ボールミルとチューブミルは、どちらも粉砕・混合工程で広く使用されていますが、ボールミルはチューブミルに比べていくつかの明確な利点があります。ボールミルは汎用性が高く、粒径10ミクロン程度の非常に微細な粉体を作ることができ、湿式・乾式どちらの粉砕プロセスにも適しています。ボールミルは、密閉式なので安全で無菌であるため、有毒物質や摩耗性物質の粉砕に特に効果的です。さらに、ボールミルは信頼性が高く、エネルギー消費量が少なく、メンテナンスが容易なことでも知られており、多くの産業用途に適しています。コンパクトな設計で連続運転が可能なため、チューブミルに比べて効率性と実用性がさらに向上します。
キーポイントの説明
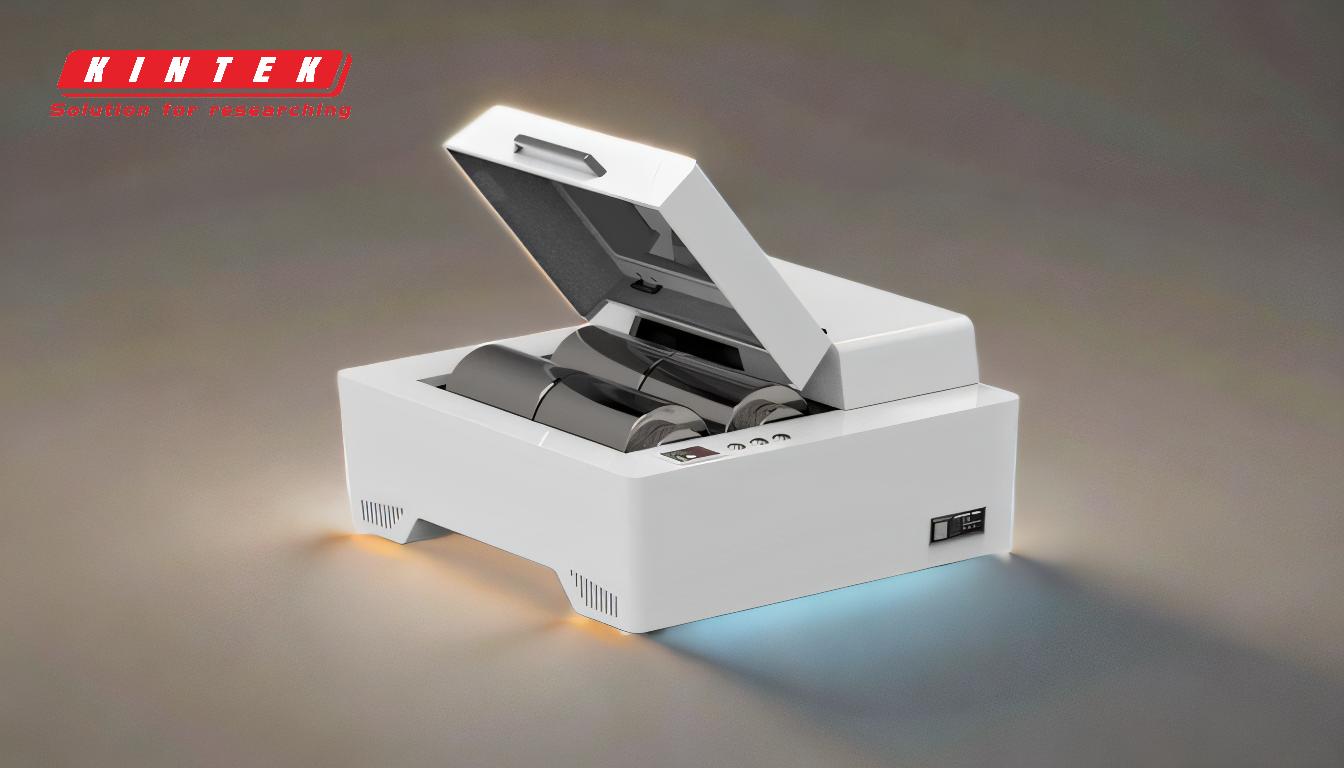
-
より細かい粒子径:
- ボールミルは、粒径10ミクロン以下の非常に微細な粉体を製造することができます。
- 医薬品、化粧品、先端材料製造などの業界では、このレベルの微粉砕が要求されることがよくあります。
- チューブミルは、微粉砕はできても、同じレベルの精密な粒度分布が得られない場合があります。
-
用途の多様性:
- ボールミルは、湿式粉砕、乾式粉砕など幅広い用途に適しています。
- 軟質から硬質、脆性から強靭なものまで、様々な材料に対応でき、汎用性が高い。
- チューブミルは一般的に特殊であり、同じレベルの適応性を提供できない場合があります。
-
安全性と無菌性のための密閉設計:
- ボールミルは密閉システムで設計されているため、有毒物質や危険物質の粉砕に最適です。
- また、密閉された容器システムは、医薬品や食品加工などの産業で重要な無菌性を維持します。
- 開放型スラリーシステムで運転されることの多いチューブミルでは、同じレベルの封じ込めと安全性が得られない場合があります。
-
連続運転能力:
- ボールミルは連続運転が可能なため、安定した生産量を必要とする大規模な工業プロセスに適しています。
- この連続運転はダウンタイムを減らし、全体的な生産性を向上させます。
- チューブミルは連続運転が可能ですが、長時間の運転では効率や信頼性が劣る場合があります。
-
研磨材に対する効果:
- ボールミルは、その堅牢な構造とスチールボールなどの粉砕メディアの使用により、研磨材の粉砕に非常に効果的です。
- 定期的に新しい粉砕メディアを追加することで摩耗を補い、長期間にわたって安定した性能を発揮します。
- チューブミルは、摩耗性の高い原料を扱うため、摩耗が激しくなり、メンテナンスが必要になる場合があります。
-
低エネルギー消費とメンテナンス:
- ボールミルはエネルギー効率に優れ、同じような粉砕作業を行うチューブミルに比べて消費電力が少ない設計になっています。
- メンテナンスの必要性が低く、清掃が簡単でスペースが小さくて済むため、長期的には費用対効果が高くなります。
- チューブミルは、より大型で複雑であるため、より多くのエネルギーとメンテナンスが必要となり、運転コストが増加します。
-
コンパクトな設計とスペース効率:
- ボールミルはコンパクトな設計で、チューブミルに比べて設置スペースが少なくて済みます。
- このスペース効率は、床面積の限られた施設では特に有利です。
- チューブミルはサイズが大きいため、設置環境によっては適さない場合もある。
まとめると、ボールミルはチューブミルに比べ、粒径が細かい、汎用性が高い、安全性が高い、連続運転が可能、研磨材に有効、エネルギー消費量が少ない、コンパクト設計などの利点があります。このような利点から、ボールミルは多くの工業用粉砕・摩砕アプリケーションに適しています。
要約表
利点 | ボールミル | チューブミル |
---|---|---|
粒子径 | 最小10ミクロンの粒子を生成 | 精度の低い粒子径減少 |
汎用性 | 湿式・乾式粉砕に適し、多様な原料に対応 | 特殊性が高く、適応性に劣る |
安全性と無菌性 | 密閉設計により安全性と無菌性を確保 | オープンスラリーシステムは安全性を損なう可能性がある |
連続運転 | 連続運転が可能で、ダウンタイムを短縮 | 連続運転では効率が落ちる |
研磨材ハンドリング | 研磨材に効果的、頑丈な構造 | 高研磨材には不向き。 |
エネルギー消費 | 低いエネルギー消費 | 高いエネルギー必要量 |
メンテナンス | 低メンテナンスで清掃が容易 | より複雑なメンテナンスが必要 |
スペース効率 | コンパクト設計で省スペース | サイズが大きいと環境によっては適さない場合がある |
研削とミリングのプロセスを強化する準備はできていますか? ボールミルについて ボールミルについて詳しく知る