導入
目次
静水圧プレスは、高品質で複雑な部品を製造するために使用される重要な製造プロセスです。静水圧プレスの一般的な 2 つの方法は、湿式バッグ静水圧プレスと乾式バッグ静水圧プレスです。このブログ投稿では、これら 2 つの方法を調べて比較し、その違い、利点、制限、さまざまなシナリオへの適合性を理解します。アイソスタティックプレスを初めて使用する場合でも、代替方法を探している場合でも、この比較研究は情報に基づいた決定を下すのに役立ちます。それでは、ウェットバッグとドライバッグの静水圧プレスの世界に飛び込んで探索してみましょう!
冷間静水圧プレスを理解する
冷間静水圧プレスの概要
冷間静水圧プレス (CIP) は、粉末に圧力を加えて室温で粉末材料を形成するために使用される技術です。圧力は通常 100 ~ 600 MPa であり、このプロセスは水、油、またはグリコール混合物などの液体媒体を使用して実行されます。 CIP の目標は、取り扱いや加工に十分な強度を備えた「未加工」部品を取得し、その後さらに焼結して最終強度を達成することです。
金属の場合、冷間静水圧プレスは理論上の密度約 100% を達成できますが、セラミック粉末の場合、密度は約 95% に達します。この技術は、さらなる焼結または熱間静水圧プレスプロセス用のブランクを製造するために一般的に使用されます。
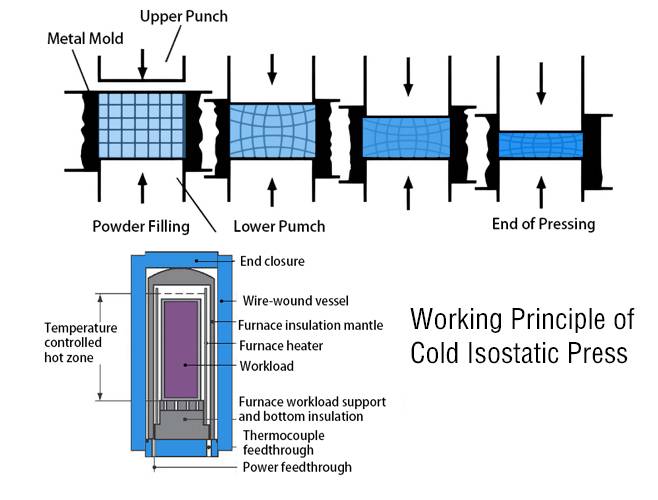
ウェットバッグ法とドライバッグ法の違い
冷間静水圧プレスはさらに湿式バッグ法と乾式バッグ法の2つの方法に分けられます。
ウェットバッグ法
ウェットバッグ法では、粉末材料を柔軟なモールドバッグに封入します。次に、このバッグを圧力容器内の高圧液体に浸します。等静圧が金型の外面に適用され、粉末が所望の形状に圧縮されます。ウェットバッグ法は複雑な形状の部品の生産に最適で、少量生産から大量生産まで対応可能です。さらに、大型製品のプレスも可能になります。
ドライバッグ法
一方、ドライバッグ法では、圧力容器自体の中に一体型の金型を作成します。粉末を型に加え、密閉します。圧力が加えられ、圧縮が完了するとパーツが取り出されます。ドライバッグ法ではウェットバッグ法で必要となる別途の浸漬工程が不要となり、自動化が容易になります。
ウェットバッグ法とドライバッグ法の両方に利点があり、さまざまな用途に適しています。 2 つの方法のどちらを選択するかは、プロジェクトの具体的な目標と関連する材料の特性によって異なります。
要約すると、冷間静水圧プレスは、室温で粉末材料を形成するための貴重な技術です。高密度の部品の製造が可能であり、金属とセラミックスの両方に使用できます。湿式バッグ法と乾式バッグ法は、目的の圧縮を達成するための異なるアプローチを提供しますが、湿式バッグ法は複雑な形状や大量生産に適しています。これらの方法の違いを理解すると、特定のニーズに最も適したアプローチを決定するのに役立ちます。
ウェットバッグ静水圧プレス
ウェットバッグ静水圧プレスの工程
湿式バッグ静水圧プレスでは、粉末を金型に充填し、圧力容器の外側でしっかりと密閉します。次に、金型を容器内の圧力流体に浸します。等静圧が金型の外面に適用され、粉末が圧縮されて固体の塊になります。このプロセスは他のタイプの冷間静水圧プレスに比べて時間がかかり、5 ~ 30 分かかります。ただし、大容量ポンプとローディング機構の進歩により、プロセスのスピードアップが可能になります。
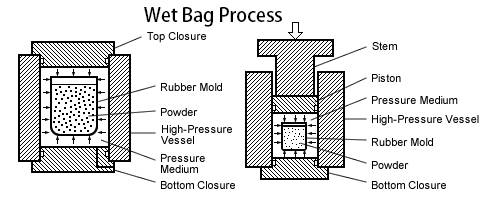
ウェットバッグ静水圧プレスを使用する利点
ウェットバッグ静水圧プレスにはいくつかの利点があります。応用性が高く、実験研究や小ロット生産に適しています。 1 つの高圧シリンダーで複数の異なる形状の部品を同時にプレスし、大型で複雑な部品を製造できます。製造プロセスが短く、コスト効率が高くなります。湿式バッグプロセスでは、ある程度複雑な形状をエラストマー金型に加工することもでき、高いコンパクト密度を実現します。
ウェットバッグ静水圧プレスを使用するための理想的なシナリオ
湿式バッグ静水圧プレスは、大型部品の製造に特に適しています。これは、高い成形密度が必要な業界や、一軸プレスでは複雑な形状を成形できない業界で一般的に使用されています。ただし、金型のロードとアンロードにより自動化が制限され、湿式バッグプレスの生産性が低下する可能性があることに注意することが重要です。工具のコストとプロセスの複雑さも、一軸プレスに比べて高くなります。
要約すると、湿式バッグ静水圧プレスは、高密度で大型で複雑な部品を製造するための多用途かつ効率的な方法を提供します。実験研究、小ロット生産、複雑な形状を必要とする産業に特に有益です。自動化と生産性の点ではいくつかの制限があるかもしれませんが、技術の進歩により湿式バッグ静水圧プレスの効率は向上し続けています。
ドライバッグ等方圧プレス
ドライバッグ静水圧プレスの工程
ドライバッグ静水圧プレスは、軸対称形状の小物部品に使用される製造方法です。スパークプラグ用の高品質セラミックボディの製造によく使用されます。このプロセスには、加圧液体に浸されたエラストマー型の中で乾燥または半乾燥粉末を圧縮することが含まれます。粉末は、スチールマンドレルなどの剛性工具と柔軟なエラストマー型を組み合わせて成形されます。セラミックの一般的な成形圧力は 21 ~ 210 MPa (3000 ~ 30000 psi) の範囲です。ドライバッグ静水圧プレスの主な利点の 1 つは、ゴム製ツールが装置に統合されており、個別の浸漬および除去のステップが不要になることです。これにより、自動化が容易になり、生産速度が速くなります。
ドライバッグ静水圧プレスを使用する利点
ドライバッグ静水圧プレスは、製造プロセスにおいていくつかの利点をもたらします。第一に、特に点火プラグ用の高品質セラミック本体の製造が可能になります。統合された金型とゴム工具により自動化が容易になり、生産率が向上します。さらに、このプロセスにより、圧縮された部品の均一な密度と低い応力が保証され、焼成中の歪みが最小限に抑えられます。これにより、困難で費用がかかる後続の機械加工の必要性が軽減されます。全体として、ドライバッグ静水圧プレスは、軸対称形状の小型部品に対して効率、精度、費用対効果をもたらします。
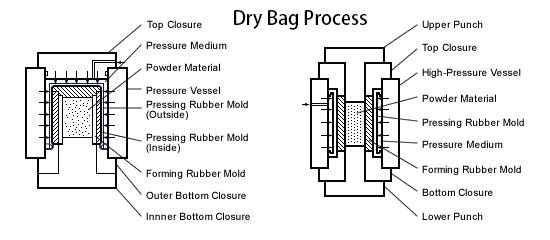
ドライバッグ静水圧プレスを使用するための理想的なシナリオ
ドライバッグ静水圧プレスは、軸対称形状の小型部品を製造する必要があるシナリオに理想的な製造方法です。特にスパークプラグ用の高品質セラミックボディの製造に適しています。ゴム製工具を装置に統合することで自動化が容易になり、大量生産に適しています。この方法は効率的、正確で、コスト効率が高く、軸対称形状の小型部品を必要とする業界にとって好ましい選択肢となっています。
ドライバッグ静水圧プレスの限界
ドライバッグ静水圧プレスには多くの利点がありますが、一定の制限もあります。制限の 1 つは、加圧液体による圧縮を受けない金型の側面に摩擦があることです。これにより、機械的プレスや押し出しなどの他のプレス方法と比較して、フレキシブルバッグに隣接するプレス面の精度が低くなる可能性があります。これにより、所望の表面仕上げを達成するためにその後の機械加工が必要になる場合があります。さらに、ドライバッグプロセスには他の方法と比較して形状とサイズの制限が多く、特定の用途に必要な表面機能を開発するためにグリーンマシニングが必要になる場合があります。
結論として、ドライバッグ静水圧プレスは、特にスパーク プラグ用の高品質セラミック体の製造において、軸対称形状の小型部品の貴重な製造方法です。効率、精度、コスト効率が高く、このようなコンポーネントを必要とする業界にとって理想的な選択肢となります。ただし、特定の用途への適合性を判断する際には、プレス面の精度の低下や形状やサイズの制限など、プロセスの制限を考慮することが重要です。
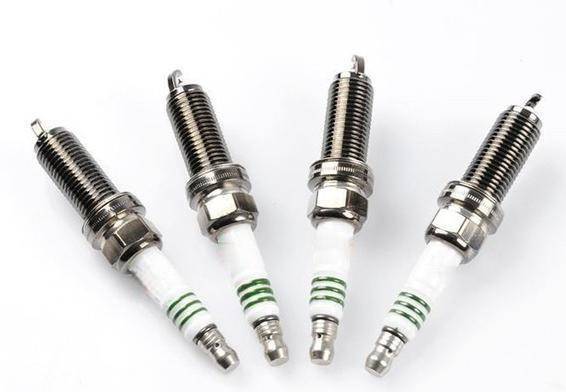
ウェットバッグとドライバッグ等方圧プレスの比較
製造工程とコストの比較
湿式バッグ静水圧プレスでは、粉末を成形型に入れ、シール後に高圧シリンダーに入れてプレスします。プレス中、金型は完全に液体に浸され、圧力伝達媒体と直接接触します。この方法は実験研究や小ロット生産に適しています。 1 つの高圧シリンダーで形状の異なる複数の部品を同時にプレスできるため、大型で複雑な部品の製造に最適です。製造プロセスが短く、コスト効率が高くなります。
静水圧プレスのドライバッグのバリエーションには、圧力容器に統合された金型の作成が含まれます。このプロセスでは、粉末が金型に追加され、密閉され、圧力が加えられて、部品が取り出されます。乾式バッグ法は、金型が容器と一体化しているため、湿式バッグ法に比べて自動化が容易です。小型部品の生産に適しており、より高い生産速度を実現します。
自動化と運用サイクルの比較
ウェットバッグ法では金型の搬入出が必要となるため、生産性が低下し、自動化が制限されます。一方、一体化された金型を備えたドライバッグ法では、自動化が容易になり、生産率が向上します。ウェットバッグ静水圧プレスの操作サイクルには、圧力容器から金型を取り外し、部品を取り出し、このプロセスを繰り返すことが含まれます。ドライバッグ法では、金型を密閉し、圧力を加えて部品を取り出します。
異なる生産量に対する適合性の比較
湿式バッグ静水圧プレスは、実験研究や小ロット生産に特に適しています。 1つの高圧シリンダーで形状の異なる複数の部品を同時にプレスできるため、大型で複雑な部品の製造に適しています。一方、ドライバッグ法は小型部品の生産に適しており、生産率が高くなります。
製品のサイズと形状の制限の比較
湿式バッグ静水圧プレスは、乾式バッグ法と比較して、大型部品の製造に適しています。これは、形状の異なる複数の部品を 1 つの高圧シリンダーで同時にプレスできるためです。しかし、湿式バッグ法における金型のロードおよびアンロードは生産性を低下させ、自動化を制限します。一体化された金型を備えたドライバッグ法では、自動化が容易になり、生産率が向上します。どちらのタイプの静水圧プレスも、一軸プレスと比較して工具コストが高く、プロセスが複雑です。
静水圧プレスは、ウェットバッグであろうとドライバッグであろうと、高いコンパクト密度を達成し、一軸プレスでは圧縮できない形状にアクセスするためによく選択されます。ウェットバッグ法を使用すると、ある程度複雑な形状をエラストマー金型に加工することができます。湿式バッグプロセスには、摩擦がほとんどないため、密度が高くなるという利点もあります。ドライバッグ法は自動化と生産速度の点で優れています。
全体として、ウェットバッグとドライバッグ静水圧プレスのどちらを選択するかは、必要な部品のサイズ、形状、生産量、自動化レベルなど、生産プロセスの特定の要件によって異なります。
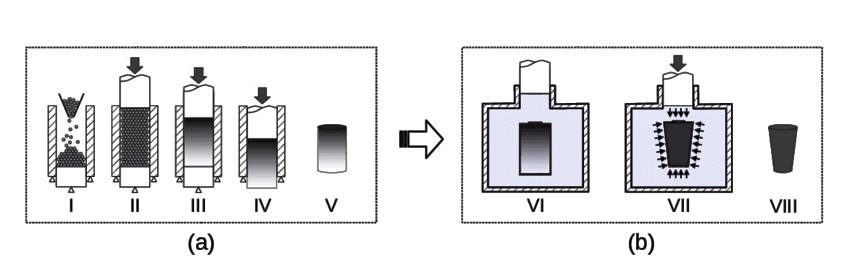
結論
結論として、湿式バッグ静水圧プレスと乾式バッグ静水圧プレスの両方に利点と限界があります。湿式バッグ静水圧プレスは、より高い圧力が必要な状況に最適であり、最終製品の均一性と密度が向上します。一方、ドライバッグ静水圧プレスは、より少量の生産量に適しており、より速いサイクルタイムを実現します。ただし、製品のサイズや形状に制限があります。最終的に、2 つの方法のどちらを選択するかは、生産プロセスの特定の要件と制約によって決まります。
この製品に興味がある場合は、当社の Web サイトを参照してください: https://kindle-tech.com/product-categories/isostatic-press 。当社は常に品質第一の原則を主張します。生産プロセスでは、高品質の素材と高度な生産技術を使用して、製品の安定性と耐久性を確保するために、プロセスのすべての段階を厳密に管理します。パフォーマンスが最高の基準を満たしていることを確認します。私たちは、お客様に優れた品質を提供することによってのみ、お客様の信頼と長期的な協力を得ることができると信じています。
無料相談はお問い合わせください
KINTEK LAB SOLUTION の製品とサービスは、世界中のお客様に認められています。弊社スタッフがどんなご質問にも喜んで対応させていただきます。無料相談にお問い合わせいただき、製品スペシャリストにご相談いただき、アプリケーションのニーズに最適なソリューションを見つけてください。