ダイヤモンドライクカーボン(DLC)コーティングは、強度、耐久性、高性能を保証する高度な蒸着技術を用いて施されます。最も一般的な方法には、物理的気相成長法(PVD)と化学的気相成長法(CVD)があり、高周波プラズマアシストCVD(RF PECVD)やホットフィラメントCVDなどのバリエーションもあります。これらの方法では、真空チャンバー内で制御された環境を作り出し、炭素原子を活性化して基板上に堆積させる。どの方法を選択するかは、基材の材質、希望するコーティングの特性、アプリケーションの要件によって決まる。DLCコーティングは一般的に薄く(0.5~2.5ミクロン)、優れた耐摩耗性、低摩擦性、耐久性を提供します。
キーポイントの説明
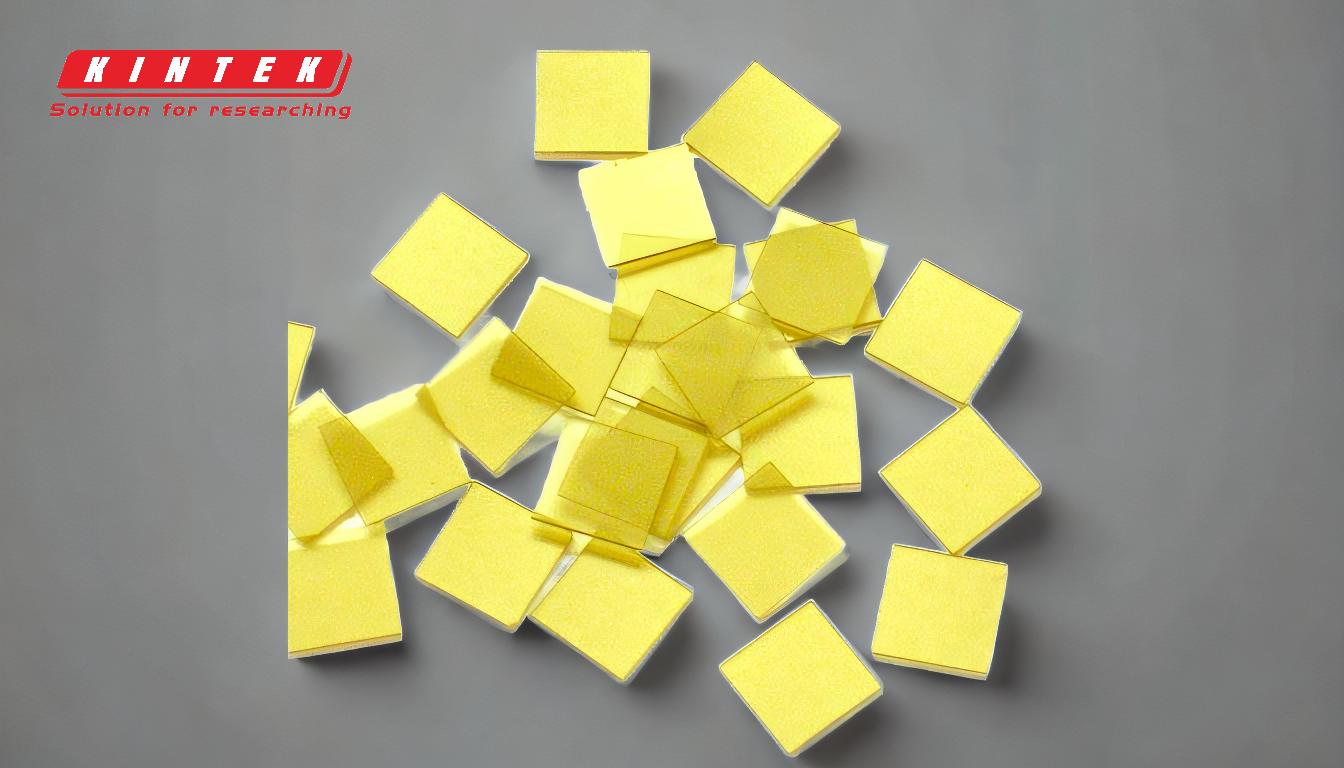
-
DLCコーティングの概要
- DLCコーティングは、sp3結合の割合が非常に高い、薄くて耐久性のある炭素層を形成するために、高度な蒸着技術を用いて施されます。
- コーティングプロセスは、基材の材質や用途に合わせて調整され、最適な性能を保証します。
-
一般的な蒸着法
-
物理蒸着(PVD):
- 原料を蒸発させ、基板上に凝縮させる。
- 超硬工具へのDLCコーティングに適しており、一般的な厚さは0.5~2.5ミクロン。
- コーティングの厚みと均一性を正確に制御できる利点がある。
-
化学気相成長法(CVD):
- 気相(水素やメタンなど)から炭素原子を基板上に堆積させる。
- 一般的な手法には、ホットフィラメントCVD、高周波プラズマアシストCVD(RF PECVD)、マイクロ波プラズマCVD(MPCVD)などがある。
- ガス分子を活性化し、ダイヤモンド膜を形成するには高温(750℃以上)が必要です。
-
物理蒸着(PVD):
-
CVDコーティングのステップ・バイ・ステップ・プロセス
-
準備
- 基材(超硬工具など)を洗浄し、コーティングが適切に付着するように準備する。
-
チャンバーへの装填
- 準備した工具を水素ガスとメタンガスを含む真空チャンバーに入れる。
-
ガス分子の活性化:
- 2,300℃以上に加熱されたタングステンワイヤーがガス分子を分解するエネルギーを供給し、工具を750℃以上に加熱する。
-
炭素原子の堆積:
- 活性化された炭素原子が工具表面で再結合し、純粋なダイヤモンド膜が形成される。
-
冷却と取り出し
- 蒸着後、工具は冷却され、チャンバーから取り出され、使用可能な状態になります。
-
準備
-
さまざまな方法の利点
-
PVD:
- 処理温度が低く、温度に敏感な基板に適している。
- 膜厚の精度と均一性が高い。
-
CVD:
- 密着性に優れた高品質で純粋なダイヤモンド膜を生成。
- 高温用途や過酷な条件に耐える基板に最適。
-
PVD:
-
DLCコーティングの用途
-
切削工具:
- 耐摩耗性を高め、工具の寿命を延ばす。
-
自動車部品
- エンジン部品の摩擦を減らし、燃費を向上させる。
-
医療機器
- 手術器具に生体適合性と耐摩耗性を提供。
-
エレクトロニクス
- ハードドライブやセンサーなどの部品の耐久性と性能を向上させる。
-
切削工具:
-
装置および消耗品購入者のための考慮事項
-
基板の適合性:
- 選択した方法が基材(超硬、鋼、セラミックなど)に適合することを確認する。
-
コーティングの厚さと均一性:
- 特定の用途に必要な厚さと均一性を評価する。
-
コストと拡張性:
- 選択した方法の大規模生産に対する費用対効果と拡張性を検討する。
-
環境と安全要因:
- 成膜プロセスにおける環境への影響と安全要件を評価する。
-
基板の適合性:
これらの重要なポイントを理解することで、装置や消耗品の購入者は、特定のニーズに最適なDLCコーティング方法について、情報に基づいた決定を下すことができ、最適な性能と費用対効果を確保することができます。
総括表
アスペクト | 詳細 |
---|---|
一般的な方法 | PVD、CVD(RF PECVD、ホットフィラメントCVD) |
膜厚 | 0.5~2.5ミクロン |
主な利点 | 耐摩耗性、低摩擦、耐久性 |
用途 | 切削工具、自動車部品、医療機器、電子機器 |
基板適合性 | 超硬, スチール, セラミックス |
温度範囲 | PVD:より低い温度、CVD:750℃以上 |
環境要因 | 真空チャンバー、制御されたガス環境 |
お客様のニーズに最適なDLCコーティングをご提案します。 今すぐ専門家にお問い合わせください !