ボールミルでの製品の大きさは、粉砕ボールのサイズと密度、粉砕時間、供給材料の物理的・化学的性質、ミルの回転速度、供給速度、ミル自体の設計(ドラムの直径と長さの比率など)など、いくつかの要因に影響されます。ボールが小さく、粉砕時間が長いほど、一般的に粒子は細かくなり、粉砕される原料の硬度や性質も重要な役割を果たす。さらに、粉砕プロセスの効率は、粉砕された製品のタイムリーな除去や粉砕機のアーマー表面の形状にも影響されます。
キーポイントの説明
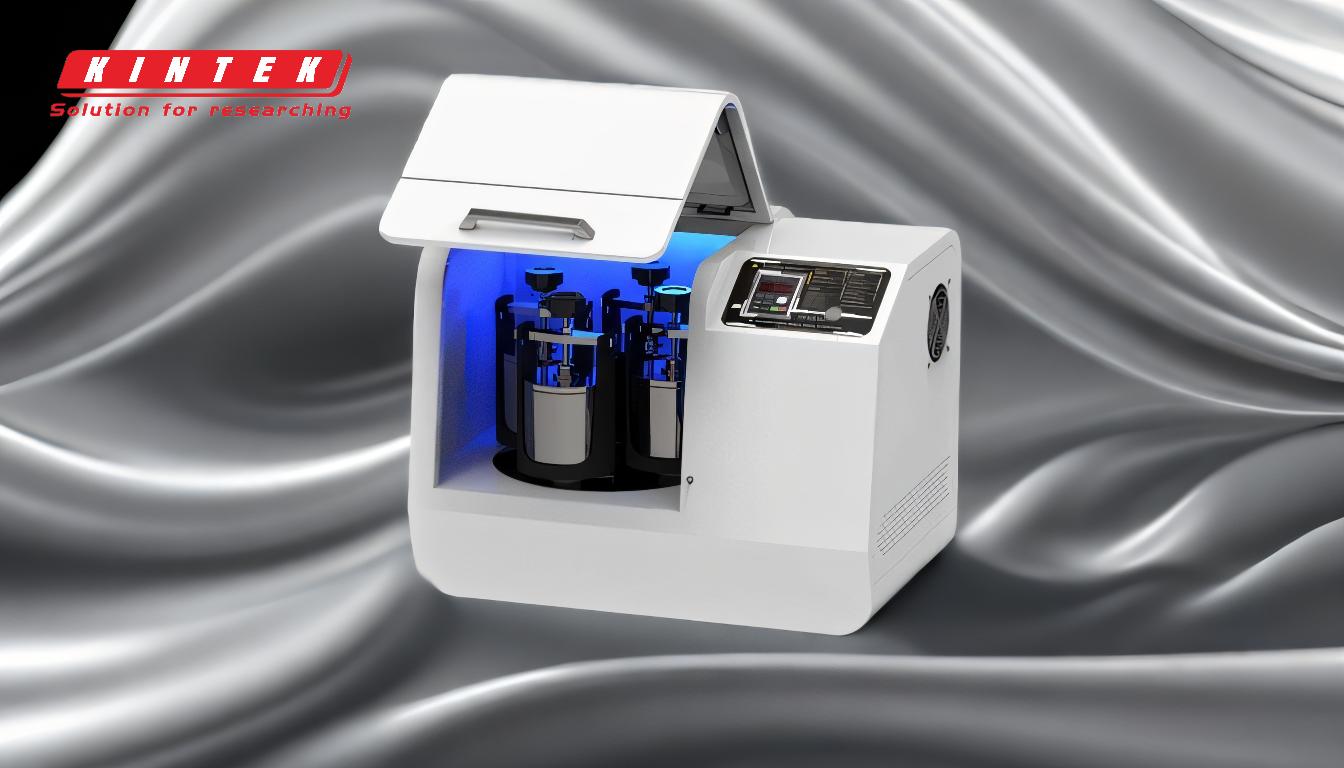
-
研削ボールのサイズと密度:
- 小さいボール:小さな粉砕ボールは、体積に対して表面積が大きく、被粉砕物との接触点が多くなるため、より微細な粒子を生成するのに有効です。
- 密度:ボールの密度が高いほど、材料により多くのエネルギーを与えることができ、より効果的な粉砕につながります。しかし、最適なサイズと密度は、処理される材料によって異なります。
-
粉砕時間:
- 長い研削時間:粉砕時間を長くすることで、ボールと原料の衝突回数が増え、一般的に粒子径が小さくなる。しかし、それ以上粉砕を続けても粒子径が大きく減少しない、収穫逓減のポイントがある。
-
供給原料の物理的・化学的特性:
- 硬度:硬い材料ほど粉砕に多くのエネルギーを必要とするため、異なるボールサイズや長い粉砕時間が必要になる場合がある。
- 材料の性質:原料のもろさ、含水率、その他の特性は、粉砕のしやすさに影響します。
-
ミルの回転速度:
- 最適速度:粉砕機の回転速度は慎重にコントロールしなければならない。回転数が低すぎると、ボールが効果的にカスケードされないことがあり、粉砕効率が低下する。回転数が高すぎるとボールが遠心分離し、粉砕効率が低下する。
-
供給速度とベッセル内のレベル:
- 送り速度:安定した適切な供給量により、粉砕効率を低下させる過負荷を防ぎます。
- 材料レベル:粉砕機内の原料の量は粉砕作用に影響します。材料が多すぎるとボールの衝撃を和らげ、少なすぎると粉砕効率が悪くなる。
-
ミルの設計:
- ドラムの直径と長さの比:ドラムの直径と長さの最適な比率(L:D比)は、通常1.56~1.64です。この比率は、粉砕機内での原料の滞留時間と粉砕プロセスの効率に影響します。
- アーマー表面形状:粉砕機の内面形状は、ボールや原料の動きに影響を与え、粉砕効率に影響を与えます。
-
粉砕された製品のタイムリーな除去:
- 効率:粉砕された製品を適時に除去することで、過粉砕を防ぎ、粉砕機の効率的な運転を保証します。過粉砕はエネルギーの浪費につながり、最終製品の品質を低下させる可能性がある。
-
滞留時間:
- 材料滞留時間:原料がミルチャンバーに滞留する時間は、粉砕の程度に直接影響します。一般的に滞留時間が長いほど粒子は細かくなりますが、非効率にならないように他の要素とのバランスをとる必要があります。
これらの要因を注意深くコントロールすることで、オペレーターはボールミリングプロセスを最適化し、特定の用途に適した粒度分布を得ることができます。
要約表
因子 | 粒子径への影響 |
---|---|
粉砕ボールのサイズと密度 | ボールが小さく、密度が高いほど細かい粒子が得られます。 |
粉砕時間 | 粉砕時間が長いと粒子径は小さくなるが、収穫が減少する可能性がある。 |
供給原料の特性 | 硬い材料や脆い材料は、粉砕に多くのエネルギーと時間を必要とする。 |
回転速度 | 最適な回転数により、効率的な粉砕を実現します。 |
送り速度と材料レベル | 安定したフィードレートと適切な材料レベルにより、粉砕効率が向上します。 |
ミル設計 | ドラム直径対長さ比(1.56~1.64)とアーマー表面形状が研削効率に影響。 |
タイムリーな製品除去 | 過粉砕を防ぎ、効率を維持します。 |
滞留時間 | 滞留時間が長いほど、より微細な粒子が得られますが、効率とのバランスをとる必要があります。 |
ボールミリングプロセスを最適化することで、優れた結果が得られます。 今すぐ専門家にご相談ください !