スパッタコーティングは、SEM試料前処理や薄膜蒸着など様々な用途で広く使用されているが、その効率、コスト、最終製品の品質に影響するいくつかの欠点がある。これらの欠点には、汚染、材料の制限、プロセスの複雑さ、装置コストに関する問題が含まれる。これらの欠点を理解することは、スパッタコーティングが特定の用途に適した技術であるかどうかを十分な情報に基づいて判断する上で極めて重要である。
要点の説明
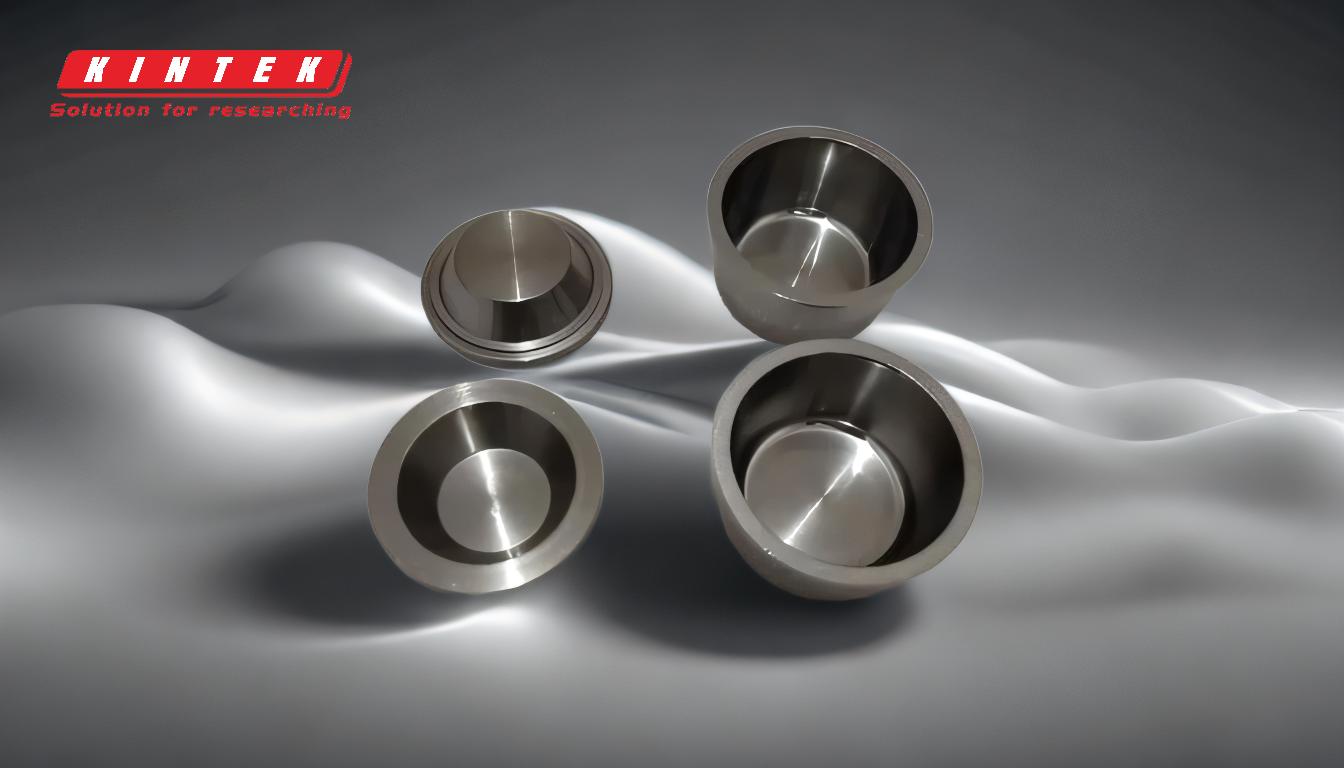
-
フィルム汚染のリスク:
- 不純物拡散:スパッタリング工程では、ターゲット材料や環境からの不純物が膜中に拡散し、汚染につながることがある。これは、高純度膜を必要とする用途で特に問題となる。
- ガス状汚染物質:スパッタリングに使用されるプラズマは、ガス状の汚染物質を活性化させる可能性があり、その汚染物質がフィルムに取り込まれることで、汚染リスクがさらに高まる。
-
材料の制限:
- 溶融温度の制約:コーティング材料の選択は、その融点によって制限される。融点が非常に高い材料はスパッタコーティングに適さない場合があり、使用できる材料の範囲が制限される。
- 反応性スパッタリングにおけるターゲットポイズニング:反応性スパッタ蒸着では、ターゲット材料がガスと反応するのを防ぐため、ガス組成を注意深く制御する必要がある。
-
プロセスの複雑さと制御:
- パラメータ最適化:スパッタコーティングには、圧力、出力、ガス組成などのパラメーターを慎重に最適化する必要がある。これには時間がかかり、かなりの専門知識が必要になることもある。
- レイヤーごとの成長制御:レイヤーごとの成長を正確に制御することは、パルスレーザー蒸着のような他の蒸着法に比べて難しい。これは、フィルムの品質や均一性に影響を与える可能性があります。
-
設備と運用コスト:
- 高価なターゲット:スパッタリングターゲットは高価であることが多く、材料の使用効率が悪いため、運用コストが高くなることがある。
- 冷却要件:スパッタリングで使用されるエネルギーの大部分は熱に変換されるため、冷却システムが必要となる。これはエネルギーコストを増加させるだけでなく、生産速度を低下させる。
-
フィルムの品質と均一性:
- 不均一な蒸着フラックス:スパッタリングにおける成膜フラックスは不均一であることが多く、均一な膜厚を得るためには移動治具を使用する必要がある。このためプロセスが複雑になる。
- 変化した表面形状:場合によっては、スパッタコーティングによって試料の表面形状が変化することがあり、表面の完全性が重要視される用途では望ましくないことがあります。
- 原子番号-コントラストの損失:コーティング材料が元の表面と置き換わることで、原子番号コントラストが失われ、SEMイメージングにおいて大きな欠点となることがある。
-
他のプロセスとの統合:
- リフトオフプロセスへの挑戦:スパッタ蒸着は、スパッタされた原子の拡散輸送のため、膜構造化のためのリフトオフプロセスとの組み合わせが難しい。これはコンタミネーションの問題につながり、完全なシャドーイングを不可能にする。
- 不活性ガスの不純物:不活性スパッタリングガスが成長膜中の不純物となり、その特性や性能に影響を及ぼす可能性がある。
まとめると、スパッタコーティングには、さまざまな材料を成膜でき、良好な密着性を実現できるなど、いくつかの利点がある一方で、重大な欠点もある。これには、汚染リスク、材料の制限、プロセスの複雑さ、高い装置コストと運用コスト、均一な膜質を達成するための課題、他のプロセスとの統合の難しさなどが含まれる。スパッタコーティングが特定の用途に適した技術であるかどうかを判断する際には、これらの要因を慎重に検討することが不可欠である。
総括表:
スパッタコーティングの欠点 | 主な課題 |
---|---|
フィルム汚染リスク | 不純物拡散、ガス状汚染物質 |
材料の制約 | 溶解温度の制約、ターゲット被毒 |
プロセス複雑性 | パラメータ最適化、層ごとの成長制御 |
高い装置コスト | 高価なターゲット、冷却要件 |
膜質の問題 | 不均一な蒸着、表面形状の変化 |
統合の課題 | リフトオフプロセスの難しさ、不活性ガスの不純物 |
スパッタコーティングがお客様の用途に適しているかどうかの判断にお困りですか? 当社の専門家に今すぐご連絡ください にご相談ください!