金型を成形するプロセス、特にブロー成形の文脈では、金型を使用してプラスチックを所望の形状に変形させることを含む。このプロセスには通常、プラスチックを溶かしてプリフォームにすること、それを金型にクランプすること、金型の形状に適合させるために空気で膨らませること、材料を冷却すること、そして最後に完成品を射出することが含まれる。ブロー成形の3つの一般的な方法は、押出成形、射出成形、延伸ブロー成形で、それぞれに固有の手順と用途があります。
キーポイントの説明
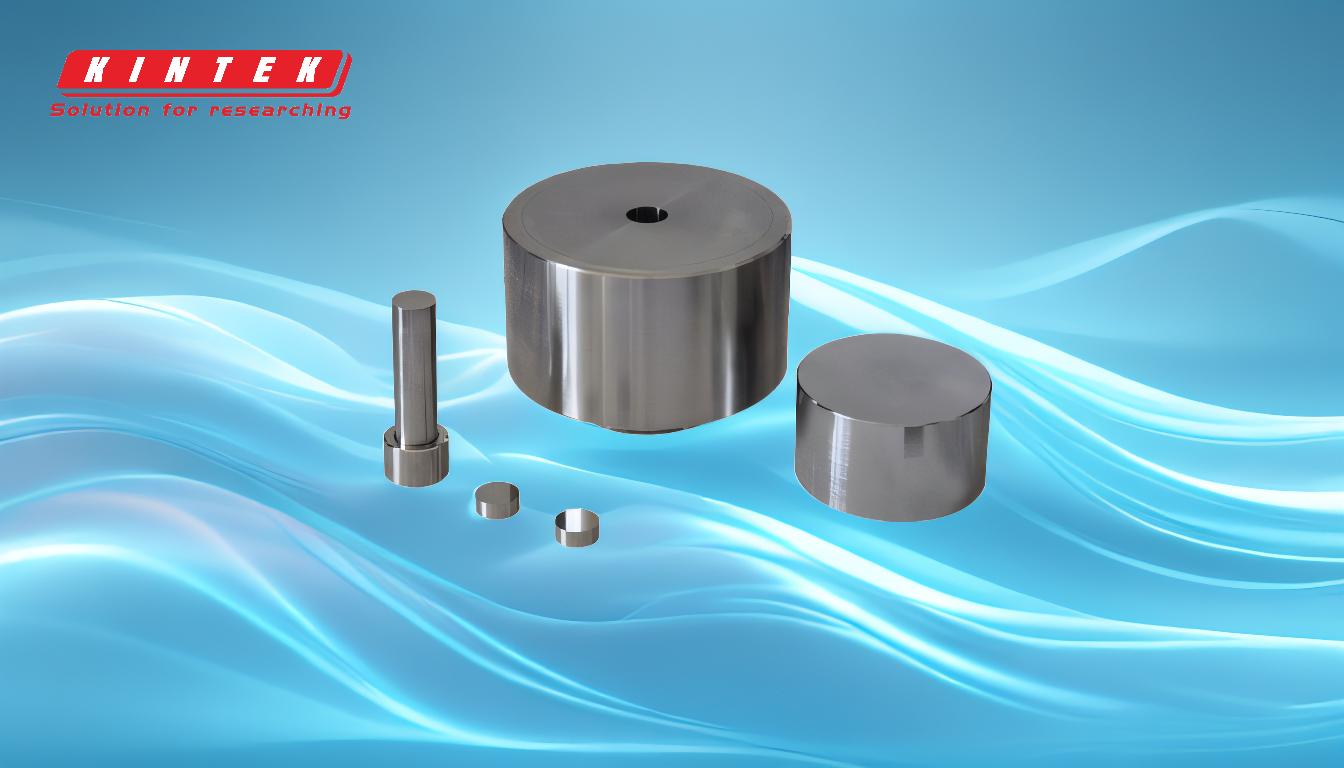
-
プラスチックを溶かしてプリフォームにする:
- プラスチックペレットや樹脂を溶かし、チューブ状のプリフォームを形成することから始まる。このプリフォームが、さらに成形される最初の形状である。
- 使用するプラスチックの種類は、柔軟性、強度、透明性など、最終製品に求められる特性によって異なります。
-
プリフォームを金型にクランプする:
- プリフォームは次に、最終製品の正確な仕様に合わせて設計された金型にクランプされる。
- 金型は通常金属製で、さまざまな形や大きさにカスタマイズできる。
-
プリフォームを空気で膨らませる:
- プリフォームがしっかりとクランプされたら、空気を送り込んでプラスチックを金型の壁に押し付ける。
- このステップにより、プラスチックは、複雑な細部やテクスチャーを含め、金型の正確な形状になります。
-
成形品を冷却する:
- プラスチックが成形された後、金型内で冷却される。冷却は、プラスチックを固化させ、新しい形状を確実に保持するために非常に重要です。
- 冷却時間は、プラスチックの厚みや使用するプラスチックの種類によって異なります。
-
完成品の取り出し:
- プラスチックが冷えて固まったら金型を開き、完成品を取り出す。
- その後、製品の品質検査が行われ、余分な材料を削ったり、部品を追加するなど、必要な仕上げが行われます。
-
一般的なブロー成形方法:
- 押出ブロー成形:この方法では、溶けたプラスチックのチューブ(パリソン)を金型に押し出し、膨らませる。ボトルや容器のような中空の成形品によく使われる。
- 射出ブロー成形:この工程は、プリフォーム金型に溶融プラスチックを注入することから始まる。その後、プリフォームをブロー金型に移し、そこで膨らませる。この方法は、医療用ボトルのような小さくて精密なものによく使われる。
- ストレッチブロー成形:この技術では、金型に吹き込む前に、プリフォームを長手方向にも半径方向にも引き伸ばす。通常、PETボトルのような高強度で軽量な容器の製造に用いられる。
これらのステップを踏むことで、メーカーは安定した品質と精度で多種多様なプラスチック製品を製造することができる。ブロー成形の各方法にはそれぞれ利点があり、製造する製品の具体的な要件に基づいて選択されます。
総括表
ステップ | 説明 |
---|---|
プラスチックを溶かしてプリフォームにする | プラスチックペレットを溶融し、最終製品の特性に合わせたチューブ状のプリフォームを形成する。 |
金型へのクランプ | プリフォームは、最終形状に合わせて設計されたカスタム金型にクランプされる。 |
空気で膨らませる | プリフォームに空気を送り込み、金型の壁に押し付け、正確な成形を行う。 |
成形品の冷却 | プラスチックは金型内で冷却され、固化して形状を保持する。 |
完成品の排出 | 冷却された製品は排出され、検査され、必要に応じて仕上げられる。 |
一般的な方法 | 押出成形、射出成形、ストレッチブロー成形、それぞれが特定の製品ニーズに適しています。 |
プラスチック成形プロセスを最適化する準備はできていますか? 当社の専門家に今すぐご連絡ください オーダーメイドのソリューションを