スパッタリングは、物理的気相成長(PVD)技術として広く用いられており、いくつかの利点と欠点がある。特に、均一性、密度、膜特性の制御に優れた高品質の薄膜を製造できる点が評価されている。しかし、コンタミネーション、リフトオフプロセスとの組み合わせの難しさ、レイヤー・バイ・レイヤー成長における能動的制御の限界といった課題は、顕著な欠点である。このような問題があるにもかかわらず、スパッタリングは、特に膜厚や材料特性の精密な制御を必要とする用途において、汎用性が高く効率的な方法であることに変わりはない。
要点の説明
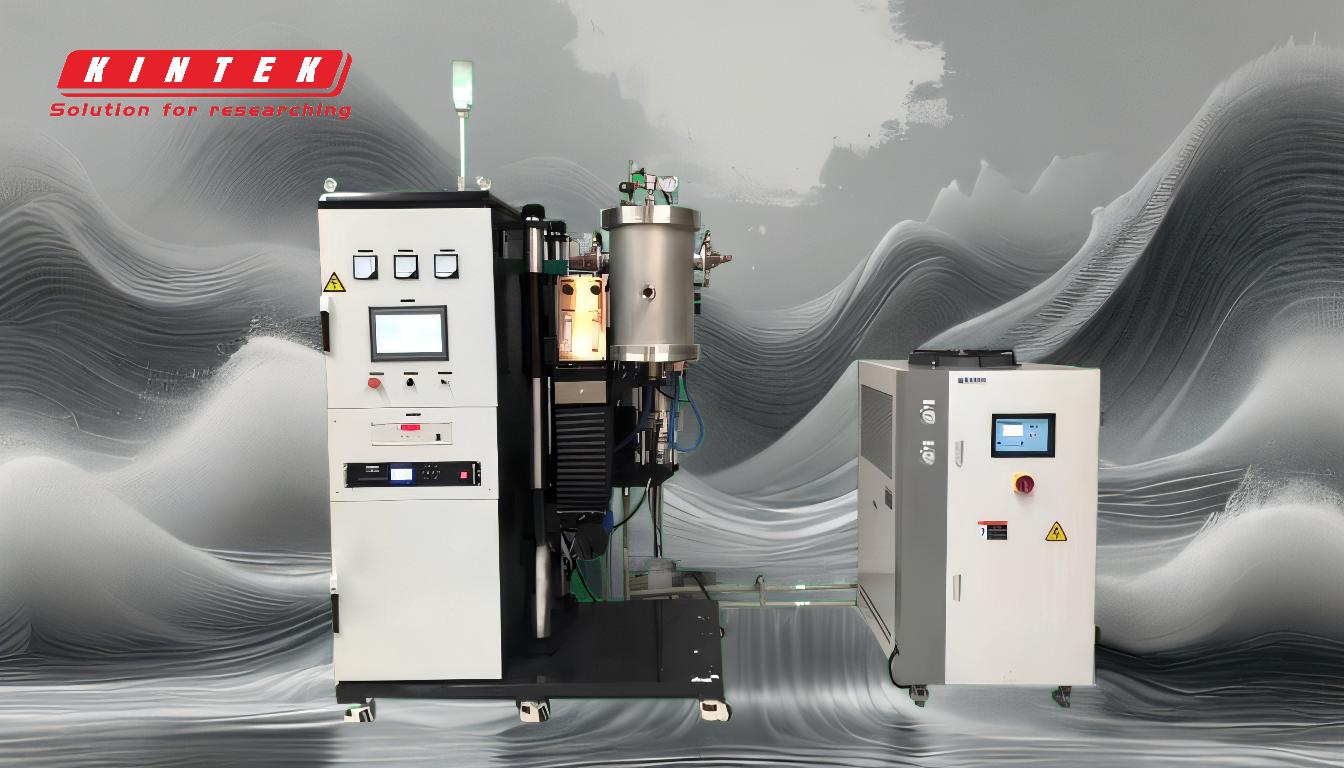
-
スパッタリングの利点:
- 高品質フィルム:スパッタリングは、低粗度、制御された粒径、精密な化学量論など、優れた形態学的品質を持つ膜を生成する。そのため、表面品質が重要視される用途に最適です。
- フィルム高密度化:このプロセスは、他の成膜方法と比較して、より優れた膜の緻密化をもたらし、機械的および光学的特性の向上につながる。
- 低残留応力:スパッタリングで成膜された膜は、低温または中温の成膜プロセスにより、一般的に低または中程度の残留応力を示し、これは基板の完全性にとって有益である。
- 高い成膜速度:スパッタリングは、膜厚の制限なしに高い成膜レートを提供するため、厚膜の製造に効率的です。
- 基板洗浄:蒸着前に真空チャンバー内で基板をクリーニングできるため、膜の密着性と品質が向上する。
- 均一性とコントロール:スパッタリングでは、電力、圧力、蒸着時間などのプロセスパラメーターを調整することで、膜厚と均一性の優れた制御が可能です。
-
スパッタリングの短所:
- 汚染問題:ソース材料やスパッタリングガスからの不純物が膜中に拡散し、汚染につながる可能性がある。このため、溶融温度や純度に基づくコーティング材料の選択が制限される。
- リフトオフプロセスの難しさ:スパッタされた原子の拡散輸送が完全なシャドーイングを不可能にし、膜構造化のためのスパッタリングとリフトオフプロセスの組み合わせを複雑にしている。
- レイヤー・バイ・レイヤー成長における課題:正確なレイヤー・バイ・レイヤー成長のための能動的制御は、パルス・レーザー蒸着法などに比べてスパッタリングではより困難である。
- 不活性ガス不純物:アルゴンなどの不活性スパッタリングガスは、成長膜中の不純物となり、その特性に影響を与える可能性があります。
-
マグネトロンスパッタリング:
- 強化された素材特性:マグネトロンスパッタリングは、基板を貫通する高エネルギー原子の均一でタイトなパターンを形成し、耐食性、耐摩耗性、特定の光学的または電気的特性などの特性を向上させます。
- 高い成膜速度と精度:この技術は、高い成膜速度と成膜プロセスの精密な制御を提供し、マイクロエレクトロニクスや半導体用途の誘電体膜や窒化膜の成膜に特に有用である。
-
用途と汎用性:
- マイクロエレクトロニクスと半導体:スパッタリングは、高品質の誘電体膜や窒化膜を精密に制御しながら成膜できるため、これらの分野で広く利用されている。
- 現在進行中の進歩:継続的な研究開発により、スパッタリングの能力と用途が拡大し、多用途で進化する技術となっている。
要約すると、スパッタリングは強力で汎用性の高い成膜技術であり、高品質の薄膜を製造する上で大きな利点がある。しかし、汚染や特定のプロセス統合の難しさといった課題もある。これらの長所と短所を理解することは、特定の用途に適した成膜方法を選択するために不可欠である。
要約表
側面 | メリット | デメリット |
---|---|---|
フィルム品質 | 低粗度、制御されたグレインサイズ、化学量論による高品質フィルム | ソース材料やスパッタリングガスによる汚染の問題 |
膜の緻密化 | 高密度化による機械的・光学的特性の向上 | リフトオフプロセスとの組み合わせが難しい |
残留応力 | 低または中程度の残留応力、基板の完全性に有益 | レイヤー・バイ・レイヤー成長におけるアクティブ制御の課題 |
蒸着速度 | 膜厚制限のない高い蒸着速度 | 膜特性に影響する不活性ガス不純物(アルゴンなど |
基板クリーニング | チャンバー内洗浄による膜の密着性と品質の向上 | |
均一性とコントロール | 膜厚と均一性を正確に制御 |
スパッタリングとその応用についてもっと知りたいですか? 当社の専門家に今すぐご連絡ください オーダーメイドのソリューションを