圧縮成形は広く使われている製造工程で、特に自動車製造のような業界では内装部品やトリムカバーの製造に採用されている。この方法では、熱と圧縮を利用して、金属、プラスチックコンパウンド、ゴムなどの原材料を金型に成形します。費用対効果や効率性など、いくつかの利点がある一方で、欠陥のリスクや金型への損傷の可能性など、独自の課題も伴います。圧縮成形のメリットとデメリットの両方を理解することは、製造プロセスにおいて十分な情報を得た上で意思決定を行う上で非常に重要です。
主なポイントを説明します:
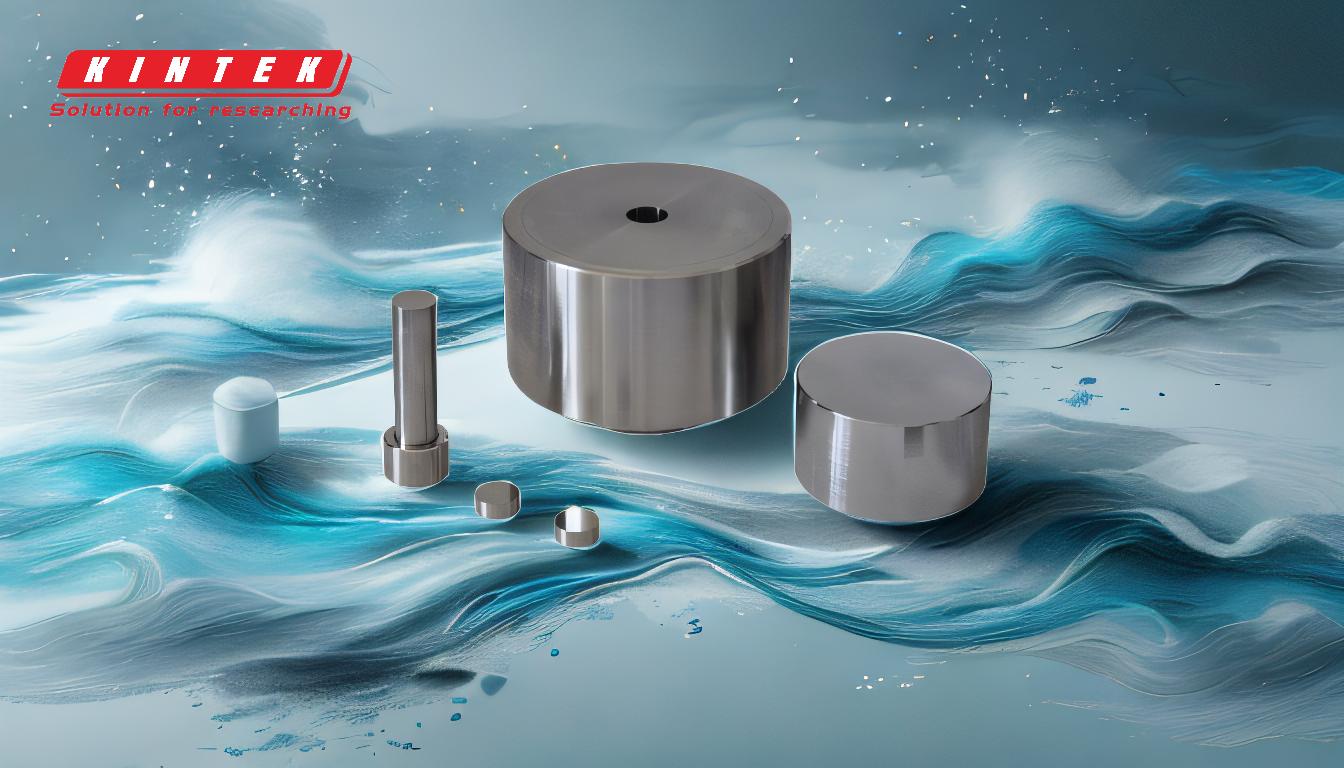
-
圧縮成形の利点
- 費用対効果: 圧縮成形は、プロジェクト全体のコストを最小限に抑えることができることで知られています。このプロセスは、材料の無駄と人件費を削減し、大規模生産のための経済的な選択肢となっています。
- 効率: 油圧プレスに支えられた圧縮成形は、迅速かつ効率的なプロセスです。油圧プレスを使用することで、材料が均等に分散され、金型が迅速かつ正確に充填されます。
- 汎用性: この方法は、金属、プラスチックコンパウンド、ゴムなど、幅広い素材に適している。特に、自動車製造における内装アプリケーションやトリムカバーの作成に最適です。
- 材料の無駄を最小限に モールドフラッシュと呼ばれる金型の特殊な溝から余分な材料が流れ出るため、材料の無駄を最小限に抑えるように設計されています。これは、生産コスト全体の削減に役立ちます。
-
圧縮成形の欠点
- 欠陥のリスク: 圧縮成形における主な課題のひとつは、各キャビティに十分な量のゴムを正確にカットしたり計量したりすることです。ストックが少なすぎたり、配置が不適切だったりすると、フローライン、ブリスター、未充填部品などの欠陥につながる可能性があります。ゴムが過剰になると、バリがひどくなり、除去が困難になる。
- 金型への損傷の可能性 圧縮成形の過程で金型が損傷する可能性がある。これは、材料を成形するために必要な高圧と高温のために発生する可能性があり、メンテナンスコストの増加とダウンタイムの可能性につながります。
- 個々の部品コストの上昇: プロジェクト全体のコストは最小限に抑えることができますが、圧縮成形の個々の部品のコストは、他の技術に比べて高くなる可能性があります。これは、工程で要求される精度と、手直しや追加の品質管理措置を必要とする欠陥の可能性があるためです。
- 材料の取り扱いの複雑さ: この工程では、金型の各キャビティに形の整った枝分かれしていないゴムストックを配置する必要がある。ストックの形状や配置にずれがあると欠陥につながるため、材料の取り扱い工程が複雑になり、時間もかかる。
-
用途と考察
- 自動車産業 圧縮成形は、サンバイザーやギアノブなど、さまざまな内装部品の製造に自動車業界で広く使用されています。このプロセスは、高度な細部と精度が要求される部品の製造に最適です。
- 材料の選択 圧縮成形では、材料の選択が非常に重要です。材料は、この工程に必要な高圧と高温に耐えるものでなければならない。さらに、欠陥の原因となることなく金型キャビティを満たすために、材料が均一に流動できなければなりません。
- プロセスの最適化 圧縮成形の利点を最大限に引き出すには、プロセスを最適化することが不可欠です。これには、材料を正確に測定して配置すること、適切な温度と圧力を維持すること、損傷を防ぐために金型を良好な状態に保つことなどが含まれます。
結論として、圧縮成形は、費用対効果、効率性、汎用性など、いくつかの利点を提供し、特に自動車産業におけるさまざまな製造アプリケーションのための一般的な選択肢となっている。しかし、欠陥のリスク、金型への損傷の可能性、個々の部品コストの上昇といった課題もあります。これらの長所と短所を理解することは、十分な情報を得た上で決定を下し、特定の用途に圧縮成形プロセスを最適化する上で極めて重要である。
総括表
側面 | メリット | デメリット |
---|---|---|
費用対効果 | 材料の無駄と人件費を削減し、大量生産に最適。 | 精度と潜在的欠陥のため、個々の部品コストが高くなる。 |
効率性 | 均一な材料分配を可能にする油圧プレスで、迅速かつ効率的に。 | フローライン、ブリスター、未充填部品などの欠陥のリスク。 |
汎用性 | 金属、プラスチック、ゴムに適し、自動車部品に最適。 | 材料の取り扱いが複雑で、金型を損傷する可能性がある。 |
材料の無駄 | モールドフラッシュの溝により、材料の無駄を最小限に抑えます。 | 過剰な材料による重いバリが発生すると、除去が困難になることがあります。 |
圧縮成形プロセスを最適化する準備はできていますか? 当社の専門家に今すぐご連絡ください オーダーメイドのソリューションを