押出成形と共押出成形は、どちらもプラスチック製品の製造に使われる製造工程だが、その複雑さと用途は異なる。一般的な押出成形は、固形のプラスチックペレットを溶かし、ダイに通してパイプ、チューブ、シートなどの連続した形状を作ります。一方、共押出成形は、複数の押出機を使用して異なる材料を1つの製品に組み合わせ、層状またはカプセル状の構造を作ります。これにより、バリア性、強度、美観の向上など、機能性を高めることができる。単一素材の製品では押出成形の方がシンプルでコスト効率が高いが、1つの製品に複数の素材特性を必要とする用途では、共押出成形が理想的である。
キーポイントの説明
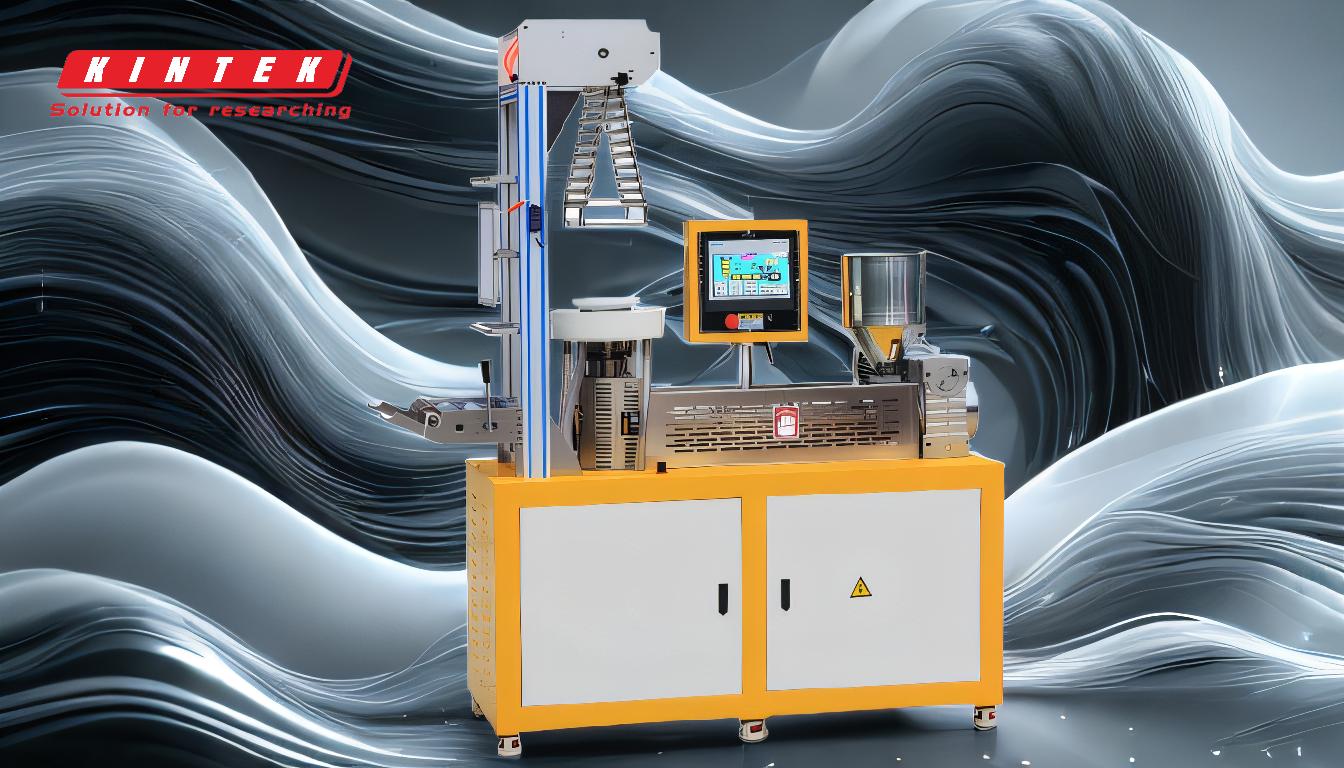
-
プロセス概要:
- 押出:標準的な押出成形では、固形のプラスチックペレットが成形機構に重力で送り込まれる。圧縮スクリューがペレットを溶かし、溶けたプラスチックがダイを通して押し出され、連続した形状が作られる。このプロセスは、パイプ、チューブ、シートなどの単一素材製品に使用される。
- 共押出:共押出では、複数の押出機が同時に作動する。各押出機はそれぞれ異なる材料を加工し、それらをダイの中で組み合わせて、複数の層やカプセル化された成分を持つ単一の製品を形成する。これは、バリア層を持つ食品包装など、複数の材料特性を必要とする製品に使用されます。
-
素材用途:
- 押出:単一種類のプラスチック素材を使用。工程が単純なため、均一な製品を生産するための費用対効果が高い。
- 共押出:複数の素材を使用し、異なる種類のプラスチックや、接着剤やバリア層など他の素材との組み合わせも可能。これにより、より複雑で機能的な製品設計が可能になります。
-
アプリケーション:
- 押出:PVCパイプ、プラスチックシート、プロファイルなどの製品によく使用される。単一の材料で十分な用途に最適。
- 共押出:多層食品包装、表面と芯材が異なる自動車部品、バリア層を持つ医療用チューブなど、複数の材料特性を必要とする用途に使用される。
-
利点と限界:
-
押出:
- 利点 :単純性、費用対効果、単一素材製品の高い生産率。
- 制限事項 :単一素材製品に限られ、より複雑な用途の要件を満たさない場合がある。
-
共押出:
- 利点 :異なる素材を組み合わせることで、製品の機能性と性能を向上させる能力。これには、バリア性、強度、美観の向上が含まれる。
- 制限事項 :複数の押出機が必要で、材料の流れや積層を正確に制御する必要があるため、より複雑で高価になる。
-
押出:
-
設備とセットアップ:
- 押出:押出機1台、ダイ1個、冷却循環機1台が必要です。 冷却サーキュレーター システム。セットアップは比較的簡単で、大量生産用に簡単に拡張できる。
- 共押出:それぞれ異なる材料専用の複数の押出機と、これらの材料を1つの製品に結合できる複雑なダイが必要。セットアップはより複雑で、材料の適切な積層と結合を保証するために精密な制御が必要です。
-
品質と性能:
- 押出:一貫した特性を持つ均一な製品ができる。ただし、特性は使用する単一材料のものに限定される。
- 共押出:強化された強度、柔軟性、バリア性能など、カスタマイズされた特性を持つ製品を作ることができる。そのため、より要求の厳しい用途に適している。
まとめると、単一素材の製品では押出成形がよりシンプルでコスト効率の高いプロセスであるのに対し、共押出成形では複数の素材を組み合わせることで、より複雑で機能的な製品を作ることができる。両者の選択は、製造する製品の具体的な要件によって決まる。
総括表
側面 | 押出 | 共押出 |
---|---|---|
プロセス | 単一押出機、単一材料、よりシンプルなプロセス | 複数の押出機、複数の材料、複雑なレイヤリング |
材料 | 単一種類のプラスチック | 複数の素材(例:プラスチック、接着剤、バリア層) |
用途 | パイプ、チューブ、シート、プロファイル | 多層食品包装、自動車部品、医療用チューブ |
利点 | コスト効率、高い生産率、シンプルさ | 機能性の向上(バリア性、強度、審美性など) |
制限事項 | 単一素材製品に限定される | より複雑で高価、精密な制御が必要 |
設備 | 単一押出機、ダイ、冷却システム | 複数の押出機、複雑なダイ、精密な積層制御 |
品質 | 一貫した特性を持つ均一な製品 | カスタマイズされた特性(強度、柔軟性、バリア性能など) |
お客様のプロジェクトで押出成形と共押出成形のどちらを選択するかお困りですか? 今すぐ当社の専門家にお問い合わせください !