化学的気相成長法(CVD)と物理的気相成長法(PVD)によって成膜されるコーティングの厚さは、成膜メカニズム、操作条件、用途の違いによって大きく異なります。一般的に、PVDコーティングは0.2~5ミクロンと薄く、装飾や機能的な目的で使用されることが多い。一方、CVDコーティングは厚く、一般的に5~10ミクロンで、高純度や高密度が要求される用途に適しています。CVDとPVDのどちらを選択するかは、希望するコーティング特性、基材の材質、特定の用途要件などの要因によって決まります。
キーポイントの説明
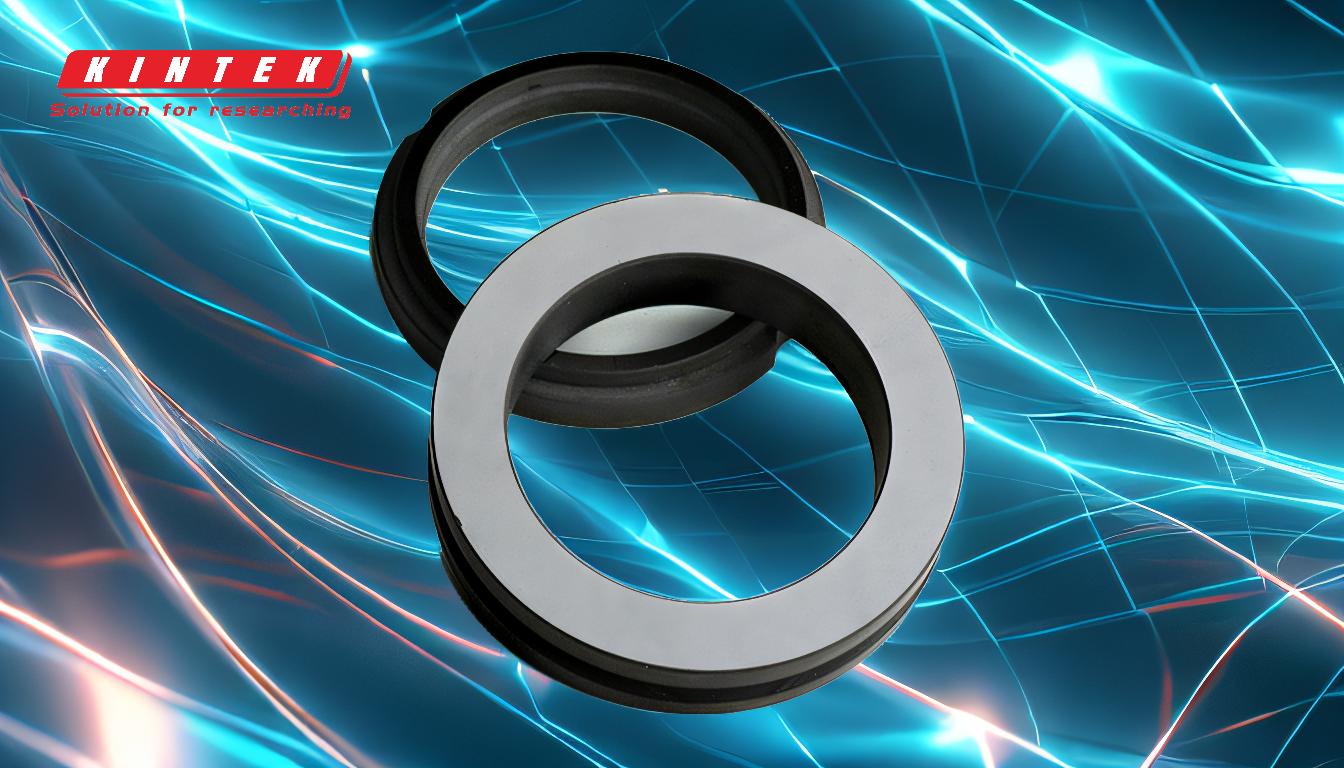
-
成膜メカニズム:
- PVD:固体材料を物理的に気化させ、それを基板上にライン・オブ・サイト方式で蒸着させる。このプロセスは通常、化学反応を伴わない。
- CVD:ガス状の前駆物質と基材との化学反応により、固体皮膜が形成される。このプロセスは多方向性があり、複雑な形状をより効果的にカバーすることができる。
-
コーティング厚さ:
- PVD:コーティングは一般的に0.2~5ミクロンと薄い。このため、PVDは、装飾仕上げや電子機器の機能層など、薄く均一なコーティングが求められる用途に適している。
- CVD:コーティングは厚く、通常5ミクロンから10ミクロンである。この厚さは、半導体製造や過酷な環境での保護層など、堅牢で耐久性のあるコーティングを必要とする用途に有利です。
-
使用温度:
- PVD:通常250℃から450℃の低温で作動する。そのため、高温に耐えられない基板に適している。
- CVD:450℃から1050℃の高温を必要とする。この高温環境は、コーティング形成に必要な化学反応を促進するが、使用できる基材の種類は限定される。
-
コーティングの均一性と密度:
- PVD:CVDに比べ、コーティングの密度が低く、均一性に欠ける。しかし、PVDコーティングはより短時間で塗布できるため、高スループット・アプリケーションに適した方法である。
- CVD:より緻密で均一なコーティングが可能。CVDに含まれる化学反応は、特に複雑な形状において、より優れた密着性と被覆性をもたらします。
-
応用例:
- PVD:装飾コーティング、耐摩耗層、エレクトロニクス産業での薄膜蒸着によく使用される。
- CVD:半導体産業、保護膜形成、高純度・高密度膜を必要とする用途に広く使用されている。
-
材料範囲:
- PVD:金属、合金、セラミックスなど、より幅広い材料を成膜できる。この汎用性により、PVDは様々な用途に適している。
- CVD:一般的にセラミックとポリマーに限定される。CVDの化学的性質により、効果的に成膜できる材料の種類が制限される。
まとめると、CVDとPVDのどちらを選択するかは、希望するコーティングの厚さ、均一性、密度、材料の種類など、アプリケーションの具体的な要件によって決まる。一般的に、薄いコーティング、装飾的なコーティング、機能的なコーティングにはPVDが好まれ、厚いコーティング、耐久性の高いコーティング、高純度のコーティングにはCVDが好まれる。
総括表
側面 | PVD | CVD |
---|---|---|
膜厚 | 0.2~5ミクロン | 5~10ミクロン |
使用温度 | 250°C ~ 450°C | 450°C ~ 1050°C |
コーティング均一性 | 均一性が低い | 均一性が高い |
コーティング密度 | 密度が低い | 高密度 |
用途 | 装飾、エレクトロニクス、耐摩耗性 | 半導体、保護膜 |
材料範囲 | 金属、合金、セラミックス | セラミックス、ポリマー |
CVDとPVDの選択でお困りですか? 今すぐ当社の専門家にお問い合わせください!