アーク溶接では、消耗電極と非消耗電極の区別は、 溶接プロセスにおける役割にある。消耗電極は、溶融して溶接プールの一部となり、ワークピースを接合する溶加材を供給するように設計されている。一方、消耗電極は溶接中に溶融しない。アークを発生させるために使用され、必要に応じて別の充填材を必要とする場合がある。これらの電極の選択は、溶接プロセス、材 料の種類、希望の溶接特性によって異なる。以下では、各タイプの主な相違点、用途、考慮 点について詳しく説明する。
キーポイントの説明
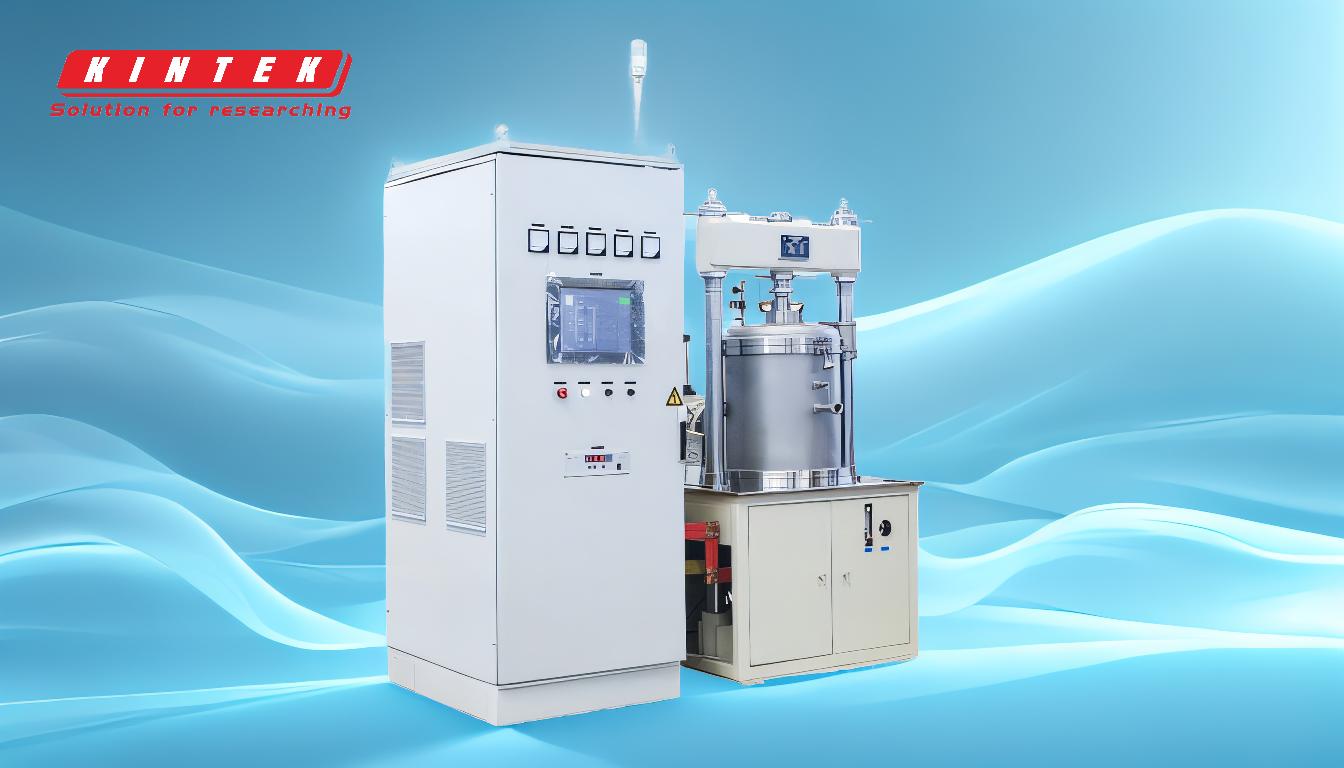
-
定義と機能:
- 消耗電極:これらの電極は溶接プロセス中に溶融し、溶接プー ルの一部となる。熱源(アーク発生器)と溶加材の両方の役割を果たす。例えば、被覆アーク溶接 (SMAW) やガス・メタル・アーク溶接 (GMAW) で使用される電極がある。
- 消耗品以外の電極:これらの電極は溶接中に溶融しない。主な役割はアークを発生させること で、追加の材料が必要な場合は、別途フィラー・ロッ ドが必要となる。例えば、タングステン・イナート・ガス (TIG)溶接に使用される電極がある。
-
素材構成:
- 消耗電極:通常、溶接される母材に適合する、または補 完する材料でできている。アークを安定させ、 溶接池を汚染から守り、溶接品質を向上させるた めに、フラックスで被覆されることが多い。
- 消耗品以外の電極:タングステンやカーボンなど、融点の高い素材から作られる。これらの素材は、溶けることなく高温に耐えることができるため選ばれる。
-
溶接プロセス:
- 消耗電極:SMAW、GMAW、FCAW (Flux-Cored Arc Welding)などのプロセスでよく使用される。これらのプロセスは、幅広い材料と板厚に適している。
- 消耗品以外の電極:主にTIG溶接に使用され、薄い材料や非鉄金属の溶接、高精度できれいな溶接を必要とする用途に最適。
-
メリットとデメリット:
-
消耗電極:
- メリット:フラックスコーティングにより、屋外や風の強い条件下でも使用しやすい。
- デメリット:除去が必要なスラグが発生する場合があり、溶接品質は電極の一貫性に影響される。
-
消耗品以外の電極:
- メリット:スパッタを最小限に抑えたクリーンで高品質な溶接が可能で、精密作業や薄い材料に最適。
- デメリット:蒸着速度が遅く、操作に熟練を要し、しばしば外部シールドガスを必要とする。
-
消耗電極:
-
アプリケーション:
- 消耗電極:汎用性が高く、厚い材料も溶接できるため、建築、造船、重加工に広く使用されている。
- 消耗品以外の電極:航空宇宙、自動車、職人的な金属加工など、高品質の溶接を必要とする産業で好まれる。
-
コストとメンテナンス:
- 消耗電極:一般に、大規模プロジェクトでは費用対効果が高いが、消耗品のため頻繁な交換が必要。
- 消耗品以外の電極:イニシャルコストは高いが、溶けないので長持ちする。ただし、磨耗により定期的な研ぎ直しや交換が必要な場合がある。
-
シールド要件:
- 消耗電極:多くの場合、フラックス・コーティングが施されており、プロセスによっては外部シールド・ガスの必要性を減らすことができる。
- 消耗品以外の電極:通常、溶接プールを大気汚染から保護するために、 外部シールド・ガス(アルゴンやヘリウムなど)が必 要となる。
-
スキルレベルとトレーニング:
- 消耗電極:初心者にも使いやすく、汎用溶接に適している。
- 消耗品以外の電極:特にTIG溶接では、アークを制御し、フィラー材を手動で送給するため、より高度な技術と訓練が必要となる。
これらの違いを理解することで、購入者は、材 料の種類、厚さ、希望する溶接品質、利用可能な資 源など、溶接プロジェクトの具体的な要件に基づ いて、十分な情報に基づいた決定を下すことができ る。
総括表:
アスペクト | 消耗電極 | 消耗品以外の電極 |
---|---|---|
定義 | 溶融して溶接プールの一部となり、溶加材となる。 | アークを発生させるため、別途フィラ ロッドが必要になる場合がある。 |
素材構成 | 母材と同じ材質でできており、フラックスでコーティングされていることが多い。 | タングステンやカーボンなどの高融点素材を使用。 |
溶接プロセス | smaw、gmaw、fcaw。 | 主にTIG溶接。 |
メリット | 蒸着速度が速く、厚い材料に適しており、屋外での使用が容易。 | 精密作業や薄い素材に最適な、クリーンで高品質な溶接。 |
デメリット | 溶接品質は電極の一貫性に左右される。 | 成膜速度が遅く、熟練と外部シールドガスが必要。 |
アプリケーション | 建設、造船、重加工。 | 航空宇宙、自動車、職人的金属加工。 |
コストとメンテナンス | 大規模なプロジェクトでは費用対効果が高いが、頻繁な交換が必要。 | 初期費用は高いが長持ちする。定期的な研ぎ直しや交換が必要な場合がある。 |
シールド要件 | フラックス・コーティングがシールドを提供し、外部ガスの必要性が少ない。 | 外部シールドガス(アルゴンやヘリウムなど)が必要。 |
スキルレベル | 初心者向けで、汎用溶接に適している。 | 精密で高品質な溶接に最適。 |
溶接プロジェクトに適した電極の選択にお困りですか? 専門家にご相談ください をご覧ください!