CVD (化学蒸着) および PVD (物理蒸着) コーティングは、材料の表面特性を向上させるためにさまざまな業界で広く使用されています。これらのコーティングの厚さは、その性能と用途に影響を与える重要な要素です。 CVD コーティングは通常、ナノメートルから 20 ミクロン未満の範囲ですが、PVD コーティングは通常より薄く、0.25 ミクロンから 5 ミクロンの範囲です。どちらの方法も、硬度、平滑性、耐食性などの目的の特性に応じて独自の利点を提供します。 CVD と PVD のどちらを選択するかは、多くの場合、基板材料、望ましいコーティング特性、操作条件など、アプリケーションの特定の要件に依存します。
重要なポイントの説明:
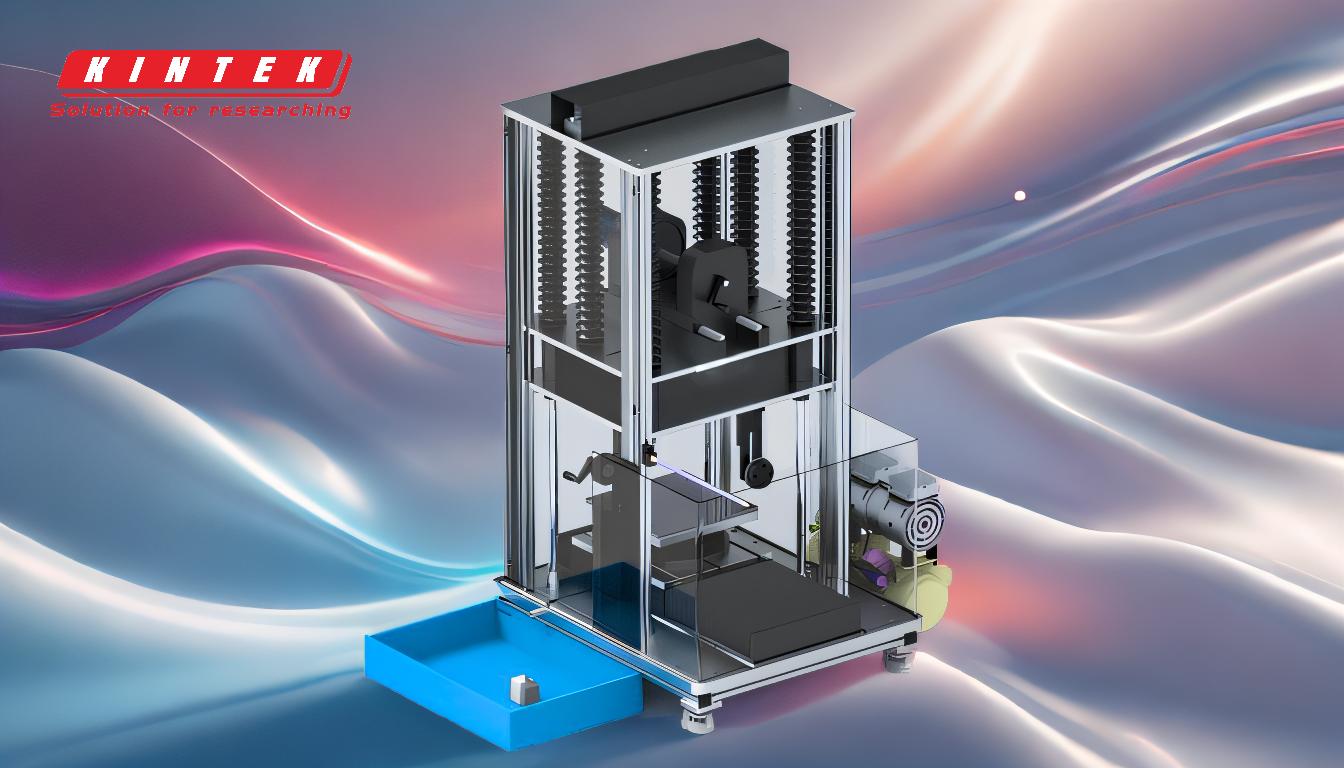
-
一般的な厚さの範囲:
- CVDコーティング: CVD 法では、ナノメートルから 20 ミクロン未満の範囲の薄膜層を堆積できます。この幅広い範囲により、より厚いコーティングが必要な用途に柔軟に対応できます。
- PVD コーティング: PVD コーティングは一般に薄く、通常は 0.25 ミクロンから 5 ミクロンの範囲です。この薄さにより、コーティングが加工部品の寸法や仕様を大幅に変更しないことが保証されます。
-
コーティングの厚さに影響を与える要因:
- CVD: CVD コーティングの厚さは、基板の種類、基板温度、反応ガスの化学組成、ガス流の全圧などのさまざまなパラメータの影響を受ける可能性があります。これらの要素を調整して、望ましいコーティングの厚さと特性を実現できます。
- PVD: PVD コーティングの厚さは、コーティング材料の種類と使用される特定の PVD プロセスによって影響されます。コーティングが同じ材料で作られている場合でも、塗布方法はその性能と特性に大きな影響を与える可能性があります。
-
アプリケーションと利点:
- CVD: CVD はより厚いコーティングを堆積できるため、耐久性と耐摩耗性、耐腐食性の向上が必要な用途によく使用されます。コーティングが厚いほど、過酷な環境でもより優れた保護を提供できます。
- PVD: PVD コーティングは薄い性質があるため、部品の元の寸法と外観を維持することが重要な用途に最適です。 PVD コーティングは、部品の外観を変えることなく、平滑性、硬度、耐食性などの特性を強化するために一般的に使用されます。
-
厚みの比較:
- CVD と PVD: CVD コーティングは非常に厚い (最大 20 ミクロン) 場合がありますが、PVD コーティングは一般に非常に薄い (0.25 ~ 5 ミクロン) です。この厚さの違いは、特定の用途に 2 つの方法のどちらかを選択する際の重要な考慮事項です。
-
性能と特性:
- CVD: CVD によって提供される厚いコーティングは、耐摩耗性と耐久性の点で優れたパフォーマンスを提供します。ただし、このプロセスにはより高い温度とより複雑な装置が必要になる場合があります。
- PVD: PVD コーティングは薄いため、コーティングの厚さを正確に制御し、部品の寸法への影響を最小限に抑える必要がある用途に最適です。また、優れた接着性と均一性でも知られています。
要約すると、CVD コーティングと PVD コーティングの厚さは大きく異なり、CVD はより要求の厳しい用途に適したより厚いコーティングを提供し、PVD は精度と美観の用途に最適なより薄いコーティングを提供します。 2 つの方法のどちらを選択するかは、必要な特性や動作条件など、アプリケーションの特定の要件によって異なります。
概要表:
側面 | CVDコーティング | PVD コーティング |
---|---|---|
厚さの範囲 | ナノメートルから < 20 ミクロン | 0.25~5ミクロン |
主要な影響要因 | 基板の種類、温度、ガス組成、圧力 | コーティング材 PVD加工タイプ |
アプリケーション | 耐久性、耐摩耗性、防食性 | 精度、滑らかさ、寸法変化が少ない |
パフォーマンス | 優れた耐摩耗性、耐久性 | 密着性、均一性、薄さに優れる |
用途に適したコーティング方法を選択するのにサポートが必要ですか? 今すぐ当社の専門家にご連絡ください。