鋼のような延性のある材料には冷間押出が適している。
- 部品サイズ:熱間押出は大きな部品に適しており、冷間押出は小さくて複雑な部品に最適です。
- 強度要件:加工硬化により高い強度と耐久性が要求される場合は、冷間押出成形が好ましい。
- コスト:小型部品の大量生産には冷間押出の方が費用対効果が高く、大型で複雑な形状には熱間押出の方が経済的である。
熱間押出しと冷間押出しの違いを理解することで、メーカーは材料、希望する特性、用途の要件に基づいて適切な方法を選択することができます。どちらの技術も現代の製造業において重要な役割を果たしており、さまざまな製品を製造する上で独自の利点を提供しています。
総括表
側面 | 熱間押出 | 冷間押出 |
---|---|---|
温度 | 高温(融点の50~75) | 室温またはそれより少し高い温度 |
材料特性 | 硬度が低く、成形が容易 | 加工硬化による強度向上 |
用途 | 自動車、航空宇宙、大型構造部品 | ファスナー、精密自動車部品、自転車部品 |
エネルギー消費 | 暖房により高い | より低く、よりエネルギー効率的 |
表面仕上げ | 酸化やスケーリングの可能性 | より良い表面仕上げとより厳しい公差 |
部品サイズ | 大きく複雑な形状に最適 | 小さくて複雑な部品に最適 |
強度要件 | 必要な力が小さい | 加工硬化による高い強度と耐久性 |
コスト面 | 大型で複雑な形状には経済的 | 小型部品の大量生産に適したコスト効率 |
お客様のプロジェクトに適した押出成形方法の選択にお困りですか? 当社の専門家に今すぐご連絡ください にご相談ください!