薄膜の接着性とは、薄膜とその基板との間の結合強度のことで、様々な用途において薄膜の耐久性、信頼性、機能性を確保するために重要である。接着性は、表面処理、材料適合性、成膜技術などの要因に影響される。接着不良は、半導体、ディスプレイ、医療機器などの用途において、薄膜の剥離、性能低下、故障につながる可能性があります。接着性を理解し最適化することは、薄膜において望ましい機械的、電気的、光学的特性を達成するために不可欠である。
キーポイントの説明
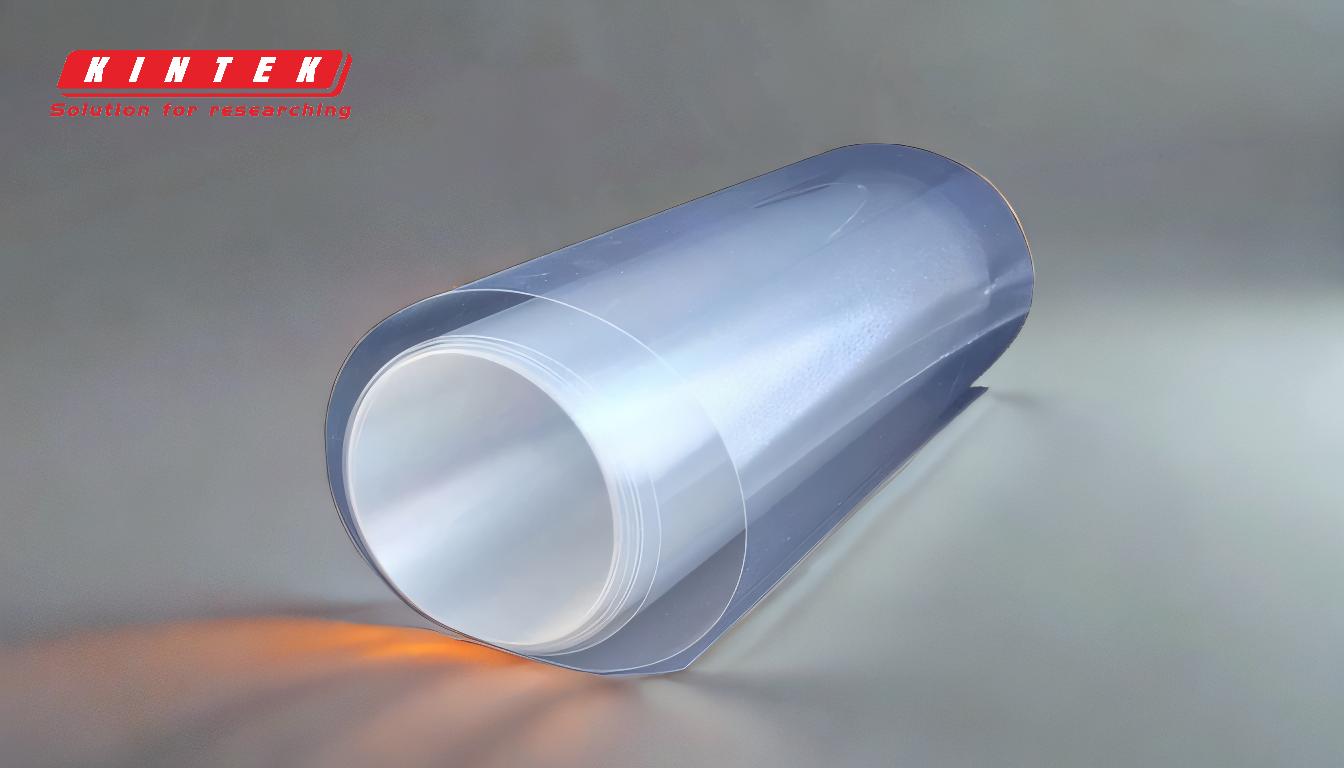
-
薄膜における接着の定義:
- 密着性とは、薄膜とその上に成膜された基板との間の結合強度を指す。機械的、熱的、環境的ストレスの下で、薄膜が基板にどれだけ密着するかを示す尺度です。
- 強固な接着力により、薄膜はその使用寿命の間、無傷で機能的な状態を保つことができます。
-
接着の重要性:
- 接着性は、半導体、ディスプレイ、医療機器などの用途における薄膜の性能と耐久性にとって非常に重要です。
- 接着性が悪いと、層間剥離やクラック、剥離につながり、薄膜やその一部であるデバイスの機能を損なうことになります。
-
接着に影響する要因:
- 表面処理:基材表面の適切な洗浄と処理(プラズマ洗浄、化学エッチングなど)により、汚染物質を除去し、反応性の表面を形成することで接着性を高める。
- 材料適合性:薄膜と基板の化学的・物理的特性が適合していなければ、強固な接合は望めない。
- 蒸着技術:物理的気相成長法(PVD)、化学的気相成長法(CVD)、原子層堆積法(ALD)などの方法は、堆積速度、温度、エネルギーを制御することで密着性に影響を与えることができる。
- 界面層:界面層(酸化膜など)の形成は、材料や条件によって、接着性を向上させたり、妨げたりする。
-
密着性の測定:
- 接着強度は、スクラッチ試験、ピール試験、プルオフ試験などの手法を用いて測定することができる。
- これらの方法では、薄膜を基材から剥がすのに必要な力を評価し、接着の質に関する定量的なデータを提供する。
-
用途と意義:
- 半導体 半導体 半導体デバイスは、強力な接着力によって信頼性の高い電気的接続が確保され、デバイスの故障を防ぐことができます。
- ディスプレイ ディスプレイ 接着はコーティングの耐久性と光学性能に影響する。
- 医療機器では 医療機器 接着は、生体適合性と長期的な機能性にとって非常に重要です。
-
課題と解決策:
- 挑戦:大面積や複雑な形状で一貫した接着を達成することは困難です。また、湿度や温度などの環境要因も接着に影響します。
- ソリューション:高度な表面処理、蒸着パラメーターの最適化、密着促進層(プライマーやタイ層など)の使用により、密着性を向上させることができる。
-
今後の動向:
- フレキシブルエレクトロニクスやナノテクノロジーなど、新たな用途における接着性を高めるための新材料や成膜技術の開発に重点を置いた研究を行っている。
- また、表面特性評価と密着性試験の革新により、薄膜の密着メカニズムの理解も進んでいます。
これらの重要なポイントに取り組むことで、メーカーや研究者は薄膜の接着を最適化し、幅広い用途における薄膜の信頼性と性能を確保することができる。
要約表
主な側面 | 詳細 |
---|---|
定義 | 薄膜と基板間の接着強度。 |
重要性 | アプリケーションの耐久性、信頼性、機能性を確保する。 |
影響因子 | 表面処理、材料適合性、蒸着技術 |
測定技術 | スクラッチ試験、剥離試験、引き剥がし試験 |
用途 | 半導体、ディスプレイ、医療機器 |
課題 | 安定した接着、環境要因。 |
ソリューション | 高度な表面処理、最適化された蒸着、接着促進層。 |
将来のトレンド | 新素材、成膜技術、高度な試験方法。 |
薄膜の接着を最適化し、優れたパフォーマンスを実現します。 今すぐ専門家にご相談ください !