スパッタコーティングは、物理的気相成長法(PVD法)の一つで、基板上に薄く均一なコーティングを施すために用いられる。このプロセスでは、スパッタリングカソードを帯電させてプラズマを発生させ、ターゲット材料に高エネルギーイオンを衝突させる。この照射によってターゲットから原子が放出され、基板上に堆積して薄膜が形成される。このプロセスには真空環境、アルゴンや酸素のような特殊なガスが必要で、ターゲット材料の均一な浸食を確実にするために磁石を使用することも多い。スパッタコーティングは、走査型電子顕微鏡(SEM)における二次電子放出の改善や、様々な産業における耐久性のある高品質コーティングの作成などの用途で広く使用されている。
主なポイントを説明します:
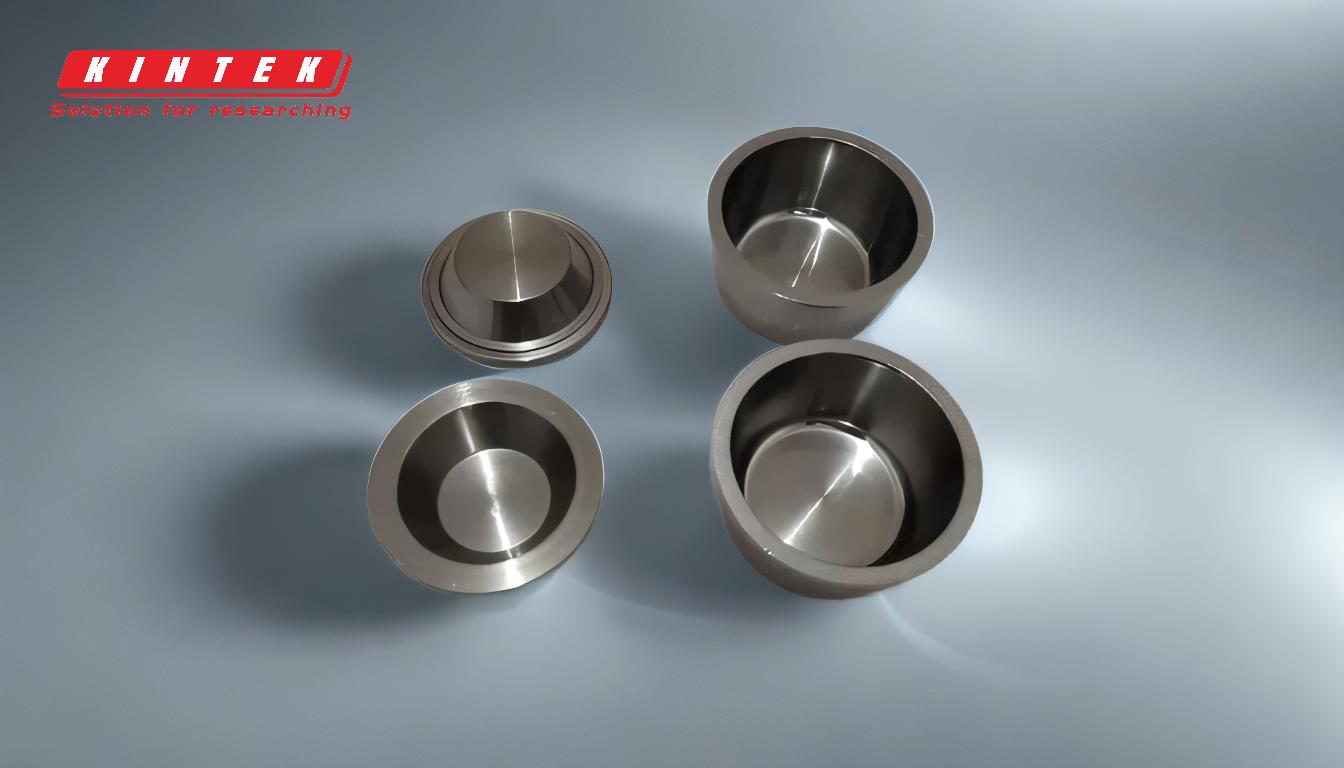
-
スパッタコーティングの概要:
- スパッタコーティングは、ターゲット材料に高エネルギーのイオンを照射して原子を放出させ、基板上に堆積させるPVDプロセスである。
- このプロセスは、導電性、耐久性、耐摩耗性などの表面特性を向上させる、薄く均一なコーティングを形成するために使用される。
-
スパッタコーティングプロセスの主な構成要素:
- 対象素材:基板にコーティングされる材料で、金属やセラミックが多い。
- 基板:コーティングが施される表面。
- スパッタリングカソード:電気を帯びてプラズマになる。
- プラズマ:電離ガスによって形成される高エネルギー状態の物質で、ターゲット物質に衝突する。
- 真空チャンバー:プロセスを促進するために低圧環境を維持する。
- プロセスガス:通常、アルゴンまたは酸素がプラズマの生成に使用される。
-
スパッタコーティングのステップ・バイ・ステップ・プロセス:
-
ステップ1:準備:
- 基板を洗浄し、スパッタリングチャンバーに入れる。
- チャンバー内を排気し、必要な真空度にする。
- プロセスガス(アルゴンまたは酸素)が導入され、コーティング組成を維持するために洗浄される。
-
ステップ2:プラズマ形成:
- スパッタリングカソードが帯電し、プラズマが形成される。
- このプラズマがターゲット材料に高エネルギーのイオンを浴びせます。
-
ステップ3:スパッタリング:
- ボンバードメントにより、ターゲット材料から原子が放出される。
- ターゲット材料の安定した均一な浸食を確実にするため、磁石がしばしば使用される。
-
ステップ4:蒸着:
- 放出された原子は真空中を移動し、基板上に堆積する。
- シャッターを使用して、基板が遊離原子にさらされるタイミングを制御することもできる。
-
ステップ5:ボンディング:
- 高エネルギーのターゲット材料が基板に衝突し、原子レベルの強い結合を形成する。
-
ステップ1:準備:
-
スパッタコーティングの利点:
- 均一性:薄く均一なコーティングが可能。
- 汎用性:金属、セラミックス、複合材など幅広い素材に使用可能。
- 強力な接着力:原子レベルの結合は、耐久性のあるコーティングを保証します。
- 表面特性の向上:導電性の向上、熱損傷の低減、SEMにおける二次電子放出の改善。
-
スパッタコーティングの用途:
- エレクトロニクス:半導体、薄膜トランジスタ、太陽電池の製造に使用される。
- 光学:反射防止コーティングやミラーの製造に応用。
- 自動車:エンジン部品の耐摩耗コーティングに使用。
- 医療機器:インプラントに生体適合性コーティングを提供。
- 研究開発:SEMやその他の分析技術用の試料作製に不可欠。
-
課題と考察:
- 熱管理:このプロセスではかなりの熱が発生するため、特殊な冷却システムが必要となる。
- 真空要件:高いバキュームが必要で、エネルギーを消費する可能性がある。
- 素材適合性:すべての材料がスパッタリングに適しているわけではなく、特定の条件や前処理が必要な場合もあります。
- コスト:特に大規模なアプリケーションや特殊なアプリケーションでは、設備コストや運用コストが高くつく可能性がある。
要約すると、スパッタコーティングは、プラズマ物理学を活用して基板上に薄く均一なコーティングを成膜する、高度に制御された汎用性の高いプロセスである。スパッタコーティングの用途はさまざまな産業に及んでおり、いくつかの課題がある一方で、コーティングの品質と耐久性の面でメリットがあるため、現代の製造および研究において貴重な技術となっている。
総括表
アスペクト | 詳細 |
---|---|
プロセス | 高エネルギーイオンを使用してターゲット原子を放出する物理蒸着(PVD)。 |
主な構成要素 | ターゲット材料、基板、スパッタリングカソード、プラズマ、真空チャンバー、ガス。 |
利点 | 均一なコーティング、強力な接着力、導電性の向上、耐久性 |
用途 | エレクトロニクス、光学、自動車、医療機器、SEMサンプル前処理。 |
課題 | 熱管理、真空要件、材料適合性、コスト。 |
スパッタコーティングがお客様のプロジェクトをどのように強化できるかをご覧ください。 今すぐ専門家にお問い合わせください !