はじめに
静水圧プレスは、様々な産業において多くの利点と用途を提供する製造プロセスである。均一な密度と形状を得るために、材料にあらゆる方向から均等な圧力をかける。この方法は、他の製造技術と比較して特に有利である。静水圧プレスは、複雑な内部形状や細長い壁を持つ部品の製造を可能にします。しかし、プレス面の精度が劣る、代替技術と比べて生産率が低いなど、等方圧プレスの限界を考慮することが重要である。
目次
静水圧プレスの概要
静水圧プレスの説明
静水圧プレスは、流体圧を利用して混合粉末を圧縮し、空隙率を減少させる粉末加工技術です。あらゆる方向から均等に圧力を加える静水圧を利用して、混合粉末を封じ込めます。このプロセスでは、金属粉末を柔軟な膜または密閉容器内に閉じ込め、粉末とそれを取り囲む加圧媒体(液体または気体)との間に圧力バリアを作ります。
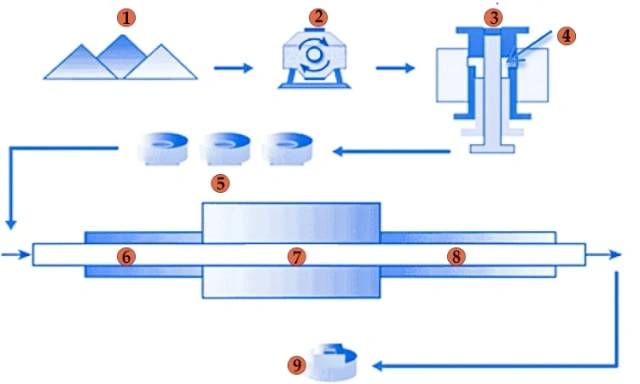
静水圧プレスの種類:ウェットバッグとドライバッグ
等方圧加圧には、一般的にウェットバッグとドライバッグの2種類がある。ウェットバッグは、プレス機の外側にエラストマー製の金型を設置し、それを圧力容器に浸します。加圧と圧縮の後、金型は容器から取り出され、部品が取り出され、この工程が繰り返されます。1回の加圧運転で複数の金型を容器に装填することができる。
一方、ドライバッグ法では、加圧容器と一体化した金型を作ることにより、浸漬工程を省くことができる。ドライバッグプロセスでは、パウダーが金型に加えられ、金型が密閉され、圧力が加えられ、部品が排出される。この工程では金型が一体化されているため、ウェットバッグ工程に比べて自動化が容易です。
セラミックの成形圧力
静水圧プレスは、セラミックや耐火物の用途に独自の利点を提供します。形状やサイズに関係なく、製品全体に均一で均等な力を加えることができます。この特性により、精密な公差を持つ製品形状の形成が可能になり、コストのかかる機械加工の必要性が減少します。等方圧加圧法は、高温耐火物、セラミックス、超硬合金、ランタノン永久磁石、炭素材料、レアメタル粉末の成形に広く使われている。
静水圧プレスは、粉末を圧密したり、鋳物の欠陥を治したりするために、さまざまな産業で使用される実行可能な生産ツールとなっている。高い成形密度を達成し、複雑な形状を作ることができるため、多くの用途で好まれている。しかし、一軸プレスと比較すると、金型費用と工程の複雑さが高くなることに注意が必要です。
静水圧プレスの利点
静水圧プレスは、他の製造方法と比べていくつかの利点があります。他の手法と比較した静水圧プレスの利点を詳しく見てみましょう:
他の製造方法と比較した静水圧プレスの利点
- 焼成時の歪みが少ない:静水圧プレスは、焼成時の歪みを最小限に抑え、最終製品の寸法精度を保証します。
- 焼成時の安定した収縮:焼成工程における等静圧プレス部品の収縮率は一定しており、予測可能で均一な結果をもたらします。
- 部品を乾燥させずに焼成できる:他の方法と異なり、等方圧プレスは、事前に乾燥させることなく部品を焼成できるため、時間とエネルギーを節約できます。
- 粉末中のバインダー濃度を低くできる:アイソスタティック・プレスでは、混合粉体中のバインダー濃度を低くすることができるため、追加の加工工程を減らすことができます。
- ほとんどの未焼成成形体は機械加工が可能です。:静水圧プレス成形された圧粉体は容易に機械加工が可能であり、製造工程に柔軟性をもたらします。
- プレス成形体の内部応力が低い:アイソスタティック・プレス加工により、成形品の内部応力が低く、割れや変形のリスクを低減します。
- 非常に大きなプレス部品:ウェットバッグ工法による超大型部品の生産に対応でき、用途が広がります。
- 低い金型コスト:静水圧プレスは、他の製造方法と比較して金型コストが低く、短納期の生産において費用対効果の高い選択肢となります。
- 一定のプレス圧力でより高い密度:等方圧プレスは、機械的なプレス方法と比較して、与えられたプレス圧力に対してより高い密度を達成し、その結果、より強く耐久性のある部品が得られます。
- 長径比の大きい成形品のプレスが可能。:静水圧プレスは、長径比の大きい成形品の製造が可能であり、幅広い用途に適しています。
- 内部形状のプレスが可能:ネジ、スプライン、セレーション、テーパなどの内面形状部品に対応でき、設計の可能性が広がります。
- 薄肉長尺部品のプレスが可能:薄肉長尺部品が可能で、製品設計の幅が広がります。
- 弱い粉体のプレスが可能:弱い粉体を効率よくプレスすることができ、材料利用率が向上し、製品全体の品質が向上します。
- 特性の異なる粉末を2層以上積層した成形品のプレスが可能です。:静水圧プレスにより、特性の異なる複数の粉末を積層した成形体を製造することができ、材料特性や性能を向上させることができます。
静水圧プレスには、さまざまな産業で好まれる製造方法となるさまざまな利点があります。その能力のいくつかを、さらに詳しく探ってみましょう。
静水圧プレスの機能
- 均一な密度:成形品の密度が均一であるため、焼結時や熱間静水圧プレス時の収縮が安定し、反りが最小限に抑えられます。
- 形状の自由度:静水圧プレスは、他の方法では困難または不可能な形状や寸法の製造を可能にし、設計の柔軟性を提供します。
- 部品サイズ:静水圧プレスは、30トンの巨大なニアネット粉末冶金形状から100グラム未満の小さなMIM部品まで、幅広い部品サイズに対応できます。
- 大型部品:等方圧加圧チャンバーのサイズのみが部品サイズの制限となるため、大型部品の製造に適しています。
- 合金化の可能性:等方圧加圧は、材料の偏析を引き起こすことなく合金元素の強化を可能にし、材料の選択肢を広げます。
- リードタイムの短縮:静水圧プレスは、試作品から量産品まで複雑な形状を経済的に製造することができ、従来の製造方法と比較してリードタイムを大幅に短縮することができます。
- 材料費と加工費の削減:ニアネットシェイプの部品は、等方圧プレスで製造することができ、材料の無駄と加工コストを削減することができます。
静水圧プレスは、そのユニークな利点と能力により、様々な産業で応用されています。静水圧プレスの一般的な用途を見てみましょう。
静水圧プレスの用途
- 医薬品
- 火薬類
- 化学薬品
- 食品
- 核燃料
- フェライト
等方圧プレスのその他の応用産業(医薬品、火薬類、化学薬品、核燃料フェライト)
アイソスタティック・プレスは、他の技術に比べ多くの利点を持つ汎用性の高い製造方法です。幅広い材料に適用でき、複雑な形状や寸法を高い精度で製造できます。均一な密度の達成、複雑な内部形状の部品のプレス、金型コストの削減など、静水圧プレスは多くの産業において価値ある製造オプションであることが証明されています。
静水圧プレスの短所
静水圧プレスは、他の技術に比べてさまざまな利点がある製造方法です。しかし、デメリットがないわけではありません。静水圧プレスの欠点を詳しく見てみましょう:
プレス面の精度が低い
静水圧プレスの欠点は、フレキシブルバッグに隣接するプレス面の精度が低いことです。つまり、所望の精度を得るためには、その後の機械加工が必要になる場合があります。これに比べ、機械的プレスや押し出し技術では、一般的にプレス面の精度が高くなります。
全自動ドライバッグプレスのコスト高
等方圧プレスで一般的に使用される全自動ドライバッグプレスは、比較的高価な噴霧乾燥粉末を必要とします。そのため、プロセス全体のコストが高くなる可能性があります。高品質の材料と特殊な設備を使用するため、このタイプのプレスにかかる費用が高くなります。
押出成形や金型成形と比較した場合の生産率の低さ
アイソスタティック・プレスは、押出成形や金型成形に比べて生産率が低い傾向があります。これは、生産量の点で効率が悪い可能性があることを意味します。異なるプレス技術を選択する際には、生産要件とスケジュールを考慮することが重要です。
このような欠点があるにもかかわらず、等方圧加圧には独自の利点があり、特定の用途では貴重な選択肢となります。焼成中の低歪みと一貫した収縮を可能にし、グリーンコンパクトの加工を可能にし、内部形状や高い長さ-直径比の部品をプレスする能力を提供します。さらに、等方圧加圧は機械的加圧よりも高い密度を達成することができ、多層の粉末を含む成形体を加圧する能力があります。
等方圧加圧の長所と短所を特定の製造ニーズと照らし合わせ、特定の用途に適した選択かどうかを判断することが重要です。
ドライバッグ静水圧プレス
ドライバッグ静水圧プレスの説明と用途
ドライバッグ静水圧プレスは、機械加工や焼結の前に、粉末材料を固体の均質な塊に圧縮する方法です。簡単なプロセスで、焼成時の歪みや割れを最小限に抑えた、整合性の高いビレットやプリフォームを製造できます。このプロセスは、軸対称形状の比較的小さな超硬合金の製造に特に適しています。
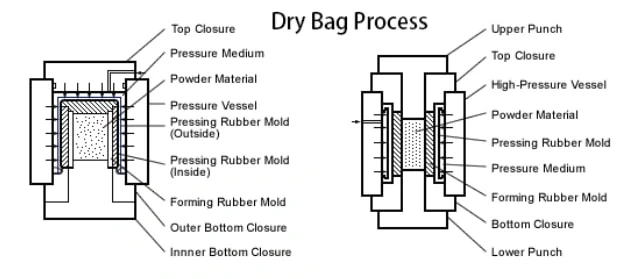
ドライバッグプロセス
ドライバッグ静水圧プレスにおける自動化の利点
ドライバッグプレスの主な利点は、自動化の可能性であり、複雑な形状の超硬合金の大量生産または半量生産をコスト効率よく行うことができます。これには、ロッド、チューブ、ブッシュ、ボール、プランジャー、ドリル、スクリュー、ノズルなどが含まれます。
また、ドライバッグ静水圧プレスの自動化により、正確な外径および内径寸法を持つ、ほぼネットシェイプの中空グリーン成形品の製造も可能になります。これにより、必要な加工量が大幅に削減され、切粉の発生が減少する。
WC-Co粉末の品質とプレス金型設計の役割
超硬グリーンコンパクトを効果的に製造するには、WC-Co粉末の品質とプレス金型の設計が重要な役割を果たす。最終製品の適切な成形と望ましい特性を確保するためには、粉末の品質を慎重に選択する必要がある。
一体型や交換型など、プレス金型の設計にはさまざまな選択肢があり、プレス工程に柔軟性をもたらします。一体型の金型は、超硬合金の成形品の寸法が一定期間一定である場合に好ましく、フレキシブルな金型システムは、頻繁に金型を交換する場合に適しています。
ドライバッグプレスの構成部品
ドライバッグプレスは、高圧ポンプ、弾性プレス金型、膜付きプレス室、圧力容器で構成される。圧力は高圧ポンプで高められ、膜を介してWC-Co粉末が放射状に充填されたプレス型に伝達される。プレス金型への装填は手動または自動で行われる。
1回のプレスは通常5~10分で、1個のグリーンコンパクトを生産する。ドライバッグシステムは、直径200mm、長さ600mmまでのロッドやチューブをプレスすることができます。このようなチューブの内径と外径は、寸法によって0.1~1mmの公差でプレスできます。
結論として、ドライバッグ等方圧加圧は、粉末材料を固体の均質な塊に圧縮するための効率的な方法である。大量生産のための自動化、正確な寸法、機械加工の必要性の低減などの利点がある。WC-Coパウダーの品質とプレス金型の設計は、成形を成功させるための重要な要素です。
湿式バッグ静水圧プレス
湿式バッグ静水圧プレスの説明と用途
ウェットバッグ技術は、粉末を金型に充填し、圧力容器の外で密閉する冷間等方圧プレスの方法です。その後、金型を容器内の圧力流体中に沈め、金型の外面に等方圧を加え、粉末を圧縮して固形塊にします。
この製法はドライバッグ等方圧プレスほど一般的ではありませんが、世界中で3000台以上のウェットバッグプレスが使用されています。ウェットバッグの大きさは、直径50mmの小さなものから2000mmの大きなものまであります。
ウェットバッグ技術は比較的時間がかかり、処理時間は5分から30分である。しかし、大容量ポンプや改良されたローディング機構を使用することで、工程をスピードアップすることができる。
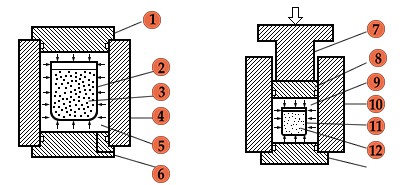
ウェットバッグプロセス (1.トップクロージャー 2.ゴム型 3.パウダー 4.高圧 5.圧力媒体 6.ボトムクロージャー 7.ステム 8.ピストン 9.圧力媒体 10.高圧容器 11.ゴム型 12.パウダー 13.ボトムクロージャー)
湿式バッグアイソプレスの利点
-
湿式バッグアイソスタティックプレスにはいくつかの利点があります:
-
密度が均一:湿式バッグ等方圧加圧は、等方圧加圧の理論的概念に近づけることができ、均一な密度と低い巻き込み応力を持つ成形体が得られます。これにより、歪みのないグリーン状態での加工が可能になります。
-
歪みの低減:湿式バッグアイソプレスで製造された部品は、焼成時にほとんど歪みが発生しないため、高価な機械加工の必要性が低減または排除されます。
自動化の可能性:湿式バッグアイソプレスは自動化に適しているため、比較的長時間の成形品を高い生産率でプレスするのに適しています。
ウェットバッグとドライバッグのアイソプレスの違い
-
ウェットバッグ等方圧とドライバッグ等方圧の主な違いは、粉体の圧縮方法です:
-
湿式バッグ等方圧加圧:湿式バッグ等方圧加圧:湿式バッグ等方圧加圧では、加圧流体中に完全に浸漬された密閉エラストマー金型内で粉末を圧縮する。この方法は、特殊部品の少量生産、試作、研究開発に使用されます。
ドライバッグ等方圧加圧:ドライバッグ等方圧プレスでは、エラストマー金型は等方圧プレスと一体化しています。加えられる圧力はほとんどが二軸であり、大量生産のためにプロセスを自動化することができます。
ウェットバッグとドライバッグのアイソスタティック・プレスには、長所と短所があります。ウェットバッグは大型部品の生産に適しており、摩擦を最小限に抑えて高密度にすることができます。しかし、金型へのロードとアンロードは生産性を低下させ、自動化を制限する可能性があります。一方、ドライバッグ等方圧加圧は、自動化と生産率において優位性があります。
全体として、等方圧プレスは、高い圧縮密度を達成し、一軸プレスでは圧縮できない形状にアクセスするために選択されます。ウェットバッグ等方圧プレスとドライバッグ等方圧プレスのどちらを選択するかは、生産工程の特定の要件によって決まります。
一軸プレスと静水圧プレスの比較
静水圧プレスで克服できる一軸プレスの限界
通常の粒子充填に関係する一軸プレスのいくつかの限界は、静水圧プレスによって克服することができます。等方加圧は、一方向からしか加圧しない一軸加圧とは異なり、あらゆる方向から加圧します。これにより、より均一な成形と高い充填均一性が可能になります。等方圧加圧には、ウェットバッグ方式とドライバッグ方式の2種類があります。
ウェットバッグ静水圧プレスでは、粉末をフレキシブルな金型に充填して密閉し、高圧容器内の液体に浸します。液体が加圧され、その圧力が金型の柔軟な壁を通して粉末に伝わり、成形が行われる。ウェットバッグ等方加圧は、一軸加圧に比べて充填の均一性が高い。圧力は1000GPaまで使用できますが、最も一般的な製造装置では200~300MPaまでです。湿式バッグ静水圧プレスは、3Dグリーンマシニングと組み合わせて、複雑なセラミック部品を非常に高い品質で製造するために使用されます。
ドライバッグ静水圧プレスは、ウェットバッグプロセスよりも自動化が容易です。このプロセスでは、ゴム型を圧力容器にしっかりと接続します。しかし、加圧された液体は全方向から作用するわけではないため、粉末成形体内の均質な粒子充填を確実にするためには、慎重な金型設計が必要です。
一軸プレスと等方圧プレスのグリーンボディの比較
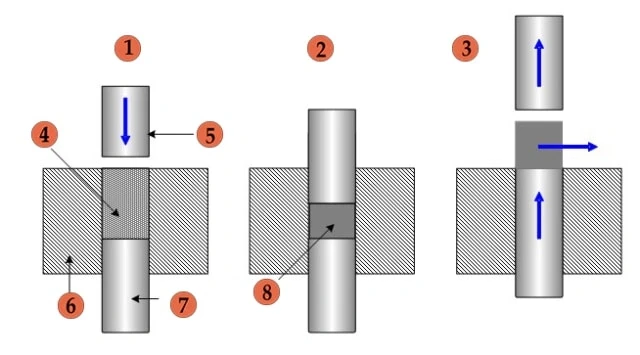
一軸プレス技術の説明図(1.金型充填段階 2.成形 3.部品排出 4.粉末 5.上パンチ 6.金型 7.下パンチ 8.「グリーン」コンパクト)
一軸プレスと等方圧プレスを比較すると、一軸プレスの方が小物形状で生産量が多い場合に適しています。しかし、金型壁の摩擦により、特にアスペクト比が大きい場合、密度が不均一になることがあります。一方、等方圧プレスは、小型でも大型でも、単純な形状でも複雑な形状でも使用できる。均一なグリーン密度が得られるため、焼結時の収縮が均一になり、形状制御や均一な特性にとって重要です。また、静水圧プレスでは、一軸プレスで使用されるワックスバインダーが不要になるため、脱ワックス作業が不要になります。
等方加圧には、低コストのエラストマー金型が使用されるが、精度の高いスチール製マンドレルに押し付けられる表面でのみ、近い公差を得ることができる。エラストマー金型と接触する表面は、厳しい公差と良好な表面仕上げを達成するために後加工が必要になる場合があります。
まとめると、等方加圧は、あらゆる方向から圧力を加えることで、一軸加圧の制限を克服しています。より高い充填均一性、焼結時の均一な収縮、ワックスバインダーが不要になります。等方圧加圧には、ウェットバッグ法とドライバッグ法があり、それぞれに利点と限界があります。
静水圧プレス用粉末の準備
静水圧プレスにおけるパウダーの要件
静水圧プレスは、流体圧を利用して部品を圧縮する粉末加工技術です。最適な結果を得るためには、静水圧プレスに使用する粉末に関して、一定の要件を満たす必要があります。
重要な要件の一つは、粉末の粒度分布です。静水圧プレスでは、粒径が1~5μmのパウダーを使用することを推奨します。この粒度範囲であれば、理論密度の98%以上の密度の材料を形成することができる。平均粒径が約0.5μmのドープされていないアルミナ粉末の使用は、これらの密度を達成するのに有効であることがわかっている。
もう一つの要件は、粉末混合物中のバインダー含有量である。バインダーは、プレス工程で粉末粒子をつなぎ合わせる役割を果たす。具体的なバインダー含有量は、使用するパウダーの種類と最終製品に望まれる特性によって異なる。通常、20%~30%のバインダーが使用され、セルロースワックス混合物が一般的です。
粒度分布とバインダー含有量の調整
静水圧プレス前の粉体調整を最適化するために、粒度分布とバインダー含有量を調整することができる。
粒度分布は、粉末をより細かい粒径に粉砕することで調整できる。理想的には、静水圧プレスに使用するパウダーの粒径は75μm以下が望ましい。このように粒径を細かくすることで、圧縮性が向上し、より均質なサンプルペレットが得られます。
バインダーの含有量は、製造する部品の特定の要件に基づいて調整することもできます。バインダーの含有量を増やすとプレスされたペレットに強度が増し、逆に減らすと多孔質構造になります。最終製品で望ましい特性を得るためには、強度と多孔性の適切なバランスを見つけることが重要です。
静水圧プレスにおけるパウダーの要件を慎重に検討し、粒度分布とバインダー含有量を調整することで、メーカーは所望の特性を備えた高品質の部品を製造することができます。静水圧プレスは、粉末成形のための多用途で効果的な方法を提供し、さまざまな材料の製造を可能にします。
結論結論として 静水圧プレス
無料相談はお問い合わせください
KINTEK LAB SOLUTION の製品とサービスは、世界中のお客様に認められています。弊社スタッフがどんなご質問にも喜んで対応させていただきます。無料相談にお問い合わせいただき、製品スペシャリストにご相談いただき、アプリケーションのニーズに最適なソリューションを見つけてください。