熱分解は、酸素のない状態で有機物を分解する熱分解プロセスである。通常、乾燥、熱分解、冷却の3段階で行われる。各段階は、原料をバイオ炭、バイオオイル、合成ガスなどの価値ある製品に変える上で重要な役割を果たす。プロセスは、温度、滞留時間、原料の種類などの要因に影響される。これらの段階を理解することは、熱分解リアクターの設計と運転を最適化するために不可欠である。 熱分解リアクター 効率的に所望の出力を達成するために
重要なポイントを解説:
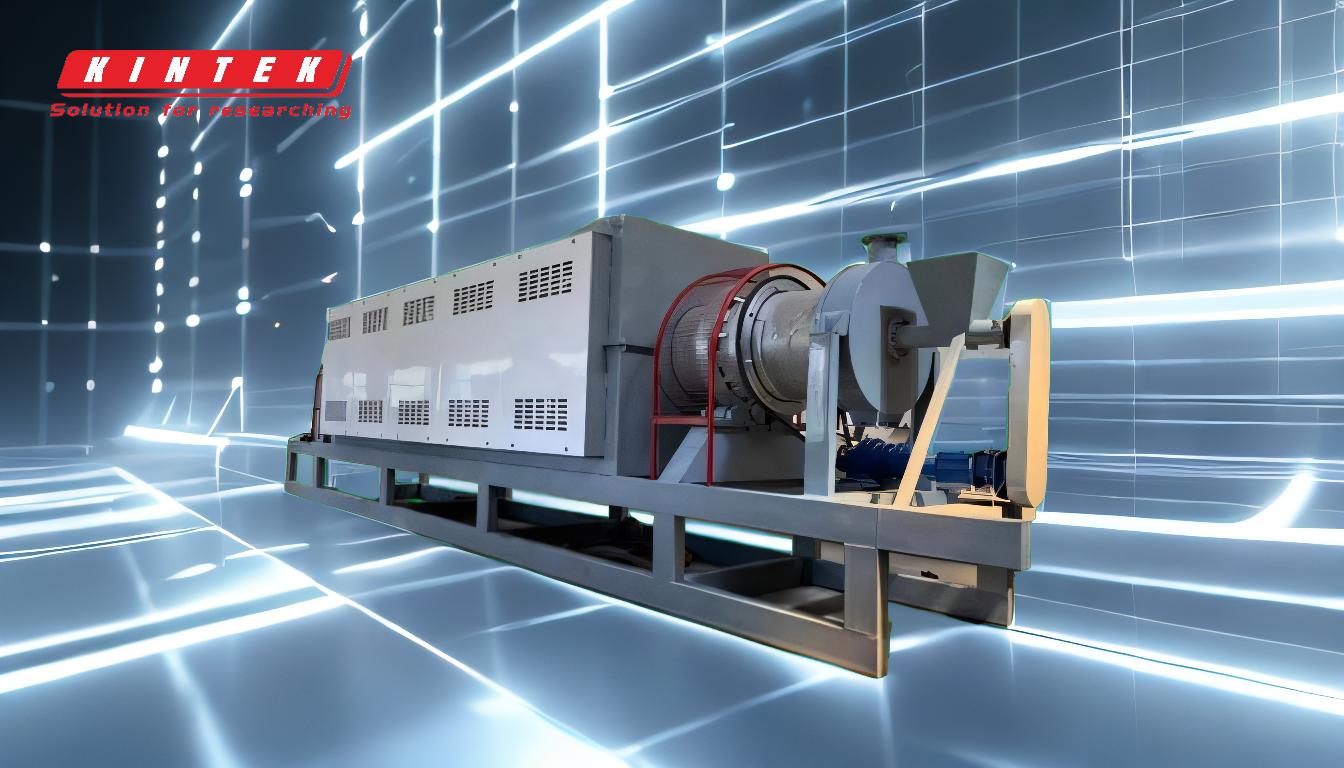
-
乾燥段階
- 熱分解の第一段階は、原料から水分を除去することである。
- 水分は熱分解プロセスを妨げ、反応器の効率を低下させるため、この段階は極めて重要である。
- この段階の温度は、化学分解を起こさずに水分を蒸発させるため、通常100℃から150℃と比較的低い。
- 適切な乾燥により、その後の熱分解反応が均一かつ効率的に行われるようになります。
-
熱分解段階
- 第2段階は熱分解プロセスの中核で、乾燥した原料が熱分解を受ける。
- この段階は酸素がない状態で行われ、燃焼を防ぎ、原料をより小さな分子に分解する。
-
希望する生成物によって、温度は300℃から800℃の範囲となる。
- 低速熱分解:低温(300℃~500℃)で運転し、滞留時間が長く、バイオ炭の生産に有利。
- 高速熱分解:高温(500℃~800℃)、短い滞留時間で運転し、バイオオイルの収率を最大化。
-
原料は3つの主要製品に変換される:
- バイオ炭:炭素を多く含む固体残渣。
- バイオオイル:有機化合物の液体混合物。
- 合成ガス:水素、一酸化炭素、メタンの混合ガス。
-
冷却段階
- 最終段階では、生成物を冷却して安定化させ、さらなる反応を防止する。
- バイオ炭は通常冷却され、土壌改良材や燃料として使用するために回収される。
- バイオオイルは気相から凝縮され、さらなる精製や燃料として使用するために貯蔵される。
- 合成ガスはしばしば洗浄され、再生可能エネルギー源や化学合成の原料として使用される。
- 効率的な冷却は、製品の品質と有用性を確保するために不可欠です。
乾燥、熱分解、冷却という3つの段階を理解することで、オペレーターは熱分解リアクターの性能を最適化することができる。 熱分解リアクター は、特定の製品収率を達成し、全体的なプロセス効率を向上させる。運転条件(温度、滞留時間、原料の種類)の選択は、各段階の結果と最終製品の分布に大きく影響する。
総括表:
ステージ | キー詳細 | 温度範囲 | 出力 |
---|---|---|---|
乾燥 | 原料から水分を除去し、効率的な熱分解を実現します。 | 100°C-150°C | 乾燥原料 |
熱分解 | 酸素のない状態での熱分解。バイオ炭、バイオオイル、合成ガスを生成する。 | 300°C-800°C | バイオ炭、バイオオイル、合成ガス |
冷却 | 製品を安定させ、さらなる反応を防ぎ、使用性を確保する。 | 種類 | 安定したバイオ炭、バイオオイル、合成ガス |
熱分解プロセスを最適化する準備はできましたか? 当社の専門家に今すぐご連絡ください オーダーメイドのソリューションを