圧縮成形は、ゴム、プラスチック、金属などの原材料を、熱と圧力を使って希望の形に成形する製造工程である。この工程は、あらかじめ計量された材料を金型のキャビティに入れることから始まります。その後、金型を閉じ、圧力を加えて材料を圧縮し、流動させてキャビティに充填する。熱はしばしば材料を軟化させ、成形を容易にし、生産をスピードアップするために使われる。モールドフラッシュと呼ばれる余分な材料は、特殊な溝から排出される。この方法は、サンバイザーやギアノブなどの内装部品を作る自動車製造などの業界で広く使われている。しかし、フローライン、ブリスター、未充填部品などの欠陥を避けるためには、材料を正確に測定し、適切な配置を確保するなどの課題に対処する必要があります。
キーポイントの説明
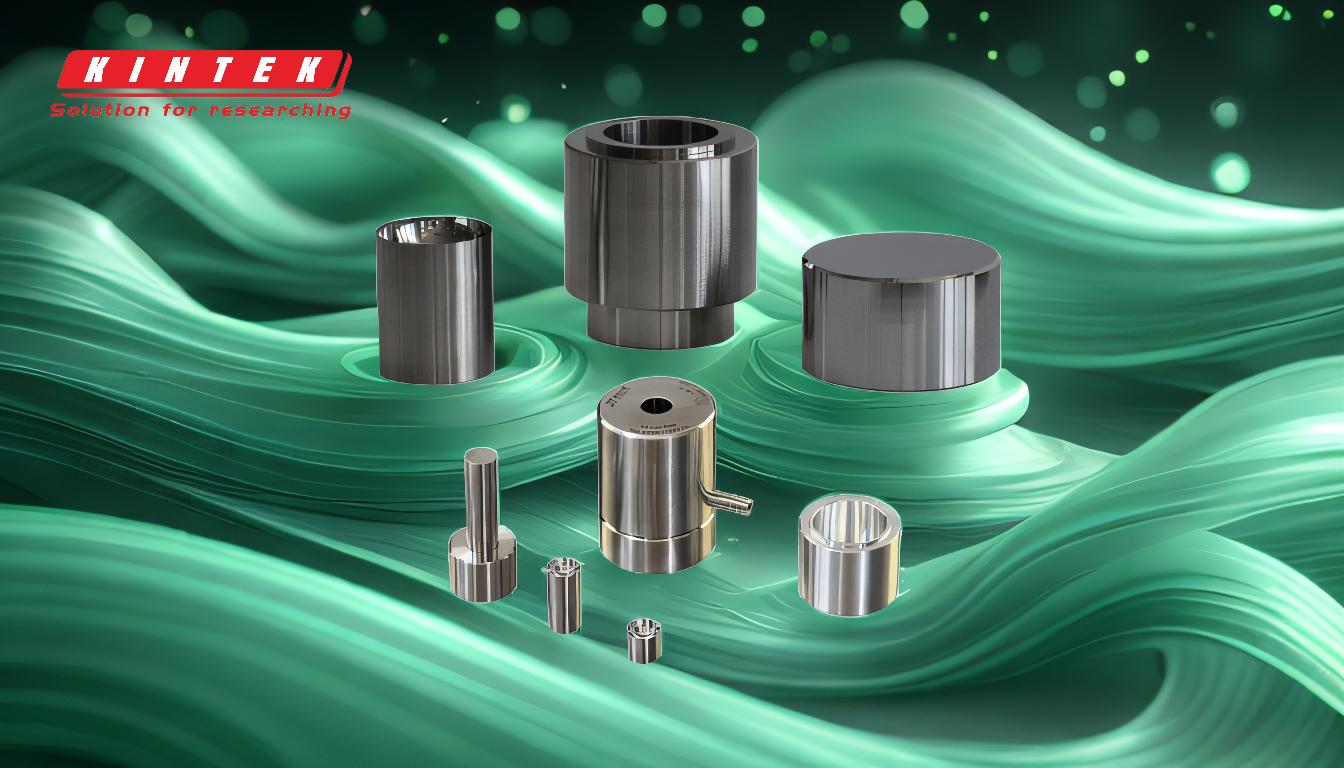
-
金型と素材の準備:
- 素材の選択:ゴム、プラスチック、金属など、目的の製品に応じて適切な原材料を選択します。
- 金型設計:金型が正しいキャビティ形状で設計され、余分な材料(モールドフラッシュ)を逃がす溝があることを確認する。
- 材料の測定:材料を正確に切断または計量し、各キャビティに適量が入るようにする。材料が少なすぎると欠陥の原因となり、多すぎると過剰なフラッシュの原因となります。
-
チャージの挿入:
- プレースメント:金型キャビティの中央に、あらかじめ計量しておいた材料を配置します。均一な分布を確保し、欠陥を避けるためには、適切な配置が重要です。
- 素材形状:金型内の流れがスムーズになるように、形の良い、枝分かれしていないゴムストックなどを使用する。
-
金型を閉じる:
- 圧力印加:上型を閉じ、油圧プレスなどで圧力をかける。圧力によって材料が流れ、キャビティに充填される。
- 温度制御:金型を一定の温度に保つことで、材料を柔らかくし、成形しやすくし、生産工程をスピードアップする。
-
成形:
- マテリアルフロー:圧力と熱の下で、材料は金型キャビティを完全に満たすように流れます。余分な材料はモールドフラッシュとして特殊な溝から排出されます。
- 硬化時間:金型内で材料が硬化し、固化するまでに十分な時間を確保してください。硬化時間は、材料の種類や最終製品に求められる特性によって異なります。
-
部品の取り外し:
- 金型を開く:材料が硬化したら、新しく形成された部分を傷つけないように慎重に金型を開きます。
- フラッシュのトリミング:溝から流れ出た余分な材料(モールドフラッシュ)を取り除きます。このステップでは、追加のトリミングや仕上げ工程が必要になる場合があります。
-
課題と解決策:
- 材料測定:正確な計量が重要です。正確な計量器具や切断器具を使用し、正しい量の材料が使用されるようにする。
- 欠陥防止:適切な配置と適切な圧力は、フローライン、ブリスター、未充填部分などの欠陥を防ぐのに役立ちます。過剰な材料は、除去が困難な重いフラッシュにつながる可能性があります。
- プロセスの最適化:圧力、温度、硬化時間を定期的にモニターし調整することで、プロセスを最適化し、製品の品質を向上させる。
-
アプリケーション:
- 自動車産業:圧縮成形は、サンバイザー、ギアノブ、トリムカバーなどの内装部品の製造に最適です。この工程は効率的で費用対効果が高く、材料の無駄や人件費を削減できます。
- その他の産業:この方法は、単純なプラスチック部品から複雑なゴム部品まで、幅広い製品を製造するために、他のさまざまな産業でも使用されています。
これらのステップに従い、課題に対処することで、圧縮成形は無駄を最小限に抑え、高品質の部品を生産するための非常に効果的な方法となります。
総括表
キーステップ | 説明 |
---|---|
素材の選択 | 製品の要件に応じて、ゴム、プラスチック、金属を選択します。 |
金型の設計 | 余分な材料(モールドフラッシュ)のために適切なキャビティと溝を持つ金型を設計します。 |
材料の測定 | 材料を正確に計量または切断し、欠陥や過剰なフラッシュを避ける。 |
チャージの挿入 | 均等になるように、金型の中央に材料を入れます。 |
型を閉じる | 圧力と熱を加えて材料を柔らかくし、形を整える。 |
部品を成形する | 金型内で材料を流動させ、硬化させる。 |
部品を取り出す | 金型を開き、余分なフラッシュをトリミングしてきれいに仕上げます。 |
用途 | 自動車および工業生産に広く使用されています。 |
圧縮成形で製造プロセスを最適化する準備はできていますか? 当社の専門家に今すぐご連絡ください までご連絡ください!