スパッタ蒸着は、様々な基板上に薄膜を形成するための汎用性が高く、広く利用されている技術である。その用途は、半導体製造、データ・ストレージ、光学、再生可能エネルギーなど、さまざまな業界に及んでいる。主な用途には、コンピューター・ハードディスク、集積回路、反射防止コーティング、太陽電池などがある。このプロセスは、精密で均一な高品質の薄膜を成膜する能力が評価され、現代の技術や産業用途に不可欠なものとなっている。
キーポイントの説明
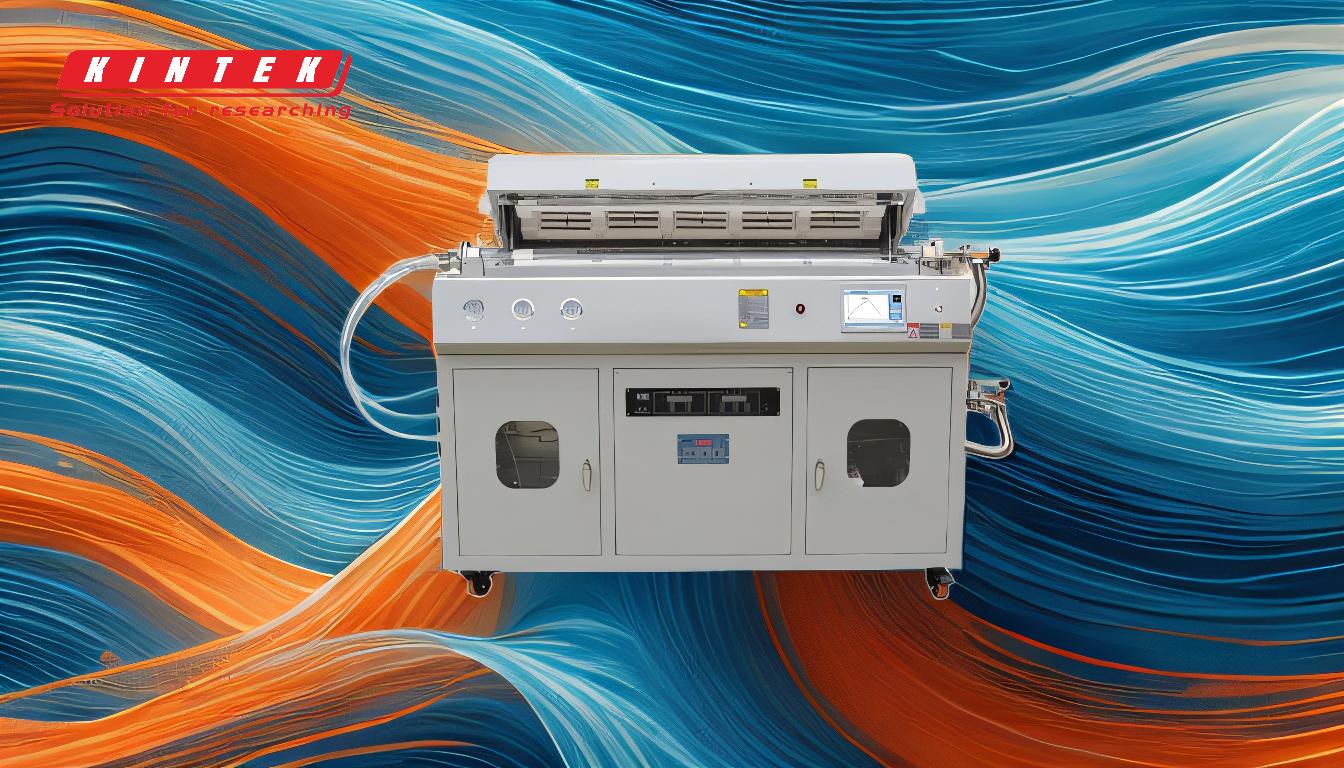
-
半導体・集積回路製造
- スパッタ蒸着は、導電性、絶縁性、または半導体材料の薄膜をシリコンウェハー上に堆積させるために、半導体産業で広く使用されている。
- これは、集積回路(IC)の相互接続、コンタクトメタル、およびその他のコンポーネントを作成するために非常に重要です。
- このプロセスにより、高精度と均一性が保証され、現代の電子機器の小型化と性能向上に不可欠なものとなっている。
-
データストレージ(ハードディスクと光メディア)
- スパッタ蒸着の最も初期の、そして最も重要な用途のひとつは、コンピュータのハードディスク製造である。
- コバルト合金などの磁性薄膜をディスク基板に成膜することで、データの保存が可能になる。
- また、CDやDVDの製造にも使用され、性能や耐久性を高めるために反射層や保護層が施される。
-
光学コーティング
- スパッタ蒸着は、ガラスに反射防止膜を形成するために用いられ、眼鏡、カメラレンズ、建築窓などに広く利用されている。
- 赤外光を反射してエネルギー効率を向上させる低放射率(Low-E)コーティングも、この技術を用いて施される。
- これらのコーティングは、まぶしさを抑え、視認性を向上させ、建物のエネルギー効率を高める上で非常に重要である。
-
工具および耐摩耗コーティング
- このプロセスは、窒化チタン(TiN)などの硬い耐摩耗性コーティングを切削工具や機械部品に蒸着するために使用されます。
- これらのコーティングは、耐摩耗性、耐腐食性、耐高温性を向上させることにより、工具の寿命を延ばす。
- 用途としては、ドリル、フライスカッター、その他の産業用工具が挙げられる。
-
太陽電池
- スパッタ蒸着は、太陽光発電システムに使用される薄膜太陽電池の製造において重要な役割を果たしている。
- テルル化カドミウム(CdTe)やセレン化銅インジウムガリウム(CIGS)のような材料の薄膜は、効率的で軽量な太陽電池パネルを作るために基板上に蒸着されます。
- この用途は、費用対効果が高く、拡張性のある太陽エネルギー・ソリューションを可能にすることで、再生可能エネルギー分野を支えている。
-
透明導電膜
- スパッタ蒸着は、タッチスクリーン、フラットパネル・ディスプレイ、フレキシブル・エレクトロニクスに不可欠なインジウム・スズ酸化物(ITO)などの透明導電膜を作成するために使用されます。
- これらの膜は高い導電性と光学的透明性を兼ね備えており、最新の電子機器に最適です。
-
装飾的・機能的コーティング
- この技術は、時計、宝飾品、自動車部品などの消費者向け製品に装飾コーティングを施すために採用されている。
- ドライフィルム潤滑剤などの機能性コーティングも、摩擦を減らして機械システムの性能を向上させるためにスパッタリングで成膜される。
-
表面物理学と分析用途
- 蒸着だけでなく、スパッタリングは表面物理学の分野でも、高純度表面の洗浄や調製に用いられている。
- スパッタリングは表面の化学組成を分析する手法でもあり、材料科学や研究において有用である。
要約すると、スパッタ蒸着は産業界に多様な用途を持つ重要な技術である。薄膜の厚さ、組成、均一性を精密に制御して成膜できるスパッタ蒸着は、現代の製造や研究に不可欠な技術である。半導体やデータストレージから再生可能エネルギーや装飾コーティングに至るまで、スパッタ蒸着は技術革新と技術進歩を推進し続けている。
総括表
用途 | 主な用途 |
---|---|
半導体製造 | インターコネクト用薄膜、ICコンタクトメタルを成膜 |
データストレージ | ハードディスク用磁性フィルム、CD/DVD用反射層を生産 |
光学コーティング | ガラスに反射防止膜とLow-E膜をコーティング |
工具および耐摩耗コーティング | 切削工具にTiNなどの硬質皮膜を成膜 |
太陽電池 | 再生可能エネルギー用薄膜太陽電池を製造 |
透明導電膜 | タッチスクリーンやディスプレイ用のITOフィルムを生産 |
装飾・機能性コーティング | 時計、宝飾品、自動車部品にコーティングを施す |
表面物理学と分析 | 表面を洗浄し、研究のために化学組成を分析します。 |
スパッタ蒸着が製造工程をどのように向上させるか、ご覧ください。 今すぐお問い合わせください !