スプレーとスパッタリングは、コーティングと薄膜蒸着に使用される2つの異なるプロセスであり、それぞれ独自のメカニズム、用途、結果を持つ。スプレーは通常、液体材料を霧状にして微細な液滴にし、表面に堆積させるもので、塗装やコーティング、表面処理によく用いられる。一方、スパッタリングは物理的気相成長(PVD)技術であり、高エネルギー・イオンの衝突によって固体のターゲット材料から原子が放出され、基板上に薄膜が形成される。主な違いは、エネルギー源、材料状態、成膜メカニズム、得られる膜の特性にある。スパッタリングは、密着力が強く、膜が緻密で、膜組成や膜厚の制御がしやすいなどの利点があり、半導体や光学コーティングなどの高精度用途に適している。スパッタリングは、大規模な用途には汎用性が高いが、精度と均一性に欠ける場合がある。
要点の説明
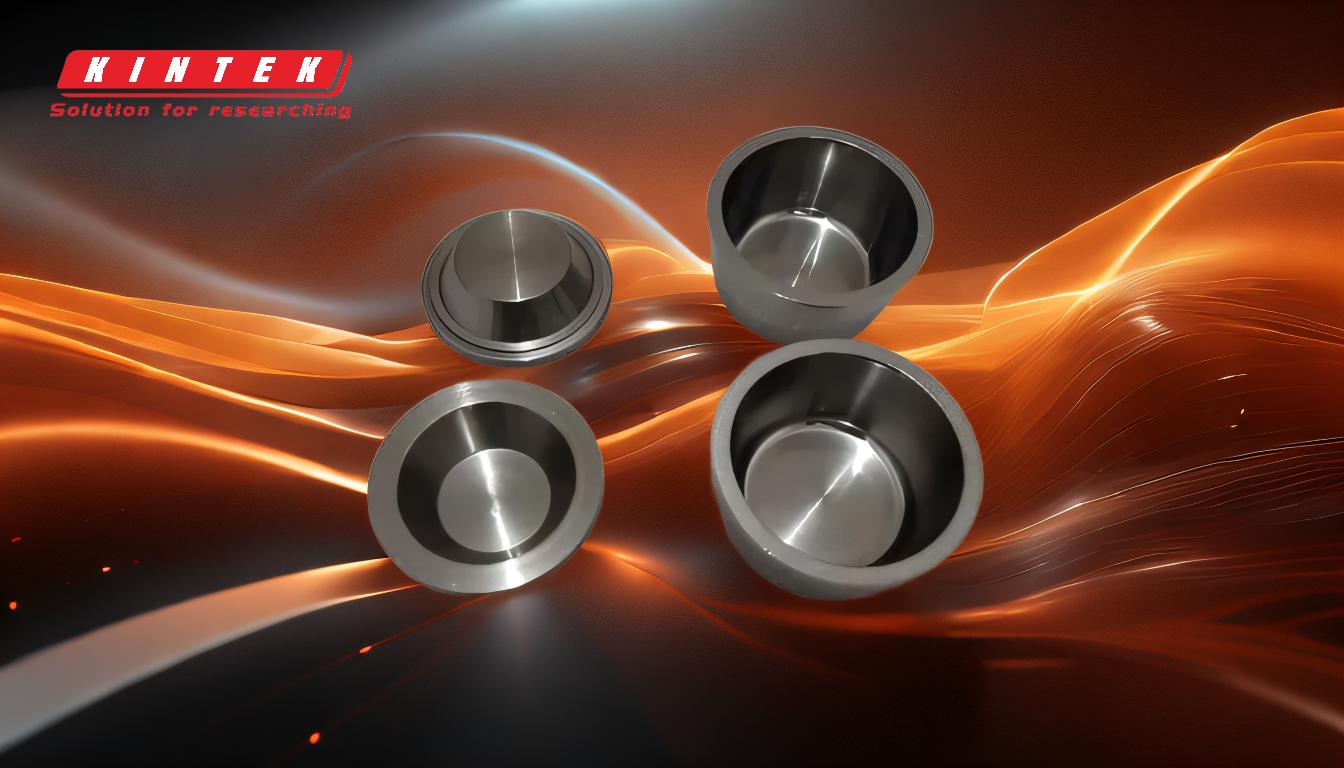
-
成膜のメカニズム:
- 溶射:液体材料(塗料、コーティング液など)を霧状にして細かい液滴にし、表面に付着させる。このプロセスは、材料を分散させるための機械的または空気圧の力に依存している。
- スパッタリング:高エネルギーイオンが固体ターゲットに衝突し、ターゲット表面から原子を放出するPVDプロセス。この原子が基板上に堆積して薄膜を形成する。このプロセスは、プラズマ生成とイオン加速によって駆動される。
-
材料の状態:
- 溶射:液体または半液体の材料を使用し、溶液、懸濁液、溶融金属であることが多い。
- スパッタリング:金属、合金、絶縁体など、固体のターゲット材料を使用する。材料は原子状または分子状で放出される。
-
エネルギー源:
- 溶射:機械的エネルギー(圧縮空気など)または熱エネルギー(溶融金属の加熱など)に頼る。
- スパッタリング:電気エネルギーを利用してプラズマを発生させ、ターゲット材料に向けてイオンを加速する。
-
蒸着速度と制御:
- 溶射:一般的に成膜速度は速いが、膜厚や均一性の精密な制御は難しい。大面積コーティングに適する。
- スパッタリング:成膜速度は低いが、膜厚や組成を精密に制御できる。半導体や光学コーティングのような高精度アプリケーションに最適。
-
膜特性:
- スプレー:スパッタリング膜に比べ、密着性、密度、均一性が劣る場合がある。高精度が要求されない用途に適している。
- スパッタリング:密着性が強く、高密度で均一性の高い膜が得られる。また、酸化などの環境要因にも強い。
-
用途:
- 溶射:自動車(塗料コーティング)、建築(表面処理)、消費財(装飾コーティング)などの産業で一般的に使用されている。
- スパッタリング:エレクトロニクス(半導体製造)、光学(反射防止コーティング)、航空宇宙(保護コーティング)などで広く使用されている。
-
環境条件:
- 溶射:材料と用途に応じて、周囲条件または制御された環境で実施できる。
- スパッタリング:汚染を最小限に抑え、成膜プロセスを正確に制御するため、真空環境が必要。
-
材料の多様性:
- 溶射:霧化して液体で蒸着できる材料に限定される。
- スパッタリング:金属、合金、絶縁体など幅広い材料の成膜が可能で、反応性ガスの添加により複雑な組成の成膜も可能。
-
設備とコスト:
- 溶射:一般に安価でシンプルな装置であるため、大規模な用途では費用対効果が高い。
- スパッタリング:真空装置やプラズマ発生装置など、より高度で高価な装置を必要とするが、膜質や精度に優れる。
-
ターゲットと基板の配置:
- 溶射:配置の自由度が低く、スプレーノズルと基板間の直視が必要な場合が多い。
- スパッタリング:スパッタリング粒子は重力の影響を受けず、複雑な形状にも均一に堆積できるため、ターゲットと基板を柔軟に配置できる。
これらの主な違いを理解することで、装置や消耗品の購入者は、精度、材料適合性、コスト面など、それぞれの用途の具体的な要件に基づいて、十分な情報に基づいた決定を下すことができる。
要約表
側面 | 溶射 | スパッタリング |
---|---|---|
メカニズム | 液体を霧化して液滴にし、機械的/空気圧力によって堆積させる。 | PVDプロセスでは、高エネルギーイオンを使用して固体ターゲットから原子を放出する。 |
材料の状態 | 液体または半液体(溶液、懸濁液、溶融金属)。 | 固体ターゲット材料(金属、合金、絶縁体)。 |
エネルギー源 | 機械的または熱的エネルギー | 電気エネルギー(プラズマ生成とイオン加速) |
蒸着速度 | 高い蒸着速度、精密な制御が困難 | 蒸着速度が低いが、膜厚と組成を正確に制御できる。 |
フィルム特性 | 密着性、密度、均一性が低い。 | 接着力が強く、密度が高く、均一性が高い。 |
用途 | 自動車、建築、消費財 | 半導体、光学、航空宇宙 |
環境ニーズ | 常温または制御された環境 | 真空環境が必要 |
材料の多様性 | 原子化可能な液体に限定。 | 金属、合金、絶縁体を含む幅広い材料。 |
コスト | 安価な装置で、大規模アプリケーションに費用対効果。 | より高価な装置、高精度のアプリケーションに最適。 |
基板の配置 | 直接視線を必要とする。 | 複雑な形状でも均一な成膜が可能。 |
お客様のアプリケーションに適したコーティングプロセスの選択にお困りですか? 当社の専門家にお問い合わせください。 にご相談ください!