CVD(Chemical Vapor Deposition)コーティングは、基板上に薄膜を成膜する技術として広く使われており、再現性やステップカバレッジに優れているため、誘電体膜、半導体膜、金属膜などさまざまな用途に適している。しかし、処理温度が高く、耐高温材料への使用が制限されることや、残留引張応力によってコーティングされた装置が壊れやすくなることなど、顕著な欠点もある。さらに、エネルギーコストが高く、低融点ポリマーへの成膜が難しいことも、CVDの適用性をさらに制約している。このような欠点があるにもかかわらず、CVDは特定の工業用途や材料科学用途において、依然として価値ある方法である。
要点の説明
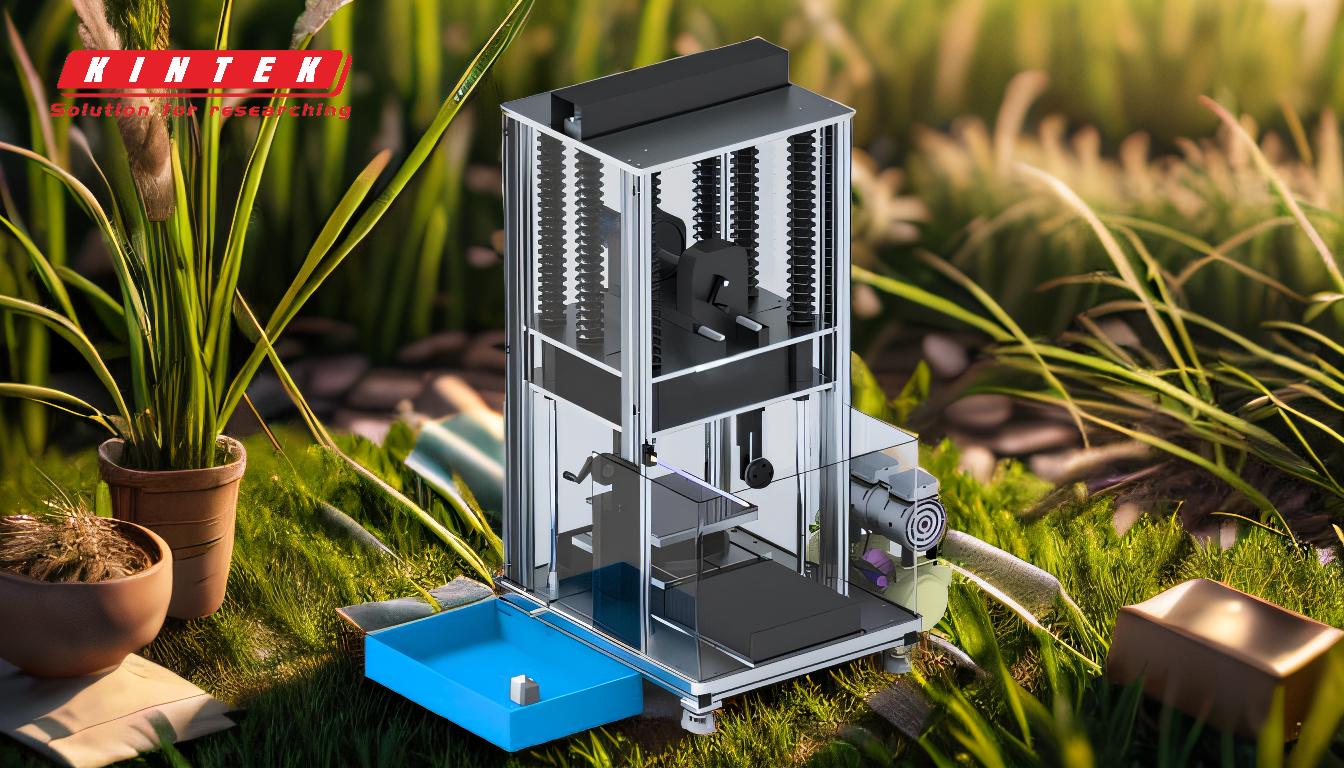
-
CVDコーティングの利点:
- 優れた再現性とステップカバレッジ: CVDコーティングは、複雑な形状であっても、一貫性のある均一なコーティングができることで知られています。そのため、半導体製造など、精密で再現性の高い成膜を必要とする用途に最適です。
- 材料蒸着における多様性: CVDは、誘電体膜(SiO2、Si3N4など)、半導体膜、金属膜、有機金属化合物など、幅広い材料を成膜できる。この汎用性により、電子機器から切削工具まで、さまざまな産業で使用されている。
-
CVDコーティングの欠点
- 高い処理温度: CVDは一般的に高温(800~1000℃)で行われるため、超硬合金のようなそのような条件に耐えられる材料に使用が限定される。そのため、低融点ポリマーや温度に敏感な基材には不向きである。
- 残留引張応力: CVDは高温で行われるため、冷却時に残留引張応力が発生し、コーティングに微細なクラックが生じることがある。これらのクラックは外部からの衝撃で伝播し、特に断続切削加工(フライス加工など)のような用途ではコーティングの破損につながる可能性がある。
- コーティング装置の脆弱性: 残留引張応力のため、CVDコーティング装置はPVD(物理蒸着)コーティング装置に比べて壊れやすい傾向がある。この壊れやすさは、機械的耐久性が重要な用途では大きな欠点となりうる。
- 高いエネルギーコスト: CVDに必要な温度まで気相を加熱するプロセスはエネルギー集約的であり、運用コストの上昇につながる。これは、大規模なアプリケーションやコスト重視のアプリケーションでは、制限要因となりうる。
- 低融点ポリマーの課題: CVDは高温になるため、低融点ポリマーへの成膜には適していない。このため、フレキシブル・エレクトロニクスやポリマー系材料など、特定の産業での適用が制限される。
-
用途と制限
- 適した用途: CVDは、半導体産業や切削工具産業など、耐熱性の高い材料や精密な成膜を必要とする用途に特に適している。
- 不向きな用途 処理温度が高く、その結果残留応力が発生するため、CVDは断続的な切断工程や融点の低い材料を含む用途には適さない。
まとめると、CVDコーティングは、再現性、ステップカバレッジ、材料の汎用性の面で大きな利点がある一方で、その高い処理温度、残留引張応力、およびコーティングされた機器の関連する壊れやすさは、顕著な欠点である。特定の用途にCVDを選択する際には、これらの要因を慎重に考慮する必要がある。
総括表
側面 | メリット | 短所 |
---|---|---|
再現性 | 一貫した均一なコーティング、複雑な形状に最適 | 高い処理温度(800~1000℃)は、材料の適合性を制限する。 |
ステップカバレッジ | 正確で再現性の高い成膜に最適 | 残留引張応力により微細なクラックが発生し、塗膜の脆弱化につながる。 |
材料の多様性 | 誘電体、半導体、金属膜、有機金属化合物の成膜が可能 | エネルギー集約型の加熱プロセスによる高いエネルギーコスト |
用途 | 耐熱性の高い材料や精密な成膜に適しています。 | 低融点ポリマーや温度に敏感な基板には不向き |
CVDコーティングがお客様の用途に適しているかどうかの判断にお困りですか? 当社の専門家に今すぐご連絡ください にご相談ください!