圧縮成形とトランスファー成形は、どちらもゴムやプラスチック部品の製造に広く使われている技術だが、その工程、設備、用途は大きく異なる。圧縮成形は金型のキャビティに直接材料を入れ、圧力をかけて成形するのに対し、トランスファー成形は金型に押し込む前に別のチャンバーで材料を予熱・加圧します。これらの違いは、材料効率、複雑さ、コストなどの要素に影響し、それぞれの方法を特定の使用ケースに適したものにします。
キーポイントの説明
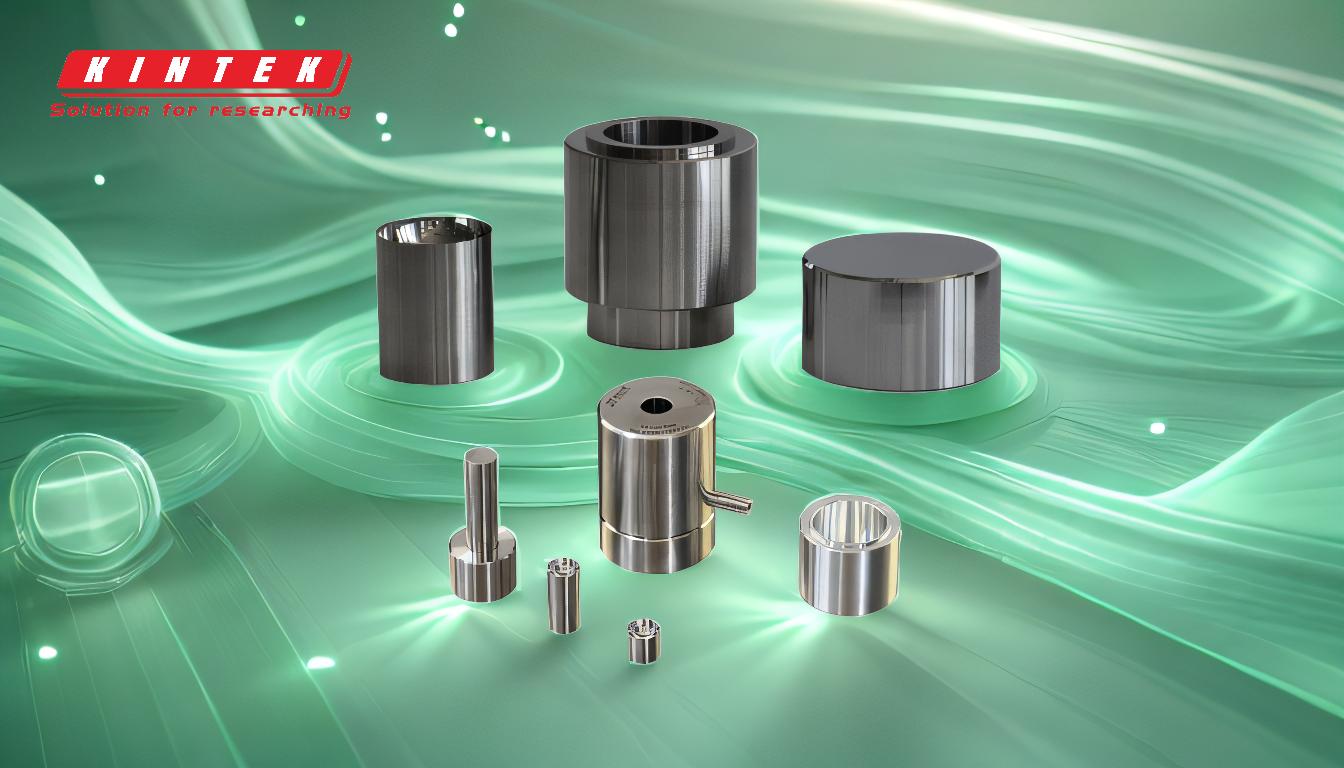
-
プロセスの違い:
-
圧縮成形:
- 材料を金型のキャビティに直接入れる。
- 金型を閉じ、圧力をかけて材料を成形する。
- モールドフラッシュと呼ばれる余分な材料は、特殊な溝から流れ出る。
- 部品や工程が少ないため、よりシンプルでコスト効率が高い。
-
トランスファー成形:
- 材料は別のチャンバー(ポット)で予熱・加圧される。
- ピストンが穴を通して材料を金型キャビティに押し込む。
- 部品(プランジャー、ポット、ピストン)が追加されるため、より複雑になる。
-
圧縮成形:
-
設備と工具:
-
圧縮成形:
- 部品点数が少なく、シンプルなセットアップが必要。
- 通常、加圧にはプラテンプレスを使用。
- 金型費が安く、リードタイムが短い。
-
トランスファー成形:
- プランジャー、シリンダー(ポット)、金型キャビティを含む。
- 金型が複雑で初期コストが高い。
- 複雑な設計や小さな部品に適している。
-
圧縮成形:
-
材料効率:
-
圧縮成形:
- 射出成形に比べて材料のロスが少ない。
- 余分な材料(モールドフラッシュ)はリサイクルや再利用が可能。
-
トランスファー成形:
- 移送プロセスによる材料ロスが大きくなる可能性がある。
- しかし、材料の流れや配置をよりよく制御することができる。
-
圧縮成形:
-
用途と適性:
-
圧縮成形:
- 複雑なデザインではなく、よりシンプルで大きな部品に最適。
- 実験室やコスト重視のプロジェクトでよく使われる。
-
トランスファー成形:
- 複雑で入り組んだ細部の部品に適している。
- 電子機器や自動車など、高い精度が要求される産業でよく使用される。
-
圧縮成形:
-
コストと効率:
-
圧縮成形:
- 設備がシンプルで材料ロスが少ないため、一般的にコスト効率が高い。
- より単純な部品では、より速い生産時間。
-
トランスファー成形:
- 工具や設備が複雑になるため、初期コストが高くなる。
- 複雑な部品の場合、二次加工の必要性が減り、効率が良くなる可能性がある。
-
圧縮成形:
まとめると、圧縮成形とトランスファー成形はどちらもゴムやプラスチック材料を成形するための効果的な技術ですが、それぞれ目的が異なり、適しているプロジェクトの種類も異なります。圧縮成形は、よりシンプルで費用対効果が高いため、大型であまり複雑でない部品に適しています。一方、トランスファー成形は精度と制御性が高く、複雑で詳細な部品に適しています。これらの違いを理解することで、特定の製造ニーズに適した方法を選択することができる。
総括表
側面 | 圧縮成形 | トランスファー成形 |
---|---|---|
工程 | 材料を金型キャビティに直接入れる | ポットで予熱・加圧された材料 |
設備 | 簡単なセットアップ、プラテンプレス | プランジャー、ポット、ピストンによる複雑なセットアップ |
材料効率 | 材料ロスが少なく、余分な材料は再利用可能 | 材料ロスが多く、流量制御が良い |
用途 | よりシンプルな大型部品 | 複雑で入り組んだ部品 |
コスト | 費用対効果に優れ、金型費用を抑えられる | イニシャルコストは高いが、精密性には優れる |
お客様のプロジェクトに適した成形技術の選択にお困りですか? 当社の専門家に今すぐご連絡ください にお問い合わせください!