スパッタコーティングは、一般的に顕微鏡、電子工学、光学などの用途で、基板上に材料の薄膜を堆積させるために使用されるプロセスである。その原理は、プラズマを利用して固体のターゲット材料から原子を放出させ、その原子が基板上に堆積して薄く均一な層を形成するというものである。このプロセスは真空環境で行われ、アルゴンガスをイオン化してプラズマを発生させる。正電荷を帯びたアルゴンイオンが負電荷を帯びたターゲット材料に向かって加速され、ターゲットから原子が放出され、基板上に堆積される。このプロセスは高度に制御され、多くの場合自動化されており、均一で高品質なコーティングを実現するために、熱とエネルギーの正確な管理が要求される。
キーポイントの説明
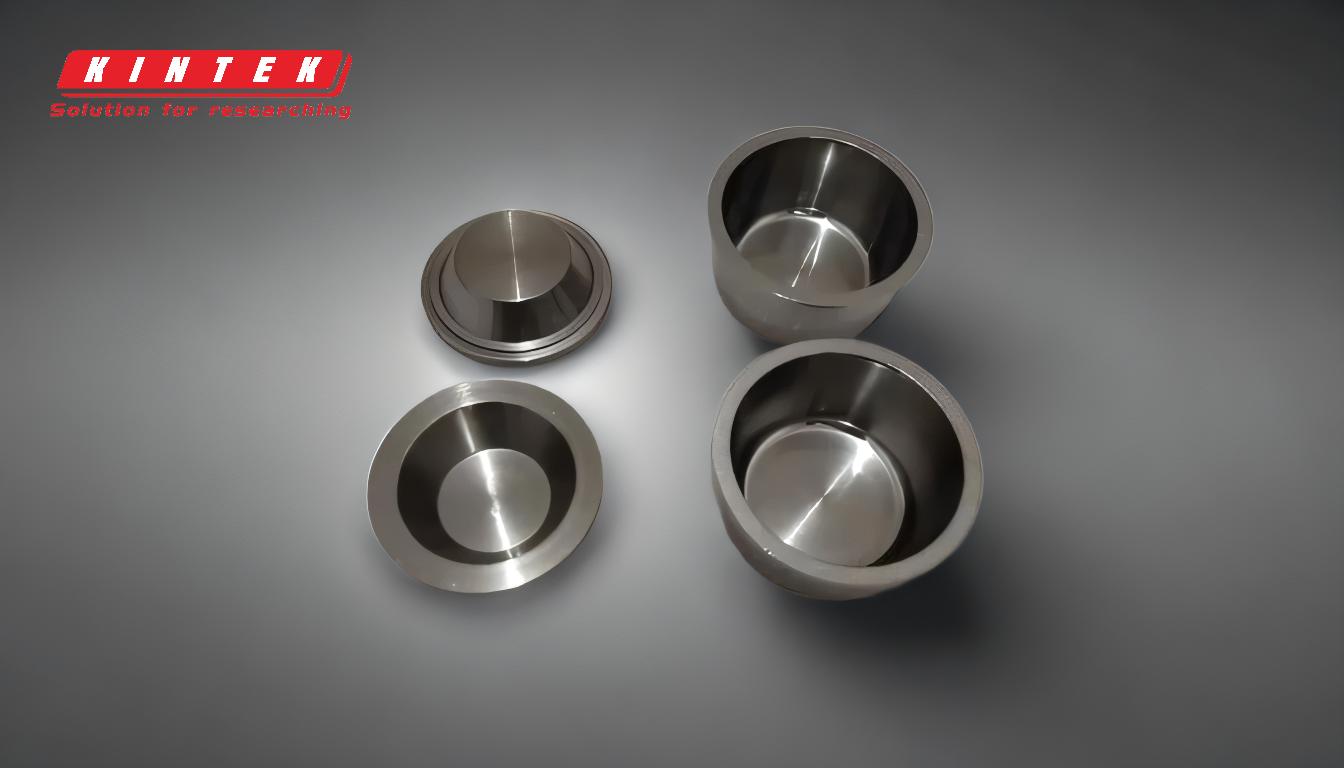
-
真空環境とプラズマ発生:
- スパッタコーティングは、汚染物質を排除し、制御された環境を確保するため、真空チャンバー内で行われる。
- アルゴンガスがチャンバー内に導入され、高電圧の電界でイオン化され、プラズマが形成される。このプラズマは、正電荷を帯びたアルゴンイオンと自由電子から構成される。
-
ターゲットとカソードのセットアップ:
- 成膜される物質であるターゲット材料は、陰極と呼ばれるマイナスに帯電した電極に接着またはクランプされる。
- プラズマを安定させ、ターゲット物質の均一な浸食を保証し、コーティングの一貫性を高めるために、しばしば磁石が使用される。
-
ターゲット原子の運動量移動と放出:
- プラズマ中の正電荷を帯びたアルゴンイオンは、電界によって負電荷を帯びたターゲット材料に向かって加速される。
- これらの高エネルギーイオンがターゲット表面に衝突すると、ターゲット原子に運動量が伝達され、スパッタリングと呼ばれるプロセスで表面から放出される。
-
基板への蒸着:
- 放出されたターゲット原子は真空中を移動し、基板上に堆積して薄膜を形成する。
- 基板は通常、均一な成膜を確実にするため、ターゲット材料の反対側に配置される。
-
熱管理:
- スパッタコーティングは、高エネルギーの衝突とプラズマ活動により、かなりの熱を発生します。
- この熱を管理し、ターゲット材料、基板、装置への損傷を防ぐために、特殊な冷却システムが使用されます。
-
自動化と精密さ:
- このプロセスは、一貫した正確なコーティングを保証するため、多くの場合自動化されており、手作業から生じる可能性のあるばらつきを低減している。
- 電圧、ガス圧、ターゲットと基板間の距離などのパラメーターを正確に制御することは、高品質のコーティングを実現するために非常に重要である。
-
用途と利点:
- スパッタコーティングは、半導体製造、光学コーティング、顕微鏡サンプル前処理など、薄く均一な膜を必要とする産業で広く使用されています。
- このプロセスでは、成膜された材料と基板との間に原子レベルの強い結合が生じ、耐久性と密着性が確保される。
これらの重要な原理を理解することで、スパッタコーティングの複雑さと精密さを理解することができ、さまざまな用途で高性能薄膜を作成するための貴重な技術となる。
総括表:
主な側面 | 詳細 |
---|---|
真空環境 | コンタミを除去し、均一なコーティングのための制御された条件を保証します。 |
プラズマ生成 | アルゴンガスをイオン化してプラズマを生成し、イオンをターゲットに向けて加速する。 |
ターゲット材料 | カソードに接着され、磁石がプラズマを安定させ、安定した侵食を行う。 |
運動量移動 | 高エネルギーイオンはターゲット原子を放出し、ターゲット原子は基板上に堆積する。 |
熱管理 | チリングシステムは、高エネルギー衝突による損傷を防ぎます。 |
自動化と高精度 | 自動化されたシステムは、正確なパラメータ制御により安定したコーティングを実現します。 |
用途 | 顕微鏡、半導体、光学分野で使用され、耐久性のある均一な膜を形成します。 |
スパッタコーティングがどのようにお客様のアプリケーションを向上させるかをご覧ください。 今すぐ専門家にお問い合わせください !