物理的気相成長法(PVD)と化学的気相成長法(CVD)は、基板上に薄膜を成膜するために使用される2つの著名な技術であるが、そのプロセス、材料、用途は大きく異なる。PVDは、固体材料を気化させて基板上に凝縮させるといった物理的な手段に頼っており、その結果、耐久性に優れた高温耐性のコーティングが得られる。一方、CVDは、気体状の前駆物質と基材との化学反応を利用するため、さまざまな材料に厚く粗い層を成膜することができる。PVDとCVDのどちらを選択するかは、希望するコーティング特性、基材との適合性、アプリケーションの要件などの要因によって決まります。
キーポイントの説明
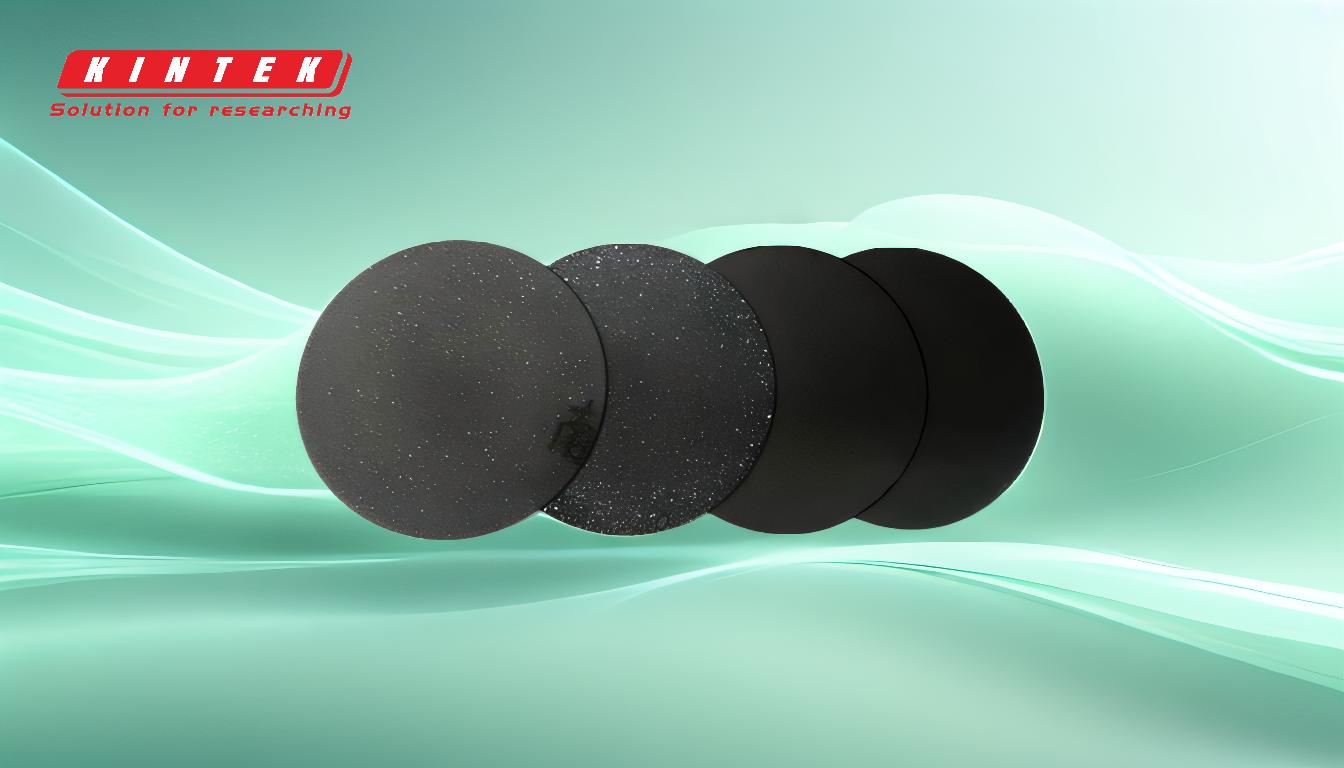
-
プロセスのメカニズム:
- PVD:物理反応を利用して固体材料を蒸気に変え、それが基板上に凝縮して薄膜を形成する。このプロセスでは、材料に化学的変化は起こらない。
- CVD:ガス状前駆体と基材表面の化学反応に依存する。反応により固体膜が生成され、気体や液体などの副生成物を伴うことが多い。
-
材料の状態:
- PVD:気化させて基板上に蒸着させる固体コーティング材料を使用。
- CVD:基材と化学反応し、目的の層を形成するガス状コーティング材を使用します。
-
温度条件:
- PVD:通常250℃から450℃の比較的低い温度で作動するため、温度に敏感な基板に適している。
- CVD:450℃から1050℃の高温を必要とするため、素材によっては使用が制限される場合があるが、より厚く堅牢なコーティングの成膜が可能。
-
コーティングの特徴:
- PVD:密着性に優れ、高温や磨耗に強く、薄く平滑で、耐久性の高いコーティングが可能。
- CVD:より厚く、より粗いコーティングが得られ、複雑な形状や内部表面を含む、より多様な素材に適用できる。
-
適応性:
- PVD:切削工具、医療機器、航空宇宙部品など、高精度、耐久性、過酷な条件への耐性を必要とする用途に最適。
- CVD:半導体デバイス、光学部品、工業用工具の保護膜など、複雑な形状に均一なコーティングが必要な用途に適している。
-
利点と限界:
-
PVDの利点:
- 高い耐久性と耐摩耗性。
- 優れた接着性と滑らかな表面仕上げ。
- 低温処理により、基材へのダメージが少ない。
-
PVDの限界:
- 直視下での成膜に限定されるため、複雑な形状のコーティングが難しい。
- CVDに比べ、一般的にコーティング膜が薄い。
-
CVDの利点:
- 複雑な形状や内面を均一にコーティングできる。
- より適合性の高い厚いコーティングが可能。
- より幅広い材料に対応
-
CVDの制限:
- 高温になると、温度に敏感な基材を損傷することがある。
- 化学副産物は、追加の取り扱いと廃棄が必要になる場合があります。
-
PVDの利点:
-
工業用途:
- PVD:自動車(エンジン部品)、航空宇宙(タービンブレード)、医療(手術器具)など、高性能コーティングを必要とする産業で一般的に使用されている。
- CVD:半導体製造(集積回路)、光学(反射防止コーティング)、産業用工具の耐摩耗コーティングなどに広く適用されている。
これらの重要な違いを理解することで、装置や消耗品の購入者は、コーティングの厚さ、基材との適合性、環境条件など、それぞれの用途の具体的な要件に基づいて、十分な情報に基づいた意思決定を行うことができる。
要約表
側面 | PVD | CVD |
---|---|---|
プロセスのメカニズム | 固体材料の物理的気化と凝縮。 | ガス状前駆体と基材との化学反応。 |
材料の状態 | 気化して堆積した固体材料。 | 気体材料が化学反応して固体膜を形成する。 |
温度範囲 | 250°C~450°C(より低い温度、敏感な基板に適している)。 | 450°C~1050°C(より高い温度で、より厚いコーティングが可能)。 |
コーティングの特徴 | 薄い、滑らか、耐久性、耐摩耗性。 | より厚く、より粗く、複雑な形状に適用可能。 |
用途 | 切削工具、医療機器、航空宇宙部品 | 半導体デバイス、光学部品、産業用工具 |
利点 | 高い耐久性、滑らかな仕上がり、低温処理 | 複雑な形状でも均一なコーティングが可能。 |
制限事項 | 直視下蒸着、より薄いコーティング。 | 高温、化学副産物。 |
PVDとCVDの選択でお困りですか? 当社の専門家に今すぐご連絡ください にお問い合わせください!