射出成形プロセスは、金型に溶融材料を射出することによって部品を製造するために使用される製造技術である。工程は通常2秒から2分で、クランプ、射出、冷却、射出の4つの主な段階から構成されています。各段階は、最終製品が望ましい仕様を満たすために重要な役割を果たします。これらの段階を理解することは、成形プロセスを最適化し、欠陥を減らし、効率を改善するために不可欠です。
キーポイントの説明
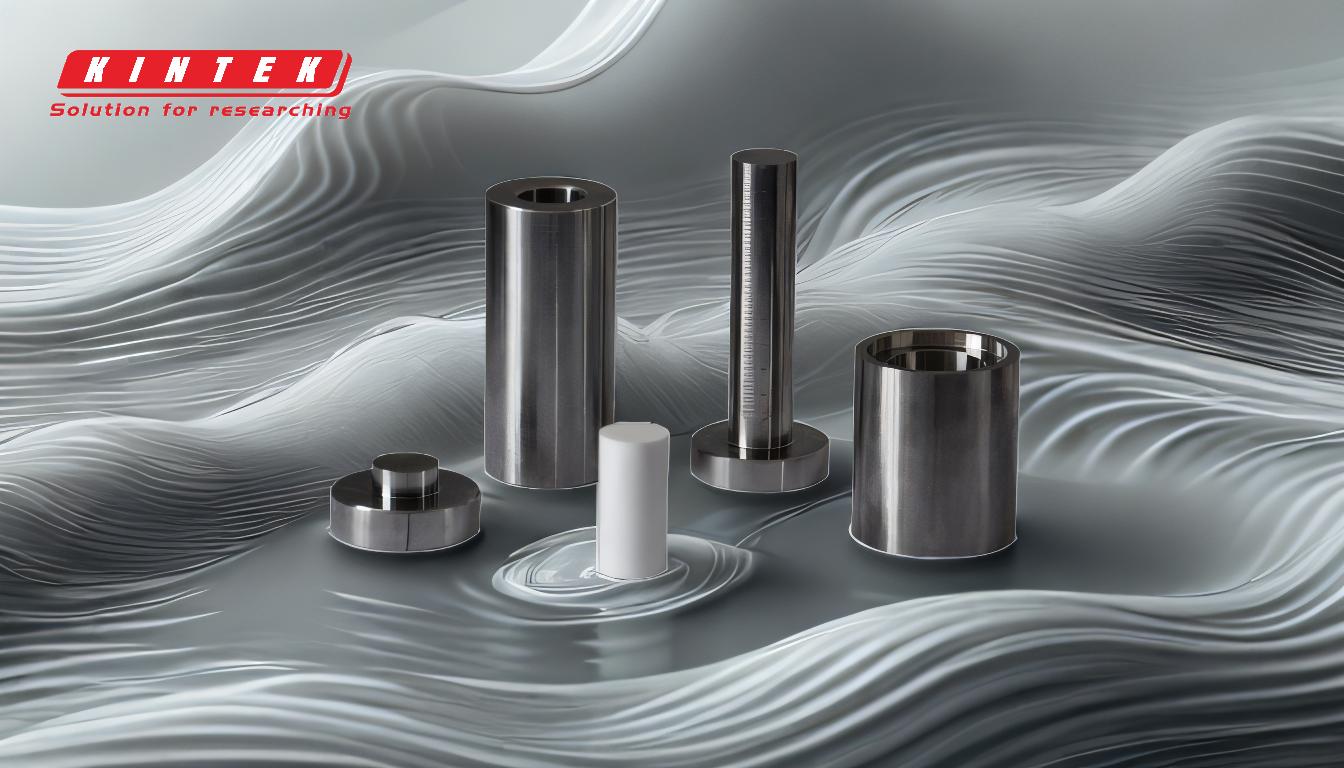
-
クランピング・ステージ:
- 目的:型締めの段階は、射出成形プロセスの最初のステップです。その主な目的は、金型の2つの半分をしっかりと閉じて、溶融材料の射出に備えることです。
- 工程:金型は射出成形機に取り付けられ、クランプユニットは射出される材料の圧力に耐えるのに十分な力で金型の半分を保持します。必要なクランプ力は、製造される部品のサイズと複雑さによって異なります。
- 重要性:適切なクランピングにより、射出段階と冷却段階において金型が閉じた状態を維持し、バリ(金型キャビティから余分な材料が出る)などの不良を防ぎます。
-
射出段階:
- 目的:射出段階では、金型キャビティに溶融材料を導入する。この段階は、最終製品を成形するために重要です。
- プロセス:通常ペレット状の材料は、射出成形機のバレルに供給され、そこで溶融状態になるまで加熱される。その後、溶融した材料が高圧下で金型キャビティに射出される。射出速度、圧力、温度は、材料が完全に均一に金型に充填されるように慎重に制御されます。
- 重要性:射出段階は、部品の表面仕上げ、寸法精度、構造的完全性の品質を決定する。射出が不十分だと、ショートショット(金型への充填が不完全)やヒケ(表面の窪み)などの欠陥につながります。
-
冷却段階:
- 目的:冷却段階では、溶融材料が金型内で固化し、金型キャビティの形状になります。
- 工程:金型キャビティが充填された後、材料は冷却され固化し始める。冷却時間は、使用する材料、部品の厚さ、金型の設計によって異なります。冷却は通常、水やその他の冷却媒体を循環させる金型内の冷却チャンネルによって促進されます。
- 重要性:適切な冷却は、部品がその形状と寸法安定性を維持するために不可欠です。冷却が不十分な場合、部品の反り、収縮、内部応力が発生する可能性があります。
-
排出段階:
- 目的:射出段階では、固化した部品を金型から取り出します。
- 工程:材料が十分に冷えて固まると、金型が開き、エジェクターピンまたはプレートが金型キャビティから部品を押し出します。その後、部品は回収され、金型は再び閉じて次のサイクルに備えます。
- 重要性:射出段階は、部品や金型に損傷を与えないよう注意深く管理する必要があります。適切な射出により、部品が傷や変形などの欠陥なくスムーズに放出されます。
まとめ
射出成形プロセスは、複雑な形状と高い精度を持つ部品を製造するための非常に効率的な方法である。クランプ、射出、冷却、射出の4つの段階は、プロセスの成功に不可欠です。高品質の部品を確実に生産するためには、各段階を注意深く制御する必要があります。これらの段階を理解することで、メーカーは成形プロセスを最適化し、欠陥を減らし、全体的な効率を向上させることができます。
総括表
ステージ | 目的 | キー詳細 |
---|---|---|
クランプ | 射出準備のために金型を確実に閉じます。 | 圧力がかかっても金型を確実に閉じ、バリなどの欠陥を防ぎます。 |
射出 | 金型キャビティに溶融材料を導入します。 | 速度、圧力、温度を制御し、完全で均一な充填を保証する。 |
冷却 | 金型内で材料を固める。 | 反り、収縮、内部応力を防ぐために冷却チャネルを使用します。 |
射出 | 固化した部品を金型から取り出します。 | エジェクターピンまたはプレートにより、傷や変形を避けながらスムーズにパーツを取り出します。 |
射出成形プロセスを最適化する準備はできましたか? 当社の専門家に今すぐご連絡ください オーダーメイドのソリューションを