ダイヤモンドライクカーボン(DLC)コーティングは、その優れた耐摩耗性、低摩擦性、化学的不活性性により広く使用されている。しかし、DLCコーティングには、処理温度の制限、高温要件による適用上の課題、応力、クラック、コーティングの均一性に関する問題など、いくつかの欠点もある。さらに、DLCコーティングは、すべての材料や用途、特に断続的な切断工程を伴うものや精密なマスキングを必要とするものには適さない場合がある。このような要因によって、DLCコーティングの有効性や適用性が制限される場合があります。
キーポイントの説明
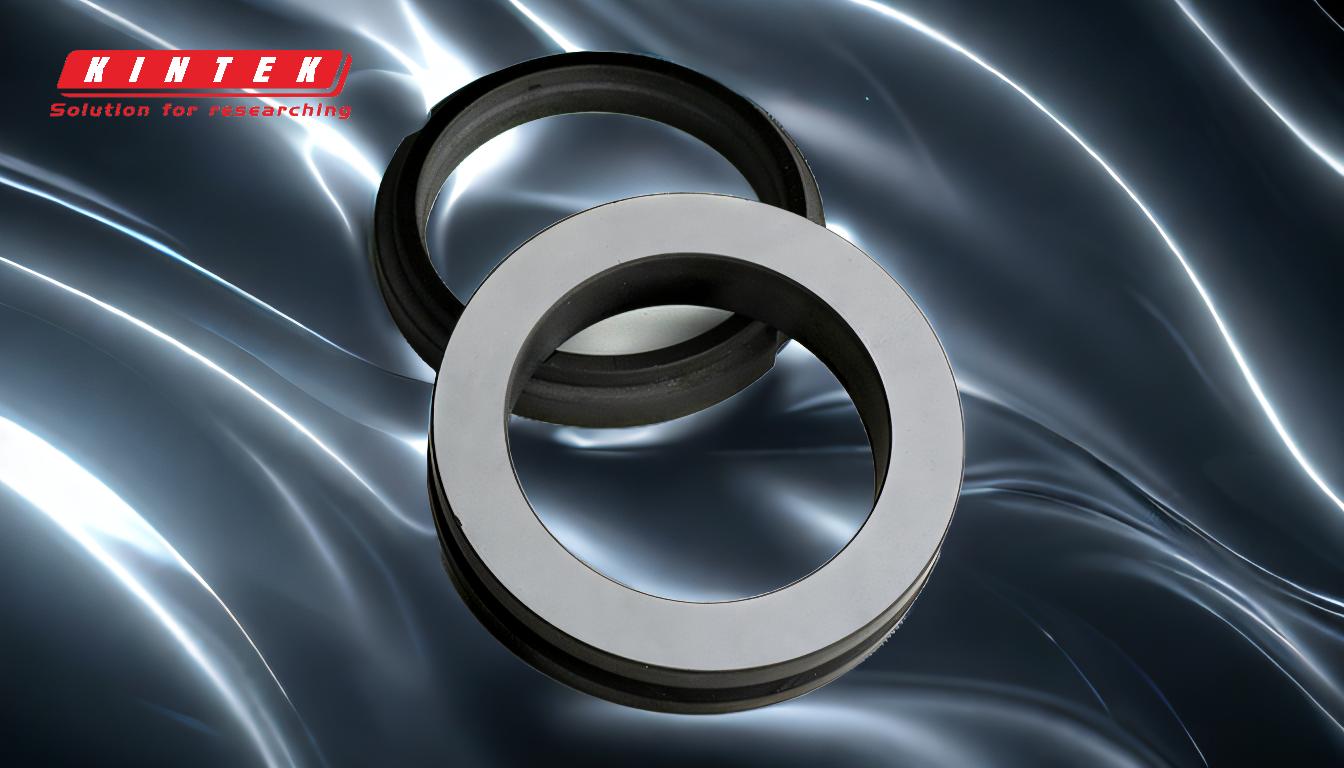
-
高い加工温度:
- DLCコーティング、特に化学気相成長法(CVD)によるコーティングは、高い処理温度(800~1000℃、1875~1925°F)を必要とする。このため、超硬合金など、このような熱に耐えられる材料に使用が限定される。多くの基材、特に融点や熱安定性の低い基材は、このような条件に耐えることができないため、DLCコーティングの適用範囲が制限される。
-
引張応力とクラック:
- CVDコーティングは厚いため(10~20μm)、冷却中に引張応力が発生することがある。この応力はしばしば微細なクラックとなり、外部からの衝撃によって伝播し、コーティングの剥離を引き起こすことがある。このため、DLCコーティングは、コーティングが破損しやすいフライス加工などの断続切削加工を伴う用途には適していない。
-
マスキングとコーティングの均一性の限界:
- CVDプロセスでは、特定の領域をマスクすることが困難であり、多くの場合、何でもありのコーティングになってしまう。この精度の低さは、選択的なコーティングを必要とする用途では問題となる。さらに、コーティングできる部品の大きさは反応室の容量によって制限され、部品はコーティングのために個々の部品に分解しなければならないことが多い。
-
不均一な粒構造と表面粗さ:
- CVDダイヤモンドコーティングの粒構造は、成長プロセスにより不均一であり、表面粗さは厚さとともに変化します。このため、サーマルスプレッダーのような滑らかな表面を必要とする用途では研磨が必要となります。不均一性は、コーティングの機械的特性や熱的特性にも影響を与える可能性がある。
-
準安定な性質と結合のばらつき:
- DLCはアモルファスまたは水素化アモルファスカーボンの準安定形態で、sp2結合とsp3結合が混在している。膜の特性はこれらの結合の比率に依存し、その比率は大きく変動する。このばらつきは、硬度、耐摩耗性、その他の重要な特性のばらつきにつながり、異なるコーティング間で均一な性能を達成することを困難にしている。
-
断続切削加工への適性の限界:
- DLCコーティングは、応力下でクラックや剥離が発生しやすいため、フライス加工のような断続切削加工では効果が低い。このような加工では、衝撃や熱サイクルが繰り返されるため、コーティングの欠陥が悪化する可能性があり、このような用途での使用は制限される。
-
物流の課題:
- CVDプロセスはオンサイト・プロセスではないため、部品は専門のコーティング・センターまで輸送する必要があります。このため、特に大型部品や複雑な部品の場合、製造工程に物流上の複雑さ、コスト、時間が加わります。
-
耐薬品性と耐摩耗性のトレードオフ:
- DLCコーティングはその優れた耐摩耗性と耐薬品性で知られていますが、これらの特性は成膜技術やコーティングの具体的な組成によって変化します。場合によっては、最適な耐摩耗性を達成するために、密着性や熱伝導性などの他の望ましい特性が犠牲になることもあります。
まとめると、DLCコーティングは耐久性、摩擦低減、耐薬品性の面で大きな利点を持つ一方で、加工温度が高いこと、応力やクラックの影響を受けやすいこと、マスキングや均一性に限界があることなどが顕著な欠点となる。特定の用途にDLCコーティングを選択する際には、これらの要素を注意深く考慮する必要がある。
総括表
デメリット | 特徴 |
---|---|
高い加工温度 | 800~1000℃が必要で、超硬合金のような耐熱性材料に限定される。 |
引張応力とクラック | 厚いコーティングは応力によるクラックを引き起こし、断続切削加工には適さない。 |
マスキングとコーティングの均一性 | CVDプロセスではマスキングの精度が低いため、均一なコーティングが得られない。 |
不均一な結晶粒構造 | 粒構造と表面粗さが異なるため、平滑な用途には研磨が必要。 |
準安定な性質と結合のばらつき | 特性はsp2/sp3結合比に依存し、硬度と耐摩耗性が一定しない。 |
断続切削への適性は限定的 | フライス加工や類似の加工では、応力や熱サイクルにより破損しやすい。 |
物流の課題 | 部品を専門センターまで輸送する必要があり、時間とコストがかかる。 |
耐薬品性と耐摩耗性のトレードオフ | 最適な耐摩耗性は、密着性や熱伝導性を損なう可能性があります。 |
DLCコーティングがお客様の用途に適しているかどうかの判断にお困りですか? 当社の専門家に今すぐご連絡ください にご相談ください!