スパッタリング技術は、高い成膜速度、優れた膜の均一性、高融点物質を含む広範な材料に対応できるといった独自の利点により、薄膜形成に広く用いられている。しかし、これらの技術には、システムの複雑さ、基板加熱の可能性、運用コストの上昇といった課題もある。この分析では、スパッタリング技術の主な利点と欠点を探り、その応用と限界について包括的に理解する。
主なポイントを解説
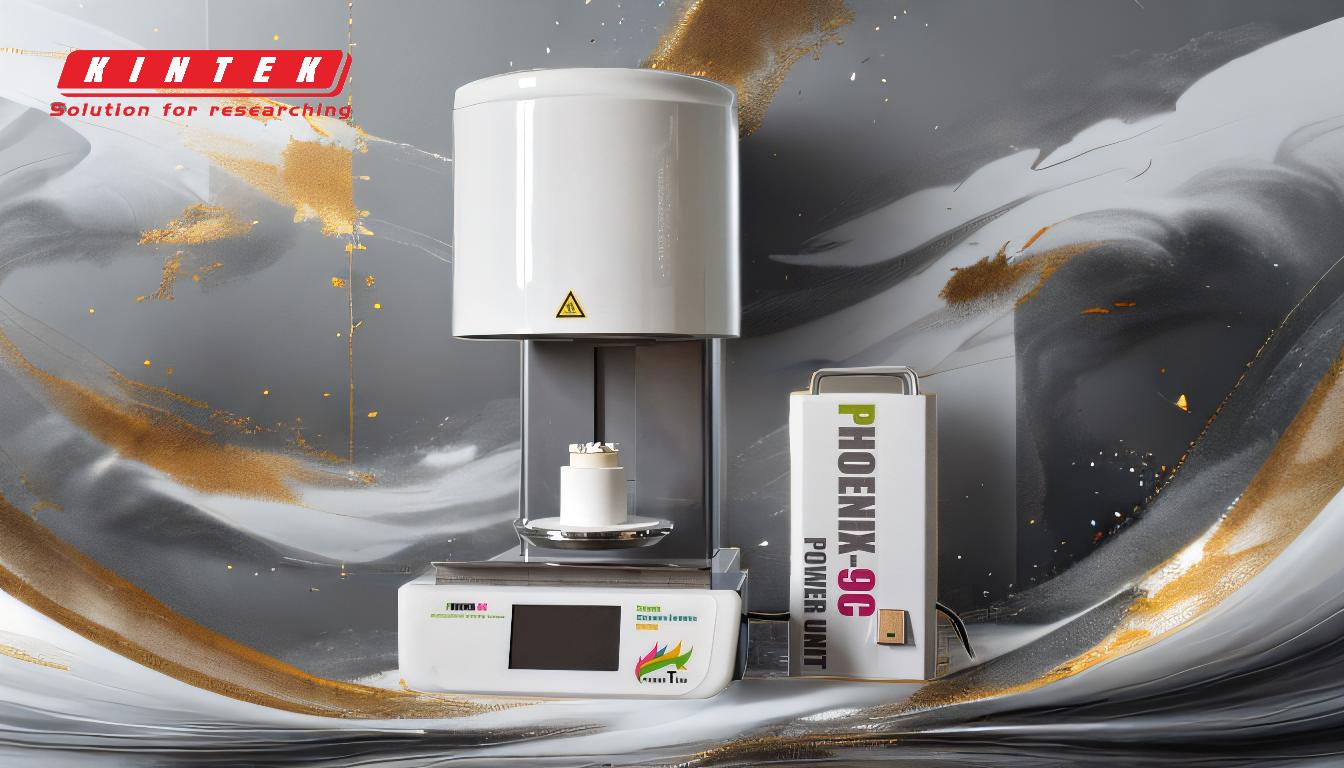
-
スパッタリング技術の利点:
- 高い蒸着率とスループット:スパッタリング技術、特にイオンビームスパッタリング(IBS)は、高い成膜速度とスループットを提供し、大規模生産に効率的です。
- 均一で高密度な膜:スパッタリングにより、低温でも優れた均一性と高密度の膜が得られます。
- 幅広い材料適合性:スパッタリングは、金属、合金、誘電体、さらには他の成膜法では困難な高融点材料など、幅広い材料に適合する。
- 分子レベルの精度:このプロセスでは、成膜を原子レベルで制御することができるため、原始的な界面を形成することができ、精密なパラメータ制御によって膜特性を調整することができる。
- 密着性の向上:スパッタリングされた原子は、蒸着された材料と比較して運動エネルギーが高く、その結果、基板への付着力が強くなります。
- 再現性と自動化:スパッタリングは、熱蒸着や電子ビーム蒸着などの方法と比較して、再現性が高く、プロセスの自動化が容易です。
- 環境および運用上の利点:スパッタリングは大気汚染を起こさず、加熱部分がなく、逆さまを含むさまざまな向きの基板にコーティングできる。
-
スパッタリング技術の短所:
- 高いシステム複雑性とコスト:スパッタリングシステムはセットアップとメンテナンスが複雑で高価であるため、小規模な事業にとっては障壁となりうる。
- 基板加熱:スパッタリング中の通電蒸気は基板を加熱する可能性があり、温度に敏感な材料には好ましくない。
- チャンバーコーティングと表面不純物:このプロセスでは、チャンバーコーティングや潜在的な表面不純物が発生する可能性があり、膜質に影響したり、追加の洗浄工程が必要になったりする。
- 誘電体の成膜レートが悪い:スパッタリングは多くの材料でうまく機能するが、誘電体材料の成膜レートは比較的悪く、特定の用途ではその効率が制限される。
- 運用上の課題:このプロセスは複雑で、パラメータを正確に制御し、汚染や欠陥を避けるために慎重に取り扱う必要があります。
-
スパッタリングの応用:
- 薄膜蒸着:スパッタリングは、エレクトロニクス、光学、コーティングなどの用途に適したナノメートルからマイクロメートルの薄膜を成膜するために広く使用されています。
- 表面クリーニングと分析:表面物理学では、スパッタリングは高純度表面のクリーニングや材料の化学組成分析に使用される。
- 合金と複合膜の作成:スパッタリングでは、合金や複合材料を一度に成膜できるため、多層構造の作成に汎用性がある。
-
他の成膜方法との比較:
- 汎用性:スパッタリングは、特に高融点材料において、材料適合性と膜質の点で熱蒸着などの方法を凌駕します。
- 精度と制御:分子レベルの精度を達成し、フィルム特性を制御できることから、スパッタリングは高度な用途に適している。
- コストと複雑さ:スパッタリングは優れた結果をもたらすが、熱蒸発のような単純な方法に比べて複雑でコストがかかる。
要約すると、スパッタリング技術は膜質、材料適合性、精度の面で大きな利点を提供し、多くのハイテク用途に不可欠なものとなっている。し か し 、こ れ に 伴 う 高 い コ ス ト 、シ ス テ ム の 複 雑 性 、運 用 面 で の 課 題 な ど を 、特 定 の 用 途 に こ の 手 法 を 選 択 す る 際 に 慎 重 に 考 慮 す る 必 要 が あ る 。
総括表
側面 | メリット | デメリット |
---|---|---|
蒸着速度 | 高い蒸着速度とスループット、大量生産に最適。 | 誘電体材料の成膜レートが悪い。 |
フィルム品質 | 優れた密着性と再現性を持つ、均一で緻密なフィルム。 | 基板加熱は、温度に敏感な材料に影響を与える場合があります。 |
材料適合性 | 金属、合金、誘電体、高融点材料に対応。 | システムの複雑性と運用コストが高い。 |
高精度 | 分子レベルの制御により、原始的な界面と調整可能な膜特性を実現。 | チャンバーコーティングや表面の不純物は、追加の洗浄が必要な場合があります。 |
環境への影響 | 大気汚染なし、加熱部品なし、汎用性の高い基材コーティング。 | 運用上の課題と潜在的な汚染リスク |
スパッタリング技術で薄膜成膜プロセスを向上させる方法をご覧ください。 今すぐご連絡ください までご連絡ください!