ダイヤモンド・コーティングとセラミック・コーティングは、硬度や耐久性といった特性において共通点はあるものの、同じものではありません。ダイヤモンドコーティングは、炭素原子をダイヤモンドの結晶構造に配列したもので、卓越した硬度、熱伝導性、耐薬品性を備えています。一方、セラミック・コーティングは、一般的に金属酸化物、炭化物、窒化物でできており、高い硬度と耐摩耗性を提供しますが、組成や特定の特性は異なります。どちらも保護や機能的な目的で使用されますが、材料組成、成膜方法、性能特性により、両者は異なります。
キーポイントの説明
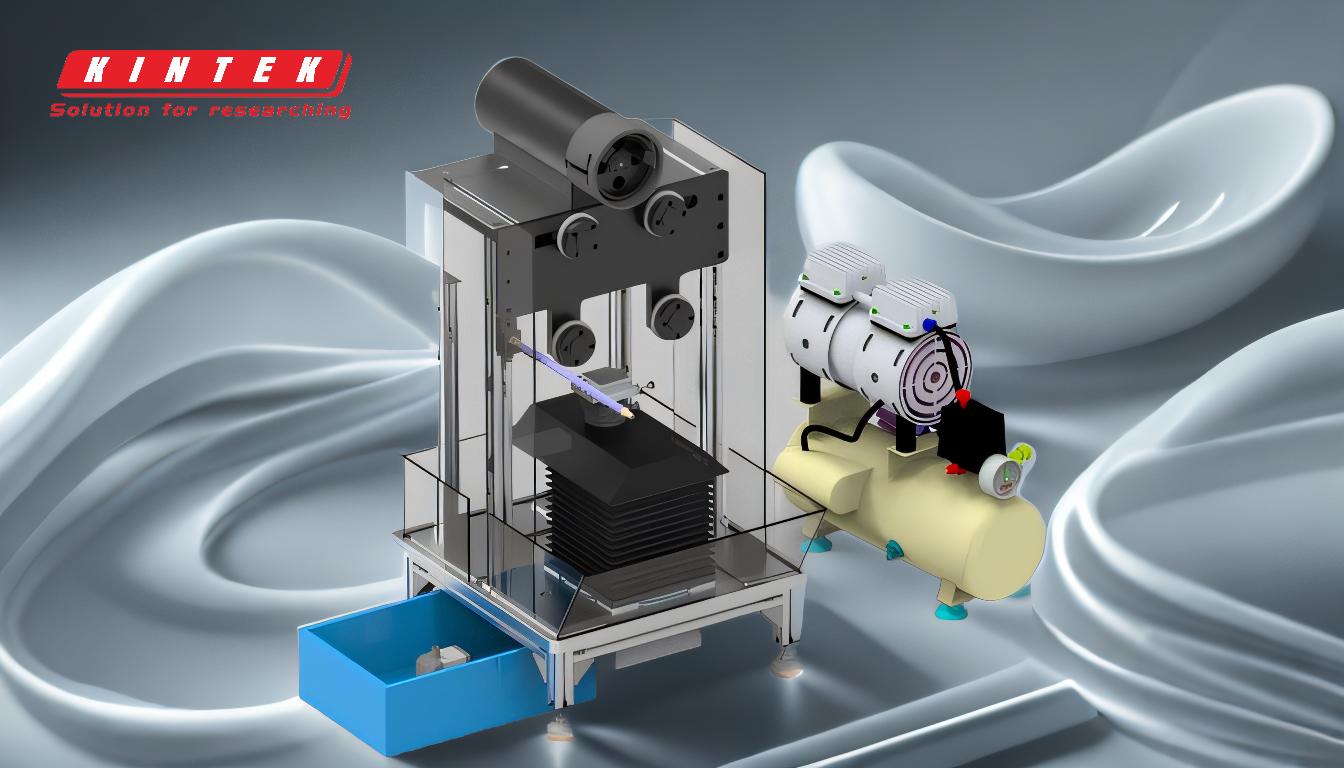
-
素材構成:
- ダイヤモンドコーティング:炭素原子がダイヤモンドの結晶格子に配列したもので、比類のない硬度と熱伝導性を持つ。化学的に不活性で耐摩耗性に優れている。
- セラミックコーティング:金属酸化物、炭化物、窒化物(酸化アルミニウム、炭化ケイ素、窒化チタンなど)から作られる。これらの材料は硬く耐久性がありますが、ダイヤモンドとは構造や性質が大きく異なります。
-
特性:
-
ダイヤモンドコーティング:
- 極めて高い硬度(天然ダイヤモンドに近い)。
- 熱伝導性に優れ、放熱用途に適している。
- 化学的に不活性で、腐食や摩耗に強い。
-
セラミックコーティング:
- 一般的にダイヤモンドより劣るが、高い硬度と耐摩耗性。
- 熱絶縁性、電気絶縁性に優れる。
- 酸化や腐食に強いが、ダイヤモンドほど化学的に不活性ではない。
-
ダイヤモンドコーティング:
-
成膜方法:
- ダイヤモンドコーティング:通常、化学気相成長法(CVD)または物理気相成長法(PVD)を用いる。このプロセスでは、粒径や表面粗さなどの特性を調整するために、気相組成と蒸着パラメーターを精密に制御します。
- セラミックコーティング:溶射、プラズマ溶射、PVD/CVDなどの方法を用いて施される。プロセスは、特定のセラミック材料と用途要件によって異なります。
-
用途:
- ダイヤモンドコーティング:切削工具、耐摩耗表面、ヒートシンクなどの高性能用途に使用。その優れた特性により、過酷な条件下での使用に最適です。
- セラミックコーティング:航空宇宙、自動車、製造業などの業界で、摩耗保護、遮熱コーティング、電気絶縁などによく使用されている。
-
コストと入手しやすさ:
- ダイヤモンドコーティング:成膜プロセスの複雑さと原材料の高コストのため、一般的に高価。独自の特性が不可欠な特殊な用途に使用される。
- セラミックコーティング:費用対効果が高く、広く入手可能なため、幅広い産業用途に適している。
まとめると、ダイヤモンドコーティングとセラミックコーティングはどちらも高い硬度と耐久性を持つが、材料組成、特性、成膜方法、用途が異なる。ダイヤモンドコーティングは、硬度と熱伝導性の点で優れていますが、より高価で特殊です。一方、セラミックコーティングは汎用性が高く、費用対効果も高いため、より幅広い用途に適している。
総括表:
側面 | ダイヤモンドコーティング | セラミックコーティング |
---|---|---|
材料構成 | ダイヤモンド結晶格子中の炭素原子 | 金属酸化物、炭化物、窒化物(酸化アルミニウム、炭化ケイ素など) |
特性 |
- 極めて高い硬度
- 優れた熱伝導性 - 化学的に不活性 |
- 高い硬度
- 熱的・電気的絶縁性が高い - 酸化に強い |
成膜方法 | CVDまたはPVD | 溶射、プラズマ溶射、PVD/CVD |
用途 | 切削工具、耐摩耗表面、ヒートシンク | 航空宇宙、自動車、製造(摩耗防止、熱障壁) |
コスト | 高価で特殊 | 費用対効果が高く、広く入手可能 |
お客様の用途に適したコーティングの選択にお困りですか? 今すぐ専門家にご相談ください!